- お役立ち記事
- Heat sealing mechanism, material design, quality assurance points, and defect countermeasures
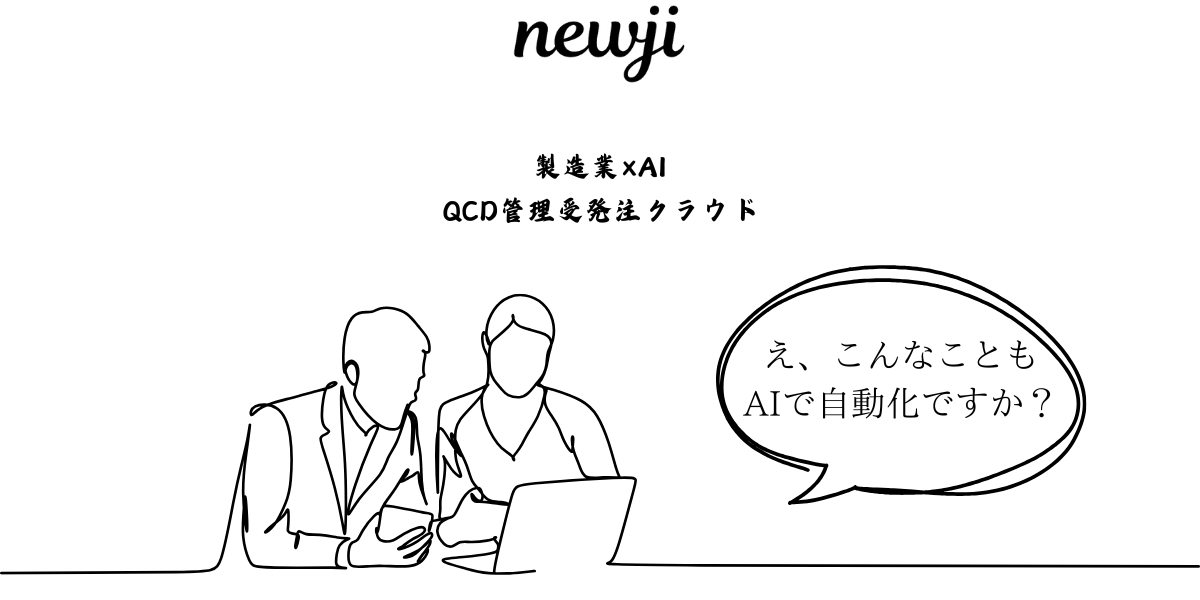
Heat sealing mechanism, material design, quality assurance points, and defect countermeasures
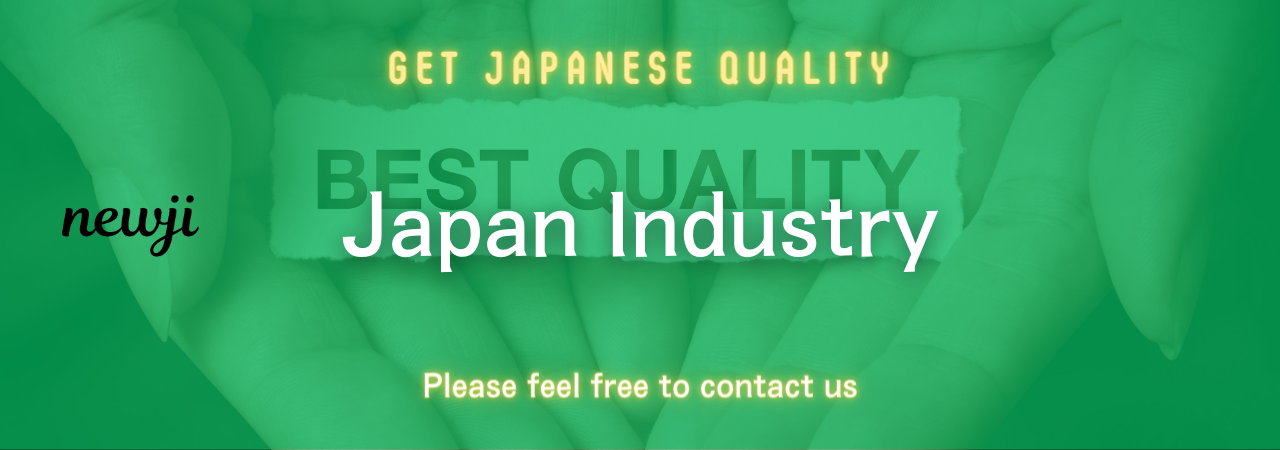
目次
Understanding Heat Sealing
Heat sealing is a process widely used in packaging to join materials, typically plastic films or foils, using heat and pressure.
It’s a crucial step in ensuring product safety, freshness, and integrity in industries like food packaging, pharmaceuticals, and consumer goods.
The heat sealing mechanism involves applying heat to the contact area, causing the materials to bond upon cooling.
Mechanism of Heat Sealing
At the core of heat sealing is the principle of thermoplastic properties.
When thermoplastic materials are heated, they melt to a semi-liquid state, allowing them to flow and bond upon application of pressure.
Once the heat and pressure are removed, the materials cool and solidify, creating a sealed joint.
There are different types of heat sealing methods including hot bar, impulse, and ultrasonic sealing.
In hot bar sealing, a bar heated to a specific temperature is pressed against the materials to be joined.
Impulse sealing involves a short burst of heat, followed by cooling under pressure.
Ultrasonic sealing uses high-frequency sound waves to create frictional heat at the interface, leading to a seal.
Material Design for Effective Sealing
Choosing the right materials is vital for an effective heat seal.
The materials must possess compatible melting points and flow properties to ensure strong adhesion.
Common materials include polyethylene, polypropylene, and laminated films, each chosen based on factors like barrier properties, flexibility, and cost.
Additionally, material thickness impacts the sealing process.
Thinner materials may require less heat but could lead to weaker seals, whereas thicker materials might necessitate more heat, risking material distortion.
Thus, balancing thickness and heat parameters is essential for optimal results.
Surface Properties and Treatments
The surface properties of the materials also play a significant role in heat sealing.
A clean surface ensures effective bonding, and treatments like corona or plasma can be applied to enhance surface energy.
These treatments improve wettability and adhesion, promoting a stronger seal.
Transparency and clarity of materials can also influence consumer perception, especially in product packaging applications, making them additional considerations in material design.
Quality Assurance in Heat Sealing
To ensure the reliability of heat seals, robust quality assurance measures are crucial.
These measures involve monitoring parameters like temperature, pressure, and sealing time, as they directly affect seal integrity.
Consistent calibration and maintenance of sealing equipment are essential to avoiding fluctuations in these parameters.
Visual inspections and destructive testing methods like peel testing can be employed to assess seal strength.
Peel testing involves applying a force perpendicular to the seal to determine its resistance to separation.
Moreover, non-destructive testing methods, such as burst testing, allow for quality checks without ruining the product.
Data Logging and Analysis
Data logging systems track environmental and operational parameters in the sealing process.
Analyzing this data helps identify trends or deviations that might lead to seal failures.
Statistical analysis tools can pinpoint variances that need attention, ensuring consistent quality in production.
Defect Countermeasures
Despite careful material selection and quality assurance, defects can occur in heat sealing processes.
Common defects include poor seals, wrinkles, and burning of materials.
Addressing these issues requires understanding their causes and implementing corrective actions.
Poor Seals
Poor seals, often caused by insufficient heat or pressure, can lead to material separation under stress.
Adjusting the sealing parameters, like increasing temperature or pressure, can mitigate this issue.
Ensuring even distribution of heat and uniform pressure application across the sealing area is also critical.
Wrinkles and Distortions
Wrinkles occur when the materials misalign during sealing, often due to improper tension in the feeding mechanism.
Correcting this requires synchronizing the film feed and ensuring even tension.
Regular equipment inspections and maintenance can prevent these alignment issues.
Burning and Material Degradation
Excessive heat causes burning or melting of materials, damaging the seal and product appearance.
Proper calibration of the sealing temperature and timing, as well as selecting materials with higher thermal resistance, can prevent burning.
In addition, ensuring the sealing equipment operates within the recommended temperature range helps avoid overheating.
Conclusion
Heat sealing is a complex but essential process in packaging, ensuring product safety and integrity.
Understanding the mechanism, carefully selecting materials, and maintaining strict quality checks are critical for successful heat seals.
By identifying and addressing defects early, manufacturers can enhance their product packaging, maintaining trust with consumers.
Continuous monitoring and adaptation of processes ensure that the heat sealing operation remains efficient, reliable, and effective.
資料ダウンロード
QCD調達購買管理クラウド「newji」は、調達購買部門で必要なQCD管理全てを備えた、現場特化型兼クラウド型の今世紀最高の購買管理システムとなります。
ユーザー登録
調達購買業務の効率化だけでなく、システムを導入することで、コスト削減や製品・資材のステータス可視化のほか、属人化していた購買情報の共有化による内部不正防止や統制にも役立ちます。
NEWJI DX
製造業に特化したデジタルトランスフォーメーション(DX)の実現を目指す請負開発型のコンサルティングサービスです。AI、iPaaS、および先端の技術を駆使して、製造プロセスの効率化、業務効率化、チームワーク強化、コスト削減、品質向上を実現します。このサービスは、製造業の課題を深く理解し、それに対する最適なデジタルソリューションを提供することで、企業が持続的な成長とイノベーションを達成できるようサポートします。
オンライン講座
製造業、主に購買・調達部門にお勤めの方々に向けた情報を配信しております。
新任の方やベテランの方、管理職を対象とした幅広いコンテンツをご用意しております。
お問い合わせ
コストダウンが利益に直結する術だと理解していても、なかなか前に進めることができない状況。そんな時は、newjiのコストダウン自動化機能で大きく利益貢献しよう!
(Β版非公開)