- お役立ち記事
- Glass Bottle Cap Manufacturing Process and Seal Performance Enhancement
月間77,185名の
製造業ご担当者様が閲覧しています*
*2025年2月28日現在のGoogle Analyticsのデータより
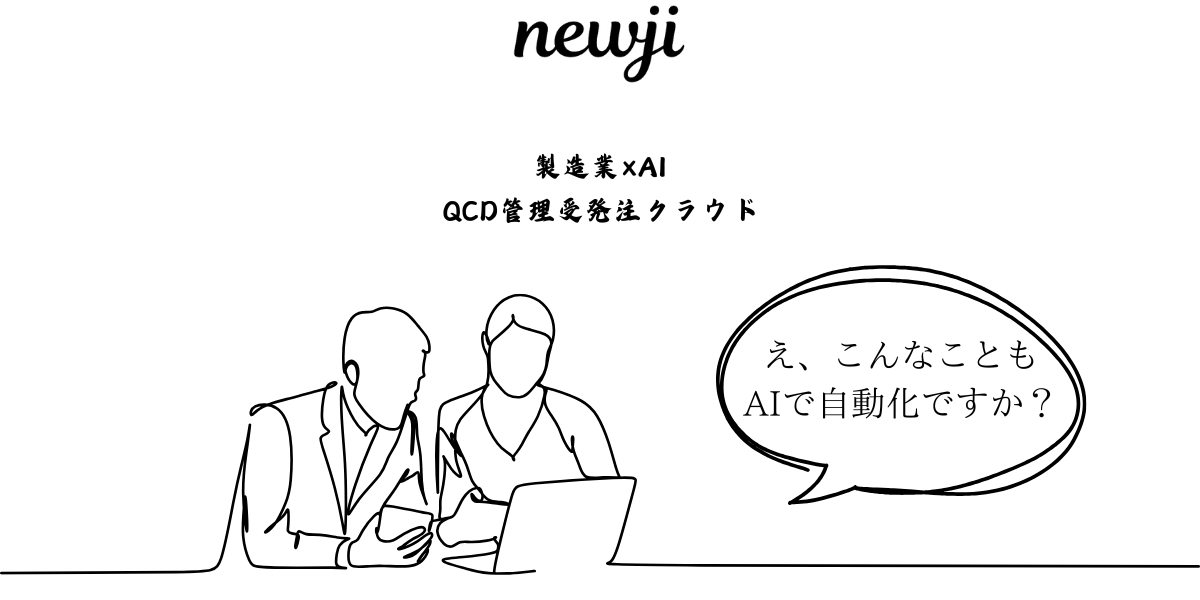
Glass Bottle Cap Manufacturing Process and Seal Performance Enhancement
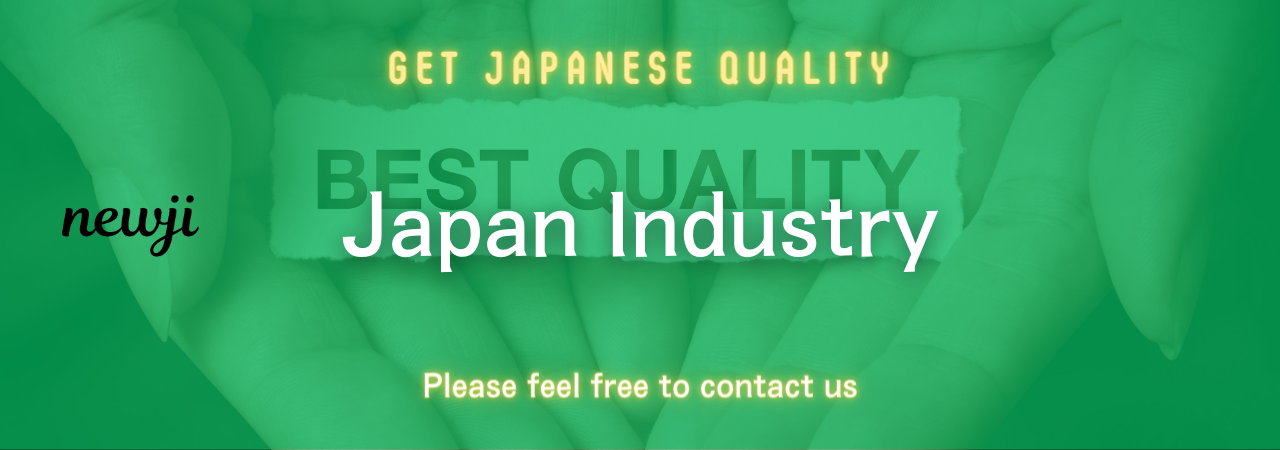
目次
Introduction to Glass Bottle Cap Manufacturing
Glass bottle caps play an essential role in the storage and preservation of various liquids.
Whether it’s your favorite beverage, a bottle of gourmet sauce, or even pharmaceutical products, the seal of a glass bottle cap is fundamental in maintaining the integrity of the contents.
Understanding the manufacturing process and how to enhance seal performance is crucial to ensure product safety and longevity.
Materials Used in Glass Bottle Caps
Before diving into the manufacturing process, it’s important to understand the materials involved.
Typically, glass bottle caps are made from metals like aluminum or steel, sometimes coated with a polymer layer to ensure a tight seal.
The use of metal provides durability and resistance to corrosion, which are vital for maintaining a good seal over time.
There are also composite materials used to achieve a specific balance between flexibility and rigidity depending on the application of the bottle cap.
Aluminum in Bottle Cap Production
Aluminum is a popular choice for bottle caps due to its lightweight nature and resistance to rust.
It provides a good degree of flexibility, allowing it to form snugly around the bottleneck.
Furthermore, it’s recyclable, making it a sustainable option for manufacturing bottle caps.
The Manufacturing Process
The production of glass bottle caps involves several complex steps that ensure the final product is both functional and reliable.
Step 1: Material Preparation
The first phase of production involves preparing raw materials.
If aluminum or steel is being used, these metals must be cut into sheets of a specific thickness to form blanks.
This is followed by cleaning the metal sheets to remove any impurities or residues that could affect the quality of the final product.
Step 2: Cutting and Shaping
Once the materials are prepared, they are cut into smaller pieces that will be shaped into caps.
A die-cutting machine is often used to punch out round blanks from the metal sheets.
These blanks are then fed into a press machine, which shapes them into the cap form.
The process involves drawing and folding, creating a cavity for the cap’s liner and ensuring the edges are smooth and uniform.
Step 3: Adding the Liner
A critical component of cap manufacturing is adding the liner.
This liner serves as the sealing mechanism between the cap and the bottle.
Liners are typically made from plastic or rubber compounds that are pressed into the cavity of the cap.
The choice of liner material depends on the type of product that will be stored in the bottle, as it must be resistant to chemical reactions with the contents.
Step 4: Threading
For screw-on caps, threading is an essential step.
This is done using a threading machine that carefully forms the threads into the inside of the cap.
The threads ensure the cap can be securely screwed onto the bottle’s neck, forming a tight seal.
Enhancing Seal Performance
Sealing performance is critical when it comes to maintaining the freshness and safety of the bottle’s contents.
Several enhancements can ensure the seal performs optimally over time.
Choosing the Right Liner Material
The liner is the key to a good seal, so selecting the appropriate material is crucial.
For example, polyethylene liners are often used for carbonated beverages as they can withstand the pressure without losing integrity.
For chemical products, a more resistant material like PVC may be required.
Ensuring Proper Fit and Alignment
A well-manufactured cap will fit snugly on the bottle, but testing for proper fit and alignment is necessary.
Misalignment can lead to leaks or compromised seals, negating the benefits of the best liner.
Advanced manufacturing techniques, including precision threading and advanced forming processes, help achieve the perfect fit.
Quality Control
Quality control is significant in the entire manufacturing process.
Random samples of caps are usually tested for fit, pressure resistance, and chemical interactions to ensure the batch meets industry standards.
Advanced automated inspection systems can detect defects and inconsistencies, preventing faulty caps from going to market.
Future Advances in Bottle Cap Technology
As technology evolves, the bottle cap manufacturing industry continues to innovate to meet new challenges and consumer demands.
Smart Cap Innovations
The concept of smart caps is an emerging trend.
These include elements like freshness indicators and RFID tags that can provide consumers with more information about the product’s contents and condition.
Such innovations can add value to the product and provide a competitive edge to manufacturers.
Sustainability and Eco-Friendly Materials
With increasing global awareness of environmental issues, the industry is focusing more on sustainably sourced and eco-friendly materials.
Innovations such as biodegradable liners and recyclable materials are being explored to reduce the carbon footprint of bottle cap production.
Conclusion
The manufacturing process of glass bottle caps and the enhancement of seal performance are critical components in ensuring the quality and safety of bottled products.
By understanding the materials, processes, and technologies involved, manufacturers can produce more effective and sustainable bottle caps.
As consumer needs and technological advancements continue to evolve, ongoing innovation in this area will remain vital.
資料ダウンロード
QCD管理受発注クラウド「newji」は、受発注部門で必要なQCD管理全てを備えた、現場特化型兼クラウド型の今世紀最高の受発注管理システムとなります。
ユーザー登録
受発注業務の効率化だけでなく、システムを導入することで、コスト削減や製品・資材のステータス可視化のほか、属人化していた受発注情報の共有化による内部不正防止や統制にも役立ちます。
NEWJI DX
製造業に特化したデジタルトランスフォーメーション(DX)の実現を目指す請負開発型のコンサルティングサービスです。AI、iPaaS、および先端の技術を駆使して、製造プロセスの効率化、業務効率化、チームワーク強化、コスト削減、品質向上を実現します。このサービスは、製造業の課題を深く理解し、それに対する最適なデジタルソリューションを提供することで、企業が持続的な成長とイノベーションを達成できるようサポートします。
製造業ニュース解説
製造業、主に購買・調達部門にお勤めの方々に向けた情報を配信しております。
新任の方やベテランの方、管理職を対象とした幅広いコンテンツをご用意しております。
お問い合わせ
コストダウンが利益に直結する術だと理解していても、なかなか前に進めることができない状況。そんな時は、newjiのコストダウン自動化機能で大きく利益貢献しよう!
(β版非公開)