- お役立ち記事
- How Digital Thread Technology Improves Manufacturing Productivity
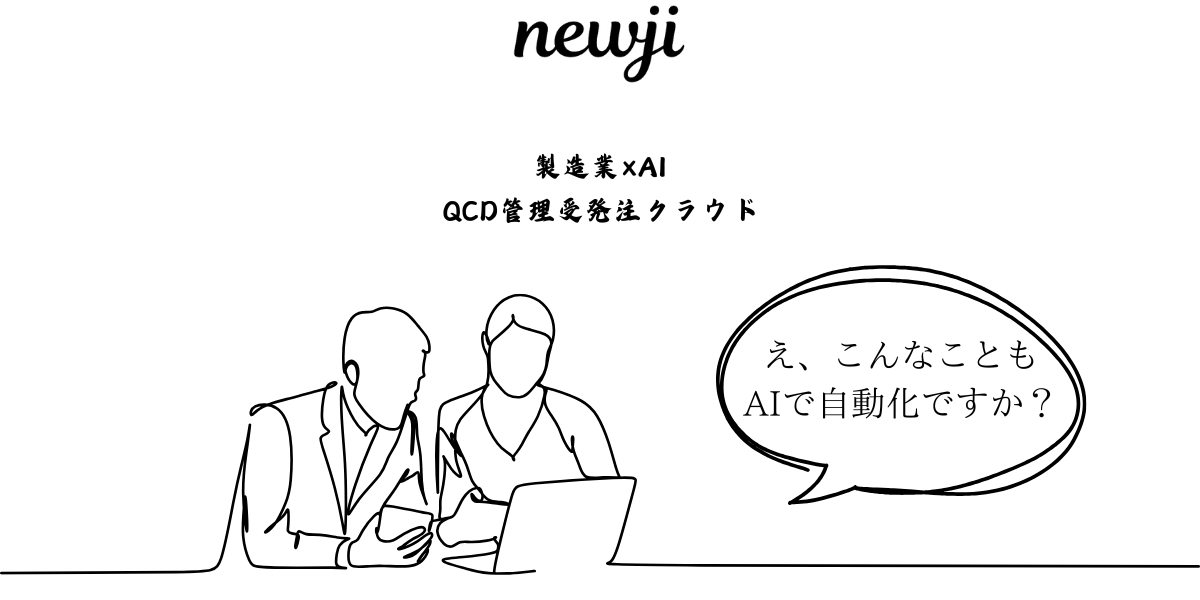
How Digital Thread Technology Improves Manufacturing Productivity
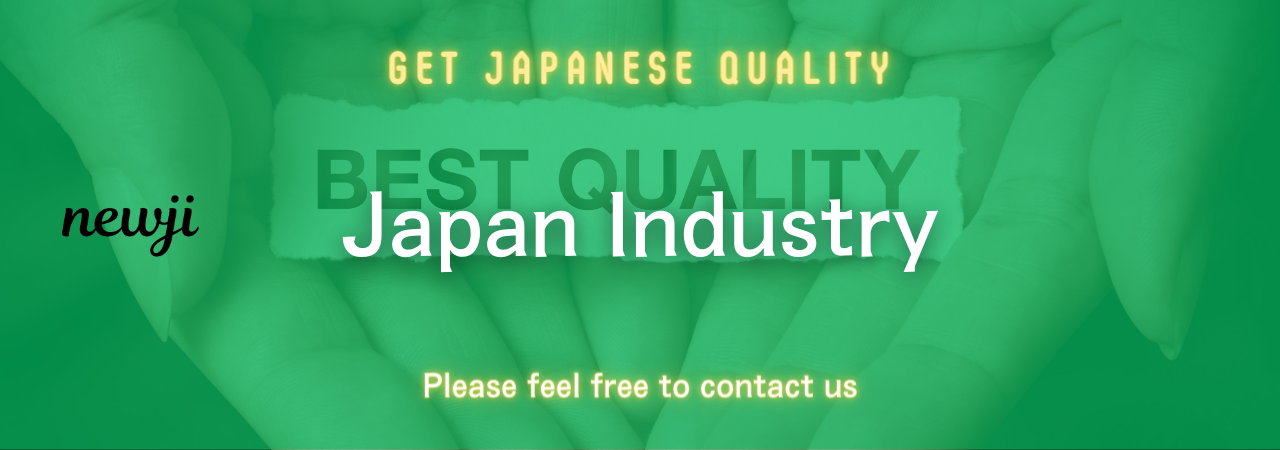
In today’s rapidly advancing technological landscape, digital thread technology has emerged as a groundbreaking tool for transforming the manufacturing sector.
Its potential to streamline processes, enhance productivity, and foster innovation is becoming increasingly evident.
Let’s dive into how digital thread technology is making waves in manufacturing.
目次
Understanding Digital Thread Technology
Digital thread is a communication framework that integrates data flow throughout the lifecycle of a product.
It creates a seamless stream of information from the initial design concept to its final delivery and beyond.
Essentially, it connects various processes, tools, and devices within a manufacturing ecosystem.
The Backbone of Connected Manufacturing
By creating a unified digital representation of a product, digital thread technology serves as the backbone for connected manufacturing.
It enables real-time data sharing, communication across different systems, and aids in maintaining a consistent flow of information.
This interconnectedness ensures that everyone involved in the production process has access to the most up-to-date information.
Enhancing Efficiency through Improved Data Management
One of the primary benefits of digital thread technology is its ability to enhance data management across the manufacturing lifecycle.
With all pertinent data linked and accessible, manufacturers can eliminate data silos and redundancies.
Streamlined Data Access
In traditional manufacturing setups, data is often scattered across various platforms and tools.
This can lead to delays and errors.
Digital thread technology centralizes data, ensuring that all stakeholders, from designers to engineers to production line workers, have immediate access to necessary information.
This improves decision-making and reduces the time spent locating data.
Improved Traceability and Transparency
Digital thread technology provides complete visibility into every phase of the product lifecycle.
This traceability is particularly beneficial for quality control and regulatory compliance.
Any issues can be quickly identified and addressed, as the entire history of a product is accessible and transparent.
Facilitating Collaboration and Innovation
Collaboration is a critical component of innovation in manufacturing.
Digital thread technology fosters teamwork by bridging the gap between different departments and external partners.
Real-Time Collaboration
With digital thread technology, teams can collaborate in real-time, regardless of their physical locations.
Designers can communicate directly with engineers and production teams, sharing insights and feedback instantly.
This immediate exchange of ideas spurs innovation and accelerates the product development cycle.
Integration with Emerging Technologies
Digital thread technology seamlessly integrates with other emerging technologies such as artificial intelligence (AI), machine learning (ML), and the Internet of Things (IoT).
This integration enables advanced analytics and predictive maintenance, further enhancing productivity.
For instance, sensors can detect potential equipment failures before they occur, minimizing downtime and improving overall efficiency.
Revolutionizing Product Lifecycle Management
Product Lifecycle Management (PLM) is a holistic approach to managing the entire lifecycle of a product.
Digital thread technology takes PLM to new heights by ensuring all lifecycle stages are interconnected.
Optimized Design and Development
During the design phase, digital thread technology allows for virtual simulations and testing.
This helps in identifying potential flaws and optimizing designs before physical prototypes are created.
As a result, the development process becomes faster and more cost-effective.
Efficient Production and Quality Assurance
In the production phase, having a comprehensive digital thread ensures that all manufacturing processes are aligned with design specifications.
This reduces the likelihood of deviations and errors.
For quality assurance, continuous monitoring and instant feedback loops ensure that any variations are promptly corrected.
Streamlined Supply Chain Management
The impact of digital thread technology extends beyond the walls of the manufacturing facility.
It also plays a crucial role in supply chain management.
With end-to-end visibility, manufacturers can better manage their suppliers, optimize inventory levels, and ensure timely delivery of materials.
This cohesion is essential for maintaining smooth operations and meeting customer demands.
Case Studies: Real-World Applications
Several leading manufacturers have already adopted digital thread technology and witnessed significant improvements in their operations.
Here are a couple of examples showcasing its impact.
Aviation Industry
In the aviation industry, digital thread technology is pivotal for managing the complex lifecycle of aircraft components.
From design and manufacturing to maintenance and upgrades, the digital thread ensures that every aspect is meticulously tracked.
This not only enhances safety but also improves the efficiency of servicing aircraft.
Automotive Manufacturing
Automotive manufacturers are leveraging digital thread technology to innovate and stay competitive.
By integrating digital threads into their production lines, they can rapidly adapt to changes in market demands and new technologies.
This agility allows for faster time-to-market for new models and features.
Challenges and the Future of Digital Thread Technology
While digital thread technology offers numerous benefits, its implementation does come with challenges.
Data security, integration with legacy systems, and the need for skilled personnel are some of the hurdles that need to be addressed.
Overcoming Implementation Challenges
To successfully implement digital thread technology, manufacturers must invest in robust cybersecurity measures to protect sensitive data.
Additionally, organizations may need to upgrade or replace legacy systems that are not compatible with the new technology.
Providing adequate training for employees to effectively use digital thread tools is also crucial.
The Future is Bright
Despite these challenges, the future of digital thread technology in manufacturing looks promising.
As technology continues to evolve, manufacturers who embrace digital threads will gain a competitive edge.
The ability to harness real-time data, foster innovation, and optimize operations will become even more critical in the years to come.
In conclusion, digital thread technology is revolutionizing manufacturing by connecting every aspect of the product lifecycle.
Its ability to enhance efficiency, facilitate collaboration, and improve data management makes it a vital tool for modern manufacturers.
As more companies adopt and integrate digital thread technology, the potential for increased productivity and innovation will undoubtedly grow, ushering in a new era of manufacturing excellence.
資料ダウンロード
QCD調達購買管理クラウド「newji」は、調達購買部門で必要なQCD管理全てを備えた、現場特化型兼クラウド型の今世紀最高の購買管理システムとなります。
ユーザー登録
調達購買業務の効率化だけでなく、システムを導入することで、コスト削減や製品・資材のステータス可視化のほか、属人化していた購買情報の共有化による内部不正防止や統制にも役立ちます。
NEWJI DX
製造業に特化したデジタルトランスフォーメーション(DX)の実現を目指す請負開発型のコンサルティングサービスです。AI、iPaaS、および先端の技術を駆使して、製造プロセスの効率化、業務効率化、チームワーク強化、コスト削減、品質向上を実現します。このサービスは、製造業の課題を深く理解し、それに対する最適なデジタルソリューションを提供することで、企業が持続的な成長とイノベーションを達成できるようサポートします。
オンライン講座
製造業、主に購買・調達部門にお勤めの方々に向けた情報を配信しております。
新任の方やベテランの方、管理職を対象とした幅広いコンテンツをご用意しております。
お問い合わせ
コストダウンが利益に直結する術だと理解していても、なかなか前に進めることができない状況。そんな時は、newjiのコストダウン自動化機能で大きく利益貢献しよう!
(Β版非公開)