- お役立ち記事
- Guidance from management for “improving waste elimination”—Specific methods that can be put into practice in the workplace
月間76,176名の
製造業ご担当者様が閲覧しています*
*2025年3月31日現在のGoogle Analyticsのデータより
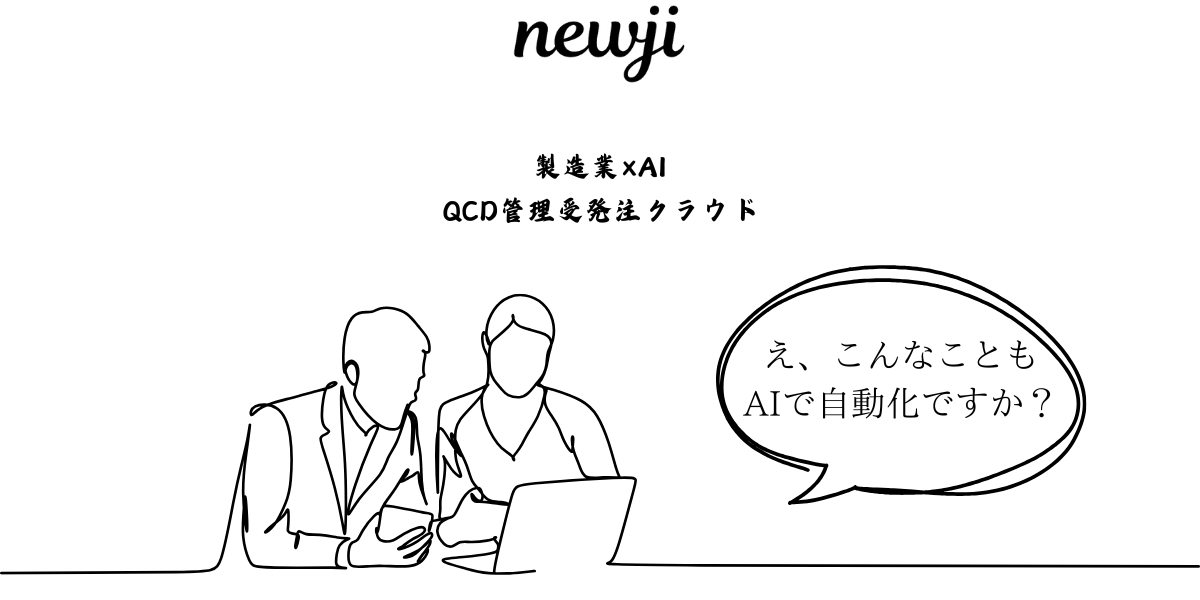
Guidance from management for “improving waste elimination”—Specific methods that can be put into practice in the workplace
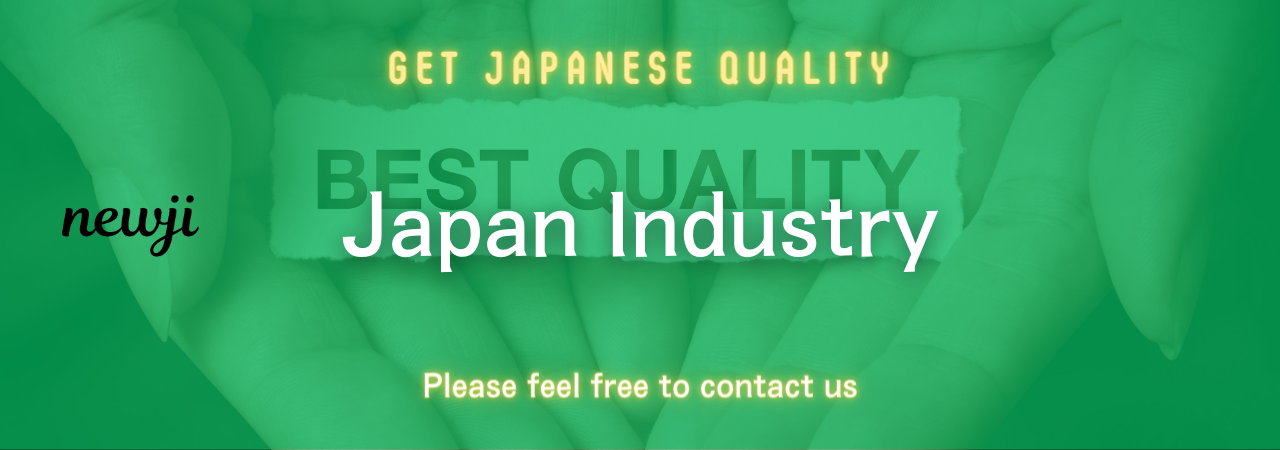
目次
Understanding Waste in the Workplace
Waste in the workplace is any activity or process that does not add value to the end product or service.
It can manifest in various forms such as excessive production, unnecessary movement, waiting time, or errors.
Understanding what constitutes waste is the first step towards identifying and eliminating it from your work processes.
Recognizing waste involves examining everyday activities and questioning their necessity and impact.
This is a critical skill for management teams striving to improve operational efficiency.
By developing this understanding, managers can guide their teams in creating a more streamlined, productive environment.
Types of Waste in Workplace Processes
In many industries, especially manufacturing, waste is categorized into seven types.
These types provide a framework for identifying and managing wasteful practices.
1. Overproduction
Producing more than what is necessary or faster than the next process can handle leads to various inefficiencies.
It ties up resources and increases storage costs, while potentially leading to obsolescence.
2. Waiting
Idle time when resources are not being fully utilized constitutes waste.
It can result from poor scheduling, equipment breakdowns, or unbalanced workloads.
3. Transport
Unnecessary movement of materials or information adds no value to the product.
Reducing this ensures that every movement or step adds to the end goal.
4. Overprocessing
Sometimes processes are more complicated or have more steps than necessary, leading to excess actions that don’t enhance the product’s value.
5. Inventory
Holding excessive stock requires additional handling, increases chances of damage, and ties up capital.
Efficient inventory management helps maintain an optimal level of stock.
6. Motion
Similar to transport, this refers to the physical movement of people that does not add value, such as excessive bending or reaching for tools.
7. Defects
Producing products that do not meet quality standards leads to rework, waste of materials, and lower customer satisfaction.
Strategies for Reducing Waste
Once waste is identified, the next step is to implement strategies to eliminate it.
Management plays a crucial role in this process by fostering a culture committed to continuous improvement.
Implement Lean Principles
Lean principles focus on maximizing value and minimizing waste.
These principles encourage a company-wide commitment towards efficiency and quality improvement.
Encourage Employee Participation
Employees are often the ones closest to the processes and can provide valuable insights into waste reduction.
Encouraging their involvement and fostering an open environment for feedback can catalyze improvement initiatives.
Standardize Processes
Creating standard operating procedures helps ensure consistency and minimizes errors.
It also makes it easier to identify deviations that may lead to waste.
Use Technology
Technological advancements, such as automation and data analytics, can greatly reduce operational waste.
They provide tools for real-time monitoring, predictive maintenance, and improved decision-making.
Implement Regular Training
Regular training sessions for employees help keep everyone updated on best practices for efficiency and waste reduction.
Informed employees can better implement and sustain waste elimination strategies.
Monitoring and Sustaining Progress
After implementing waste reduction strategies, it is essential to monitor their effectiveness.
This involves setting measurable goals and assessing progress continuously.
Use Key Performance Indicators (KPIs)
KPIs provide a quantitative measure to track improvements.
Examples include productivity rates, defect rates, and cycle time reductions.
Conduct Regular Audits
Regular audits help identify new opportunities for waste elimination and ensure compliance with established procedures.
These can help sustain improvements over the long term.
Foster a Culture of Continuous Improvement
Creating a work environment that values continuous improvement encourages employees to always seek ways to enhance processes and eliminate waste.
Conclusion
Improving waste elimination is a dynamic process that requires the commitment and wise guidance of management.
By understanding waste types and implementing practical strategies, organizations can achieve significant improvements in productivity and profitability.
Furthermore, fostering an inclusive culture of continuous improvement ensures that these changes are sustainable.
With these practices, businesses can not only enhance their operational efficiency but also contribute positively towards their environmental and social responsibilities.
資料ダウンロード
QCD管理受発注クラウド「newji」は、受発注部門で必要なQCD管理全てを備えた、現場特化型兼クラウド型の今世紀最高の受発注管理システムとなります。
ユーザー登録
受発注業務の効率化だけでなく、システムを導入することで、コスト削減や製品・資材のステータス可視化のほか、属人化していた受発注情報の共有化による内部不正防止や統制にも役立ちます。
NEWJI DX
製造業に特化したデジタルトランスフォーメーション(DX)の実現を目指す請負開発型のコンサルティングサービスです。AI、iPaaS、および先端の技術を駆使して、製造プロセスの効率化、業務効率化、チームワーク強化、コスト削減、品質向上を実現します。このサービスは、製造業の課題を深く理解し、それに対する最適なデジタルソリューションを提供することで、企業が持続的な成長とイノベーションを達成できるようサポートします。
製造業ニュース解説
製造業、主に購買・調達部門にお勤めの方々に向けた情報を配信しております。
新任の方やベテランの方、管理職を対象とした幅広いコンテンツをご用意しております。
お問い合わせ
コストダウンが利益に直結する術だと理解していても、なかなか前に進めることができない状況。そんな時は、newjiのコストダウン自動化機能で大きく利益貢献しよう!
(β版非公開)