- お役立ち記事
- Harnessing Back Electromotive Force: A Deep Dive into Japanese Manufacturing Innovations
Harnessing Back Electromotive Force: A Deep Dive into Japanese Manufacturing Innovations
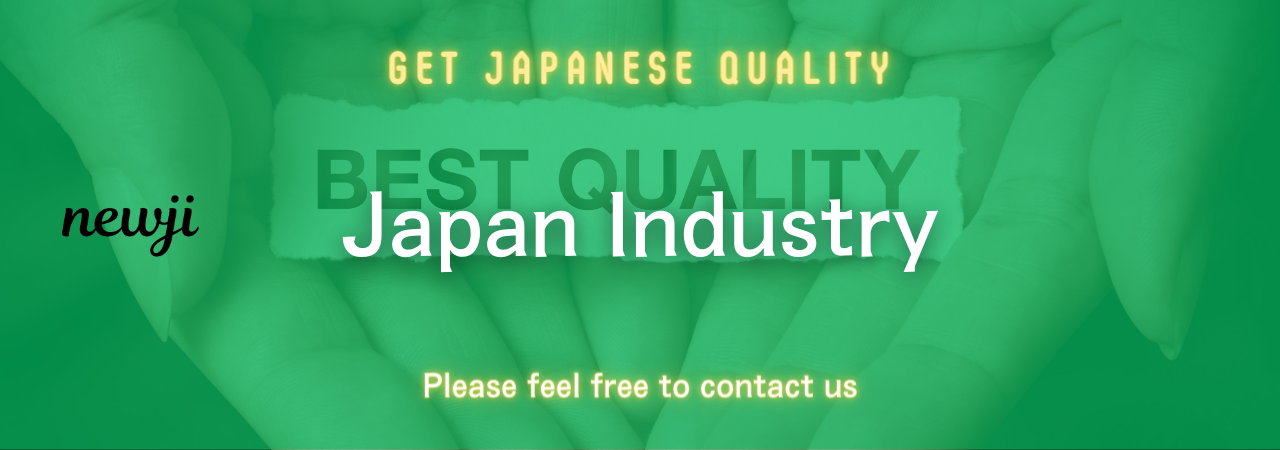
目次
Understanding Back Electromotive Force in Modern Manufacturing
Back electromotive force (Back EMF) is a fundamental concept in electrical engineering, particularly relevant in the operation of motors and generators. It refers to the voltage generated by a motor when it is spinning, acting in opposition to the applied voltage that drives the motor. This phenomenon is not only a critical factor in the efficiency and control of electric motors but also a pivotal element in various manufacturing innovations.
In the context of manufacturing, Back EMF plays a crucial role in the performance and reliability of machinery. Understanding and harnessing Back EMF can lead to significant improvements in energy efficiency, motor control, and overall system stability. Japanese manufacturers, renowned for their engineering prowess, have developed advanced techniques to optimize Back EMF, contributing to their leadership in the global manufacturing sector.
Japanese Innovations in Harnessing Back Electromotive Force
Japan’s manufacturing industry has long been at the forefront of integrating advanced electrical engineering concepts into practical applications. The country’s approach to harnessing Back EMF is characterized by precision, efficiency, and a deep understanding of both theoretical and applied aspects of electromagnetism.
Advanced Motor Control Systems
Japanese manufacturers have pioneered the development of sophisticated motor control systems that effectively utilize Back EMF. These systems enable precise speed and torque control by leveraging the inherent properties of Back EMF. By accurately measuring and compensating for Back EMF, manufacturers can achieve smoother motor operation, reduced energy consumption, and enhanced performance.
Energy Recovery Technologies
One of the significant areas where Back EMF is harnessed is in energy recovery technologies. Japanese companies have developed systems that capture the energy generated by Back EMF during motor deceleration or braking. This recovered energy can then be reused within the system, leading to improved energy efficiency and reduced operational costs.
Integration with Smart Manufacturing
The integration of Back EMF-based technologies with smart manufacturing systems is another area where Japanese innovation shines. By combining Back EMF sensing with IoT (Internet of Things) and AI (Artificial Intelligence), manufacturers can achieve real-time monitoring and predictive maintenance. This integration enhances the reliability of manufacturing equipment and minimizes downtime, contributing to higher productivity levels.
The Role of Procurement and Purchasing in Leveraging Back EMF Innovations
Effective procurement and purchasing strategies are essential for integrating Back EMF innovations into manufacturing processes. Japanese suppliers offer a range of advanced components and systems designed to maximize the benefits of Back EMF, but navigating this landscape requires a strategic approach.
Advantages of Sourcing from Japanese Suppliers
Sourcing Back EMF-related technologies from Japanese suppliers offers several advantages. Japanese manufacturers are known for their high-quality standards, reliability, and technological expertise. By procuring components such as advanced motor controllers, energy recovery systems, and smart sensors from Japanese sources, companies can ensure the integration of cutting-edge technology into their manufacturing processes.
Additionally, Japanese suppliers often provide comprehensive support and customization services, allowing manufacturers to tailor solutions to their specific needs. This level of collaboration enhances the effectiveness of Back EMF implementations and fosters long-term partnerships.
Disadvantages and Challenges
While there are significant benefits to sourcing from Japanese suppliers, there are also challenges to consider. Language barriers, cultural differences, and complex supply chain logistics can pose obstacles. Moreover, the higher cost of advanced Japanese technology may be a concern for some manufacturers, especially those operating on tight budgets.
To mitigate these challenges, it is crucial to establish clear communication channels, engage in thorough contract negotiations, and develop strong relationships with suppliers. Understanding the nuances of Japanese business practices and leveraging local expertise can also help overcome potential hurdles.
Supplier Negotiation Techniques for Back EMF Technologies
Negotiating with Japanese suppliers requires a blend of cultural sensitivity, strategic planning, and technical knowledge. Successful negotiations can lead to favorable terms, customized solutions, and long-term partnerships that benefit both parties.
Cultivating Relationships
In Japanese business culture, building trust and strong relationships is paramount. Investing time in developing personal connections with suppliers can lead to more collaborative and flexible negotiations. Regular visits, face-to-face meetings, and mutual respect are essential components of this relationship-building process.
Understanding Supplier Capabilities
A deep understanding of the supplier’s capabilities and technological expertise is crucial. Conducting thorough research on the supplier’s product offerings, technological advancements, and quality standards allows for more informed negotiations. It also demonstrates a genuine interest in the supplier’s business, fostering mutual respect and trust.
Clear Communication and Specifications
Clear and precise communication of requirements is vital to ensure that the supplier can meet the specific needs related to Back EMF technologies. Providing detailed specifications, performance expectations, and quality standards helps prevent misunderstandings and ensures that the delivered components or systems align with manufacturing goals.
Market Conditions Influencing Back EMF Innovations
The market dynamics surrounding Back EMF technologies are shaped by various factors, including technological advancements, regulatory changes, and global economic conditions. Understanding these factors is essential for making informed procurement decisions and staying competitive in the manufacturing sector.
Technological Advancements
Rapid advancements in electrical engineering and smart manufacturing technologies continue to drive innovations in Back EMF. The development of more efficient motor control systems, energy recovery solutions, and integrated IoT devices presents new opportunities for manufacturers to enhance their operations.
Japanese manufacturers are particularly adept at integrating these advancements into practical applications, maintaining their position as leaders in the field. Staying abreast of these technological trends is crucial for companies looking to leverage Back EMF in their manufacturing processes.
Regulatory Environment
Global and regional regulations related to energy efficiency, emissions, and manufacturing standards significantly impact the adoption of Back EMF technologies. Stricter energy efficiency standards in regions like Europe and North America drive manufacturers to seek advanced solutions that comply with regulatory requirements.
Japanese suppliers often lead in meeting and exceeding these standards, offering products that not only comply but also provide additional benefits such as enhanced performance and cost savings.
Economic Factors
Economic conditions, including exchange rates, trade policies, and supply chain stability, influence the procurement of Back EMF technologies. The strength of the Japanese yen, for instance, can affect the cost of sourcing components from Japan. Additionally, global supply chain disruptions can impact the availability and lead times of essential technologies.
Manufacturers must develop flexible procurement strategies that account for these economic variables, such as diversifying suppliers and exploring cost-effective sourcing options to mitigate risks.
Best Practices for Integrating Back EMF Innovations
Successfully integrating Back EMF innovations into manufacturing processes requires a strategic approach that encompasses planning, execution, and continuous improvement. The following best practices can help manufacturers maximize the benefits of Back EMF technologies.
Comprehensive Planning and Assessment
Before implementing Back EMF innovations, it is essential to conduct a thorough assessment of current manufacturing processes and identify areas where Back EMF can provide the most significant benefits. This includes evaluating existing motor systems, energy consumption patterns, and maintenance procedures.
Developing a detailed implementation plan that outlines goals, timelines, and resource requirements ensures a structured approach to integration, minimizing disruptions and optimizing outcomes.
Collaboration with Suppliers
Collaborating closely with Japanese suppliers during the integration process facilitates the successful adoption of Back EMF technologies. Suppliers can provide valuable insights, technical support, and customization options to ensure that the components and systems align with the specific needs of the manufacturing operation.
Establishing joint development initiatives and continuous feedback loops can lead to innovative solutions and ongoing improvements.
Training and Skill Development
Investing in training and skill development for the workforce is crucial for the effective utilization of Back EMF technologies. Employees should be educated on the principles of Back EMF, the operation of new motor control systems, and the maintenance of energy recovery devices.
Providing hands-on training and fostering a culture of continuous learning ensures that the workforce is equipped to handle the complexities of advanced manufacturing technologies.
Monitoring and Optimization
Implementing real-time monitoring systems enables manufacturers to track the performance of Back EMF technologies continuously. Utilizing data analytics and predictive maintenance tools helps identify potential issues early, allowing for timely interventions and optimizations.
Regularly reviewing performance metrics and seeking opportunities for process improvements ensures that the benefits of Back EMF innovations are fully realized and sustained over time.
Case Studies: Success Stories from Japanese Manufacturing
Examining real-world examples of successful Back EMF integration provides valuable insights into best practices and potential challenges. Japanese manufacturing companies have demonstrated impressive results by effectively harnessing Back EMF in various applications.
Automotive Industry
In the automotive sector, Japanese manufacturers have implemented Back EMF-based regenerative braking systems in electric vehicles. These systems capture the energy generated during braking and reuse it to recharge the vehicle’s battery, enhancing energy efficiency and extending driving range.
This innovation not only contributes to environmental sustainability but also offers cost savings and improved vehicle performance, showcasing the practical benefits of Back EMF technologies.
Industrial Robotics
Japanese companies specializing in industrial robotics have integrated Back EMF-based control systems to enhance the precision and responsiveness of robotic arms. By leveraging Back EMF sensing, these robots achieve smoother movements, higher accuracy, and reduced energy consumption, leading to increased productivity and lower operational costs.
Such advancements demonstrate the versatility of Back EMF applications across different manufacturing domains.
Smart Manufacturing Solutions
In smart manufacturing environments, Back EMF is utilized to optimize various processes, including conveyor systems, automated assembly lines, and material handling equipment. Japanese manufacturers have developed intelligent control systems that adapt to real-time conditions, ensuring optimal performance and minimal energy wastage.
These smart solutions contribute to the overall efficiency and competitiveness of manufacturing operations, highlighting the strategic importance of Back EMF innovations.
Future Trends in Back Electromotive Force Technologies
The future of Back EMF technologies in manufacturing is poised for significant advancements, driven by ongoing research, technological breakthroughs, and increasing demands for energy efficiency and sustainability.
Integration with AI and Machine Learning
The integration of Back EMF technologies with artificial intelligence (AI) and machine learning opens new avenues for optimizing motor control systems and energy recovery processes. AI algorithms can analyze vast amounts of data from Back EMF sensors to predict maintenance needs, optimize energy usage, and enhance overall system performance.
This convergence of technologies promises to usher in a new era of intelligent manufacturing systems that are more adaptive and efficient.
Advancements in Material Science
Innovations in material science are leading to the development of more efficient and durable components for Back EMF applications. Advanced materials with superior electrical and thermal properties enable the creation of compact, high-performance motor control units and energy recovery systems.
These advancements contribute to improved reliability, reduced size and weight, and enhanced performance of Back EMF technologies in manufacturing equipment.
Enhanced Energy Management Systems
Future developments in energy management systems will leverage Back EMF technologies to achieve greater energy efficiency and sustainability. Advanced energy storage solutions, combined with intelligent energy distribution networks, will enable manufacturers to maximize the benefits of energy recovery and minimize waste.
These enhanced energy management systems will play a critical role in meeting global energy conservation goals and reducing the environmental impact of manufacturing operations.
Conclusion: Embracing Back EMF for Manufacturing Excellence
Harnessing Back Electromotive Force represents a significant opportunity for manufacturers to enhance their operations, achieve greater energy efficiency, and maintain a competitive edge in a rapidly evolving landscape. Japanese manufacturing innovations in this domain exemplify the potential of Back EMF to drive technological advancements and operational excellence.
By adopting best practices in procurement, fostering strong supplier relationships, and integrating advanced Back EMF technologies, manufacturers can unlock new levels of performance and sustainability. As the industry continues to evolve, the strategic implementation of Back EMF innovations will be a key determinant of success, positioning manufacturers to thrive in the future of smart and efficient manufacturing.
資料ダウンロード
QCD調達購買管理クラウド「newji」は、調達購買部門で必要なQCD管理全てを備えた、現場特化型兼クラウド型の今世紀最高の購買管理システムとなります。
ユーザー登録
調達購買業務の効率化だけでなく、システムを導入することで、コスト削減や製品・資材のステータス可視化のほか、属人化していた購買情報の共有化による内部不正防止や統制にも役立ちます。
NEWJI DX
製造業に特化したデジタルトランスフォーメーション(DX)の実現を目指す請負開発型のコンサルティングサービスです。AI、iPaaS、および先端の技術を駆使して、製造プロセスの効率化、業務効率化、チームワーク強化、コスト削減、品質向上を実現します。このサービスは、製造業の課題を深く理解し、それに対する最適なデジタルソリューションを提供することで、企業が持続的な成長とイノベーションを達成できるようサポートします。
オンライン講座
製造業、主に購買・調達部門にお勤めの方々に向けた情報を配信しております。
新任の方やベテランの方、管理職を対象とした幅広いコンテンツをご用意しております。
お問い合わせ
コストダウンが利益に直結する術だと理解していても、なかなか前に進めることができない状況。そんな時は、newjiのコストダウン自動化機能で大きく利益貢献しよう!
(Β版非公開)