- お役立ち記事
- Gasketed Flange Joints: Mechanics, Leakage Prevention, and Design
月間76,176名の
製造業ご担当者様が閲覧しています*
*2025年3月31日現在のGoogle Analyticsのデータより
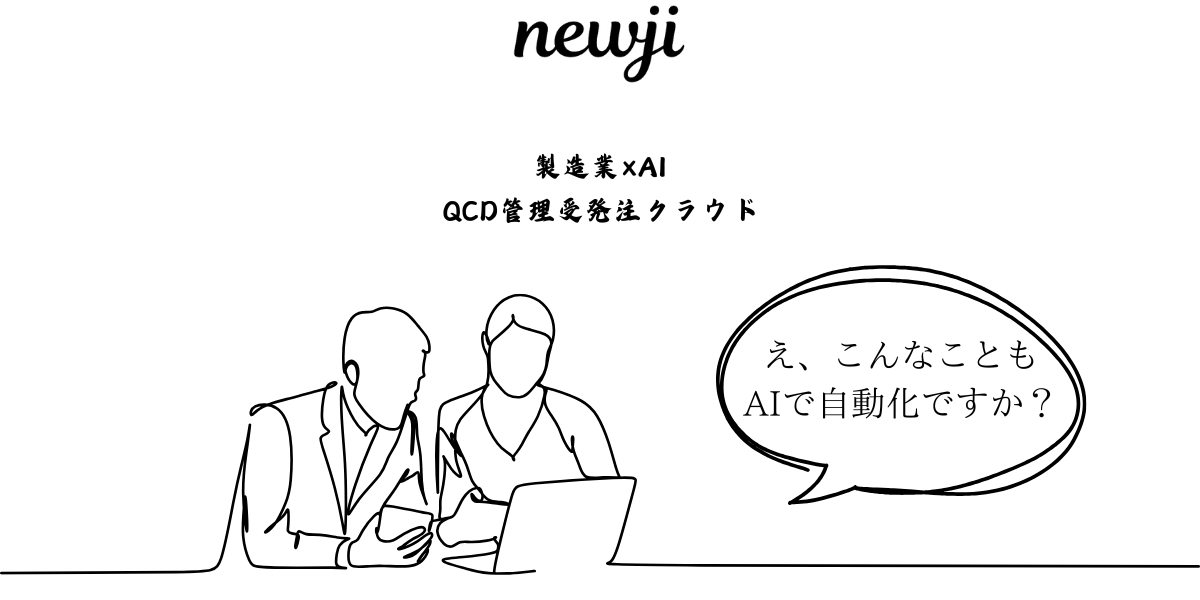
Gasketed Flange Joints: Mechanics, Leakage Prevention, and Design
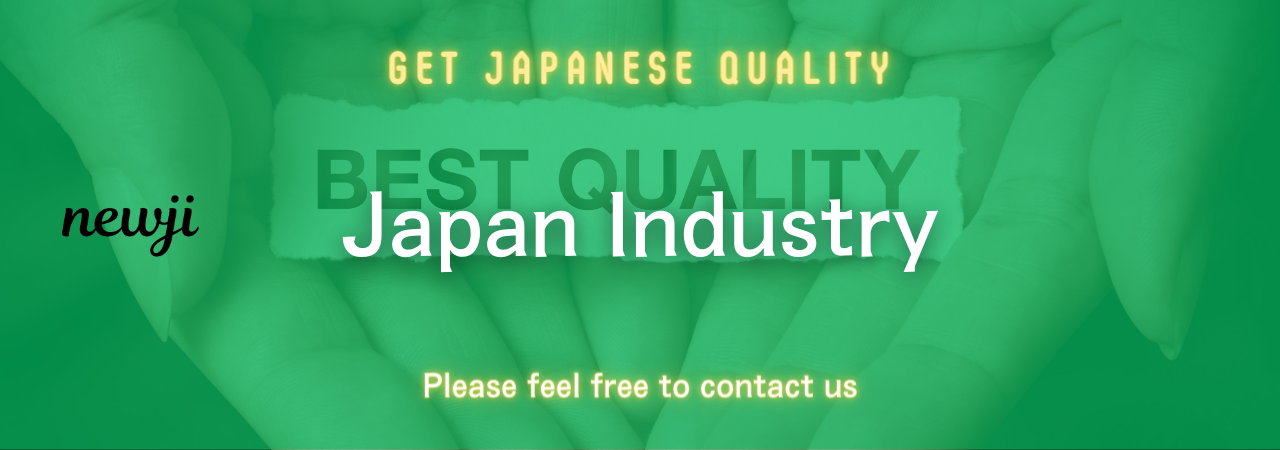
Gasketed flange joints are critical components in various industrial systems, including piping, pressure vessels, and equipment connections.
These joints use gaskets to create a tight seal between two or more surfaces, ensuring that fluids such as gases and liquids do not escape.
Understanding the mechanics of these joints, preventing leakage, and designing them effectively is crucial for maintaining system integrity and safety.
目次
Understanding Gasketed Flange Joints
Gasketed flange joints consist of several key components: flanges, gaskets, bolts, and nuts.
The flanges are typically circular discs with holes for bolts, designed to be joined to pipes or equipment surfaces.
The gasket, often made from a softer material, is placed between the flanges to ensure a seal.
When the bolts are tightened, the gasket is compressed and deforms to fill any irregularities between the flange surfaces.
This compression creates a sealing force that prevents fluid leakage.
The Role of Gaskets
Gaskets play a pivotal role in the effectiveness of flange joints.
They are designed to withstand different pressures, temperatures, and fluid types.
The choice of gasket material is crucial as it must be compatible with the fluid it will encounter and the environmental conditions to which it will be exposed.
Common materials include rubber, graphite, PTFE, and various metal composites.
Each material has specific properties, such as resistance to high temperatures or chemical corrosion, that make it suitable for certain applications.
Mechanics of Flange Joint Assembly
The mechanical aspect of assembling a gasketed flange joint focuses on achieving the correct amount of gasket compression.
This is typically done by applying a specified torque to the bolts using a torque wrench.
Proper torque application is critical; insufficient torque may lead to leakage, while excessive torque might damage the gasket or flanges.
The assembly process usually follows specific guidelines and standards to ensure reliability and safety.
Engineers often use torque charts that specify the required bolt tension based on factors like bolt size and material.
Importance of Bolt Patterns
Bolt patterns, or the sequence in which bolts are tightened, also significantly affect the assembly process.
Using an alternating or star pattern helps ensure even distribution of load across the flange surfaces, minimizing the risk of uneven gasket compression and leaks.
This pattern reduces the possibility of flange warping, which can lead to joint failure over time.
Preventing Leakage in Gasketed Flange Joints
Leakage prevention starts with choosing the right components and follows through to careful installation and maintenance.
One of the primary causes of leakage is improper gasket selection or installation.
To prevent this, engineers must consider the operating conditions and properties of the fluid being transported.
Regular inspections and maintenance of gasketed flange joints can help identify potential issues before they lead to significant problems.
Inspectors look for signs of wear, corrosion, or damage to the gasket and flange surfaces.
Addressing Environmental Factors
Environmental conditions, such as temperature fluctuations and exposure to chemicals, can impact the lifespan and performance of gasketed joints.
Ensuring that the gasket material is suitable for the specific environment is essential.
For example, in high-temperature applications, a gasket material resistant to thermal degradation should be chosen.
Regular monitoring of operating conditions can provide data to predict joint performance and schedule timely maintenance.
Design Considerations for Gasketed Flange Joints
Designing effective gasketed flange joints involves several considerations to ensure durability and performance.
Engineers must calculate the forces and loads that the joint will encounter under operating conditions.
This includes internal pressure, temperature, and mechanical vibrations.
They also consider the type of fluid and its potential impact on materials.
Calculations for bolt load, gasket stress, and flange strength are essential elements of the design process.
These calculations help determine the appropriate gasket material and thickness, bolt size, and flange specifications.
Standards and Guidelines
Numerous industry standards and guidelines, such as those from the American Society of Mechanical Engineers (ASME) and the International Organization for Standardization (ISO), provide frameworks for designing and assembling gasketed flange joints.
Adhering to these standards can help ensure safety, reliability, and compatibility across different systems and components.
Using software tools for simulation and modeling can also be beneficial.
These tools predict the behavior of flange joints under various conditions, allowing engineers to optimize the design before physical assembly.
Challenges and Innovations in Flange Joint Technology
Despite the critical role that gasketed flange joints play, they are not without challenges.
Fatigue, corrosion, and improper assembly can lead to failures, posing safety risks.
Innovations in flange joint technology continue to address these issues.
Advancements in gasket materials, such as the development of high-performance elastomers and metal-reinforced gaskets, offer improved durability and resistance to harsh environments.
Automated assembly techniques and advanced monitoring systems provide real-time data, enabling proactive maintenance and reducing downtime.
The Future of Gasketed Flange Joints
As industries evolve and new materials and technologies emerge, the design and application of gasketed flange joints will continue to advance.
The integration of smart technology in these joints, such as sensors and IoT connectivity, may allow for better monitoring and predictive maintenance.
This could revolutionize how industries approach maintenance, efficiency, and safety in their systems.
In conclusion, understanding the mechanics, design, and maintenance of gasketed flange joints is crucial for ensuring system integrity and preventing leaks.
By focusing on proper component selection, careful assembly, and regular maintenance, industries can maintain safe and efficient operations.
資料ダウンロード
QCD管理受発注クラウド「newji」は、受発注部門で必要なQCD管理全てを備えた、現場特化型兼クラウド型の今世紀最高の受発注管理システムとなります。
ユーザー登録
受発注業務の効率化だけでなく、システムを導入することで、コスト削減や製品・資材のステータス可視化のほか、属人化していた受発注情報の共有化による内部不正防止や統制にも役立ちます。
NEWJI DX
製造業に特化したデジタルトランスフォーメーション(DX)の実現を目指す請負開発型のコンサルティングサービスです。AI、iPaaS、および先端の技術を駆使して、製造プロセスの効率化、業務効率化、チームワーク強化、コスト削減、品質向上を実現します。このサービスは、製造業の課題を深く理解し、それに対する最適なデジタルソリューションを提供することで、企業が持続的な成長とイノベーションを達成できるようサポートします。
製造業ニュース解説
製造業、主に購買・調達部門にお勤めの方々に向けた情報を配信しております。
新任の方やベテランの方、管理職を対象とした幅広いコンテンツをご用意しております。
お問い合わせ
コストダウンが利益に直結する術だと理解していても、なかなか前に進めることができない状況。そんな時は、newjiのコストダウン自動化機能で大きく利益貢献しよう!
(β版非公開)