- お役立ち記事
- Global Standardization in Procurement and Purchasing Departments of Manufacturing: Unifying Processes and Sharing Best Practices
Global Standardization in Procurement and Purchasing Departments of Manufacturing: Unifying Processes and Sharing Best Practices
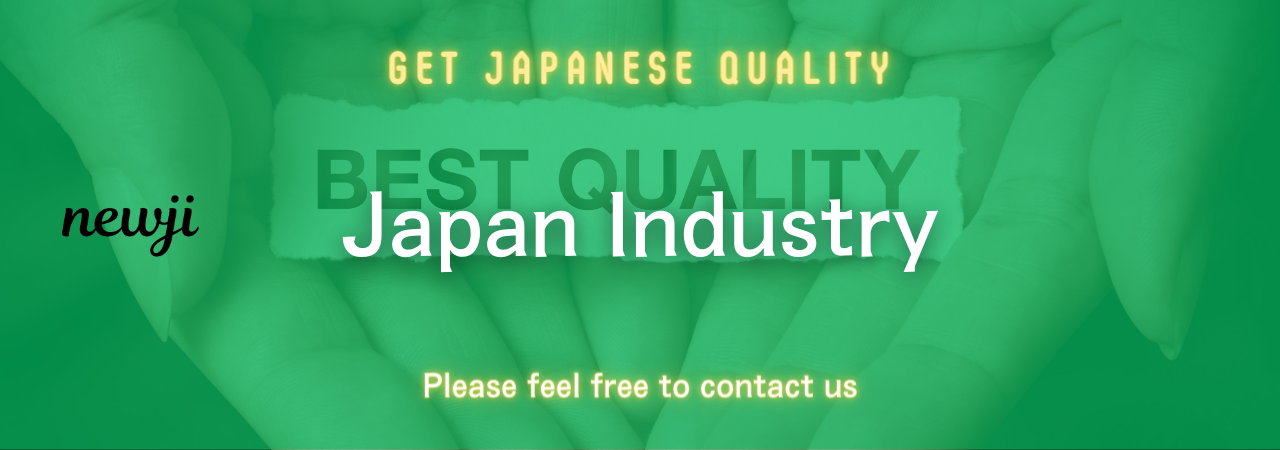
Global standardization in procurement and purchasing departments is a critical aspect of a successful manufacturing company.
By creating unified processes and sharing best practices across various locations, organizations can achieve significant cost savings, efficiency improvements, and a competitive edge in the market.
This article will explore the importance of global standardization, the benefits it brings, and practical steps to achieve it within procurement and purchasing departments in manufacturing.
目次
The Importance of Global Standardization
Global standardization involves creating a cohesive approach across different geographical regions and sites within an organization.
In the context of procurement and purchasing, it means implementing uniform procedures, policies, and strategies.
This uniformity helps to streamline operations, reduce inconsistencies, and ensure that everyone in the organization follows the same practices.
Enhanced Efficiency
Standardized processes eliminate redundant procedures and remove unnecessary complexities.
When teams across the globe follow the same protocols, it minimizes confusion and reduces the time spent on training.
This leads to smoother operations and quicker decision-making, enhancing overall efficiency.
Cost Savings
Global standardization leads to bulk purchasing and contracting, allowing companies to negotiate better deals with suppliers.
It reduces administrative costs by minimizing the need for repetitive training and process re-engineering.
Additionally, standardized processes mean fewer mistakes and, therefore, fewer costly corrections.
Quality Assurance
Consistent procurement practices ensure that suppliers meet the same quality standards, regardless of location.
This uniformity in quality control helps in maintaining the integrity of the manufacturing process and the final product.
Consequently, customers receive high-quality products consistently, bolstering the brand’s reputation.
The Benefits of Sharing Best Practices
Best practices refer to the most efficient and effective ways of completing tasks based on repeatable procedures that have been proven over time.
When these best practices are shared across procurement and purchasing departments, it can lead to further improvements in processes and operations.
Leveraging Expertise
Different regions or sites may have unique insights or innovative methods that can benefit the entire organization.
By sharing these best practices, companies can leverage the collective expertise of their global operations, fostering a culture of continuous improvement.
Consistent Supplier Management
With shared best practices, supplier management becomes more consistent.
It enables better supplier evaluation and monitoring, ensuring that only top-performing suppliers are retained.
This consistency strengthens the supply chain and ensures that quality standards are consistently met.
Risk Mitigation
By adopting proven best practices, organizations can mitigate risks associated with procurement and purchasing activities.
Shared knowledge about past pitfalls or successful strategies enables teams to avoid common mistakes, enhancing the overall risk management framework.
Steps to Achieve Global Standardization and Share Best Practices
Achieving global standardization and effectively sharing best practices require a strategic approach.
Here are practical steps to get started:
1. Conduct a Gap Analysis
Start by conducting a thorough gap analysis of your current procurement and purchasing processes across different locations.
Identify disparities and areas for improvement.
This analysis will provide a clear picture of where standardization is needed and which best practices can be implemented.
2. Develop Standard Operating Procedures (SOPs)
Create detailed Standard Operating Procedures (SOPs) for procurement and purchasing activities.
Ensure these SOPs are comprehensive and easy to understand.
They should cover all aspects of the procurement process, including supplier selection, negotiation, contracts, and quality control.
3. Implement a Centralized Procurement System
Adopt a centralized procurement system that can be accessed by teams across different locations.
This system should support collaboration, data sharing, and process monitoring.
A centralized system ensures that everyone follows the same protocols and facilitates the sharing of best practices.
4. Provide Comprehensive Training
Offer training programs to ensure that all employees understand and can effectively implement the standardized processes.
This training should cover the new SOPs, the centralized procurement system, and any best practices being introduced.
Regular refresher courses can help keep the knowledge up-to-date.
5. Monitor and Evaluate
Continuously monitor the implementation of standardized processes and the adoption of best practices.
Use Key Performance Indicators (KPIs) to measure the effectiveness of these implementations.
Regularly evaluate the processes and make adjustments as needed to ensure continuous improvement.
6. Foster a Culture of Collaboration
Encourage a culture where employees from different locations can share their insights and experiences.
Use communication tools and platforms to facilitate discussions and knowledge sharing.
Rewarding and recognizing contributions can motivate employees to engage more actively in sharing best practices.
Conclusion
Global standardization in procurement and purchasing departments within manufacturing companies is essential for achieving operational excellence.
It enhances efficiency, brings about cost savings, assures quality, and mitigates risks.
By sharing best practices, organizations can leverage collective expertise, maintain consistent supplier management, and further reduce operational risks.
Implementing a strategic plan with practical steps such as gap analysis, developing SOPs, centralized systems, comprehensive training, and fostering collaboration can lead to successful standardization and shared best practices.
Ultimately, these efforts contribute significantly to the overall success and competitiveness of the manufacturing organization in the global market.
資料ダウンロード
QCD調達購買管理クラウド「newji」は、調達購買部門で必要なQCD管理全てを備えた、現場特化型兼クラウド型の今世紀最高の購買管理システムとなります。
ユーザー登録
調達購買業務の効率化だけでなく、システムを導入することで、コスト削減や製品・資材のステータス可視化のほか、属人化していた購買情報の共有化による内部不正防止や統制にも役立ちます。
NEWJI DX
製造業に特化したデジタルトランスフォーメーション(DX)の実現を目指す請負開発型のコンサルティングサービスです。AI、iPaaS、および先端の技術を駆使して、製造プロセスの効率化、業務効率化、チームワーク強化、コスト削減、品質向上を実現します。このサービスは、製造業の課題を深く理解し、それに対する最適なデジタルソリューションを提供することで、企業が持続的な成長とイノベーションを達成できるようサポートします。
オンライン講座
製造業、主に購買・調達部門にお勤めの方々に向けた情報を配信しております。
新任の方やベテランの方、管理職を対象とした幅広いコンテンツをご用意しております。
お問い合わせ
コストダウンが利益に直結する術だと理解していても、なかなか前に進めることができない状況。そんな時は、newjiのコストダウン自動化機能で大きく利益貢献しよう!
(Β版非公開)