- お役立ち記事
- Harnessing the Power of EMC Service: Revolutionizing Japanese Manufacturing Excellence
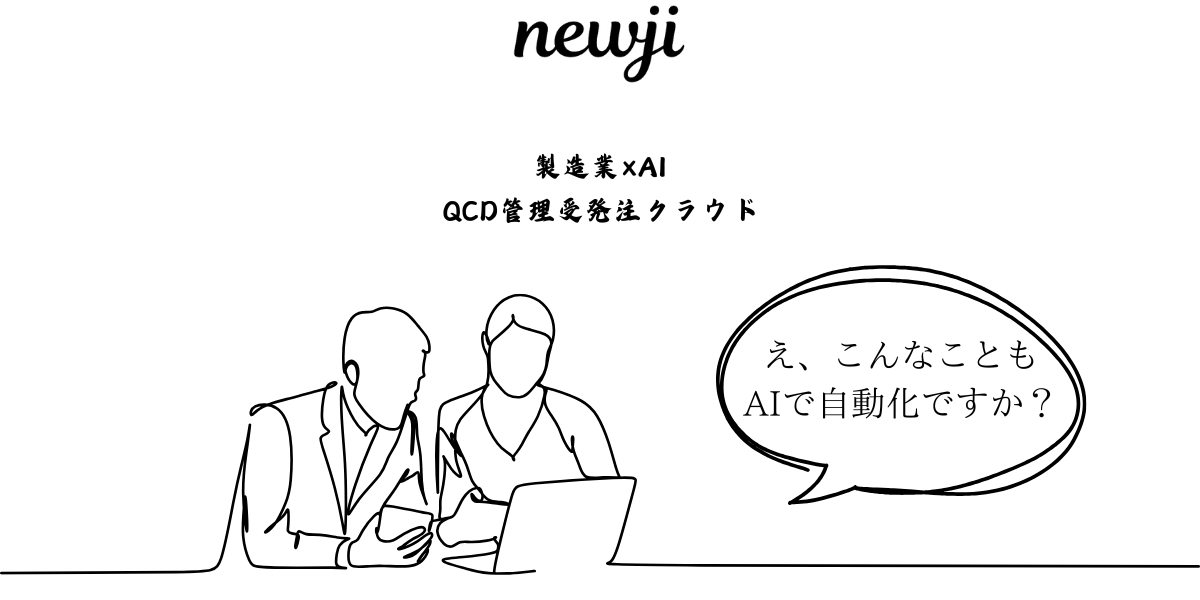
Harnessing the Power of EMC Service: Revolutionizing Japanese Manufacturing Excellence
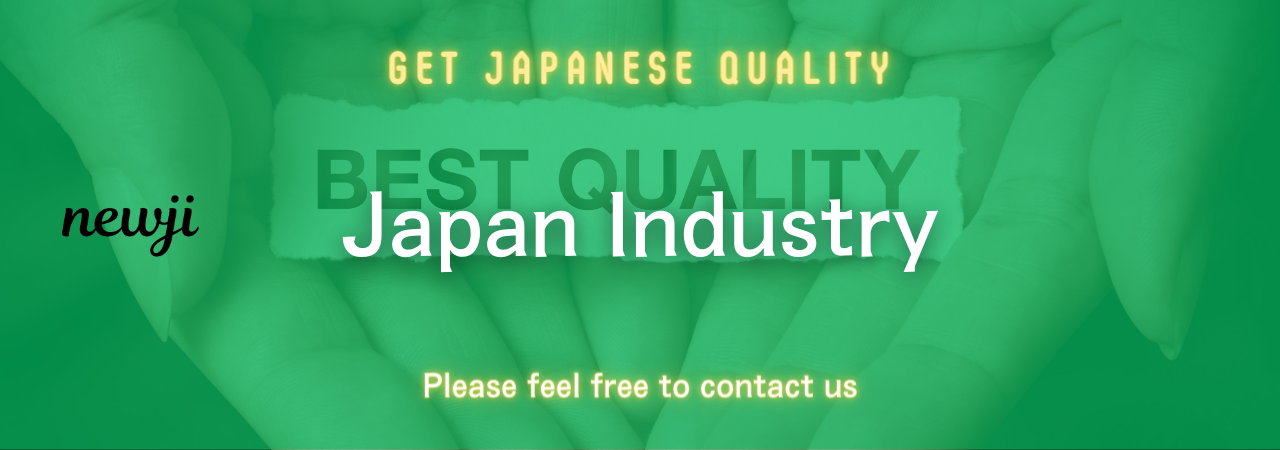
目次
Introduction to EMC Service in Japanese Manufacturing
Japanese manufacturing has long been synonymous with quality, precision, and innovation. Central to this reputation is the effective implementation of EMC Service, a strategic approach that enhances manufacturing processes and ensures excellence. EMC Service, standing for Excellence in Manufacturing Collaboration, bridges gaps between procurement, production, and quality control, fostering a synergistic environment that drives success. This article explores how leveraging EMC Service can revolutionize Japanese manufacturing, delving into its practical applications, advantages, challenges, and best practices.
The Role of EMC Service in Procurement and Purchasing
Procurement and purchasing are critical components of the manufacturing supply chain. EMC Service plays a pivotal role in optimizing these functions, ensuring that companies acquire the best materials at competitive prices while maintaining high standards of quality. By fostering strong relationships with suppliers and emphasizing collaboration, EMC Service enhances the efficiency and reliability of the procurement process.
Streamlining Supplier Selection
Selecting the right suppliers is fundamental to manufacturing success. EMC Service employs a rigorous selection process that evaluates suppliers based on quality, reliability, and cost-effectiveness. This ensures that only the most capable suppliers become partners, reducing the risk of disruptions and ensuring consistent material quality.
Enhancing Supplier Relationships
Building strong relationships with suppliers is a cornerstone of EMC Service. Regular communication, mutual trust, and shared goals lead to long-term partnerships that benefit both parties. This collaborative approach facilitates better negotiation terms, timely deliveries, and the ability to quickly address any issues that arise.
Advantages of Implementing EMC Service
Implementing EMC Service offers numerous benefits that contribute to manufacturing excellence. These advantages span operational efficiency, cost savings, quality improvement, and enhanced innovation.
Operational Efficiency
EMC Service streamlines manufacturing processes by promoting seamless integration between different departments. This integration reduces bottlenecks, accelerates production timelines, and ensures that all aspects of manufacturing work in harmony. The result is a more efficient operation with higher output and lower lead times.
Cost Savings
By optimizing procurement strategies and fostering competitive supplier relationships, EMC Service helps reduce costs. Bulk purchasing, better negotiation terms, and reduced waste all contribute to significant cost savings. These savings can be reinvested into other areas of the business, driving further growth and innovation.
Quality Improvement
Quality control is a critical aspect of Japanese manufacturing. EMC Service enhances quality by ensuring that only the best materials are sourced and that suppliers adhere to stringent quality standards. Continuous monitoring and feedback loops help maintain high quality throughout the production process, minimizing defects and ensuring customer satisfaction.
Enhanced Innovation
Collaboration through EMC Service fosters a culture of innovation. By working closely with suppliers and encouraging the sharing of ideas, companies can develop new products and improve existing ones. This collaborative environment drives continuous improvement and keeps manufacturing processes at the cutting edge of technology.
Challenges and Disadvantages of EMC Service
While EMC Service offers substantial benefits, it also presents certain challenges that companies must navigate to achieve success.
Complexity of Implementation
Implementing EMC Service requires significant coordination and effort. Integrating different departments, aligning goals, and establishing effective communication channels can be complex and time-consuming. Companies must invest in training and change management to ensure a smooth transition.
Dependence on Supplier Reliability
EMC Service relies heavily on the reliability of suppliers. If a supplier fails to deliver on time or cannot maintain quality standards, it can disrupt the entire manufacturing process. Companies must carefully select suppliers and establish contingency plans to mitigate this risk.
Cultural Differences
In an international context, cultural differences between companies and their suppliers can pose challenges. Misunderstandings and differing business practices can hinder collaboration. Effective cross-cultural communication and mutual respect are essential to overcoming these barriers.
Supplier Negotiation Techniques in EMC Service
Effective negotiation with suppliers is vital for maximizing the benefits of EMC Service. Japanese procurement practices emphasize fairness, long-term relationships, and mutual benefit, which are key to successful negotiations.
Building Trust and Long-Term Relationships
Japanese business culture places a high value on trust and long-term relationships. Negotiations are not just about immediate gains but about establishing a foundation for ongoing collaboration. Building strong relationships based on trust can lead to better terms and more cooperative problem-solving.
Emphasizing Mutual Benefits
Negotiations should focus on creating win-win scenarios where both parties benefit. By understanding the needs and constraints of suppliers, companies can propose solutions that satisfy both sides. This approach fosters cooperation and ensures sustainable partnerships.
Leveraging Data and Market Insights
Effective negotiations are grounded in solid data and market insights. Understanding market conditions, supplier costs, and industry trends enables companies to make informed decisions and negotiate favorable terms. Data-driven strategies enhance the effectiveness of negotiations and lead to better outcomes.
Flexibility and Adaptability
Flexibility is essential in negotiations. Being open to alternative solutions and adaptable to changing circumstances can help overcome obstacles and reach agreements. A flexible approach demonstrates respect for the supplier’s needs and fosters a collaborative atmosphere.
Market Conditions Affecting EMC Service
Understanding the market conditions is crucial for the successful implementation of EMC Service. Various factors influence procurement strategies and supplier relationships, including economic trends, supply chain dynamics, and technological advancements.
Economic Trends
Global economic trends impact the availability and cost of materials. Companies must stay informed about economic indicators and adjust their procurement strategies accordingly. In times of economic uncertainty, securing reliable suppliers and maintaining cost control become even more critical.
Supply Chain Dynamics
The complexity of global supply chains can affect the effectiveness of EMC Service. Factors such as transportation delays, geopolitical issues, and regulatory changes can disrupt supply chains. Companies must develop resilient supply chain strategies that can adapt to these changes and maintain smooth operations.
Technological Advancements
Advancements in technology can enhance EMC Service by improving communication, data analysis, and automation. Implementing the latest technologies can streamline procurement processes, enhance supplier collaboration, and provide deeper insights into market trends. Staying abreast of technological developments is essential for maintaining a competitive edge.
Best Practices for Maximizing EMC Service Effectiveness
To fully harness the power of EMC Service, companies should adopt best practices that enhance collaboration, efficiency, and quality across the manufacturing process.
Continuous Improvement and Kaizen
Adopting a continuous improvement mindset, such as the Kaizen philosophy, ensures that EMC Service remains effective over time. Regularly reviewing processes, seeking feedback, and implementing incremental changes contribute to sustained excellence and adaptability.
Integrated Communication Systems
Effective communication is the backbone of EMC Service. Implementing integrated communication systems that facilitate real-time information sharing and collaboration across departments and with suppliers enhances coordination and responsiveness.
Comprehensive Training Programs
Investing in comprehensive training programs for employees ensures that everyone understands the principles and practices of EMC Service. Training fosters a culture of collaboration and equips staff with the skills needed to effectively implement and sustain EMC initiatives.
Performance Metrics and Monitoring
Establishing clear performance metrics and monitoring progress is essential for evaluating the success of EMC Service. Key performance indicators (KPIs) related to procurement efficiency, cost savings, quality control, and supplier performance help identify areas for improvement and guide strategic decisions.
Risk Management Strategies
Implementing robust risk management strategies helps mitigate potential disruptions and uncertainties. Identifying potential risks, developing contingency plans, and maintaining flexibility in procurement and production processes ensures resilience and continuity.
Case Studies: Success Stories in Japanese Manufacturing
Examining real-world examples of companies that have successfully implemented EMC Service provides valuable insights into best practices and effective strategies.
Case Study 1: Toyota Motor Corporation
Toyota is renowned for its implementation of the Toyota Production System (TPS), which incorporates EMC Service principles. By fostering close relationships with suppliers and emphasizing continuous improvement, Toyota has achieved unparalleled efficiency and quality in its manufacturing processes. Collaborative problem-solving and mutual trust with suppliers have enabled Toyota to maintain its position as a global leader in the automotive industry.
Case Study 2: Sony Corporation
Sony has leveraged EMC Service to drive innovation and maintain high standards of quality in its electronics manufacturing. By working closely with suppliers and integrating advanced technologies, Sony has successfully developed cutting-edge products that meet evolving market demands. The company’s commitment to collaboration and excellence has solidified its reputation for reliability and innovation.
Case Study 3: Panasonic Corporation
Panasonic has utilized EMC Service to enhance its procurement and production management processes. Through strategic partnerships with suppliers and a focus on efficiency and quality, Panasonic has streamlined its supply chain and reduced costs. The company’s dedication to continuous improvement and supplier collaboration has contributed to its sustained success in the global market.
Future Trends in EMC Service and Japanese Manufacturing
As the manufacturing landscape evolves, EMC Service must adapt to emerging trends and challenges. Staying ahead of these developments is crucial for maintaining excellence and competitiveness.
Digital Transformation
The ongoing digital transformation in manufacturing includes the adoption of technologies such as the Internet of Things (IoT), artificial intelligence (AI), and big data analytics. These technologies can enhance EMC Service by providing deeper insights into procurement and production processes, enabling more informed decision-making and greater efficiency.
Sustainable Manufacturing
Sustainability is becoming increasingly important in manufacturing. EMC Service can integrate sustainable practices by selecting environmentally responsible suppliers, optimizing resource use, and reducing waste. Emphasizing sustainability not only benefits the environment but also meets the growing consumer demand for green products.
Globalization and Localization
Balancing globalization with localization is a key trend affecting EMC Service. While global supply chains offer cost advantages and access to diverse suppliers, localization can enhance resilience and responsiveness. Companies must strategically manage their supply chains to leverage the benefits of both global and local suppliers.
Advanced Automation and Robotics
Automation and robotics are transforming manufacturing processes. Integrating these technologies with EMC Service can further enhance efficiency, reduce labor costs, and improve precision. Advanced automation enables more consistent quality and faster production cycles, contributing to overall manufacturing excellence.
Conclusion: Embracing EMC Service for Manufacturing Excellence
Harnessing the power of EMC Service is a transformative strategy for Japanese manufacturing companies seeking to maintain and enhance their reputation for excellence. By optimizing procurement and purchasing, fostering strong supplier relationships, and embracing continuous improvement, companies can achieve greater efficiency, cost savings, and quality in their manufacturing processes. While challenges exist, the benefits of EMC Service far outweigh the drawbacks, offering a pathway to sustained success in a competitive global market. Adopting best practices and staying attuned to emerging trends will ensure that EMC Service continues to drive innovation and excellence in Japanese manufacturing for years to come.
資料ダウンロード
QCD調達購買管理クラウド「newji」は、調達購買部門で必要なQCD管理全てを備えた、現場特化型兼クラウド型の今世紀最高の購買管理システムとなります。
ユーザー登録
調達購買業務の効率化だけでなく、システムを導入することで、コスト削減や製品・資材のステータス可視化のほか、属人化していた購買情報の共有化による内部不正防止や統制にも役立ちます。
NEWJI DX
製造業に特化したデジタルトランスフォーメーション(DX)の実現を目指す請負開発型のコンサルティングサービスです。AI、iPaaS、および先端の技術を駆使して、製造プロセスの効率化、業務効率化、チームワーク強化、コスト削減、品質向上を実現します。このサービスは、製造業の課題を深く理解し、それに対する最適なデジタルソリューションを提供することで、企業が持続的な成長とイノベーションを達成できるようサポートします。
オンライン講座
製造業、主に購買・調達部門にお勤めの方々に向けた情報を配信しております。
新任の方やベテランの方、管理職を対象とした幅広いコンテンツをご用意しております。
お問い合わせ
コストダウンが利益に直結する術だと理解していても、なかなか前に進めることができない状況。そんな時は、newjiのコストダウン自動化機能で大きく利益貢献しよう!
(Β版非公開)