- お役立ち記事
- High-Speed Cutting Techniques in Metalworking and Their Applications
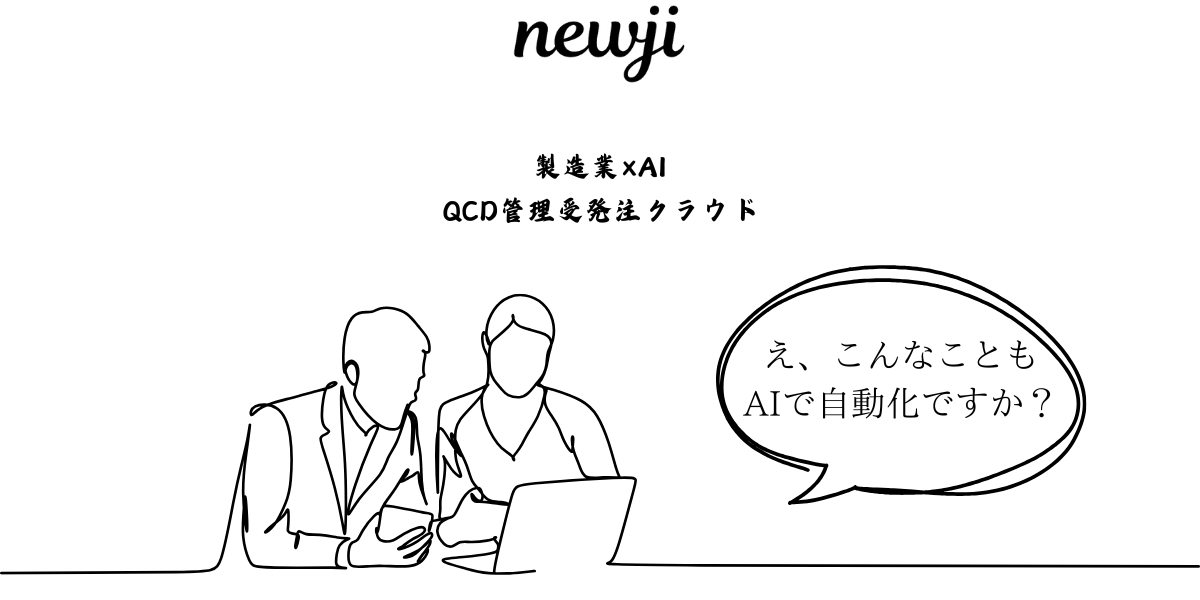
High-Speed Cutting Techniques in Metalworking and Their Applications
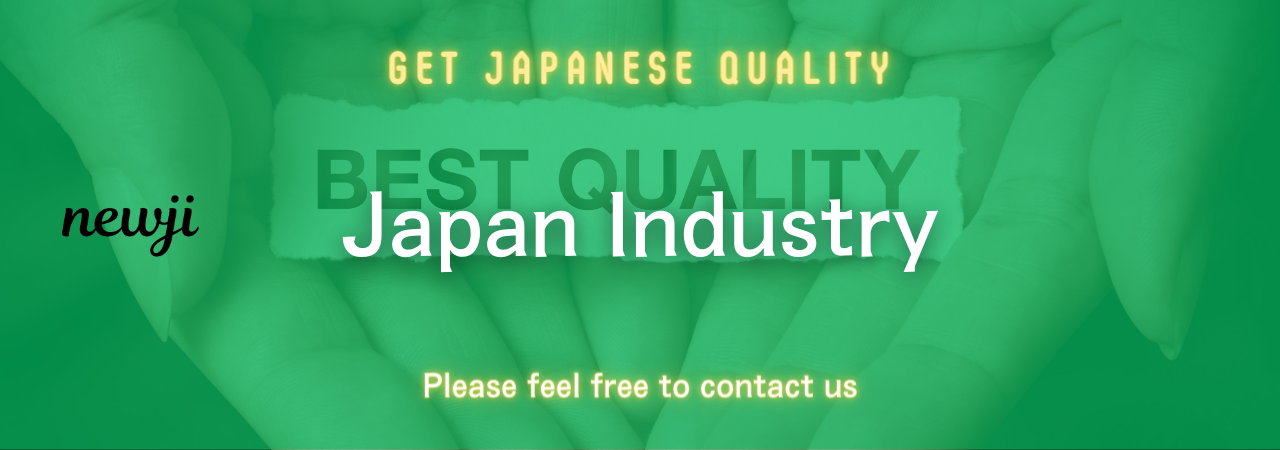
目次
Introduction to High-Speed Cutting Techniques
High-speed cutting in metalworking is revolutionizing the manufacturing industry.
With advanced machinery and innovative techniques, metal parts can now be produced with unprecedented speed and precision.
This not only enhances productivity but also reduces costs and improves the quality of the finished products.
High-speed cutting is becoming increasingly popular in various industries, from automotive to aerospace, due to its efficiency and effectiveness.
What is High-Speed Cutting?
High-speed cutting refers to the use of tools and machines able to operate at much higher speeds than traditional equipment.
The primary goal is to remove material quickly while maintaining or even improving surface finish and accuracy.
This cutting method reduces cycle times, increases throughput, and allows manufacturers to keep up with the demand for faster production rates.
Key Components of High-Speed Cutting
To achieve high-speed cutting, several components are critical.
These include advanced cutting tools like carbide or ceramic inserts, high-performance CNC machines, and appropriate coolant systems to manage the heat generated during the process.
The right combination of these elements ensures that the cutting process is efficient, stable, and produces high-quality results.
Benefits of High-Speed Cutting
High-speed cutting offers several significant advantages over traditional cutting methods.
Increased Productivity
One of the most immediate benefits is increased productivity.
With the ability to cut faster, companies can produce more parts in the same amount of time.
This can lead to shorter lead times and the ability to meet tight production schedules with ease.
Improved Product Quality
Despite the higher speed, high-speed cutting often results in better surface finishes and more precise dimensions.
This is because the faster cutting speeds minimize the deformations and other issues commonly associated with slower processes.
Consistency in quality is crucial in industries where precision is paramount.
Cost Reduction
By increasing the speed of production and reducing the amount of waste per part, companies can significantly cut down on operational costs.
High-speed cutting requires less machine power, reducing energy consumption, and extending the life of cutting tools due to more efficient processing.
Versatility Across Materials
High-speed cutting is not limited to a specific type of metal.
It can be effectively applied to a wide range of materials, from soft aluminum to hard steels and even non-metallic materials.
This versatility makes it a valuable technique across various sectors requiring different materials.
Applications of High-Speed Cutting
The applications of high-speed cutting techniques are vast, with impacts felt across various industrial fields.
Automotive Industry
In the automotive sector, high-speed cutting is crucial for manufacturing components that require high precision and durability.
Parts like engine blocks, brake rotors, and transmission parts benefit from high-speed cutting thanks to its ability to meet the industry’s exacting standards.
Aerospace Industry
The aerospace industry also relies heavily on high-speed cutting.
Here, precision and consistency are vital, with components often subjected to extreme conditions.
High-speed cutting is used to manufacture parts such as turbine blades and structural components that demand tight tolerances and lightweight materials.
Medical Device Manufacturing
In medical device manufacturing, where precision can mean the difference between success and failure, high-speed cutting ensures that parts such as surgical tools and implants meet strict quality standards.
This method provides the precision necessary to create parts with intricate designs and tiny dimensions.
Electronics Industry
The electronics industry benefits from high-speed cutting in the production of parts for consumer electronics, where miniaturization and precision are key.
High-speed cutting techniques are employed to create components like connectors and casings, which require exacting specifications and high-quality finishes.
Challenges in High-Speed Cutting
While high-speed cutting offers many benefits, it also presents several challenges that manufacturers must address to maximize its potential.
Heat Management
At high speeds, cutting generates more heat, which can affect both the tool and the material being cut.
Effective cooling systems and temperature control mechanisms are essential to prevent degradation of tool life and to maintain material integrity.
Tool Wear
The increased speed and forces involved in high-speed cutting can lead to accelerated tool wear.
Choosing the right materials for cutting tools, such as carbide or ceramics, is crucial to extend tool life and reduce downtime due to tool changes.
Machine Stability
Machines used for high-speed cutting must be incredibly stable and rigid to handle the demands of the process.
Any vibration or instability can lead to errors or imperfect surfaces, requiring rigorous testing and calibration to maintain the desired standards.
Future of High-Speed Cutting in Metalworking
The future of high-speed cutting in metalworking looks promising, with continuous advancements in technology and processes.
Advancements in Tooling
With ongoing research in materials science, new cutting tool materials and coatings are continually being developed.
These advancements will likely improve the speed, precision, and durability of high-speed cutting tools.
Integration with Automation
The integration of high-speed cutting with automation and smart manufacturing systems is expected to further enhance productivity.
This will allow real-time monitoring and adjustments to improve efficiency and reduce human intervention.
Conclusion
High-speed cutting techniques in metalworking are transforming production processes across industries.
By increasing productivity, improving quality, and reducing costs, these techniques offer significant advantages to manufacturers.
While challenges exist, advancements in technology promise a bright future for high-speed cutting, making it a cornerstone of modern manufacturing.
資料ダウンロード
QCD調達購買管理クラウド「newji」は、調達購買部門で必要なQCD管理全てを備えた、現場特化型兼クラウド型の今世紀最高の購買管理システムとなります。
ユーザー登録
調達購買業務の効率化だけでなく、システムを導入することで、コスト削減や製品・資材のステータス可視化のほか、属人化していた購買情報の共有化による内部不正防止や統制にも役立ちます。
NEWJI DX
製造業に特化したデジタルトランスフォーメーション(DX)の実現を目指す請負開発型のコンサルティングサービスです。AI、iPaaS、および先端の技術を駆使して、製造プロセスの効率化、業務効率化、チームワーク強化、コスト削減、品質向上を実現します。このサービスは、製造業の課題を深く理解し、それに対する最適なデジタルソリューションを提供することで、企業が持続的な成長とイノベーションを達成できるようサポートします。
オンライン講座
製造業、主に購買・調達部門にお勤めの方々に向けた情報を配信しております。
新任の方やベテランの方、管理職を対象とした幅広いコンテンツをご用意しております。
お問い合わせ
コストダウンが利益に直結する術だと理解していても、なかなか前に進めることができない状況。そんな時は、newjiのコストダウン自動化機能で大きく利益貢献しよう!
(Β版非公開)