- お役立ち記事
- Global supplier management method to shorten procurement lead time
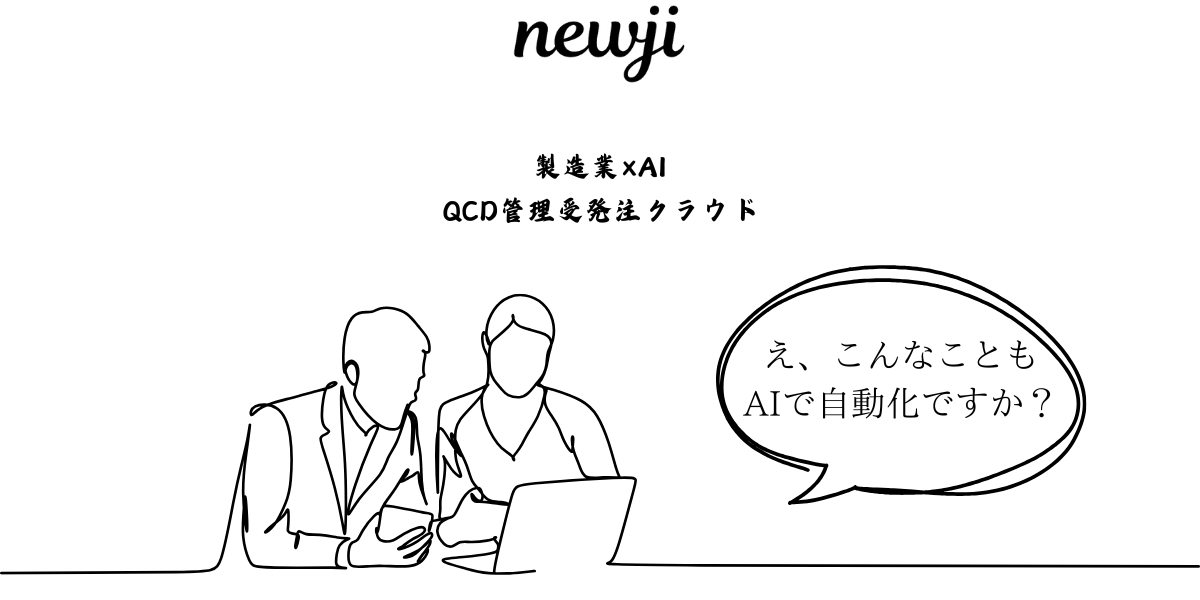
Global supplier management method to shorten procurement lead time
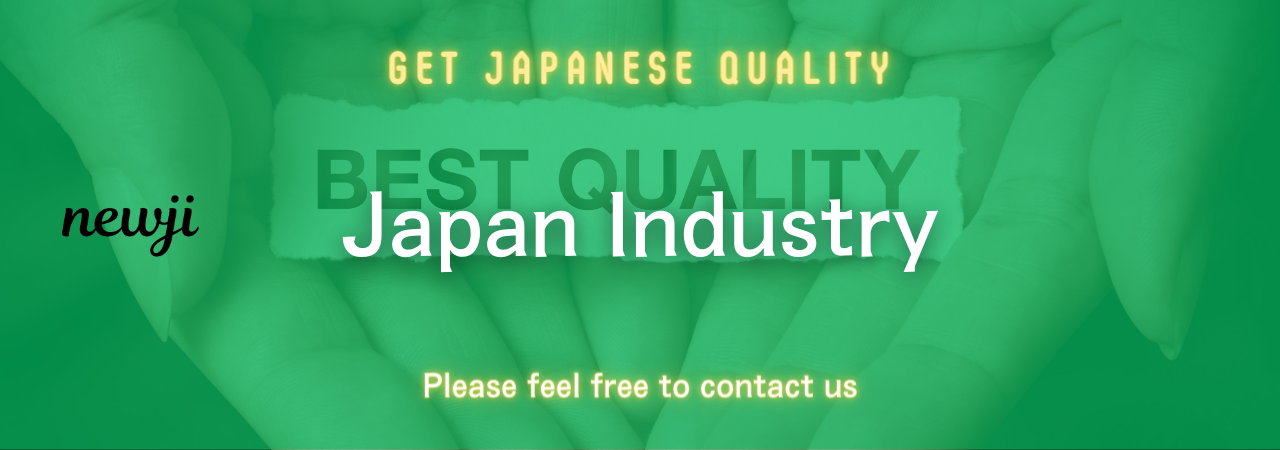
目次
Understanding Global Supplier Management
In the fast-paced world of business, managing suppliers on a global scale is more important than ever.
Global supplier management involves the coordination and oversight of suppliers located in different parts of the world.
This process ensures that businesses receive the goods and materials they need in a timely and efficient manner.
By managing suppliers effectively, companies can shorten procurement lead times, reduce costs, and improve overall supply chain efficiency.
But how exactly can businesses achieve this? Let’s explore some key strategies.
Effective Communication and Collaboration
One of the foundations of successful global supplier management is effective communication.
Companies should establish clear lines of communication with their suppliers to prevent misunderstandings and delays.
This involves setting up regular meetings, using digital communication tools, and maintaining open channels for feedback and concerns.
In addition, fostering collaboration with suppliers can lead to more innovative solutions and improved processes.
By working together, companies and suppliers can identify potential issues early and develop strategies to address them quickly.
Building Strong Relationships
Developing strong relationships with suppliers is another critical component.
Trust and mutual respect between a company and its suppliers can significantly impact procurement lead times.
When suppliers feel valued and appreciated, they are more likely to prioritize your orders and respond promptly to your needs.
To build strong relationships, it is important to show appreciation, provide regular feedback, and meet commitments consistently.
These actions help to establish a reliable partnership, which can lead to better service and quicker delivery times.
Implementing Technology Solutions
In today’s digital age, technology plays a significant role in managing global suppliers.
Many businesses are turning to technology solutions to streamline their supply chain processes and reduce lead times.
Some of the tools that companies use include supplier relationship management (SRM) systems, automated procurement software, and advanced analytics platforms.
Supplier Relationship Management Systems
SRM systems allow companies to track and analyze supplier performance.
These systems provide valuable insights into lead times, delivery schedules, and product quality.
With this information, businesses can identify areas for improvement and work with suppliers to implement changes.
SRM systems also facilitate better communication and collaboration, helping to build stronger supplier relationships.
Automated Procurement Software
Automated procurement software streamlines the ordering process by automating routine tasks such as order placement, invoicing, and payment.
This reduces the time and effort required for procurement, allowing businesses to focus on more strategic tasks.
Automation also minimizes the risk of human error, leading to more accurate orders and quicker processing times.
Advanced Analytics
Advanced analytics platforms help businesses make data-driven decisions regarding their supply chain.
By analyzing historical data, companies can predict demand patterns, identify potential bottlenecks, and optimize their inventory levels.
This information allows businesses to allocate resources more effectively, leading to shorter lead times and increased efficiency.
Strategic Sourcing and Diversification
Strategic sourcing involves selecting suppliers based on factors such as cost, quality, and delivery performance.
By working with the right suppliers, businesses can ensure that they receive high-quality products at competitive prices and within the required timeframes.
Furthermore, strategic sourcing helps companies mitigate risks associated with supply chain disruptions.
Diversification of Suppliers
Diversifying the supplier base is another strategy to shorten procurement lead times.
Relying on a single supplier can be risky, especially during unforeseen disruptions or when demand suddenly spikes.
Having multiple suppliers for the same product ensures continuity in the supply chain and provides options to meet urgent needs.
Diversification can also foster competition among suppliers, encouraging them to provide better prices and service quality.
Investing in Supplier Development
Many companies overlook the benefits of investing in supplier development.
Supplier development involves helping suppliers improve their performance and capabilities.
This can include providing training, sharing expertise, or even investing in technology upgrades.
Benefits of Supplier Development
A developed supplier is more likely to meet your requirements accurately and promptly, thus reducing lead times.
Furthermore, investing in supplier development builds stronger relationships and loyalty, resulting in a more reliable and agile supply chain.
By helping suppliers enhance their abilities, businesses can enhance their competitive edge in the market.
Conclusion
Global supplier management is a complex yet essential part of modern business operations.
Companies that master this process stand to gain a significant advantage by shortening procurement lead times and improving overall efficiency.
By focusing on effective communication, using technology, strategically sourcing suppliers, diversifying the supplier base, and investing in supplier development, businesses can optimize their supply chains for better performance.
In an ever-evolving global market, these strategies will not only boost efficiency but also drive growth and success.
資料ダウンロード
QCD調達購買管理クラウド「newji」は、調達購買部門で必要なQCD管理全てを備えた、現場特化型兼クラウド型の今世紀最高の購買管理システムとなります。
ユーザー登録
調達購買業務の効率化だけでなく、システムを導入することで、コスト削減や製品・資材のステータス可視化のほか、属人化していた購買情報の共有化による内部不正防止や統制にも役立ちます。
NEWJI DX
製造業に特化したデジタルトランスフォーメーション(DX)の実現を目指す請負開発型のコンサルティングサービスです。AI、iPaaS、および先端の技術を駆使して、製造プロセスの効率化、業務効率化、チームワーク強化、コスト削減、品質向上を実現します。このサービスは、製造業の課題を深く理解し、それに対する最適なデジタルソリューションを提供することで、企業が持続的な成長とイノベーションを達成できるようサポートします。
オンライン講座
製造業、主に購買・調達部門にお勤めの方々に向けた情報を配信しております。
新任の方やベテランの方、管理職を対象とした幅広いコンテンツをご用意しております。
お問い合わせ
コストダウンが利益に直結する術だと理解していても、なかなか前に進めることができない状況。そんな時は、newjiのコストダウン自動化機能で大きく利益貢献しよう!
(Β版非公開)