- お役立ち記事
- Gate design and molded product quality improvement that new employees in the quality control department of the plastic molding industry should know
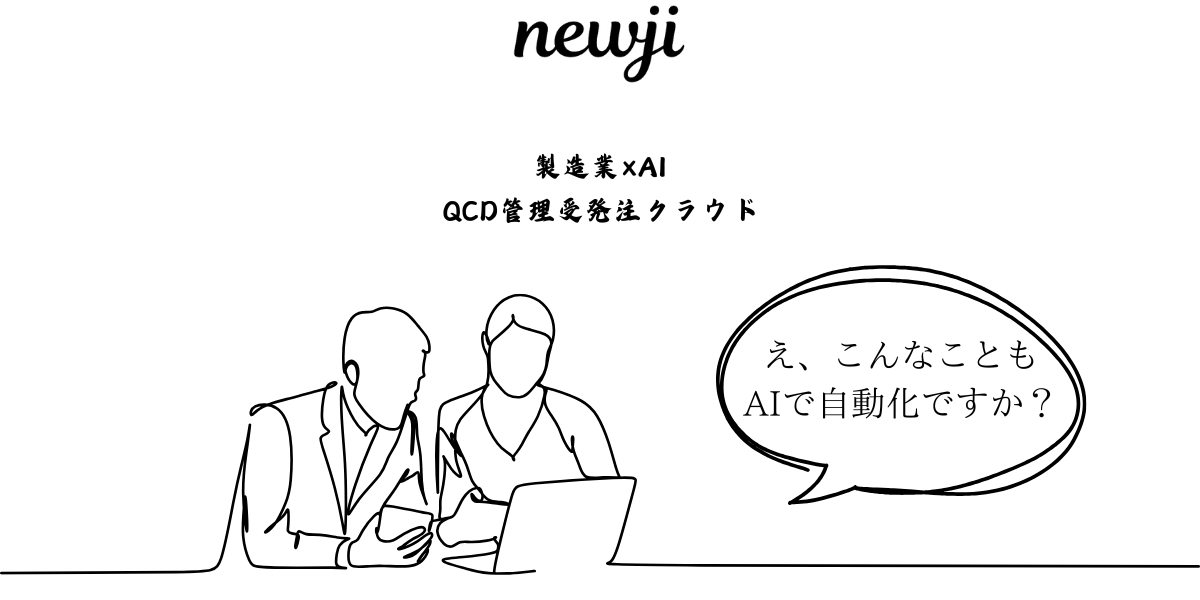
Gate design and molded product quality improvement that new employees in the quality control department of the plastic molding industry should know
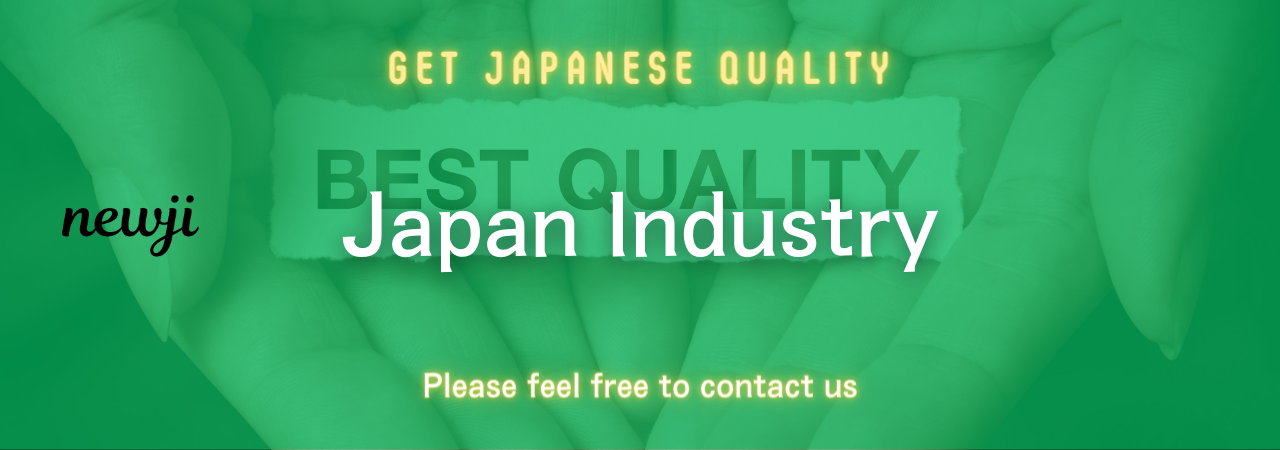
目次
Understanding Gate Design in Plastic Molding
In the plastic molding industry, gate design is a pivotal factor that influences the quality of molded products.
As a new employee in the quality control department, it’s essential to grasp the basics of gate design.
Gates are small openings that allow the molten plastic to flow into the mold cavity during the injection molding process.
Choosing the correct gate design is crucial for ensuring that a product is free from defects and meets desired quality standards.
The gate’s size, location, and type can affect the flow of plastic, cooling rate, and structural integrity of the finished product.
Knowing how to evaluate and optimize these parameters can significantly impact the final outcome of the molding process.
The Importance of Gate Location
The location of a gate is fundamental to achieving high-quality molded products.
Ideally, the gate should be positioned to allow the plastic to fill the mold evenly, minimizing potential defects like warping, sink marks, or voids.
A poorly located gate can lead to unbalanced flow, causing stress and weaknesses in the material.
Additionally, the gate should be placed in a position that allows for easy removal and minimizes marks or blemishes on the product’s surface.
By strategically placing the gate, manufacturers can enhance the aesthetic appeal and functionality of the final product.
Different Types of Gate Designs
There are several types of gate designs used in plastic molding, each with its unique advantages and applications.
As a quality control team member, understanding these types will help you in evaluating their impact on product quality.
1. **Edge Gate**:
– Commonly used in various applications, edge gates are located on the parting line of the mold.
– They provide a solid flow of material and are easily removed after molding.
2. **Submarine Gate**:
– Known for its automatic degating feature, a submarine gate is placed below the parting line and emerges from the part’s surface.
– It’s ideal for complex shapes where aesthetic is a concern.
3. **Hot Tip Gate**:
– Used for runnerless molds, hot tip gates provide a direct feed into the cavity.
– This type diminishes material waste and offers uniform melting, which is optimal for intricate designs.
4. **Fan Gate**:
– A fan gate spreads the flow across the surface of the part, reducing stress.
– It’s used for large flat parts to avoid warping and enhance surface quality.
Impact on Molded Product Quality
The quality of a molded product is directly linked to the effectiveness of gate design.
A well-optimized gate ensures that the flow of material is consistent, fills all areas of the mold, and cools uniformly.
This consistency reduces the likelihood of defects and improves the mechanical properties of the finished item.
Furthermore, the gate design impacts cycle time and cost-efficiency.
A properly configured gate can reduce cycle time by promoting faster cooling and ejection, leading to increased production rates and lower operational costs.
This is critical in maintaining competitiveness in the plastic molding market.
Common Gate Design Issues
Despite the best design intentions, issues can still arise if the gate is not appropriately managed.
Recognizing these potential problems early can save time and resources in the production process.
1. **Jetting**:
– Occurs when the plastic shoots too rapidly into the cavity, leading to a turbulent flow instead of a smooth one.
– Adjusting the gate size or location often remedies this issue.
2. **Burn Marks**:
– These marks occur due to trapped air or gas within the mold, typically a result of improper venting connected with gate placement.
– Ensuring adequate ventilation and modifying the gate can mitigate this defect.
3. **Weld Lines**:
– Appear when two flow fronts meet and do not fully bond; gate placement plays a crucial role in minimizing these marks.
– Changing the flow path by repositioning the gate can help overcome this challenge.
Strategies for Quality Enhancement
To enhance the quality of molded products, several strategies can be employed in conjunction with effective gate design.
– **Use of Simulation Software**:
Implementing computer-aided engineering (CAE) tools to simulate the injection molding process helps optimize gate design before any physical molds are made.
This allows for adjustments to be made virtually, reducing the likelihood of errors.
– **Iterative Testing and Feedback**:
Continuously testing molds and gathering data on performance leads to improvements in gate design, ensuring higher quality over time.
Engage in proactive troubleshooting to address any issues that arise promptly.
– **Cross-functional Collaboration**:
Work closely with design and manufacturing teams to ensure that everyone understands the implications of gate design choices.
Collaborative efforts lead to more comprehensive solutions, resulting in better quality control.
Conclusion
As a new member of the quality control department in the plastic molding industry, understanding gate design is essential for ensuring the production of high-quality molded products.
By focusing on the correct type, location, and parameters of gates, you can substantially influence the product’s overall quality and operational effectiveness.
Being proactive in addressing design issues and collaborating across departments will help you maintain and improve the standards of molded products.
With these insights, you’ll be well-equipped to contribute to the industry’s advancements and deliver top-notch products to the market.
資料ダウンロード
QCD調達購買管理クラウド「newji」は、調達購買部門で必要なQCD管理全てを備えた、現場特化型兼クラウド型の今世紀最高の購買管理システムとなります。
ユーザー登録
調達購買業務の効率化だけでなく、システムを導入することで、コスト削減や製品・資材のステータス可視化のほか、属人化していた購買情報の共有化による内部不正防止や統制にも役立ちます。
NEWJI DX
製造業に特化したデジタルトランスフォーメーション(DX)の実現を目指す請負開発型のコンサルティングサービスです。AI、iPaaS、および先端の技術を駆使して、製造プロセスの効率化、業務効率化、チームワーク強化、コスト削減、品質向上を実現します。このサービスは、製造業の課題を深く理解し、それに対する最適なデジタルソリューションを提供することで、企業が持続的な成長とイノベーションを達成できるようサポートします。
オンライン講座
製造業、主に購買・調達部門にお勤めの方々に向けた情報を配信しております。
新任の方やベテランの方、管理職を対象とした幅広いコンテンツをご用意しております。
お問い合わせ
コストダウンが利益に直結する術だと理解していても、なかなか前に進めることができない状況。そんな時は、newjiのコストダウン自動化機能で大きく利益貢献しよう!
(Β版非公開)