- お役立ち記事
- Geometric Tolerance Design Method Correct use of geometric tolerances to create mechanical design drawings and its key points
月間77,185名の
製造業ご担当者様が閲覧しています*
*2025年2月28日現在のGoogle Analyticsのデータより
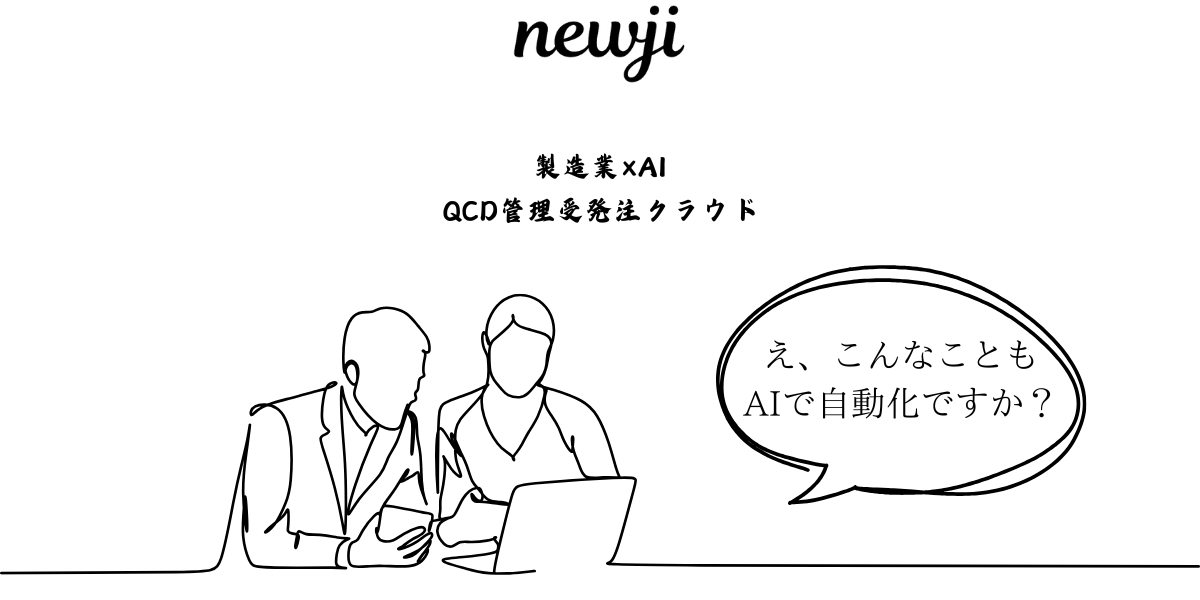
Geometric Tolerance Design Method Correct use of geometric tolerances to create mechanical design drawings and its key points
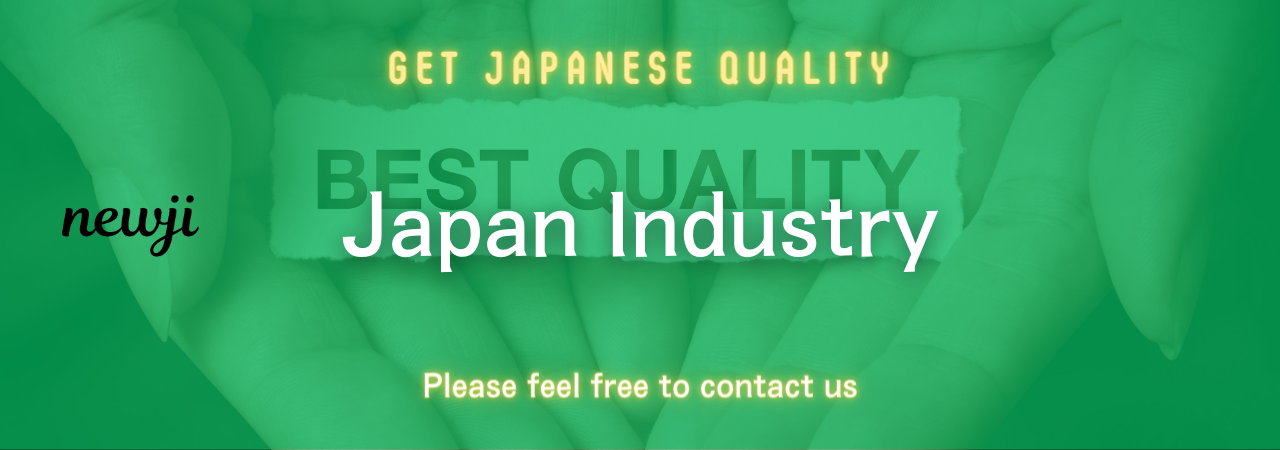
目次
Understanding Geometric Tolerances
Geometric tolerances are a crucial aspect of mechanical design drawings.
They provide specific guidelines to ensure parts fit and function together as intended.
By specifying geometric tolerances, designers communicate the allowable variations in the shapes and positions of features on a part.
These elements impact the part’s manufacturability, assembly, and functionality.
The geometric tolerancing system was standardized to provide consistency across industries.
This system helps to describe the form, orientation, and location relationships of part features.
When applied correctly, geometric tolerances ensure that manufactured parts meet design specifications, reducing production issues and ensuring quality.
Key Aspects of Geometric Tolerances
To apply geometric tolerances effectively, it’s vital to grasp several key aspects.
Feature Control Frames
Feature control frames are the centerpiece of geometric tolerancing.
These frames contain the symbols and values needed to specify a particular tolerance.
A typical feature control frame includes the geometric characteristic symbol, tolerance value, and datum references.
These symbols standardize communication, ensuring that every engineer and machinist interprets the drawing consistently.
Datum Reference Frames
Datums are theoretical and invisible planes, lines, or points on an object that serve as a reference for measuring other features.
They provide a ‘zero’ point from which other dimensional measurements are made.
Datum reference frames ensure that components align properly during assembly.
Geometric Characteristic Symbols
These are symbols used in feature control frames to describe geometric tolerances.
Common symbols include flatness, perpendicularity, parallelism, angularity, and roundness.
Each symbol provides specific control over a feature’s geometry, ensuring it fits within acceptable limits.
Material Condition Modifiers
Material condition modifiers, such as Maximum Material Condition (MMC) and Least Material Condition (LMC), are used to specify conditions under which geometric tolerances apply.
They help balance manufacturing costs with functional performance, providing greater flexibility in design.
Benefits of Using Geometric Tolerances
Applying geometric tolerances offers significant advantages to manufacturers and designers.
Enhanced Clarity and Communication
Geometric tolerances eliminate ambiguity in design drawings.
They ensure that everyone involved understands the specifications and requirements, reducing the possibility of costly errors during production.
Improved Part Fit and Function
By precisely defining the permissible limits of part features, geometric tolerances ensure that parts assemble easily and function as intended.
This reduces assembly time and increases product reliability and performance.
Cost-Effective Production
With clear tolerancing, manufacturers can minimize rework and scrap, optimizing the production process.
This efficiency reduces material waste and operational costs, contributing significantly to the bottom line.
Enhanced Quality Assurance
Geometric tolerances provide measurable criteria for quality assurance.
They help detect deviations early in the production process, allowing for quality control measures to be implemented.
Steps for Correct Use of Geometric Tolerances
Employing geometric tolerances properly involves several structured steps.
Determine Functional Requirements
Begin by identifying the essential functional requirements of the part or assembly.
Understanding how the part will interact with other components sets the stage for defining appropriate tolerances.
Select Critical Features
Once functional requirements are clear, determine which features are critical to those functions.
These features will often require tighter tolerances to ensure reliability and performance.
Assign Appropriate Tolerances
For each critical feature, determine the geometric tolerance that will best control its shape, size, and position.
Consider both the functional needs and manufacturing capabilities.
Consider Datum Features
Identify appropriate datums for your design, considering how parts will orient and interact during assembly.
Ensure that datum selection reflects functional priorities and simplifies the measurement process.
Simulate and Validate
Before finalizing your design, simulate assembly and function to ensure that tolerances provide the desired fit and performance.
Validation helps identify potential issues before manufacturing begins, saving time and resources.
Common Pitfalls and How to Avoid Them
Understanding common mistakes in geometric tolerance design can prevent issues.
Over-Tolerancing
One frequent mistake is applying too-tight tolerances to non-critical features.
This can drive up manufacturing costs without adding value.
Focus on the critical features and apply reasonable tolerances to non-critical areas.
Ignoring Manufacturing Capabilities
Designers sometimes fail to communicate with manufacturing teams, leading to tolerances that aren’t feasible.
Collaboration ensures that design specifications align with production capabilities.
Poor Datum Selection
Inappropriate datum choices can complicate assembly and inspection.
Select datums that logically relate to how the part will function and fit within the assembly.
Incomplete Tolerances
Avoid leaving features without necessary tolerances, as this can result in parts that do not meet functional needs.
Comprehensive tolerancing ensures that all aspects of a part’s design are controlled.
Conclusion
Geometric tolerances are critical for translating design intent into tangible, functional products.
By understanding the principles of geometric tolerances, using effective feature control frames, and involving all stakeholders in the design process, designs can achieve intended functionality and quality, paving the way for successful manufacturing outcomes.
Through careful planning and execution, geometric tolerances optimize both product performance and production efficiency.
資料ダウンロード
QCD管理受発注クラウド「newji」は、受発注部門で必要なQCD管理全てを備えた、現場特化型兼クラウド型の今世紀最高の受発注管理システムとなります。
ユーザー登録
受発注業務の効率化だけでなく、システムを導入することで、コスト削減や製品・資材のステータス可視化のほか、属人化していた受発注情報の共有化による内部不正防止や統制にも役立ちます。
NEWJI DX
製造業に特化したデジタルトランスフォーメーション(DX)の実現を目指す請負開発型のコンサルティングサービスです。AI、iPaaS、および先端の技術を駆使して、製造プロセスの効率化、業務効率化、チームワーク強化、コスト削減、品質向上を実現します。このサービスは、製造業の課題を深く理解し、それに対する最適なデジタルソリューションを提供することで、企業が持続的な成長とイノベーションを達成できるようサポートします。
製造業ニュース解説
製造業、主に購買・調達部門にお勤めの方々に向けた情報を配信しております。
新任の方やベテランの方、管理職を対象とした幅広いコンテンツをご用意しております。
お問い合わせ
コストダウンが利益に直結する術だと理解していても、なかなか前に進めることができない状況。そんな時は、newjiのコストダウン自動化機能で大きく利益貢献しよう!
(β版非公開)