- お役立ち記事
- Honing Technology in Manufacturing
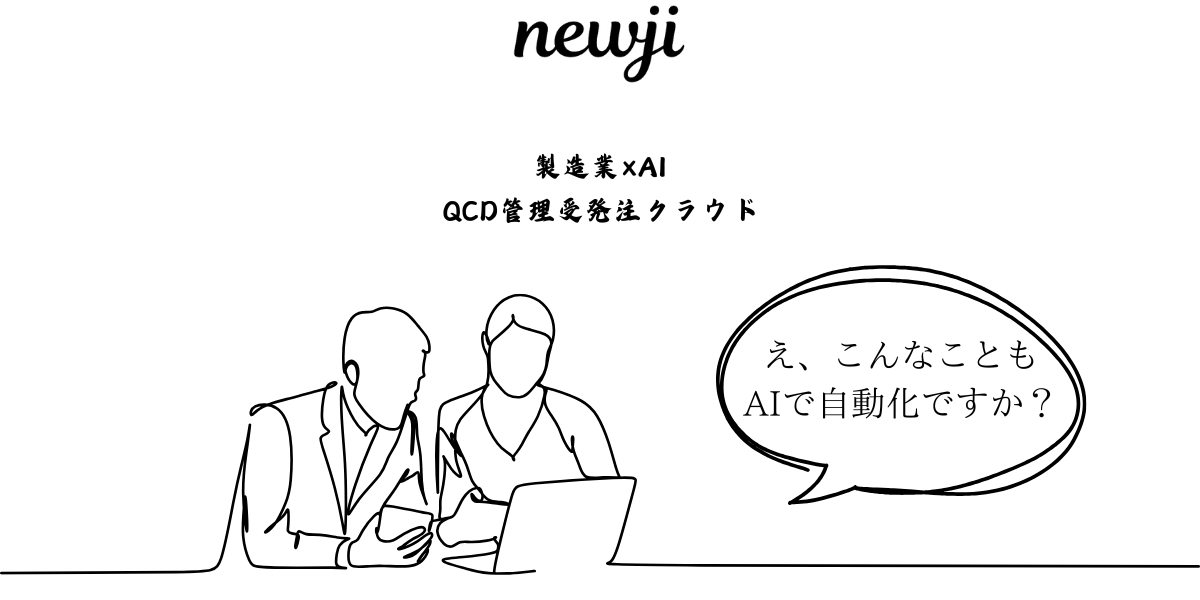
Honing Technology in Manufacturing
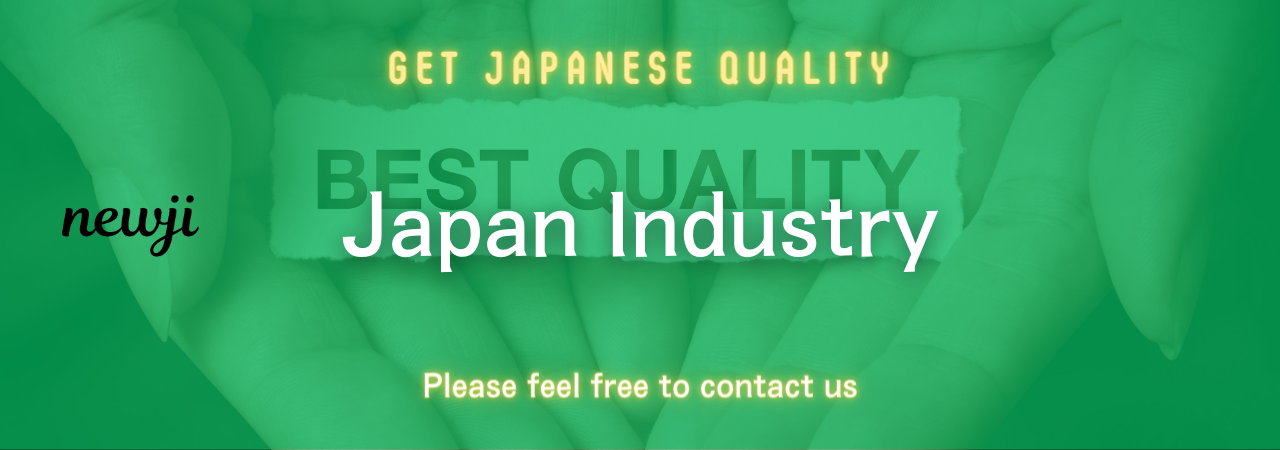
Understanding Honing in Manufacturing
In the world of manufacturing, precision is key.
One vital technique that contributes to this precision is honing.
But what exactly is honing, and why is it so important in manufacturing?
Simply put, honing is a process used to improve the geometric form or texture of a surface.
It plays a crucial role in creating high-quality products, ensuring they meet exact specifications and perform optimally.
The Basics of Honing
Honing is mainly used to refine the surface of a part, ensuring it is smooth and meets precise dimensional tolerances.
This technique involves an abrasive grinding stone or tool that follows a controlled path across the material’s surface.
Honing is particularly effective in correcting the roundness, taper, and size of bores or holes.
The abrasives used for honing can range from stones composed of natural minerals to those made from manufactured compounds such as aluminum oxide or silicon carbide.
The choice of honing stones greatly influences the surface finish and material removal rate, making it a highly adaptable process for different materials and specifications.
Importance of Honing in Industry
Honing is a critical process in a variety of industries, including automotive, aerospace, hydraulics, and medical manufacturing.
In the automotive industry, for instance, honing is used to finish engine cylinders.
This ensures proper functioning by reducing friction, thus enhancing efficiency and longevity.
In aerospace and hydraulics, where tolerance levels are exceptionally tight, honing guarantees the reliability and safety of components, which might operate under extreme conditions.
Medical manufacturing also utilizes honing to produce precise and smooth surgical instruments and implants, where patient safety and effectiveness are paramount.
Types of Honing Processes
Several honing techniques are used across different industries, tailored to specific applications and requirements.
One common method is **manual honing**, which involves hand-held tools for smaller or less critical surfaces.
Though it requires skill and experience, manual honing allows for excellent control, making it ideal for delicate tasks.
**Machine honing**, on the other hand, is used for larger-scale operations.
These machines are capable of honing thousands of parts with consistent precision and are primarily employed in mass production facilities.
Machine honing can be further categorized into vertical and horizontal honing machines, each suited for specific types of parts.
**Single-pass honing** is another specialized process where the tool only passes through the part once.
This method is particularly efficient for high-volume production runs, as it is faster than traditional multi-pass honing, though it requires precise initial setups.
Advancements in Honing Technology
The honing process has come a long way with modern technology advancing its applications and efficacy.
With the integration of CNC (Computer Numerical Control) technology, honing machines have become more automated.
This advancement allows for greater precision, repeatability, and speed, effectively reducing production time and waste.
Furthermore, developments in abrasive materials have paved the way for enhanced honing stones that last longer and cut more efficiently.
Research continues into super-abrasives such as cubic boron nitride and diamond, which promise even greater efficiency and durability.
Moreover, honing machines are now equipped with advanced measuring systems and sensors.
These enable operators to monitor the process closely and make real-time adjustments, ensuring superior quality control.
Predictive maintenance technologies are also integrated into modern systems, minimizing downtime and operational costs.
Challenges and Considerations
Despite its advantages, honing is not without challenges.
Choosing the right honing process and materials is critical and depends on factors like part size, material composition, and desired finish.
Improper process selection can lead to defects, increased waste, and higher production costs.
Additionally, honing abrasive particles can generate a significant amount of heat during the process, posing a risk of overheating and warping the material.
To mitigate this, effective cooling and lubrication systems must be implemented within the honing machine setup.
Finally, operators need to be skilled and trained to manage the intricacies of the honing process, especially in manual honing settings.
As technology advances, continuous learning and adaptation are necessary for manufacturers to maintain an edge in competitive markets.
Conclusion
Honing has established itself as an indispensable part of the manufacturing industry, contributing significantly to the accuracy and quality of finished products.
Its ability to refine surfaces to meet stringent specifications ensures the functional and aesthetic standards of manufactured parts.
With ongoing advancements in technology and materials, honing continues to evolve, offering even greater precision and efficiency in the manufacturing landscape.
For industries that prioritize product integrity and performance, honing remains a key process, essential for keeping up with ever-demanding market expectations.
資料ダウンロード
QCD調達購買管理クラウド「newji」は、調達購買部門で必要なQCD管理全てを備えた、現場特化型兼クラウド型の今世紀最高の購買管理システムとなります。
ユーザー登録
調達購買業務の効率化だけでなく、システムを導入することで、コスト削減や製品・資材のステータス可視化のほか、属人化していた購買情報の共有化による内部不正防止や統制にも役立ちます。
NEWJI DX
製造業に特化したデジタルトランスフォーメーション(DX)の実現を目指す請負開発型のコンサルティングサービスです。AI、iPaaS、および先端の技術を駆使して、製造プロセスの効率化、業務効率化、チームワーク強化、コスト削減、品質向上を実現します。このサービスは、製造業の課題を深く理解し、それに対する最適なデジタルソリューションを提供することで、企業が持続的な成長とイノベーションを達成できるようサポートします。
オンライン講座
製造業、主に購買・調達部門にお勤めの方々に向けた情報を配信しております。
新任の方やベテランの方、管理職を対象とした幅広いコンテンツをご用意しております。
お問い合わせ
コストダウンが利益に直結する術だと理解していても、なかなか前に進めることができない状況。そんな時は、newjiのコストダウン自動化機能で大きく利益貢献しよう!
(Β版非公開)