- お役立ち記事
- GD&T design method that accurately conveys the basics of geometric tolerance/tolerance design and design intent and utilizes it to improve drawing quality
GD&T design method that accurately conveys the basics of geometric tolerance/tolerance design and design intent and utilizes it to improve drawing quality
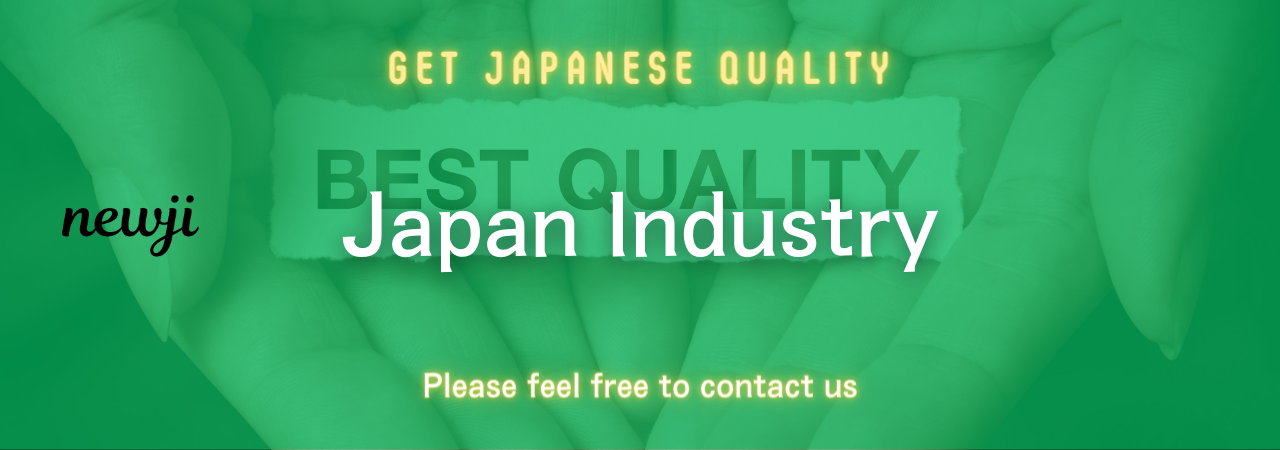
目次
Understanding GD&T and Its Importance
Geometric Dimensioning and Tolerancing (GD&T) is a system used to define and communicate engineering tolerances.
It provides a clear and concise method for describing the size, form, orientation, and location of features on an engineering drawing.
This precise communication of design intent is crucial, particularly in today’s complex manufacturing environments where precision is paramount.
By conveying the designer’s intent accurately, GD&T ensures that all features of a part or assembly meet the required specifications.
Unlike traditional dimensioning, GD&T uses a symbolic language to express geometric relationships and tolerances.
These symbols specify allowable variations in the geometry of a part, ensuring consistency and interchangeability in production.
As a result, GD&T plays a vital role in reducing ambiguity and enhancing the quality of engineering drawings.
The Basics of Geometric Tolerance
At its core, geometric tolerance defines the acceptable limits of variation in a feature’s geometry.
GD&T breaks down these tolerances into several categories: form, orientation, location, and runout.
Form Tolerances
Form tolerances deal with the shape of features and include flatness, straightness, circularity, and cylindricity.
These tolerances ensure that a feature’s shape stays within specified boundaries.
For example, flatness ensures that a surface lies within two parallel planes and does not deviate excessively from a flat plane.
Orientation Tolerances
Orientation tolerances control the tilting of features, and include perpendicularity, angularity, and parallelism.
These tolerances ensure that features are aligned correctly with reference to other features.
Perpendicularity, for instance, ensures that a surface is at a right angle to a datum.
Location Tolerances
Location tolerances specify the exact position of a feature and include position, concentricity, and symmetry.
These tolerances are crucial in ensuring that features are located in the correct place on a part.
Position tolerance, for example, considers the location, size, and orientation of a feature within allowable limits.
Runout Tolerances
Runout tolerances address the deviation of a feature when revolving around a datum axis.
They include circular runout and total runout.
These tolerances are important in parts requiring precision rotation, such as shafts or bearings.
Design Intent and GD&T
One of the main advantages of GD&T is its ability to convey design intent with clarity and precision.
By using GD&T, designers can explicitly state the functional requirements of a part and its relationship with other parts.
This clarity helps avoid costly production errors and ensures that all stakeholders, including engineers, machinists, and quality control personnel, are aligned on project requirements.
Defining design intent with GD&T involves specifying what is critical to the function and performance of the part.
This involves selecting appropriate datums, tolerances, and features based on their impact on the part’s role in an assembly.
For example, if a feature must fit snugly with a mating part, precise position tolerancing can ensure interchangeable parts during manufacturing.
Improving Drawing Quality with GD&T
With GD&T, engineering drawings are improved by providing unambiguous specifications, minimizing assumptions and interpretation errors.
This precision in communication leads to higher manufacturing efficiency and product quality.
One of the key benefits is increased consistency across the production process.
By setting clear geometric boundaries, GD&T ensures that parts can be produced time and time again within the specified tolerances, even when made in different facilities.
This consistency reduces the risk of rework and defects, leading to cost savings and a shorter time-to-market.
Moreover, by accurately defining the geometric tolerances, GD&T facilitates better quality control.
Inspection procedures are streamlined as GD&T provides the parameters for measurement and tolerance checks.
This results in improved inspection efficiency and reliability, as inspectors have a clear understanding of what is required.
Benefits of Implementing GD&T in Design
Implementing GD&T in the design process has several noteworthy advantages.
Firstly, it enhances communication among all stakeholders by providing a universal language for defining geometric attributes.
This reduces misunderstandings and ensures that everyone involved in the design and manufacturing processes is on the same page.
Additionally, GD&T allows for greater design flexibility.
Designers can specify which features are critical and which have greater allowable variations, optimizing material usage and cost.
This flexibility can lead to innovative designs that maintain functionality while reducing production expenses.
Furthermore, GD&T improves overall product quality.
By defining and controlling the geometric aspects of a design, it helps in achieving higher precision and reliability in the final product.
This quality assurance is essential in heavily regulated industries like aerospace and automotive, where safety and performance are non-negotiable.
Conclusion
The GD&T design method is integral in conveying geometric tolerance and design intent accurately.
By leveraging the systematic and standardized approach of GD&T, engineers and manufacturers can significantly improve the quality of engineering drawings and the parts they produce.
Understanding and implementing GD&T effectively not only enhances communication and consistency but also drives cost efficiency and innovation in product design.
For those in the engineering and manufacturing sectors, mastering GD&T is essential for maintaining a competitive edge and delivering high-quality products that meet the rigorous demands of today’s market.
資料ダウンロード
QCD調達購買管理クラウド「newji」は、調達購買部門で必要なQCD管理全てを備えた、現場特化型兼クラウド型の今世紀最高の購買管理システムとなります。
ユーザー登録
調達購買業務の効率化だけでなく、システムを導入することで、コスト削減や製品・資材のステータス可視化のほか、属人化していた購買情報の共有化による内部不正防止や統制にも役立ちます。
NEWJI DX
製造業に特化したデジタルトランスフォーメーション(DX)の実現を目指す請負開発型のコンサルティングサービスです。AI、iPaaS、および先端の技術を駆使して、製造プロセスの効率化、業務効率化、チームワーク強化、コスト削減、品質向上を実現します。このサービスは、製造業の課題を深く理解し、それに対する最適なデジタルソリューションを提供することで、企業が持続的な成長とイノベーションを達成できるようサポートします。
オンライン講座
製造業、主に購買・調達部門にお勤めの方々に向けた情報を配信しております。
新任の方やベテランの方、管理職を対象とした幅広いコンテンツをご用意しております。
お問い合わせ
コストダウンが利益に直結する術だと理解していても、なかなか前に進めることができない状況。そんな時は、newjiのコストダウン自動化機能で大きく利益貢献しよう!
(Β版非公開)