- お役立ち記事
- How Digital Transformation (DX) is Revolutionizing Japanese Manufacturing Industry
月間76,176名の
製造業ご担当者様が閲覧しています*
*2025年3月31日現在のGoogle Analyticsのデータより
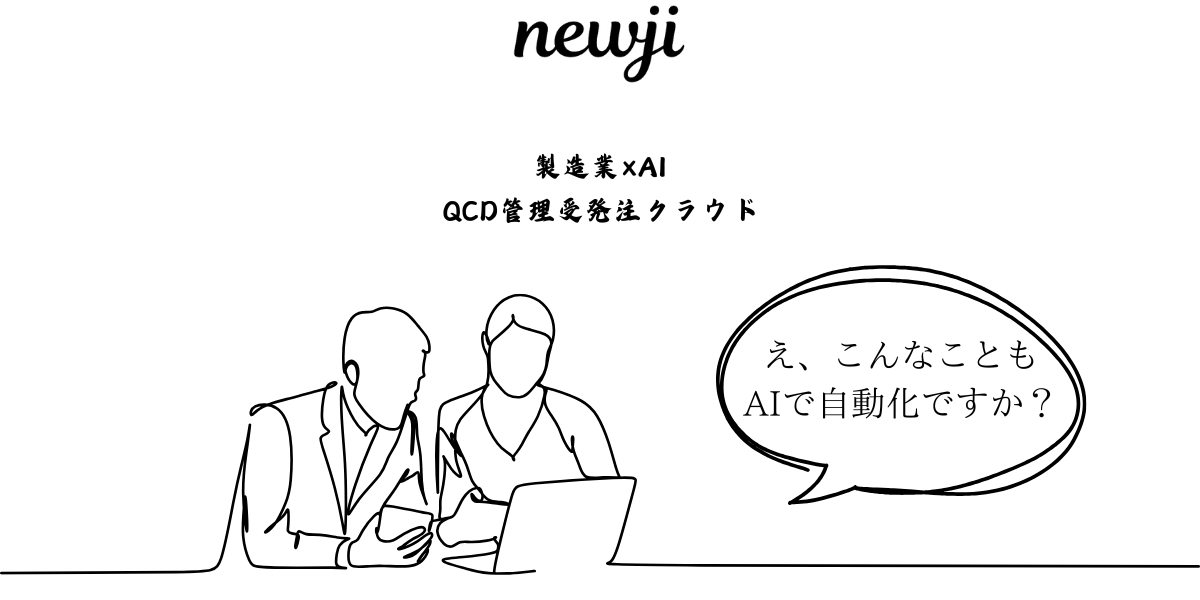
How Digital Transformation (DX) is Revolutionizing Japanese Manufacturing Industry
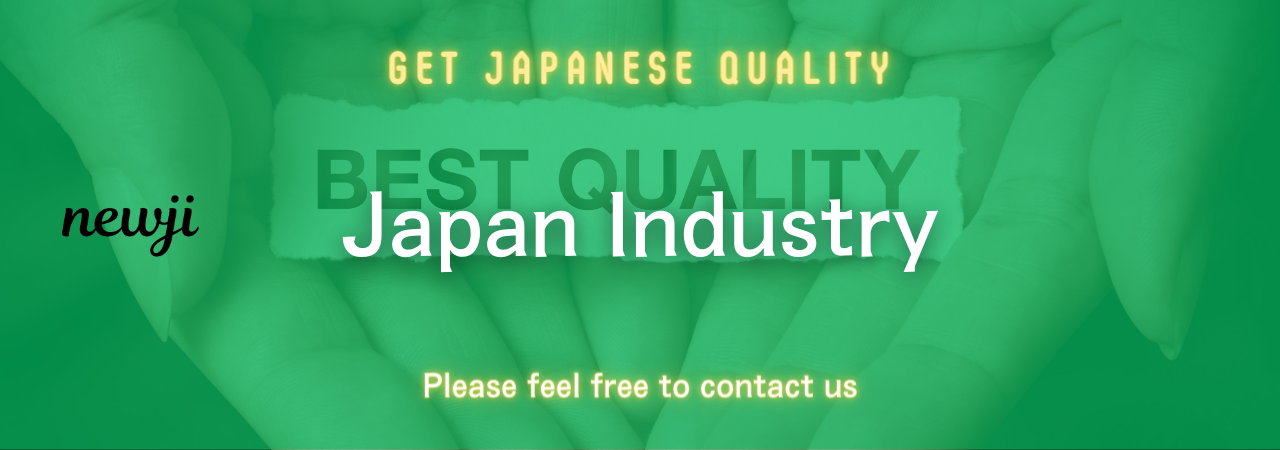
目次
Introduction to Digital Transformation (DX) in Japanese Manufacturing
The manufacturing sector in Japan, known for its precision, quality, and innovation, has been a global leader for decades.
However, the landscape of manufacturing is rapidly evolving, influenced heavily by advancements in digital technologies.
Digital Transformation (DX) is not just a buzzword; it heralds a new era of efficiency, quality control, and strategic procurement.
For Japanese manufacturers, embracing DX presents both opportunities and challenges. This article delves into how DX is revolutionizing the Japanese manufacturing industry from multiple angles, including procurement, logistics, production, and quality control.
The Drivers of Digital Transformation in Japanese Manufacturing
Global Competition and Customer Expectations
Global competition is fiercer than ever, pushing manufacturers to innovate continually.
Customers today expect high-quality products delivered quickly and at competitive prices.
DX enables manufacturers to meet these expectations by streamlining processes and improving agility.
Technological Advancements
The rapid development of technologies such as the Internet of Things (IoT), Artificial Intelligence (AI), and Machine Learning (ML) is a significant driver of DX.
These technologies help in predictive maintenance, real-time data analysis, and automating routine tasks, making operations more efficient and productive.
Government Initiatives
The Japanese government has been actively promoting DX through various initiatives and regulations aimed at fostering technological adoption.
Programs such as the “Connected Industries” initiative encourage manufacturers to integrate digital technologies across their operations.
Impact of DX on Procurement and Purchasing
Enhanced Supplier Management
One of the primary benefits of DX in procurement is the improved relationship with suppliers.
Digital platforms enable real-time communication, making it easier to share information and collaborate.
This transparency fosters trust and facilitates better negotiation terms.
Automated Procurement Processes
Traditional procurement processes are often manual, time-consuming, and error-prone.
Automation tools streamline these processes, from requisition to payment, reducing the risk of errors and freeing up human resources to focus on strategic tasks.
Data-Driven Decision Making
DX allows procurement teams to leverage data analytics for better decision-making.
By analyzing historical data, market trends, and supplier performance, companies can make more informed choices about where to source materials, how to negotiate contracts, and when to place orders.
Advantages and Disadvantages of DX in Manufacturing
Advantages
Increased Efficiency
Automation of routine tasks and optimized workflows lead to significant time savings.
This increased efficiency translates to lower operational costs and faster time-to-market for new products.
Improved Quality Control
Advanced digital tools enable real-time monitoring and analytics, leading to higher quality products.
Techniques such as predictive maintenance can identify potential issues before they become critical, reducing downtime and ensuring consistent quality.
Better Customer Satisfaction
Enhanced efficiency and quality control directly impact customer satisfaction.
With the ability to deliver high-quality products quickly, manufacturers can meet customer demands more effectively, leading to higher loyalty and repeat business.
Disadvantages
High Initial Investment
The adoption of digital technologies often requires a substantial initial investment in infrastructure, software, and training.
For small to medium-sized enterprises, this can be a significant burden.
Skills Gap
Digital transformation necessitates a skilled workforce familiar with new technologies.
This may require comprehensive training programs, which can be both time-consuming and expensive.
Data Security Concerns
With increased reliance on digital tools and platforms, the risk of cyber-attacks and data breaches also rises.
Manufacturers must invest in robust cybersecurity measures to protect sensitive information.
Supplier Negotiation Techniques in the Age of DX
Leveraging Data Analytics
Data analytics can be a powerful tool in supplier negotiations.
By analyzing market trends and historical performance data, procurement teams can enter negotiations armed with valuable insights.
This knowledge can lead to more favorable terms and conditions.
Real-Time Communication
Digital platforms facilitate real-time communication between manufacturers and suppliers.
This ensures that both parties are always on the same page, reducing misunderstandings and building stronger relationships.
Collaborative Planning
Using digital tools for collaborative planning can help align production schedules with supplier capabilities.
This minimizes disruptions in the supply chain and ensures a steady flow of materials.
Current Market Conditions for DX in Japan
Growing Investments
Investment in DX technologies is on the rise in Japan.
Both large corporations and SMEs are recognizing the importance of digital transformation and are allocating resources accordingly.
Government Support
As mentioned earlier, government initiatives are playing a crucial role in promoting DX.
Various subsidies and grants are available to encourage manufacturers to adopt digital technologies.
Technological Ecosystem
Japan boasts a robust technological ecosystem, with numerous companies specializing in DX solutions.
This ecosystem provides valuable support and resources for manufacturers looking to embark on their DX journey.
Best Practices for Implementing DX in Manufacturing
Start Small, Scale Gradually
It is advisable to start with pilot projects to test the feasibility and benefits of DX technologies.
Once proven successful, these projects can be scaled gradually across the organization.
Invest in Training
Continuous training programs are essential to bridge the skills gap.
Investing in employee development ensures that the workforce is well-equipped to handle new technologies.
Focus on Cybersecurity
With the increasing reliance on digital platforms, robust cybersecurity measures are vital.
Regular audits, employee training, and investment in security infrastructure can mitigate risks.
Conclusion
Digital transformation is revolutionizing the Japanese manufacturing industry by enhancing efficiency, improving quality control, and enabling data-driven decision-making.
While the journey is fraught with challenges such as high initial investments and cybersecurity concerns, the long-term benefits far outweigh these hurdles.
By leveraging advanced technologies and following best practices, Japanese manufacturers can stay competitive in the global market and continue to uphold their legacy of excellence.
The future of manufacturing in Japan is undoubtedly digital, and those who embrace this transformation will lead the way into the next era of industrial innovation.
資料ダウンロード
QCD管理受発注クラウド「newji」は、受発注部門で必要なQCD管理全てを備えた、現場特化型兼クラウド型の今世紀最高の受発注管理システムとなります。
ユーザー登録
受発注業務の効率化だけでなく、システムを導入することで、コスト削減や製品・資材のステータス可視化のほか、属人化していた受発注情報の共有化による内部不正防止や統制にも役立ちます。
NEWJI DX
製造業に特化したデジタルトランスフォーメーション(DX)の実現を目指す請負開発型のコンサルティングサービスです。AI、iPaaS、および先端の技術を駆使して、製造プロセスの効率化、業務効率化、チームワーク強化、コスト削減、品質向上を実現します。このサービスは、製造業の課題を深く理解し、それに対する最適なデジタルソリューションを提供することで、企業が持続的な成長とイノベーションを達成できるようサポートします。
製造業ニュース解説
製造業、主に購買・調達部門にお勤めの方々に向けた情報を配信しております。
新任の方やベテランの方、管理職を対象とした幅広いコンテンツをご用意しております。
お問い合わせ
コストダウンが利益に直結する術だと理解していても、なかなか前に進めることができない状況。そんな時は、newjiのコストダウン自動化機能で大きく利益貢献しよう!
(β版非公開)