- お役立ち記事
- How Equipment Monitoring Systems Are Revolutionizing Japanese Manufacturing Efficiency
月間76,176名の
製造業ご担当者様が閲覧しています*
*2025年3月31日現在のGoogle Analyticsのデータより
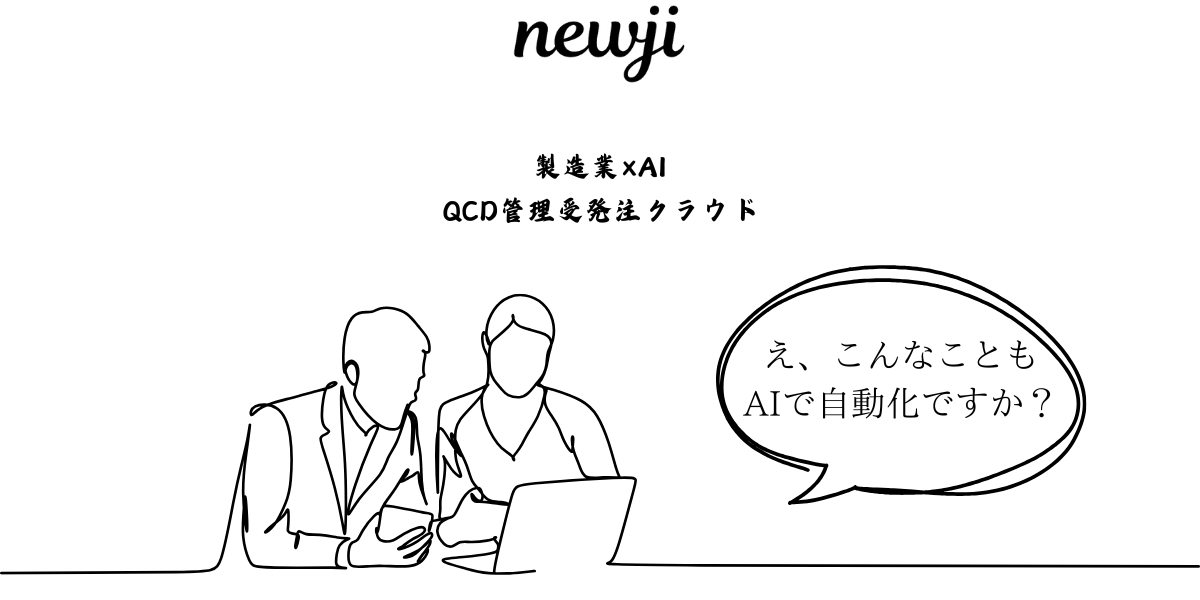
How Equipment Monitoring Systems Are Revolutionizing Japanese Manufacturing Efficiency
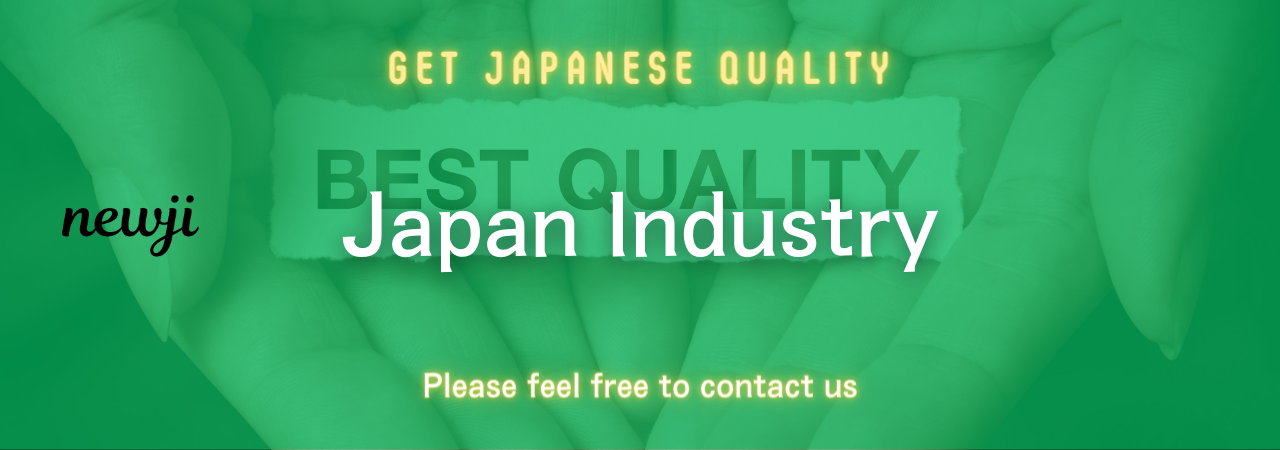
目次
Introduction to Equipment Monitoring Systems in Japanese Manufacturing
Japanese manufacturing has long been synonymous with precision, quality, and efficiency. In recent years, the integration of advanced equipment monitoring systems has further revolutionized the industry, enhancing productivity and maintaining Japan’s competitive edge in the global market. This article delves into how these systems are transforming manufacturing processes, the advantages and disadvantages they bring, effective supplier negotiation techniques, current market conditions, and best practices for implementation.
The Evolution of Equipment Monitoring Systems
From Traditional Methods to Digital Solutions
Traditionally, Japanese manufacturers relied on manual inspections and scheduled maintenance to ensure equipment functionality. While effective to an extent, these methods were time-consuming and prone to human error. The advent of digital technologies introduced equipment monitoring systems that provide real-time data, predictive maintenance, and extensive analytics, significantly enhancing operational efficiency.
Key Technological Advancements
Several technological advancements have propelled the development of modern equipment monitoring systems:
– **Internet of Things (IoT):** Connects machines and sensors, enabling seamless data exchange.
– **Artificial Intelligence (AI) and Machine Learning (ML):** Analyzes data patterns to predict equipment failures and optimize performance.
– **Big Data Analytics:** Processes vast amounts of data to derive actionable insights.
– **Cloud Computing:** Provides scalable storage and processing power for data-intensive applications.
These technologies collectively contribute to the creation of intelligent monitoring systems that are integral to modern Japanese manufacturing.
Advantages of Equipment Monitoring Systems
Enhanced Operational Efficiency
One of the primary benefits of equipment monitoring systems is the significant improvement in operational efficiency. Real-time monitoring allows for immediate detection of anomalies, reducing downtime and ensuring continuous production. By optimizing machine usage, manufacturers can achieve higher throughput without compromising quality.
Predictive Maintenance
Predictive maintenance is a game-changer in manufacturing. Instead of relying on scheduled maintenance, which may lead to unnecessary interventions or unexpected failures, predictive maintenance uses data-driven insights to perform maintenance only when necessary. This approach not only extends equipment lifespan but also reduces maintenance costs and minimizes production interruptions.
Quality Control and Consistency
Maintaining consistent product quality is crucial for Japanese manufacturers. Equipment monitoring systems provide detailed data on machine performance, ensuring that production processes remain within specified parameters. This leads to uniform product quality, fewer defects, and enhanced customer satisfaction.
Cost Savings
By minimizing downtime, reducing maintenance costs, and optimizing resource utilization, equipment monitoring systems contribute to substantial cost savings. Additionally, the ability to predict and prevent equipment failures reduces the financial impact of unexpected breakdowns.
Improved Safety
Safety is paramount in manufacturing environments. Equipment monitoring systems can detect hazardous conditions and trigger alarms or automated shutdowns to prevent accidents. This proactive approach to safety enhances workplace conditions and protects employees from potential harm.
Disadvantages and Challenges
High Initial Investment
Implementing advanced equipment monitoring systems requires a significant initial investment. Costs include purchasing hardware and software, integrating systems into existing infrastructure, and training staff. For some manufacturers, especially small and medium-sized enterprises (SMEs), the upfront costs can be a barrier to adoption.
Data Security Concerns
With the increased reliance on digital technologies and data exchange, data security becomes a critical concern. Manufacturers must ensure that their equipment monitoring systems are protected against cyber threats, data breaches, and unauthorized access. Implementing robust cybersecurity measures is essential to safeguard sensitive information.
Integration with Legacy Systems
Many Japanese manufacturing facilities operate with legacy systems that may not be compatible with modern equipment monitoring technologies. Integrating new systems with existing infrastructure can be complex and time-consuming, requiring careful planning and technical expertise.
Skill Gap and Training
The successful implementation of equipment monitoring systems requires a workforce proficient in digital technologies and data analysis. Bridging the skill gap through comprehensive training programs is crucial to maximize the benefits of these systems.
Supplier Negotiation Techniques for Procurement
Building Strong Relationships
In Japanese business culture, building strong, trust-based relationships with suppliers is essential. Establishing long-term partnerships can lead to better terms, reliability, and collaborative problem-solving. Investing time in relationship-building fosters mutual respect and understanding.
Understanding Supplier Capabilities
Before entering negotiations, thoroughly understanding the supplier’s capabilities, strengths, and limitations is vital. This knowledge allows manufacturers to set realistic expectations, identify areas for collaboration, and negotiate terms that are beneficial for both parties.
Leveraging Technology for Negotiations
Utilizing data from equipment monitoring systems can strengthen negotiation positions. By presenting evidence of production needs, performance metrics, and potential areas for improvement, manufacturers can negotiate more effectively, ensuring that suppliers align with their operational requirements.
Focusing on Total Cost of Ownership (TCO)
Negotiations should consider the total cost of ownership rather than just the initial purchase price. Factors such as maintenance costs, lifecycle expenses, and potential savings from efficiency improvements should be part of the negotiation strategy to ensure comprehensive value.
Emphasizing Quality and Reliability
Japanese manufacturing prioritizes quality and reliability. During negotiations, emphasizing these aspects ensures that suppliers understand the critical nature of their role in the production process and are committed to maintaining high standards.
Market Conditions Impacting Equipment Monitoring Systems
Global Supply Chain Dynamics
The global supply chain landscape significantly affects the procurement and implementation of equipment monitoring systems. Fluctuations in supply chain stability, availability of components, and geopolitical factors can influence the cost and accessibility of these technologies.
Technological Advancements
Rapid advancements in technology drive the continuous evolution of equipment monitoring systems. Staying abreast of the latest developments ensures that manufacturers can adopt cutting-edge solutions that offer competitive advantages.
Economic Factors
Economic conditions, including inflation rates, currency exchange fluctuations, and overall economic growth, impact the investment decisions of manufacturers. A stable economic environment encourages investment in new technologies, while economic uncertainty may lead to cautious spending.
Regulatory Environment
Regulatory standards related to data security, environmental impact, and workplace safety influence the adoption of equipment monitoring systems. Compliance with these regulations is essential to avoid legal repercussions and maintain operational licenses.
Competitive Pressure
Intense competition in the manufacturing sector drives the need for continuous improvement. Equipment monitoring systems provide the necessary tools to enhance efficiency, reduce costs, and maintain high-quality standards, enabling manufacturers to stay ahead of competitors.
Best Practices for Implementing Equipment Monitoring Systems
Comprehensive Needs Assessment
Before implementing an equipment monitoring system, conduct a thorough needs assessment to identify specific requirements, goals, and challenges. This ensures that the chosen system aligns with the manufacturing processes and addresses key pain points effectively.
Choosing the Right Technology Partner
Selecting a reliable technology partner is crucial for successful implementation. Evaluate potential partners based on their expertise, track record, support services, and ability to customize solutions to meet specific manufacturing needs.
Integration with Existing Systems
Ensure that the new equipment monitoring system seamlessly integrates with existing machinery, software, and workflows. This reduces disruption to operations and facilitates a smooth transition to the new system.
Employee Training and Engagement
Invest in comprehensive training programs to equip employees with the necessary skills to operate and manage the new system. Engaging staff in the implementation process fosters a culture of innovation and ensures that the system is utilized to its full potential.
Data Management and Security
Establish robust data management and security protocols to protect sensitive information. Implement measures such as encryption, access controls, and regular security audits to safeguard data integrity and prevent unauthorized access.
Continuous Monitoring and Improvement
Post-implementation, continuously monitor the performance of the equipment monitoring system and seek feedback from users. Use this information to make necessary adjustments, optimize processes, and drive continuous improvement.
Scalability and Future-Proofing
Choose systems that are scalable and adaptable to future technological advancements. This ensures that the investment remains valuable as the manufacturing landscape evolves and new requirements emerge.
Case Studies: Success Stories from Japanese Manufacturers
Automotive Industry Leader
A leading Japanese automotive manufacturer implemented an advanced equipment monitoring system across its production lines. The system’s real-time data analysis and predictive maintenance capabilities reduced machine downtime by 30%. Additionally, the enhanced data insights allowed for optimized production schedules, resulting in a 15% increase in overall efficiency.
Electronics Manufacturing Giant
An electronics manufacturer integrated IoT-based monitoring systems into its assembly lines. The data collected facilitated quality control improvements, reducing defect rates by 20%. The company also experienced significant cost savings through efficient resource utilization and minimized waste.
Precision Machinery Manufacturer
A precision machinery manufacturer adopted AI-powered monitoring systems to oversee its complex production processes. The system’s ability to predict equipment failures enabled proactive maintenance, extending machinery lifespan by 25%. Furthermore, the detailed performance analytics supported continuous process enhancements, maintaining the company’s reputation for high-quality products.
The Future of Equipment Monitoring in Japanese Manufacturing
Integration with Industry 4.0
Industry 4.0, characterized by smart factories and interconnected systems, is shaping the future of Japanese manufacturing. Equipment monitoring systems will play a pivotal role in this transformation, enabling seamless data exchange, automation, and enhanced decision-making capabilities.
Advancements in AI and Machine Learning
AI and machine learning will drive the next wave of innovations in equipment monitoring. Predictive analytics will become more sophisticated, allowing for even more accurate forecasting of equipment performance and maintenance needs.
Increased Adoption of Edge Computing
Edge computing will become increasingly important, enabling real-time data processing and analysis directly at the source of data generation. This reduces latency, enhances cybersecurity, and supports more efficient operational workflows.
Sustainable Manufacturing Practices
Sustainability will continue to be a key focus area. Equipment monitoring systems will assist manufacturers in reducing energy consumption, minimizing waste, and optimizing resource usage, contributing to more environmentally friendly manufacturing practices.
Enhanced Human-Machine Collaboration
The future will see greater collaboration between humans and machines. Equipment monitoring systems will provide valuable insights and support decision-making, allowing human workers to focus on more strategic and creative tasks, ultimately leading to a more innovative and productive workforce.
Conclusion
Equipment monitoring systems are undeniably transforming Japanese manufacturing, driving unprecedented levels of efficiency, quality, and competitiveness. While challenges such as high initial investments and data security concerns exist, the benefits far outweigh the drawbacks. By adopting best practices, leveraging advanced technologies, and fostering strong supplier relationships, Japanese manufacturers can harness the full potential of these systems. As the industry continues to evolve, equipment monitoring will remain a cornerstone of innovation, ensuring that Japanese manufacturing remains a global leader in quality and efficiency.
資料ダウンロード
QCD管理受発注クラウド「newji」は、受発注部門で必要なQCD管理全てを備えた、現場特化型兼クラウド型の今世紀最高の受発注管理システムとなります。
ユーザー登録
受発注業務の効率化だけでなく、システムを導入することで、コスト削減や製品・資材のステータス可視化のほか、属人化していた受発注情報の共有化による内部不正防止や統制にも役立ちます。
NEWJI DX
製造業に特化したデジタルトランスフォーメーション(DX)の実現を目指す請負開発型のコンサルティングサービスです。AI、iPaaS、および先端の技術を駆使して、製造プロセスの効率化、業務効率化、チームワーク強化、コスト削減、品質向上を実現します。このサービスは、製造業の課題を深く理解し、それに対する最適なデジタルソリューションを提供することで、企業が持続的な成長とイノベーションを達成できるようサポートします。
製造業ニュース解説
製造業、主に購買・調達部門にお勤めの方々に向けた情報を配信しております。
新任の方やベテランの方、管理職を対象とした幅広いコンテンツをご用意しております。
お問い合わせ
コストダウンが利益に直結する術だと理解していても、なかなか前に進めることができない状況。そんな時は、newjiのコストダウン自動化機能で大きく利益貢献しよう!
(β版非公開)