- お役立ち記事
- Ghosting Causes and Solutions in Manufacturing
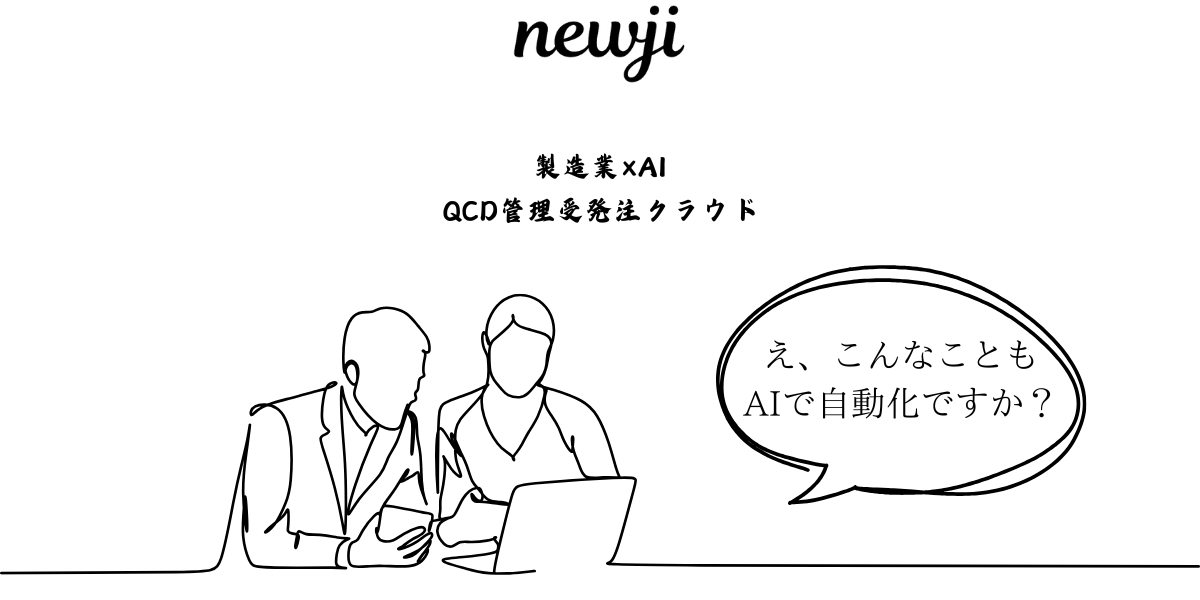
Ghosting Causes and Solutions in Manufacturing
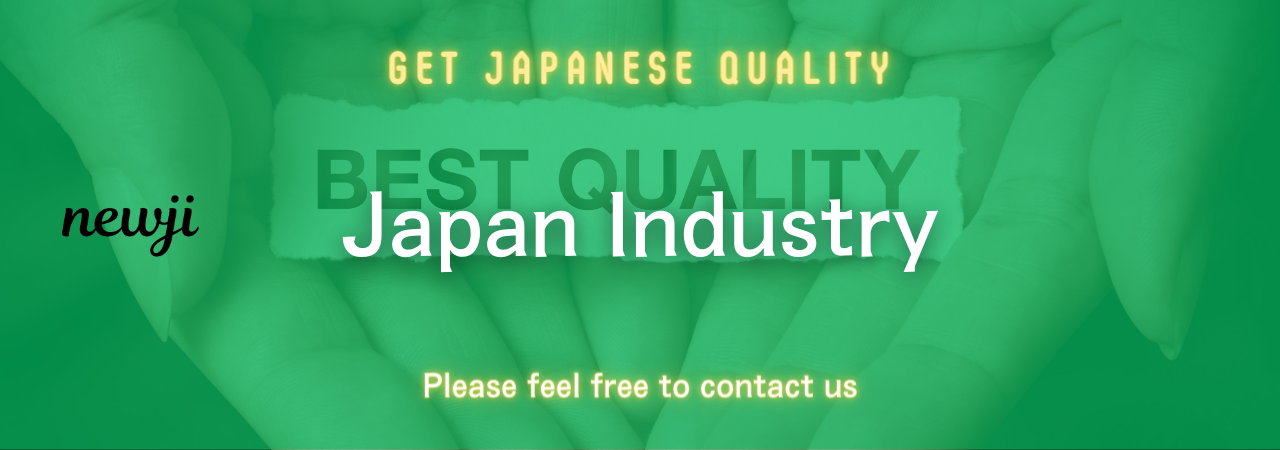
In today’s manufacturing world, ghosting can create significant problems.
Understanding what ghosting is, why it happens, and how to solve it can help keep operations running smoothly.
Let’s dive in to uncover the mysteries behind ghosting in manufacturing.
目次
What is Ghosting in Manufacturing?
Ghosting in manufacturing refers to unintended marks, patterns, or residual images that appear on a product’s surface.
These marks can be quite troubling, especially when the final product needs to have a pristine and uniform appearance.
Ghosting can occur during various stages of manufacturing, and identifying its roots is crucial for quality control.
Common Causes of Ghosting
Improper Temperature Control
One of the most frequent causes of ghosting is improper temperature management.
If machinery or materials are not maintained within optimal temperature ranges, it can lead to uneven cooling and unwanted marks.
Proper temperature regulation can mitigate this issue significantly.
Dust and Contaminants
Another common culprit is the presence of dust and contaminants.
Foreign particles on the production line can transfer to the surface of the product, leading to ghosting.
Ensuring a clean manufacturing environment is essential, involving regular cleaning protocols and proper air filtration systems.
Incorrect Pressure Settings
Pressure settings play a vital role in many manufacturing processes.
Incorrect pressure can cause materials to adhere excessively or insufficiently, resulting in ghosting.
Regular calibration and maintenance of equipment ensure that pressure settings remain within the required thresholds.
Poor Quality Raw Materials
The quality of raw materials used in production can impact the likelihood of ghosting.
Substandard materials often have inconsistencies that contribute to unwanted marks.
Using high-quality materials and establishing rigorous quality checks can help prevent this issue.
Solutions to Ghosting in Manufacturing
Regular Equipment Maintenance
Maintaining equipment regularly is essential.
Consistent checks and service ensure that machines operate within their designated parameters.
This can prevent issues like temperature fluctuations, incorrect pressure, and more, reducing the risk of ghosting.
Streamlining Quality Control
Implementing stringent quality control measures at various stages of production helps catch and mitigate ghosting before the product reaches the final stage.
This might include visual inspections, automated detection systems, and rigorous testing protocols.
Investing in Clean Manufacturing Environments
A clean manufacturing environment minimizes the risk of contaminants leading to ghosting.
This involves not just cleaning surfaces but also having effective air filtration systems in place to reduce airborne particles.
Maintaining cleanliness ensures that the environment does not contribute to ghosting issues.
Training and Workforce Education
Ensuring that all personnel are adequately trained in recognizing and preventing ghosting can make a significant difference.
Training programs should include identification of ghosting causes, as well as steps to prevent and address these issues.
Advanced Solutions
Using Coatings and Shielding Technologies
Advanced coatings and shielding technologies can help prevent ghosting.
Coatings can create a protective layer that reduces the likelihood of marks forming, while shielding technologies can protect sensitive materials from contaminants.
Automation and Precision Controls
Integrating automation and precision control systems can enhance accuracy and consistency in production processes.
Automated systems can regulate pressure, temperature, and other critical factors with high precision, thereby reducing the risk of ghosting.
Data Analytics and Predictive Maintenance
Leveraging data analytics helps predict when and where ghosting might occur.
By analyzing trends and patterns in the production process, manufacturers can take proactive measures to address potential issues before they become problematic.
Predictive maintenance also ensures that equipment operates optimally.
The Importance of Addressing Ghosting
Ghosting can lead to product defects and unsatisfied customers.
It can tarnish a brand’s reputation and result in financial losses due to production delays or returns.
Taking measures to prevent and resolve ghosting keeps production smooth, maintains product quality, and ensures customer satisfaction.
Addressing ghosting reflects a commitment to quality and operational efficiency.
Final Thoughts
Ghosting in manufacturing can be a significant challenge, but understanding its causes and implementing effective solutions can mitigate this issue.
From maintaining proper temperature control to leveraging advanced technologies, there are many strategies manufacturers can use to prevent ghosting.
By staying vigilant and proactive, manufacturers can ensure high-quality output and continued success in their operations.
Understanding and tackling ghosting is essential for a smooth and efficient manufacturing process.
Applying the solutions discussed will not only improve product quality but also enhance overall operational efficiency.
Remember, the goal is to produce flawless products that satisfy customers and uphold the reputation of your manufacturing process.
資料ダウンロード
QCD調達購買管理クラウド「newji」は、調達購買部門で必要なQCD管理全てを備えた、現場特化型兼クラウド型の今世紀最高の購買管理システムとなります。
ユーザー登録
調達購買業務の効率化だけでなく、システムを導入することで、コスト削減や製品・資材のステータス可視化のほか、属人化していた購買情報の共有化による内部不正防止や統制にも役立ちます。
NEWJI DX
製造業に特化したデジタルトランスフォーメーション(DX)の実現を目指す請負開発型のコンサルティングサービスです。AI、iPaaS、および先端の技術を駆使して、製造プロセスの効率化、業務効率化、チームワーク強化、コスト削減、品質向上を実現します。このサービスは、製造業の課題を深く理解し、それに対する最適なデジタルソリューションを提供することで、企業が持続的な成長とイノベーションを達成できるようサポートします。
オンライン講座
製造業、主に購買・調達部門にお勤めの方々に向けた情報を配信しております。
新任の方やベテランの方、管理職を対象とした幅広いコンテンツをご用意しております。
お問い合わせ
コストダウンが利益に直結する術だと理解していても、なかなか前に進めることができない状況。そんな時は、newjiのコストダウン自動化機能で大きく利益貢献しよう!
(Β版非公開)