- お役立ち記事
- High-Precision Positioning Mechanism Design for Semiconductor Inspection Equipment
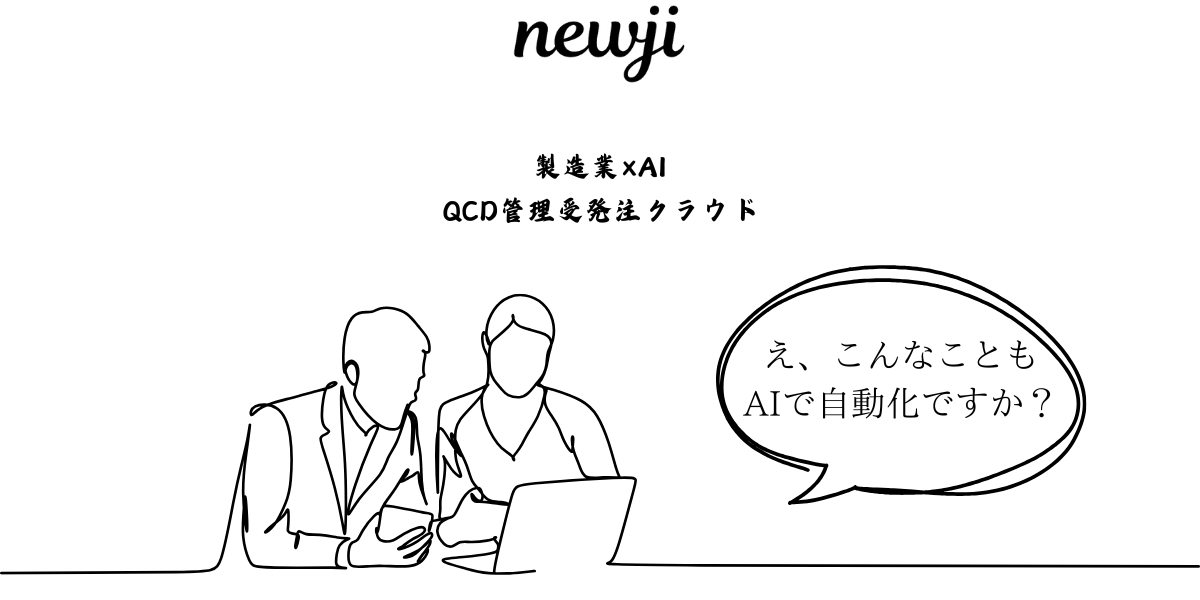
High-Precision Positioning Mechanism Design for Semiconductor Inspection Equipment
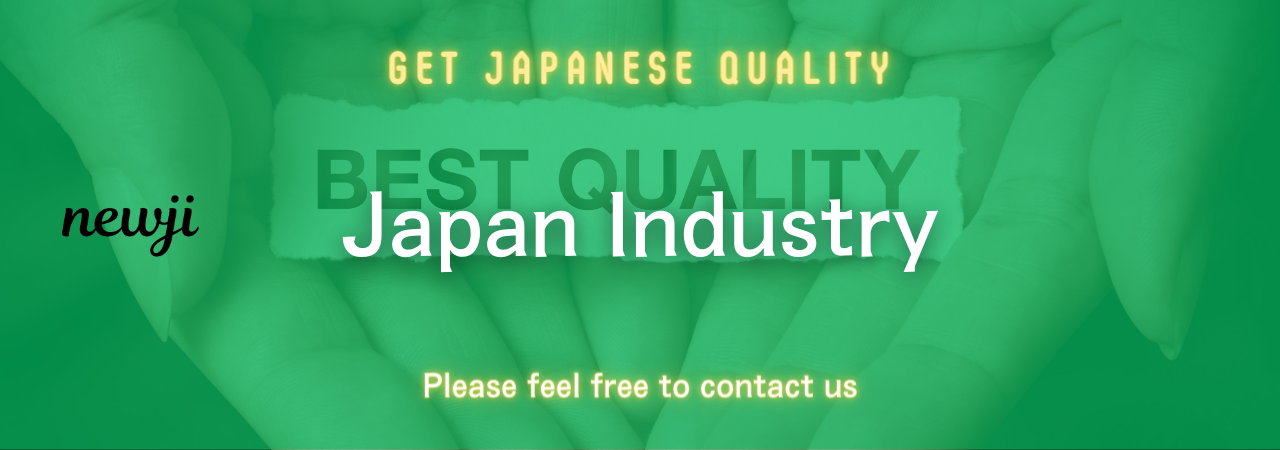
In the world of semiconductor inspection equipment, achieving high-precision positioning is crucial for maintaining the integrity and quality of semiconductor products. As these inspection processes become increasingly sophisticated, the demand for a meticulously engineered positioning mechanism grows. To navigate the complex requirements of these systems, it is essential to comprehend the nuances of high-precision positioning mechanism design.
目次
Understanding the Importance of High-Precision Positioning
Semiconductor devices are intricately designed with components that are often just a few nanometers in size. This means that any misalignment, no matter how minute, can compromise the functionality of the device.
Therefore, high-precision positioning is not merely a luxury but a necessity in semiconductor inspection equipment.
When inspecting semiconductor wafers, the equipment must detect defects with high accuracy and reliability. High-precision positioning enables the equipment to focus on specific areas with exceptional detail, ensuring that any defects, however small, are identified promptly. This precision is also vital in aligning the semiconductor components during assembly, which can significantly affect the performance and longevity of the final product.
Key Components of High-Precision Positioning Mechanisms
Several components come together to form the high-precision positioning mechanisms used in semiconductor inspection equipment. Understanding these elements helps in improving accuracy and efficiency.
Actuators
Actuators are integral to the movement and positioning of the inspection equipment. Various types of actuators, including piezoelectric, linear, and rotary actuators, are employed based on the requirements of the inspection task.
Piezoelectric actuators, for example, provide highly accurate movements by converting electrical energy into mechanical displacement.
They are particularly suited for applications requiring fine adjustments and rapid response times.
Encoders
Encoders are tools that provide feedback on the position of the moving components. They are essential for the precise control of the inspection process.
There are two main types of encoders: absolute and incremental.
Absolute encoders can provide the exact position of an element at any given moment, while incremental encoders measure the relative position from a starting point. The choice of encoder depends on the nature of the inspection and the level of precision needed.
Guideways
Guideways are the components that ensure smooth and controlled movement of the inspection head or table. These come in linear and rotary forms, and their design can significantly affect the precision of the positioning mechanism.
Linear guideways, such as ball screws or linear rails, offer high accuracy in movement, which is crucial for the precise inspection of semiconductor wafers. Rotary guideways, on the other hand, facilitate accurate rotational movements required in certain applications.
Design Considerations for High-Precision Positioning Mechanisms
Designing a high-precision positioning mechanism for semiconductor inspection equipment involves several crucial considerations. Each factor plays a pivotal role in ensuring the equipment operates with the requisite accuracy and reliability.
Minimizing Thermal Drift
Thermal drift occurs when components expand or contract due to temperature changes, resulting in positioning errors. To counteract this, materials with low thermal expansion coefficients, such as ceramics or specific metal alloys, are often used.
Additionally, implementing temperature control systems within the equipment can help maintain a stable environment, reducing the risk of thermal drift. This can be achieved using cooling systems or by maintaining the inspection area at a consistent temperature.
Vibration Control
External vibrations can severely impact the precision of semiconductor inspection equipment. To mitigate this, designers can incorporate vibration isolation systems and damping materials into the mechanism.
Vibration isolation systems, such as air bearings or active damping systems, help reduce the impact of external vibrations, ensuring the stability and precision of the inspection process. Using materials like viscoelastic polymers can also dampen vibrations and enhance the accuracy of the equipment.
Accuracy and Repeatability
Accuracy refers to the positioning mechanism’s ability to reach a target position precisely, while repeatability indicates the system’s capability to return to the same position consistently.
Ensuring both high accuracy and repeatability is essential for effective semiconductor inspection. Engineers achieve this by carefully selecting components, such as high-precision encoders and low-backlash actuators, and by implementing sophisticated control algorithms.
The Role of Advanced Control Systems
To achieve high-precision positioning, advanced control systems are employed. These systems manage the operation of the actuators, encoders, and other components, ensuring seamless and precise movement.
Closed-Loop Control Systems
Closed-loop control systems use feedback from encoders to continuously adjust the position of the inspection head or table. This feedback enables the system to correct any deviations in real-time, maintaining high accuracy throughout the inspection process.
By employing closed-loop control, the positioning mechanism can adapt to changes in the inspection environment, such as temperature fluctuations or external vibrations, ensuring consistent performance.
Advanced Algorithms
Sophisticated algorithms are used to enhance the performance of the positioning mechanism. These algorithms can predict and compensate for errors, such as thermal drift or mechanical wear, further improving the accuracy and repeatability of the system.
Machine learning techniques can also be integrated into the control systems, allowing the equipment to learn from previous inspections and optimize its performance over time.
Future Trends in High-Precision Positioning Mechanism Design
As semiconductor technology continues to advance, so too does the need for even more precise inspection equipment.
Several emerging trends are shaping the future of high-precision positioning mechanism design.
Nanotechnology
The incorporation of nanotechnology in positioning mechanisms is revolutionizing semiconductor inspection. Nano-positioning systems can achieve sub-nanometer accuracy, allowing for the inspection of even the tiniest defects in semiconductor wafers.
This level of precision is particularly crucial as semiconductor components continue to shrink in size, requiring even more detailed inspections.
Smart Materials
Smart materials, such as shape-memory alloys and piezoelectric materials, are becoming increasingly popular in positioning mechanism design. These materials can change their properties in response to external stimuli, such as temperature or electric fields, providing enhanced control and precision.
By incorporating smart materials into the design, engineers can develop positioning mechanisms that are more responsive and adaptable to changing inspection requirements.
Integration with AI
Artificial intelligence (AI) is playing an increasingly significant role in semiconductor inspection equipment. By integrating AI with high-precision positioning mechanisms, manufacturers can develop systems that can adapt to new challenges and improve their performance over time.
AI-powered control systems can analyze vast amounts of data from previous inspections, identifying patterns and optimizing the positioning mechanism for better accuracy and repeatability.
In summary, the design of high-precision positioning mechanisms for semiconductor inspection equipment is a complex and multifaceted process. By understanding the importance of precision, the key components, and the critical design considerations, engineers and designers can develop advanced systems that meet the stringent demands of the semiconductor industry. As technology continues to evolve, the future of high-precision positioning holds even greater promise, with innovations such as nanotechnology, smart materials, and AI paving the way for more efficient, accurate, and reliable semiconductor inspections.
資料ダウンロード
QCD調達購買管理クラウド「newji」は、調達購買部門で必要なQCD管理全てを備えた、現場特化型兼クラウド型の今世紀最高の購買管理システムとなります。
ユーザー登録
調達購買業務の効率化だけでなく、システムを導入することで、コスト削減や製品・資材のステータス可視化のほか、属人化していた購買情報の共有化による内部不正防止や統制にも役立ちます。
NEWJI DX
製造業に特化したデジタルトランスフォーメーション(DX)の実現を目指す請負開発型のコンサルティングサービスです。AI、iPaaS、および先端の技術を駆使して、製造プロセスの効率化、業務効率化、チームワーク強化、コスト削減、品質向上を実現します。このサービスは、製造業の課題を深く理解し、それに対する最適なデジタルソリューションを提供することで、企業が持続的な成長とイノベーションを達成できるようサポートします。
オンライン講座
製造業、主に購買・調達部門にお勤めの方々に向けた情報を配信しております。
新任の方やベテランの方、管理職を対象とした幅広いコンテンツをご用意しております。
お問い合わせ
コストダウンが利益に直結する術だと理解していても、なかなか前に進めることができない状況。そんな時は、newjiのコストダウン自動化機能で大きく利益貢献しよう!
(Β版非公開)