- お役立ち記事
- Guide to improving the efficiency of receiving and storing imported goods and selecting a subcontractor
月間77,185名の
製造業ご担当者様が閲覧しています*
*2025年2月28日現在のGoogle Analyticsのデータより
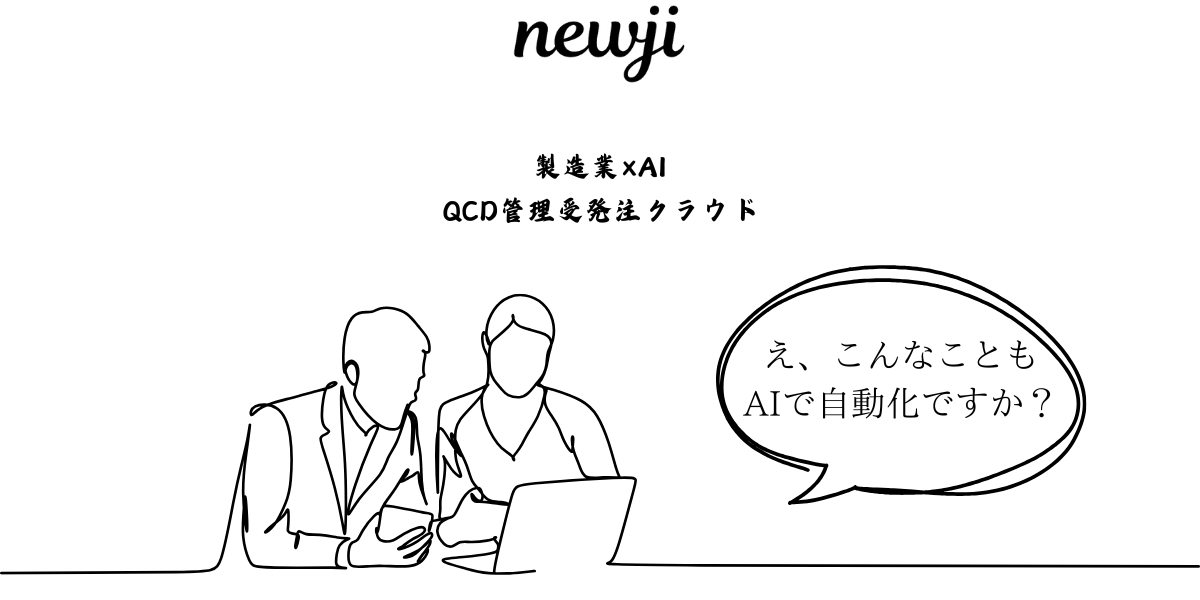
Guide to improving the efficiency of receiving and storing imported goods and selecting a subcontractor
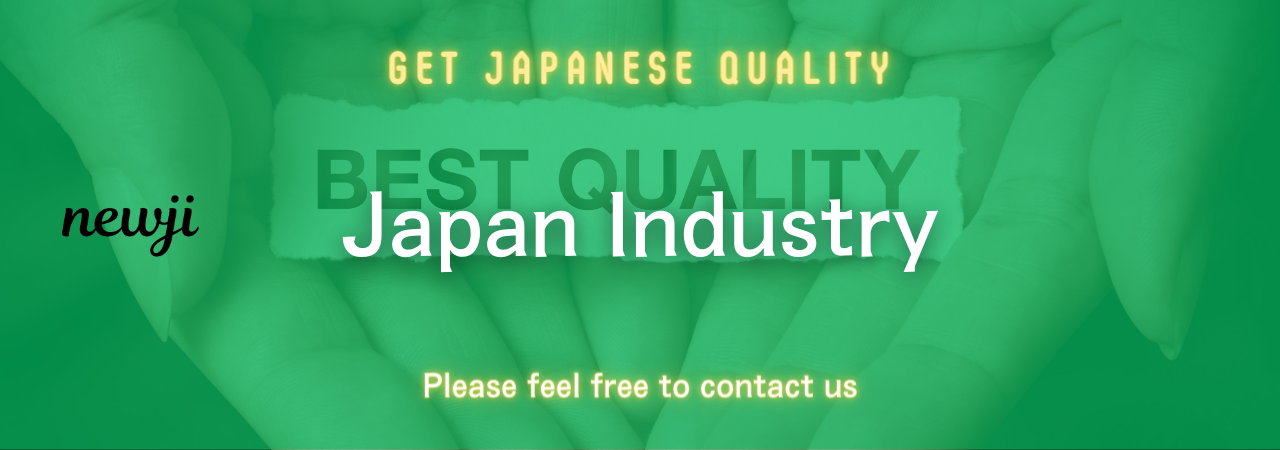
目次
Introduction
Efficiently receiving and storing imported goods is a critical aspect of supply chain management.
For businesses engaged in international trade, optimizing these processes can lead to significant cost savings and improved customer satisfaction.
Furthermore, the selection of appropriate subcontractors plays a vital role in achieving these goals.
In this guide, we will explore strategies to enhance the efficiency of receiving and storing imported goods and provide insights into selecting the right subcontractor for your business.
Streamlining the Receiving Process
1. Implement Advance Shipping Notices (ASNs)
Advance Shipping Notices (ASNs) are electronic documents that provide detailed information about a shipment before it arrives.
Utilizing ASNs allows businesses to prepare in advance, allocate resources efficiently, and reduce bottlenecks.
By knowing what to expect, companies can schedule staff and equipment to match the incoming goods, resulting in a smoother receiving process.
2. Utilize Barcode and RFID Technologies
Barcode and Radio-Frequency Identification (RFID) technologies are indispensable tools for inventory management.
Implementing these systems helps automate the tracking and recording of goods as they arrive.
They minimize manual entry errors and speed up the receiving process, allowing for a more accurate and efficient inventory management system.
3. Conduct Regular Staff Training
Training staff regularly ensures that they are updated with the best practices and the latest technology used in receiving goods.
Skilled employees can process shipments faster and more accurately, which reduces waiting times and enhances overall efficiency.
Optimizing Storage Solutions
1. Design an Effective Warehouse Layout
An optimized warehouse layout is crucial for efficient storage and retrieval of goods.
Consider using vertical storage and narrow aisles to maximize space.
Organization is key; ensure that items are strategically placed for easy access, with the most frequently moved goods located near dispatch areas.
2. Implement Inventory Management Systems
Inventory management systems (IMS) are essential for tracking goods within a warehouse.
These systems can track item movement, manage stock levels, and provide real-time data to inform decision-making.
The right IMS can significantly reduce the time spent on manual inventory checks and help avoid overstocking or stockout situations.
3. Schedule Routine Maintenance and Inspections
Regular maintenance and inspection of storage facilities and equipment help prevent delays.
Ensuring that machinery and storage systems are in good working order minimizes downtime and enhances operational efficiency.
Selecting the Right Subcontractor
1. Analyze Subcontractor Capabilities
When selecting a subcontractor, it’s crucial to assess their capabilities against your business needs.
Consider factors such as their experience in handling specific types of goods, capacity, and technological prowess.
A subcontractor with the right expertise can contribute significantly to the efficiency of your supply chain.
2. Evaluate Pricing and Contracts
Cost is always a significant consideration in selecting a subcontractor.
However, it’s essential to weigh the price against the quality of service provided.
Ensure that the subcontractor’s pricing model aligns with your profit margins and that their contracts offer flexibility in terms of service adjustments.
3. Prioritize Communication and Reliability
Strong communication is the backbone of a successful subcontracting relationship.
Investigate the subcontractor’s communication practices to ensure quick and accurate information flow.
Additionally, a reliable subcontractor will meet deadlines consistently and handle goods with care.
Monitoring and Continuous Improvement
1. Measure Performance with KPIs
Establish key performance indicators (KPIs) to monitor the efficiency of your receiving and storage operations.
KPIs such as lead times, order accuracy, and inventory turnover rates can provide valuable insights into areas needing improvement.
2. Implement Feedback Loops
Use feedback loops to gather insights from staff, customers, and subcontractors.
Implementing suggestions and adapting operations based on constructive feedback can drive continuous improvements in efficiency.
3. Invest in Technology Upgrades
Stay abreast of technological advancements that could benefit your operations.
Investing in modern technology such as automation and IoT devices can further enhance efficiency in receiving and storing goods.
Conclusion
Optimizing the processes of receiving and storing imported goods, as well as selecting the right subcontractor, are crucial for maintaining an efficient supply chain.
By adopting strategies such as utilizing advanced technologies, designing effective layouts, and establishing strong subcontractor partnerships, businesses can significantly enhance their operational efficiency.
Continuous monitoring and improvement, driven by data and feedback, will ensure that these processes remain effective and adaptable to changing market demands.
The right approach will not only streamline operations but also provide a competitive edge in the global market.
資料ダウンロード
QCD管理受発注クラウド「newji」は、受発注部門で必要なQCD管理全てを備えた、現場特化型兼クラウド型の今世紀最高の受発注管理システムとなります。
ユーザー登録
受発注業務の効率化だけでなく、システムを導入することで、コスト削減や製品・資材のステータス可視化のほか、属人化していた受発注情報の共有化による内部不正防止や統制にも役立ちます。
NEWJI DX
製造業に特化したデジタルトランスフォーメーション(DX)の実現を目指す請負開発型のコンサルティングサービスです。AI、iPaaS、および先端の技術を駆使して、製造プロセスの効率化、業務効率化、チームワーク強化、コスト削減、品質向上を実現します。このサービスは、製造業の課題を深く理解し、それに対する最適なデジタルソリューションを提供することで、企業が持続的な成長とイノベーションを達成できるようサポートします。
製造業ニュース解説
製造業、主に購買・調達部門にお勤めの方々に向けた情報を配信しております。
新任の方やベテランの方、管理職を対象とした幅広いコンテンツをご用意しております。
お問い合わせ
コストダウンが利益に直結する術だと理解していても、なかなか前に進めることができない状況。そんな時は、newjiのコストダウン自動化機能で大きく利益貢献しよう!
(β版非公開)