- お役立ち記事
- German Precision Meets Japanese Innovation: A Deep Dive into Advanced Plastic Processing Techniques
German Precision Meets Japanese Innovation: A Deep Dive into Advanced Plastic Processing Techniques
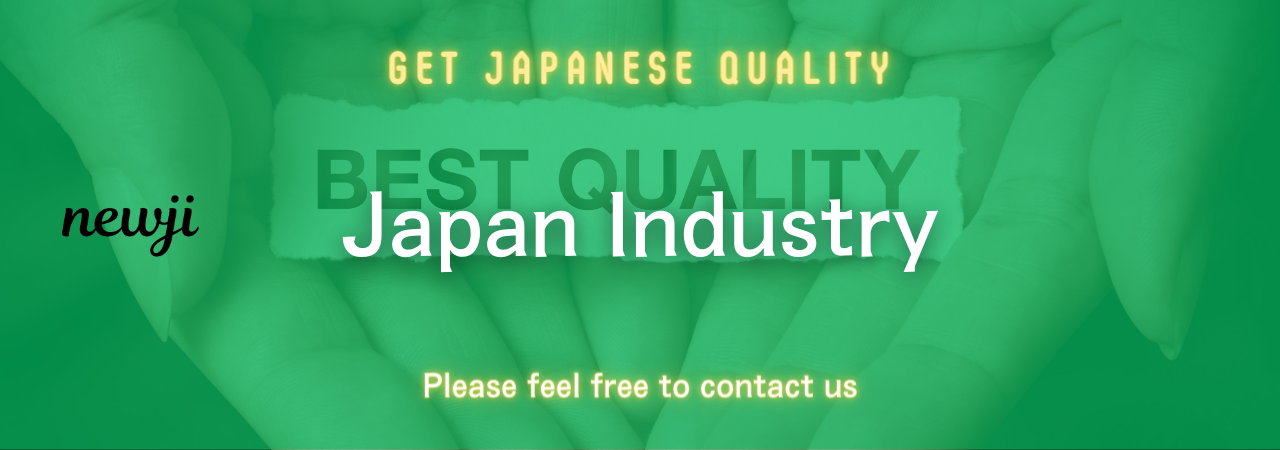
目次
Introduction
Plastic processing is a critical aspect of modern manufacturing, and the convergence of German and Japanese methodologies offers a unique blend of precision and innovation.
The synergy between German precision engineering and Japanese innovative approaches to manufacturing can lead to significant advancements in plastic processing techniques.
This article will explore various facets of plastic processing, from procurement and purchasing to supplier negotiation techniques and market conditions, emphasizing the best practices to maximize efficiency and quality.
Understanding German Precision in Plastic Processing
Core Principles of German Engineering
German engineering is renowned for its attention to detail and stringent quality control.
The core principles revolve around precision, reliability, and meticulous planning.
In plastic processing, these principles translate into systems that minimize waste, enhance accuracy, and ensure consistent product quality.
Key Techniques in German Plastic Processing
One of the most famous techniques involves the use of high-precision molds.
These molds are crafted to exact specifications, ensuring that every plastic part produced fits precisely within its designated tolerances.
Another technique is the use of advanced extrusion technologies, which allow for the creation of complex shapes with high precision and minimal material wastage.
The Innovation Behind Japanese Plastic Processing
Emphasis on Continuous Improvement
Japanese plastic processing techniques are deeply rooted in the philosophy of Kaizen, which means continuous improvement.
This approach focuses on incremental changes that enhance productivity and quality over time, rather than sweeping changes.
Adoption of Advanced Technologies
Japanese manufacturers are quick to adopt and refine cutting-edge technologies.
For instance, the use of robotic automation in plastic injection molding is widespread, ensuring high-speed production without compromising on quality.
Advanced monitoring systems are also employed to track real-time data, enabling immediate adjustments to the production process to maintain optimal conditions.
The Benefits of Combining German and Japanese Techniques
Enhanced Precision and Efficiency
By integrating German precision with Japanese innovation, manufacturers can achieve higher levels of efficiency and accuracy.
The meticulous planning and quality control standards of German engineering, when combined with the innovative and adaptive strategies of Japanese manufacturing, create robust processes that minimize defects and maximize output.
Cost-Effectiveness
While the initial investment in high-precision equipment and advanced technologies may be substantial, the long-term benefits include reduced material waste, lower labor costs due to automation, and fewer defective products.
This results in a more cost-effective production process.
Challenges and Disadvantages
Initial Investment and Training
One of the significant challenges is the high initial cost associated with acquiring advanced German and Japanese equipment.
Additionally, the workforce must be adequately trained to operate and maintain these sophisticated systems, which can result in increased upfront costs and time delays.
Cultural Differences
While the combination of German and Japanese methodologies can be beneficial, cultural differences in business practices and communication can pose challenges.
For instance, the German focus on detailed planning and documentation may clash with the Japanese emphasis on practical, on-the-ground problem-solving.
Effective Supplier Negotiation Techniques
Building Long-Term Relationships
Both German and Japanese cultures emphasize the importance of long-term relationships in business.
When negotiating with suppliers, focus on building trust and demonstrating a commitment to a mutually beneficial partnership.
This approach can lead to better terms and more reliable service.
Leveraging Market Knowledge
Stay informed about market conditions and trends.
Having up-to-date knowledge about material costs, technological advancements, and industry standards can give you leverage in negotiations.
For example, if you know that a particular type of plastic is experiencing a price drop, you can use this information to negotiate better pricing.
Technical Expertise
Demonstrating a deep technical understanding of plastic processing can also be advantageous.
Suppliers are more likely to respect and accommodate the requirements of a well-informed buyer who can speak their language and understand the complexities involved.
Market Conditions and Trends
Global Supply Chain Dynamics
The plastic processing industry is heavily influenced by global supply chain dynamics.
Factors such as raw material availability, transportation costs, and geopolitical issues can impact the availability and pricing of plastic materials.
Technological Advancements
Continuous advancements in technology are shaping the market.
For instance, developments in biodegradable plastics and sustainable manufacturing practices are creating new opportunities and challenges.
Staying abreast of these trends can help manufacturers remain competitive and adapt to changing market demands.
Best Practices for Procurement and Purchasing
Comprehensive Supplier Evaluation
Before committing to a supplier, conduct a thorough evaluation of their capabilities, including their technical expertise, production capacity, and quality control measures.
Site visits and audits can provide valuable insights into their operations and ensure they meet your standards.
Clear Specifications and Standards
Provide suppliers with detailed specifications and quality standards for your plastic processing needs.
This clarity helps avoid misunderstandings and ensures that the supplied materials or components meet your requirements.
Emphasize Quality Control
Implement stringent quality control measures at every stage of procurement and purchasing.
From the initial selection of raw materials to the final inspection of finished products, maintaining high standards ensures consistency and reduces defects.
Conclusion
The combination of German precision and Japanese innovation in plastic processing offers a powerful formula for success in modern manufacturing.
While there are challenges and initial investments involved, the long-term benefits of enhanced efficiency, higher-quality products, and cost-effectiveness make it a worthwhile endeavor.
By implementing best practices in procurement and purchasing, leveraging effective supplier negotiation techniques, and staying informed about market conditions and trends, manufacturers can fully harness the advantages of advanced plastic processing techniques to stay ahead in the competitive landscape.
資料ダウンロード
QCD調達購買管理クラウド「newji」は、調達購買部門で必要なQCD管理全てを備えた、現場特化型兼クラウド型の今世紀最高の購買管理システムとなります。
ユーザー登録
調達購買業務の効率化だけでなく、システムを導入することで、コスト削減や製品・資材のステータス可視化のほか、属人化していた購買情報の共有化による内部不正防止や統制にも役立ちます。
NEWJI DX
製造業に特化したデジタルトランスフォーメーション(DX)の実現を目指す請負開発型のコンサルティングサービスです。AI、iPaaS、および先端の技術を駆使して、製造プロセスの効率化、業務効率化、チームワーク強化、コスト削減、品質向上を実現します。このサービスは、製造業の課題を深く理解し、それに対する最適なデジタルソリューションを提供することで、企業が持続的な成長とイノベーションを達成できるようサポートします。
オンライン講座
製造業、主に購買・調達部門にお勤めの方々に向けた情報を配信しております。
新任の方やベテランの方、管理職を対象とした幅広いコンテンツをご用意しております。
お問い合わせ
コストダウンが利益に直結する術だと理解していても、なかなか前に進めることができない状況。そんな時は、newjiのコストダウン自動化機能で大きく利益貢献しよう!
(Β版非公開)