- お役立ち記事
- Grinding Techniques and Applications: Grinding Techniques for Surface Finishing and Precision
Grinding Techniques and Applications: Grinding Techniques for Surface Finishing and Precision
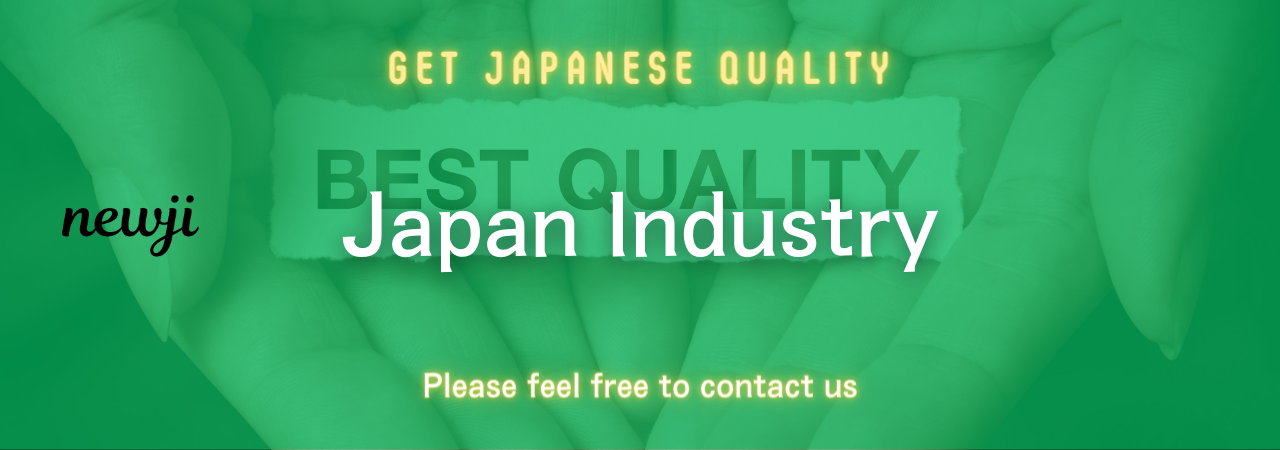
Grinding is a familiar process in various industries, ensuring that materials are cut, shaped, and smoothed to meet precise specifications and surface finishes. Whether in manufacturing, construction, or any other field requiring precise manipulation of materials, understanding grinding techniques and their applications is crucial.
目次
What is Grinding?
Grinding is a machining process that uses an abrasive wheel to remove material from a workpiece.
The primary purpose is to achieve a high level of precision and an excellent surface finish.
Grinding is especially useful for materials that are hard to machine by other methods, such as hardened steel.
The abrasive particles on the wheel’s surface cut tiny chips off the workpiece, leaving a smooth, finished surface.
Different Types of Grinding Techniques
Grinding techniques vary based on the material being worked on and the desired outcome.
Here are some of the most common types:
Surface Grinding
Surface grinding is one of the most common grinding techniques.
It is typically used to produce smooth finishes on flat surfaces.
The workpiece is held in place on a table, and a grinding wheel moves back and forth across the surface, removing small amounts of material at a time.
Centerless Grinding
Centerless grinding involves holding the workpiece without any external supports.
Instead, the workpiece is supported by a blade and rotated by a regulating wheel.
This technique is beneficial for producing high volumes of small cylindrical parts with tight tolerances.
Cylindrical Grinding
Cylindrical grinding is used to shape the exterior of an object.
The workpiece is rotated around a central axis, while a grinding wheel moves parallel to the workpiece’s axis.
This method is commonly used for precision grinding of cylindrical components such as shafts and rollers.
Internal Grinding
Internal grinding focuses on finishing the interior of a cylindrical workpiece.
The grinding wheel moves inside the hollow part, grinding it to the desired size and surface finish.
This technique is often used for parts like bearings or other hollow components.
Tool and Cutter Grinding
Tool and cutter grinding use specialized machinery to sharpen or create cutting tools.
The grinding wheel can be manipulated to produce specific shapes and angles required for various cutting applications.
This technique is vital in maintaining the accuracy and efficiency of cutting tools.
Applications of Grinding in Various Industries
Grinding techniques have widespread applications across multiple industries.
Automotive Industry
In the automotive industry, grinding is essential in producing precise components like engine parts and transmission gears.
Surface finish and dimensional accuracy are crucial to ensure the optimal performance of these components.
Aerospace Industry
The aerospace industry relies on grinding techniques to create precise parts that withstand extreme conditions.
High-tolerance components like turbine blades and landing gear parts require precise grinding for both performance and safety reasons.
Medical Field
In the medical field, grinding is used to manufacture surgical instruments and implants.
Precision and surface finish are critical, as these components often come into direct contact with human tissues.
Construction Industry
Grinding in construction mainly involves preparing surfaces for finishing or repairing worn-out structures.
Grinding ensures surfaces are smooth, clean, and ready for the next stage of construction or refurbishment.
Importance of Surface Finishing and Precision
Surface finishing and precision are fundamental aspects of grinding that contribute to the longevity and functionality of parts.
Surface Finishing
Achieving a proper surface finish is crucial for reducing friction, wear, and corrosion.
A smooth surface can improve the appearance and functionality of the workpiece.
Special attention to surface finishing is vital in applications where reduced friction is essential, such as in bearings and sliding components.
Precision
Precision in grinding ensures parts meet specific dimensional requirements, maintaining tight tolerances and ensuring proper fit and function.
Precision is necessary for applications where even a small deviation can lead to significant issues, such as in aerospace and automotive parts.
Essential Grinding Tools and Equipment
Various tools and equipment are integral to effective grinding.
Grinding Wheels
Grinding wheels come in different shapes, sizes, and materials.
They are the primary tools in grinding operations, deciding the level of precision and surface finish that can be achieved.
Wheels can be made of various abrasive materials, including aluminum oxide, silicon carbide, and diamond.
Bench Grinders
Bench grinders are versatile machines used for sharpening tools and shaping small workpieces.
They are commonly found in workshops and garages, providing a convenient means for abrasive work.
Surface Grinders
Surface grinders are specialized machines designed for producing smooth, flat surfaces.
These machines maintain both precision and finish quality, making them ideal for high-precision applications.
Cylindrical Grinders
Cylindrical grinders are used for shaping the exterior of cylindrical objects.
These machines ensure precision and are indispensable in creating shafts, rollers, and similar components.
Safety Precautions in Grinding
Safety is paramount when grinding, as the process involves high-speed abrasive wheels that can be hazardous if not handled properly.
Proper PPE (Personal Protective Equipment)
Always wear appropriate PPE, including safety glasses, gloves, and hearing protection.
This gear protects against flying debris, sparks, and loud noise.
Machine Maintenance
Regular maintenance of grinding machines is essential to ensure they function correctly and safely.
Inspect wheels for cracks or damages, and replace them if necessary.
Training
Proper training is crucial to operate grinding machines safely and effectively.
Ensure all operators understand the machine’s functions and safety procedures before starting any grinding operation.
In conclusion, grinding techniques and their applications are vast and varied.
These processes are integral to creating precise parts and surfaces across numerous industries, from automotive to medical fields.
Understanding the different types of grinding, their specific applications, and the importance of surface finish and precision is essential for any professional involved in material machining.
資料ダウンロード
QCD調達購買管理クラウド「newji」は、調達購買部門で必要なQCD管理全てを備えた、現場特化型兼クラウド型の今世紀最高の購買管理システムとなります。
ユーザー登録
調達購買業務の効率化だけでなく、システムを導入することで、コスト削減や製品・資材のステータス可視化のほか、属人化していた購買情報の共有化による内部不正防止や統制にも役立ちます。
NEWJI DX
製造業に特化したデジタルトランスフォーメーション(DX)の実現を目指す請負開発型のコンサルティングサービスです。AI、iPaaS、および先端の技術を駆使して、製造プロセスの効率化、業務効率化、チームワーク強化、コスト削減、品質向上を実現します。このサービスは、製造業の課題を深く理解し、それに対する最適なデジタルソリューションを提供することで、企業が持続的な成長とイノベーションを達成できるようサポートします。
オンライン講座
製造業、主に購買・調達部門にお勤めの方々に向けた情報を配信しております。
新任の方やベテランの方、管理職を対象とした幅広いコンテンツをご用意しております。
お問い合わせ
コストダウンが利益に直結する術だと理解していても、なかなか前に進めることができない状況。そんな時は、newjiのコストダウン自動化機能で大きく利益貢献しよう!
(Β版非公開)