- お役立ち記事
- “How Japanese Manufacturing Excels in Compliance with Standards: A Blueprint for Global Success”
“How Japanese Manufacturing Excels in Compliance with Standards: A Blueprint for Global Success”
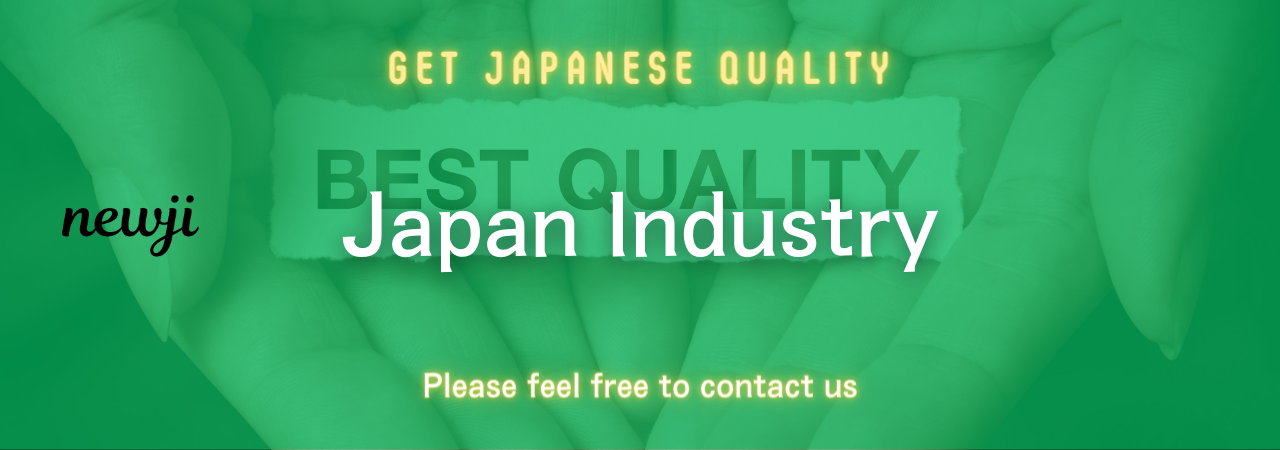
目次
Introduction
When it comes to precision, efficiency, and quality, Japanese manufacturing stands at the pinnacle of global industry standards.
With a legacy rooted in principles like Kaizen (continuous improvement) and a methodical approach to production, Japanese manufacturers have carved a niche that is synonymous with reliability and excellence.
One key aspect that sets Japanese manufacturers apart is their unparalleled adherence to standards and compliance.
In an era where global supply chains are intricately connected, understanding how Japanese manufacturing excels in compliance can provide invaluable insights and a blueprint for global success.
The Foundation: Cultural Values and Philosophies
Kaizen: The Heart of Continuous Improvement
At the core of Japanese manufacturing is the philosophy of Kaizen, which translates to “change for better” or “continuous improvement.”
Kaizen is not just a principle but a culture embedded within Japanese companies.
Every employee, from top management to factory workers, is encouraged to contribute ideas for improvements.
This collective responsibility for quality and efficiency ensures that compliance with standards is a shared goal.
Genchi Genbutsu: The Essence of Hands-on Analysis
Another fundamental Japanese manufacturing philosophy is Genchi Genbutsu, meaning “go and see for yourself.”
This principle emphasizes the importance of firsthand observation and data collection.
Managers and engineers are encouraged to visit the production floor, interact with operators, and observe processes directly.
This hands-on approach ensures that any deviations from standards are identified and corrected promptly.
Quality Control: The Rigorous Adherence to Standards
Statistical Process Control (SPC)
Japanese manufacturers are pioneers in the application of Statistical Process Control.
SPC tools are employed to monitor and control production processes by analyzing data collected in real-time.
By identifying variations and trends, companies can maintain consistent product quality and ensure compliance with stringent standards.
Total Quality Management (TQM)
Total Quality Management is another critical approach that underscores the Japanese commitment to quality and compliance.
TQM is an integrated system focused on continuous quality improvement of products and processes.
Every department and function within the organization collaborates to achieve quality objectives, ensuring that every stage of production adheres to established standards.
Advanced Production Techniques
Lean Manufacturing
Lean Manufacturing, also known as the Toyota Production System (TPS), is a production methodology that emphasizes waste reduction and efficiency.
By focusing on value-adding activities and eliminating waste, Japanese manufacturers can maintain high standards of quality and efficiency.
Techniques such as Just-In-Time (JIT) inventory management and Jidoka (automation with a human touch) play a pivotal role in ensuring that standards are consistently met.
Six Sigma
Six Sigma is a data-driven methodology aimed at eliminating defects and ensuring process excellence.
Japanese companies often integrate Six Sigma with their existing quality control frameworks to achieve near-perfect compliance with standards.
This rigorous approach to problem-solving and process optimization helps in achieving substantial improvements in quality, cost, and delivery.
Supplier Relationships and Procurement Practices
Keiretsu: A Unique Business Network
A notable aspect of Japanese procurement practices is the Keiretsu system, which is a network of long-term, mutually beneficial relationships between manufacturers and suppliers.
This close-knit network fosters a high level of trust and collaboration, ensuring that suppliers are equally committed to maintaining high standards and compliance.
Regular audits, shared technology, and joint development projects are common practices within Keiretsu, contributing to overall quality and compliance.
Supplier Development and Training
Japanese companies place a strong emphasis on supplier development and training.
Suppliers are often treated as extensions of the manufacturing company, and efforts are made to align their processes and standards with the parent company’s requirements.
This may include regular training sessions, workshops, and collaborative improvement initiatives, ensuring that suppliers can meet stringent compliance standards.
Market Conditions and Competitive Advantages
Global Market Position
Japanese manufacturing has a strong global market presence due to its reputation for quality and reliability.
Compliance with international standards such as ISO, JIS (Japanese Industrial Standards), and industry-specific benchmarks allows Japanese manufacturers to compete effectively in global markets.
This commitment to compliance not only enhances their market positioning but also instills confidence in international customers.
Technological Innovation
Innovation is a cornerstone of Japanese manufacturing.
Continuous investment in research and development ensures that Japanese companies remain at the forefront of technological advancements.
Innovative technologies such as AI, IoT, and advanced robotics are increasingly integrated into manufacturing processes, enhancing precision and compliance with standards.
This technological edge provides a significant competitive advantage in global markets.
Challenges and Areas for Improvement
Adapting to Rapid Market Changes
One challenge that Japanese manufacturers face is the ability to adapt quickly to rapid market changes and evolving customer demands.
While their focus on compliance and quality is a strength, it can sometimes result in slower response times to new market trends.
Increasing flexibility and agility in production processes can help Japanese companies better navigate dynamic market conditions.
Global Supply Chain Risks
Global supply chain disruptions, such as those caused by natural disasters or geopolitical tensions, pose significant risks to Japanese manufacturing.
Ensuring compliance across a global supply chain requires robust risk management strategies and contingency planning.
Diversifying suppliers and enhancing supply chain transparency can mitigate these risks and ensure continued adherence to standards.
Best Practices for Global Manufacturers
Embracing a Culture of Continuous Improvement
Global manufacturers can benefit from adopting the Japanese philosophy of continuous improvement.
Encouraging employees at all levels to contribute ideas for process enhancement promotes a culture of quality and compliance.
Implementing Kaizen initiatives can lead to incremental but substantial improvements over time.
Prioritizing Hands-on Management
The principle of Genchi Genbutsu underscores the importance of firsthand observation and management involvement in production processes.
By adopting a hands-on approach, global manufacturers can identify issues early and ensure that standards are met consistently.
Regular management visits to the production floor and direct communication with operators can facilitate this practice.
Leveraging Advanced Quality Control Tools
The use of advanced quality control tools such as SPC and Six Sigma can greatly enhance a company’s ability to comply with standards.
Investing in data-driven methodologies for process monitoring and improvement ensures that deviations are swiftly addressed.
This proactive approach to quality control can help global manufacturers achieve high standards of compliance.
Conclusion
Japanese manufacturing has set a benchmark for excellence in compliance with standards.
Through cultural values such as Kaizen and Genchi Genbutsu, rigorous quality control methodologies, and advanced production techniques, Japanese companies have created a blueprint for global success.
By fostering strong supplier relationships, investing in technological innovation, and continuously striving for improvement, Japanese manufacturers maintain their position as global leaders in quality and reliability.
Global manufacturers can learn much from the Japanese approach, adopting best practices that emphasize continuous improvement, hands-on management, and advanced quality control.
By doing so, they can enhance their own compliance with standards, achieve higher levels of efficiency, and succeed in the competitive landscape of global manufacturing.
資料ダウンロード
QCD調達購買管理クラウド「newji」は、調達購買部門で必要なQCD管理全てを備えた、現場特化型兼クラウド型の今世紀最高の購買管理システムとなります。
ユーザー登録
調達購買業務の効率化だけでなく、システムを導入することで、コスト削減や製品・資材のステータス可視化のほか、属人化していた購買情報の共有化による内部不正防止や統制にも役立ちます。
NEWJI DX
製造業に特化したデジタルトランスフォーメーション(DX)の実現を目指す請負開発型のコンサルティングサービスです。AI、iPaaS、および先端の技術を駆使して、製造プロセスの効率化、業務効率化、チームワーク強化、コスト削減、品質向上を実現します。このサービスは、製造業の課題を深く理解し、それに対する最適なデジタルソリューションを提供することで、企業が持続的な成長とイノベーションを達成できるようサポートします。
オンライン講座
製造業、主に購買・調達部門にお勤めの方々に向けた情報を配信しております。
新任の方やベテランの方、管理職を対象とした幅広いコンテンツをご用意しております。
お問い合わせ
コストダウンが利益に直結する術だと理解していても、なかなか前に進めることができない状況。そんな時は、newjiのコストダウン自動化機能で大きく利益貢献しよう!
(Β版非公開)