- お役立ち記事
- Generic Drug Manufacturing Process and Quality Control
Generic Drug Manufacturing Process and Quality Control
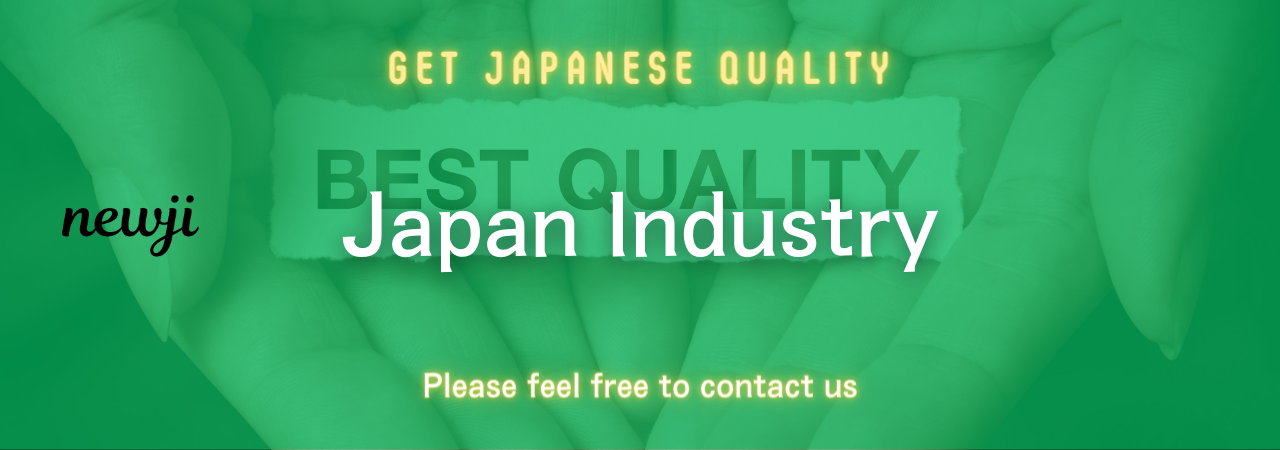
Generic drugs play a significant role in healthcare by providing affordable medication alternatives to brand-name drugs.
They help millions of people gain access to necessary treatments without the high costs often associated with branded medications.
Understanding the generic drug manufacturing process and how quality control is maintained can give us confidence in these cost-effective solutions.
目次
What Are Generic Drugs?
Generic drugs are medications that have the same active ingredients, strength, dosage form, and route of administration as their brand-name counterparts.
However, they are usually sold at a lower price.
Once the patent protection on a brand-name drug expires, other manufacturers can produce and sell the generic version.
These generics must meet the same strict standards of quality, safety, and efficacy set by regulatory authorities such as the Food and Drug Administration (FDA) in the United States.
The Manufacturing Process of Generic Drugs
The process of manufacturing generic drugs is intricate and heavily regulated.
Let’s break down the main stages involved:
Research and Development (R&D)
Before a generic drug reaches the market, considerable research and development are required.
This phase involves:
– Identifying the Brand-Name Drug’s Composition: Scientists analyze the brand-name drug’s formulation to replicate its active ingredients and properties accurately.
– Conducting Preclinical Studies: Preliminary tests are performed to evaluate the generic version’s safety and effectiveness.
– Formulation Development: Researchers work on creating a solid, liquid, or other forms of the generic drug to match the original drug precisely.
Raw Material Sourcing
Raw materials used in the production of generic drugs must meet stringent quality standards.
Manufacturers source active pharmaceutical ingredients (APIs) and excipients (inactive substances) from reputable suppliers.
These ingredients undergo rigorous testing to ensure their purity, potency, and compliance with regulatory guidelines.
Manufacturing and Production
Once the raw materials are approved, they are moved to the manufacturing stage.
This phase includes several critical steps:
– Weighing and Measuring: Precise amounts of APIs and excipients are weighed and measured to ensure consistency in the final product.
– Mixing and Blending: The raw materials are mixed and blended using advanced equipment to create a uniform composition.
– Granulation: In many cases, the mixture undergoes granulation to form granules, which aid in producing tablets or capsules.
– Compression and Encapsulation: Granules are compressed into tablets or encapsulated into capsules.
– Coating: Some tablets receive a coating to enhance their stability, appearance, or taste.
– Packaging: The final products are packaged in appropriate containers, such as blister packs, bottles, or boxes, to protect them from environmental factors.
Quality Control in Generic Drug Manufacturing
Quality control (QC) is a critical component of generic drug manufacturing.
It ensures that each batch of medication meets the required standards for safety, efficacy, and quality.
The QC process involves several layers of inspection and testing:
In-Process Quality Control
During the manufacturing process, various in-process quality control tests are conducted.
These checks help to identify and rectify any issues early on.
Common in-process QC measures include:
– Uniformity Testing: Ensuring that each tablet or capsule contains the correct amount of active ingredient.
– Dissolution Testing: Checking how quickly the active ingredient dissolves in the body to ensure proper absorption.
– Weight Variation: Verifying that the weight of tablets or capsules remains consistent across the batch.
– Hardness and Friability Testing: Assessing the strength and durability of the tablets.
Finished Product Testing
After manufacturing, finished products go through rigorous testing to confirm their quality.
Key finished product tests include:
– Chemical Analysis: Measuring the concentration of active ingredients to ensure they fall within the specified range.
– Microbial Testing: Screening for microbial contamination to guarantee the product’s safety.
– Stability Testing: Evaluating how the product holds up under different environmental conditions over time.
Regulatory Compliance and Approval
Before a generic drug can be marketed, it must receive approval from regulatory authorities.
This involves submitting an Abbreviated New Drug Application (ANDA) to organizations like the FDA.
The ANDA includes comprehensive data on the drug’s formulation, manufacturing process, and quality control measures.
Regulatory authorities carefully review the application, conducting inspections and audits to ensure compliance with all standards.
Once approved, the generic drug can be manufactured and distributed for consumer use.
Maintaining Continuous Quality Control
Even after a generic drug is approved and on the market, manufacturers must maintain ongoing quality control practices.
This ensures that every batch produced continues to meet the high standards required.
Regular audits, inspections, and monitoring of production facilities help identify and address any potential issues.
Manufacturers often implement good manufacturing practices (GMP) to guide their production and quality control processes.
These practices involve detailed protocols and guidelines for every stage of the manufacturing process.
Conclusion
The manufacturing process and quality control measures for generic drugs are comprehensive and stringent.
From initial research and development to raw material sourcing, production, and final product testing, every step is designed to ensure the safety, efficacy, and quality of generic medications.
Understanding these processes can give us confidence in the reliability of generic drugs as affordable alternatives to brand-name medications.
Next time you pick up a generic prescription, you can be assured that it has undergone thorough scrutiny to meet the highest standards in pharmaceutical manufacturing.
資料ダウンロード
QCD調達購買管理クラウド「newji」は、調達購買部門で必要なQCD管理全てを備えた、現場特化型兼クラウド型の今世紀最高の購買管理システムとなります。
ユーザー登録
調達購買業務の効率化だけでなく、システムを導入することで、コスト削減や製品・資材のステータス可視化のほか、属人化していた購買情報の共有化による内部不正防止や統制にも役立ちます。
NEWJI DX
製造業に特化したデジタルトランスフォーメーション(DX)の実現を目指す請負開発型のコンサルティングサービスです。AI、iPaaS、および先端の技術を駆使して、製造プロセスの効率化、業務効率化、チームワーク強化、コスト削減、品質向上を実現します。このサービスは、製造業の課題を深く理解し、それに対する最適なデジタルソリューションを提供することで、企業が持続的な成長とイノベーションを達成できるようサポートします。
オンライン講座
製造業、主に購買・調達部門にお勤めの方々に向けた情報を配信しております。
新任の方やベテランの方、管理職を対象とした幅広いコンテンツをご用意しております。
お問い合わせ
コストダウンが利益に直結する術だと理解していても、なかなか前に進めることができない状況。そんな時は、newjiのコストダウン自動化機能で大きく利益貢献しよう!
(Β版非公開)