- お役立ち記事
- High-precision metal sintering technology and its application in the medical device market
月間77,185名の
製造業ご担当者様が閲覧しています*
*2025年2月28日現在のGoogle Analyticsのデータより
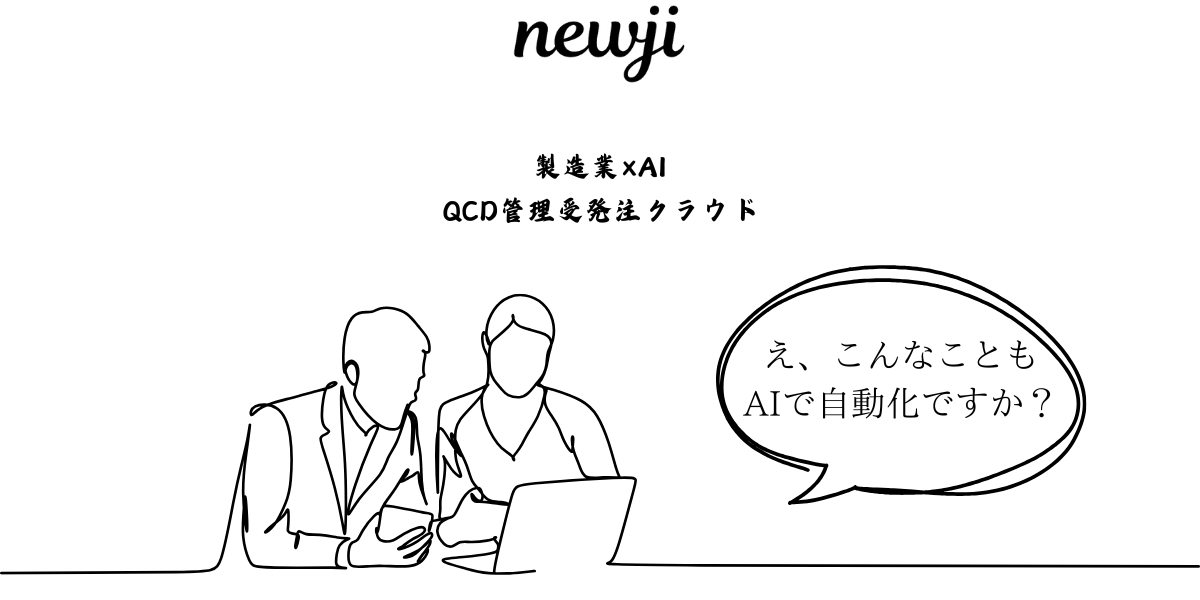
High-precision metal sintering technology and its application in the medical device market
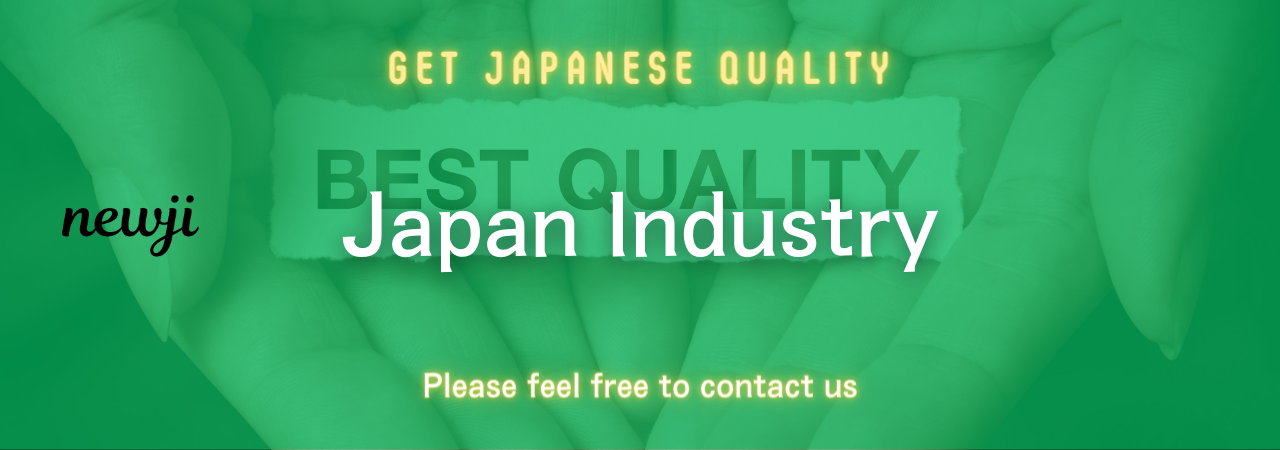
目次
Introduction to Metal Sintering Technology
Metal sintering is a remarkable technology that has played a pivotal role in transforming various industries, and it is making significant inroads in the medical device market.
The process involves fusing metal particles together through heat without reaching the point of liquefaction.
This results in a solid, coherent mass that retains the properties of metal but with enhanced precision and intricacy.
The advent of high-precision metal sintering technology has further expanded its potential, making it a key player in the manufacturing of medical devices.
The Basics of High-Precision Metal Sintering
High-precision metal sintering typically involves advanced additive manufacturing techniques like Selective Laser Sintering (SLS) or Direct Metal Laser Sintering (DMLS).
These techniques utilize lasers to heat and fuse metal powders layer by layer, crafting components that range from simple to highly intricate designs.
This precise control over the sintering process helps in maintaining tight tolerances and achieving excellent surface finishes, which are essential for medical devices where accuracy is paramount.
Benefits of Metal Sintering in Medical Devices
Customization and Personalization
One of the standout benefits of metal sintering in the medical sector is the ability to customize and personalize devices.
Every patient’s anatomy can be different, making personalization critical in fields like orthopedics and prosthetics.
The precision of metal sintering allows for the creation of bespoke implants and devices that fit perfectly to individual patient profiles.
Complex Geometries and Lightweight Structures
Metal sintering allows for the creation of complex geometries that are often impossible to achieve with traditional manufacturing methods.
This is particularly beneficial for medical devices that require intricate internal lattice structures for improved performance and reduced weight.
For example, spinal implants and stents benefit from enhanced design capabilities without compromising on strength or functionality.
Material Efficiency and Cost-Effectiveness
The process is incredibly efficient in terms of material usage, as it minimizes waste produced during the manufacturing process.
This efficiency translates into cost savings, particularly important in the healthcare industry where budget constraints are a constant concern.
Additionally, the rapid prototyping capabilities of metal sintering ensure faster development and deployment of medical devices, decreasing time-to-market.
Applications in the Medical Device Market
Orthopedic Implants
Orthopedic implants have seen tremendous advancements due to metal sintering technology.
Components such as knee and hip replacements can be highly customized, ensuring better fit and function for patients.
Moreover, the ability to create porous implants encourages better osseointegration, where the implant fuses more effectively with bone tissue.
Dental Applications
In the field of dentistry, metal sintering is used to produce crowns, bridges, and dental implants with superior precision and durability.
Dental professionals can offer patients products that are both functional and aesthetically pleasing.
The accuracy afforded by metal sintering plays a vital role in successful dental restorative procedures.
Surgical Instruments
Another crucial application is in the production of complex surgical tools that require precision manufacturing.
Metal sintering allows for the production of lightweight, robust tools that improve surgical accuracy and outcomes.
Custom tools tailored for specific procedures can be manufactured quickly, allowing surgeons to tailor operations to the specific needs of their patients.
Prosthetics
The landscape of prosthetics is undergoing radical change with the use of metal sintering technology.
It enables the creation of lightweight, durable prosthetic limbs that are customized to the individual user.
These prosthetics offer increased comfort and functionality, allowing users to perform daily activities with greater ease.
Challenges and Future Outlook
While metal sintering technology in medical applications brings numerous benefits, there are challenges that the industry must overcome.
The initial investment in sintering equipment can be high, and there is a learning curve associated with mastering the technology.
Moreover, rigorous regulatory approvals are necessary, given the critical nature of medical devices.
Looking to the future, with ongoing advancements in sintering techniques and materials, the medical device market stands to gain even more.
Research is focused on new alloys and composites that are biocompatible, and the continued miniaturization of devices could open new possibilities in minimally invasive procedures.
Conclusion
High-precision metal sintering technology is revolutionizing the medical device market by enabling the production of customized, complex, and efficient components.
Its application spans a wide range of devices from implants to prosthetics, making healthcare solutions more individualized and effective.
As the technology continues to evolve, its impact on patient care and outcomes promises to be profound, shaping the future of the medical industry in unprecedented ways.
資料ダウンロード
QCD管理受発注クラウド「newji」は、受発注部門で必要なQCD管理全てを備えた、現場特化型兼クラウド型の今世紀最高の受発注管理システムとなります。
ユーザー登録
受発注業務の効率化だけでなく、システムを導入することで、コスト削減や製品・資材のステータス可視化のほか、属人化していた受発注情報の共有化による内部不正防止や統制にも役立ちます。
NEWJI DX
製造業に特化したデジタルトランスフォーメーション(DX)の実現を目指す請負開発型のコンサルティングサービスです。AI、iPaaS、および先端の技術を駆使して、製造プロセスの効率化、業務効率化、チームワーク強化、コスト削減、品質向上を実現します。このサービスは、製造業の課題を深く理解し、それに対する最適なデジタルソリューションを提供することで、企業が持続的な成長とイノベーションを達成できるようサポートします。
製造業ニュース解説
製造業、主に購買・調達部門にお勤めの方々に向けた情報を配信しております。
新任の方やベテランの方、管理職を対象とした幅広いコンテンツをご用意しております。
お問い合わせ
コストダウンが利益に直結する術だと理解していても、なかなか前に進めることができない状況。そんな時は、newjiのコストダウン自動化機能で大きく利益貢献しよう!
(β版非公開)