- お役立ち記事
- High-quality technology and response in repair services for RIDGID tools
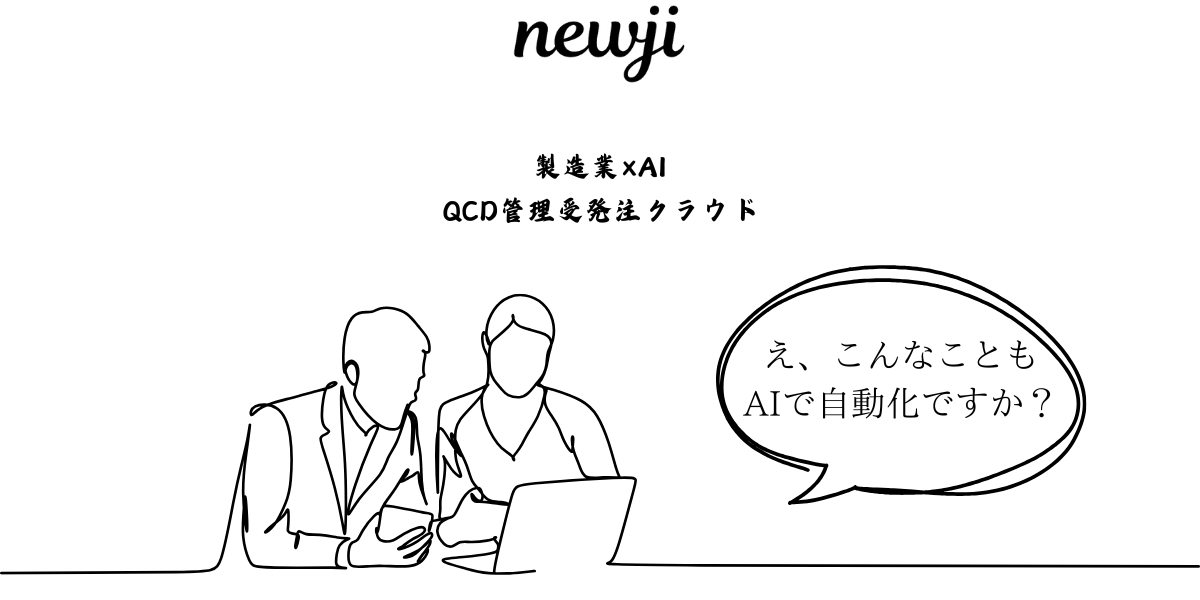
High-quality technology and response in repair services for RIDGID tools
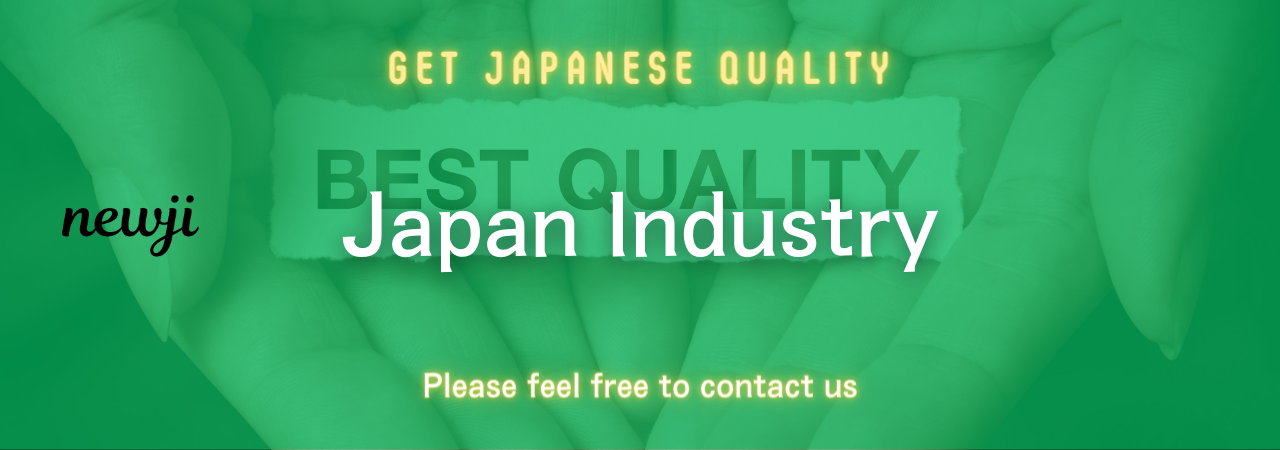
目次
Understanding RIDGID Tools and Their Importance
RIDGID tools are renowned for their durability and reliability in the construction and plumbing industries.
These tools are designed to withstand tough conditions and deliver consistent performance, making them favorites among professionals.
Whether it’s pipe wrenches, power drives, or threading equipment, RIDGID tools are built for precision and long-term use.
However, like any other tool, RIDGID products can experience wear and tear over time.
When a RIDGID tool requires repair, it’s vital to entrust it to experts who understand the intricacies and standards of these high-quality tools.
High-Quality Repair Services
When it comes to repairing RIDGID tools, high-quality service is non-negotiable.
The right repair center will have technicians who are not only experienced but also specialized in RIDGID products.
This specialization ensures that the repair is conducted using the proper tools, techniques, and replacement parts.
An essential aspect of high-quality repair is the use of genuine RIDGID parts.
These parts are manufactured under RIDGID’s strict standards, ensuring that the repaired tool maintains its original quality and performance.
Genuine parts, combined with expert repair techniques, help extend the life of the tool significantly.
The Role of Advanced Technology in Repairs
In repairing RIDGID tools, advanced technology plays a crucial role.
Modern repair centers employ state-of-the-art diagnostic equipment to identify issues accurately.
This technology allows for precise identification of problems, reducing the time needed for repairs and improving the outcome.
Moreover, technology aids in ensuring that the tools are recalibrated perfectly post-repair.
This aspect is critical, as incorrect calibration can lead to reduced efficiency and potentially cause further damage in the long run.
Technician Training and Expertise
The quality of repair service is heavily dependent on the technician’s training and expertise.
Repair technicians who deal with RIDGID tools undergo rigorous training to stay updated with the latest repair techniques and RIDGID product developments.
Continuous education programs for technicians ensure that they are well-versed in handling all types of RIDGID products.
Their expertise allows them to troubleshoot challenging problems and provide solutions that preserve the tool’s integrity and functionality.
Prompt and Efficient Service
Time is a crucial factor in repair services for RIDGID tools, as downtime can affect work schedules and productivity.
Reputable repair services aim to provide prompt and efficient repair, minimizing the time the tool is out of commission.
Many centers offer expedited services for urgent repairs, ensuring that tools are quickly back in action.
Streamlined repair processes and effective inventory management of parts contribute to faster turnaround times without compromising on quality.
Comprehensive Customer Support
High-quality repair services also include comprehensive customer support.
From initial diagnosis to post-repair follow-ups, customer support plays a vital role in ensuring customer satisfaction.
A good repair service keeps the customer informed throughout the repair process, explaining the steps being taken and providing detailed feedback.
This communication helps build trust and ensures that the customer feels their tools are in capable hands.
Preventive Maintenance and Longevity
Besides repairs, service centers often provide preventive maintenance services.
Regular maintenance checks help in identifying potential issues before they become major problems, thus extending the tool’s life.
Preventive maintenance includes cleaning, lubrication, and calibration checks.
These services ensure the tools operate at their best, reducing the risk of unexpected breakdowns.
A well-maintained RIDGID tool not only enhances performance but also offers an excellent return on investment over time.
Choosing the Right Repair Service
When selecting a repair service for RIDGID tools, it’s crucial to consider several factors.
Verification of the service center’s authorization and certification by RIDGID is a critical step.
This certification indicates adherence to RIDGID’s standards and quality assurance protocols.
Customer reviews and testimonials can also provide insights into the repair service’s reputation and reliability.
A service center with positive feedback likely offers consistent, high-quality service backed by expertise and customer care.
Finally, consider the service center’s location and the convenience of drop-off or pick-up services.
In some cases, mobile repair services can be a valuable option for onsite repairs, saving time and logistics.
Conclusion
Repair services for RIDGID tools demand a balance of quality, technology, and expertise.
Opting for high-quality repair services ensures that these durable tools continue delivering excellent performance year after year.
Professionalism in repairs, coupled with preventive maintenance, guarantees reduced downtime and an enhanced lifespan for your RIDGID tools.
By choosing a repair service that meets RIDGID standards, users can protect their investment and ensure that their tools remain in peak condition.
資料ダウンロード
QCD調達購買管理クラウド「newji」は、調達購買部門で必要なQCD管理全てを備えた、現場特化型兼クラウド型の今世紀最高の購買管理システムとなります。
ユーザー登録
調達購買業務の効率化だけでなく、システムを導入することで、コスト削減や製品・資材のステータス可視化のほか、属人化していた購買情報の共有化による内部不正防止や統制にも役立ちます。
NEWJI DX
製造業に特化したデジタルトランスフォーメーション(DX)の実現を目指す請負開発型のコンサルティングサービスです。AI、iPaaS、および先端の技術を駆使して、製造プロセスの効率化、業務効率化、チームワーク強化、コスト削減、品質向上を実現します。このサービスは、製造業の課題を深く理解し、それに対する最適なデジタルソリューションを提供することで、企業が持続的な成長とイノベーションを達成できるようサポートします。
オンライン講座
製造業、主に購買・調達部門にお勤めの方々に向けた情報を配信しております。
新任の方やベテランの方、管理職を対象とした幅広いコンテンツをご用意しております。
お問い合わせ
コストダウンが利益に直結する術だと理解していても、なかなか前に進めることができない状況。そんな時は、newjiのコストダウン自動化機能で大きく利益貢献しよう!
(Β版非公開)