- お役立ち記事
- Guidelines for the development and practical application of ceramic matrix composites that design department leaders in the aircraft parts manufacturing industry should know
Guidelines for the development and practical application of ceramic matrix composites that design department leaders in the aircraft parts manufacturing industry should know
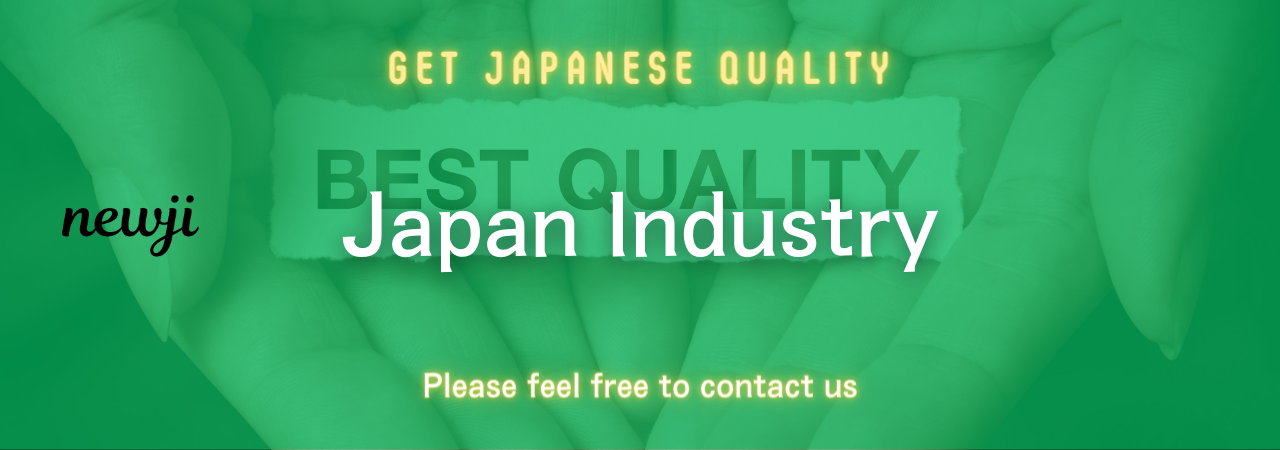
目次
Understanding Ceramic Matrix Composites (CMCs)
Ceramic Matrix Composites (CMCs) are materials composed of ceramic fibers embedded in a ceramic matrix.
CMCs offer several benefits over traditional materials used in the aircraft industry, such as metals and alloys.
Their lightweight nature, combined with high resistance to thermal shock and oxidation, make them hot commodities.
Thus, knowing how to develop and apply these materials can provide a significant advantage to aircraft design departments.
The Advantages of CMCs in Aircraft Manufacturing
One of the primary benefits of CMCs is their ability to withstand high temperatures.
This quality makes them especially useful in applications subjected to extreme heat, such as engine components.
Unlike metals, CMCs maintain structural integrity at higher temperatures, enhancing the overall performance and efficiency of an aircraft.
CMCs are also known for their superior strength-to-weight ratio.
Aircraft manufacturing increasingly prioritizes reducing weight to improve fuel efficiency and reduce emissions.
CMCs can significantly contribute to achieving this goal, as they are both light and strong.
Additionally, these composites offer excellent resistance to corrosion and wear.
This characteristic reduces the need for frequent maintenance and increases the lifespan of critical aircraft parts.
As a result, using CMCs can lead to cost savings over time.
Guidelines for Developing CMCs
Developing CMCs involves several steps, from choosing the right materials to performing rigorous testing.
Understanding these guidelines is essential for leaders in the aircraft parts manufacturing industry.
Selecting the Right Materials
The first step in CMC development is selecting appropriate materials for the ceramic fibers and the matrix.
Materials typically used include silicon carbide, alumina, and mullite, each offering unique properties.
Silicon carbide fibers, for example, provide excellent thermal and mechanical properties.
Alumina, on the other hand, offers a balance of strength and cost-efficiency.
The choice of materials should align with the specific requirements of the aircraft parts being developed.
Understanding these needs is crucial for ensuring the final product meets the necessary performance standards.
Design and Fabrication Techniques
Designing CMCs involves considering factors such as fiber architecture and matrix composition.
The architecture of the fibers can significantly affect the strength and flexibility of the final composite.
Common architectures include woven, braided, or unidirectional fibers.
Each configuration offers different benefits, depending on the application.
Fabricating CMCs requires techniques like chemical vapor infiltration or melt infiltration.
These processes ensure the matrix material adequately surrounds the fibers, creating a robust composite.
Choosing the right fabrication technique is as important as the design itself, influencing the final properties of the CMC.
Testing and Quality Assurance
Once developed, CMCs undergo extensive testing to ensure they meet industry standards and performance requirements.
These tests examine mechanical properties, thermal stability, and resistance to environmental factors.
Conduct rigorous testing to identify any potential weaknesses early on and address them before mass production.
Quality assurance processes are vital for maintaining consistency and reliability in CMCs.
Implementing stringent quality checks during both production and post-production phases helps ensure high-quality composites.
Practical Application of CMCs
Successfully applying CMCs in aircraft manufacturing involves understanding their potential applications and integrating them into existing designs.
Engine Components
CMCs are particularly valuable for components subjected to high temperatures, such as turbine blades and exhaust systems.
Their ability to maintain integrity under extreme conditions boosts engine efficiency and reduces the cooling requirements.
This efficiency translates into better fuel economy and a reduction in harmful emissions.
Structural Components
Beyond engines, CMCs can be used in structural aircraft components.
Their strength and lightweight nature allows for innovative design possibilities, reducing overall aircraft weight.
This reduction not only improves performance but also enhances safety by providing robust yet flexible structures.
Aerospace and Defense Applications
Outside of commercial aircraft, CMCs find applications in aerospace and defense sectors.
Their durability and resistance to extreme environments make them suitable for spacecraft and military aircraft components.
Developments in CMC technology could lead to advancements in these fields, offering improved performance and reliability.
Moving Forward with CMCs
As the aircraft industry progresses, the demand for advanced materials like CMCs will only increase.
Staying ahead of the curve requires a thorough understanding of CMC development and application guidelines.
Leaders in design departments will find that investing in CMC technology not only brings immediate benefits but also prepares their companies for future industry trends.
By embracing these materials, manufacturers can create higher-performing, more efficient aircraft that meet the evolving demands of the market.
資料ダウンロード
QCD調達購買管理クラウド「newji」は、調達購買部門で必要なQCD管理全てを備えた、現場特化型兼クラウド型の今世紀最高の購買管理システムとなります。
ユーザー登録
調達購買業務の効率化だけでなく、システムを導入することで、コスト削減や製品・資材のステータス可視化のほか、属人化していた購買情報の共有化による内部不正防止や統制にも役立ちます。
NEWJI DX
製造業に特化したデジタルトランスフォーメーション(DX)の実現を目指す請負開発型のコンサルティングサービスです。AI、iPaaS、および先端の技術を駆使して、製造プロセスの効率化、業務効率化、チームワーク強化、コスト削減、品質向上を実現します。このサービスは、製造業の課題を深く理解し、それに対する最適なデジタルソリューションを提供することで、企業が持続的な成長とイノベーションを達成できるようサポートします。
オンライン講座
製造業、主に購買・調達部門にお勤めの方々に向けた情報を配信しております。
新任の方やベテランの方、管理職を対象とした幅広いコンテンツをご用意しております。
お問い合わせ
コストダウンが利益に直結する術だと理解していても、なかなか前に進めることができない状況。そんな時は、newjiのコストダウン自動化機能で大きく利益貢献しよう!
(Β版非公開)