- お役立ち記事
- “How Japanese Manufacturing is Revolutionizing the Fight Against Volatile Organic Compounds”
“How Japanese Manufacturing is Revolutionizing the Fight Against Volatile Organic Compounds”
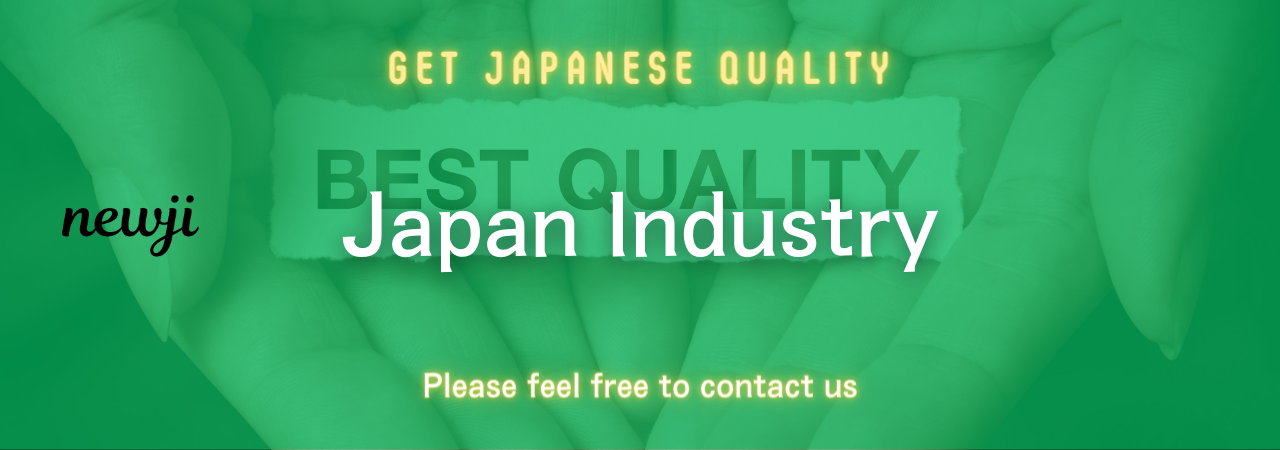
目次
Introduction
Volatile Organic Compounds (VOCs) have long been a pressing issue in manufacturing industries worldwide.
These organic chemicals, which easily vaporize at room temperature, are known for their adverse environmental and health impacts.
Exposure to VOCs can lead to serious health issues such as respiratory problems, headaches, and even long-term organ damage.
Environmentally, VOCs are key contributors to air pollution and the formation of ground-level ozone.
Japanese manufacturing companies are known for their rigorous quality control and innovative approaches.
With the ever-increasing global focus on sustainability and the stringent environmental regulations at home, Japan has been spearheading efforts to combat VOC emissions.
In this article, we will delve into how Japanese manufacturing is revolutionizing the fight against VOCs by examining practical strategies, advantages and disadvantages, supplier negotiation techniques, market conditions, and best practices.
Understanding VOCs and Their Impact
What Are VOCs?
Volatile Organic Compounds (VOCs) are a group of organic chemicals that have high vapor pressures, causing them to evaporate easily into the atmosphere.
Common sources of VOCs in manufacturing include solvents, paints, adhesives, and various chemical production processes.
Health and Environmental Impact
VOCs pose significant health risks, including eye, nose, and throat irritation, headaches, loss of coordination, and damage to the liver, kidney, and central nervous system.
Some VOCs are even suspected or known to cause cancer in humans.
Environmentally, VOCs contribute to the formation of ground-level ozone and smog, exacerbating air pollution and having detrimental effects on ecosystems.
Japan’s Approach to Tackling VOCs
Regulatory Framework
Japan has implemented stringent regulations to control VOC emissions.
The Air Pollution Control Law mandates VOC emission reductions from industrial sources.
Companies are required to monitor their VOC emissions and adopt best available technologies to minimize environmental impact.
Innovative Technologies
Japanese manufacturers are known for their innovation.
Many companies have adopted advanced technologies such as solvent recycling systems, low-VOC or VOC-free materials, and state-of-the-art filtration systems.
These technologies not only reduce VOC emissions but also enhance production efficiency.
Process Optimization
Japanese factories are highly efficient, thanks in part to methodologies such as Lean Manufacturing and Six Sigma.
These practices help in identifying and eliminating waste, including VOC emissions.
Process optimization techniques like these are essential in reducing volatile organic compounds.
Practical Strategies for Reducing VOCs
Material Substitution
One effective strategy to combat VOC emissions is substituting high-VOC materials with low-VOC or VOC-free alternatives.
For instance, water-based paints and adhesives are much less harmful compared to their solvent-based counterparts.
Japanese manufacturers have been at the forefront of developing and utilizing these safer alternatives.
Closed-loop Systems
Closed-loop systems that capture and recycle solvents and other VOC materials are another practical approach.
These systems reduce the amount of VOCs released into the atmosphere and lower the cost of raw materials by recycling waste.
Advanced Filtration and Ventilation
High-efficiency particulate air (HEPA) filters and activated carbon filters are commonly used in Japanese manufacturing facilities.
These advanced filtration systems are capable of capturing even the smallest particles and VOC vapors, significantly reducing emissions.
Advantages and Disadvantages
Advantages
1. **Regulatory Compliance**: Adhering to VOC regulations ensures that companies avoid hefty fines and sanctions.
2. **Health and Safety**: Reducing VOC emissions leads to a healthier work environment, which can result in increased employee productivity and reduced sick leave.
3. **Environmental Impact**: Lowering VOC emissions contributes to cleaner air and a healthier planet, enhancing corporate social responsibility credentials.
Disadvantages
1. **Cost**: Implementing low-VOC technologies and materials can be expensive initially.
2. **Technical Challenges**: Adopting new technologies often requires retraining personnel and may face technical hitches.
3. **Supply Chain Adjustments**: Shifting to low-VOC materials may necessitate renegotiation with suppliers and potential disruptions in the supply chain.
Supplier Negotiation Techniques
Building Long-term Relationships
When negotiating with suppliers, building long-term relationships can provide significant leverage.
Suppliers are more likely to make concessions such as price reductions or priority deliveries to maintain a valuable partnership.
Quality over Price
While cost is an important factor, prioritizing quality can lead to better long-term outcomes.
High-quality, low-VOC materials may cost more upfront but can result in greater efficiency and less waste, ultimately saving money.
Transparent Communication
Clear and transparent communication about your company’s VOC reduction goals can help suppliers understand your needs better.
This transparency can facilitate the identification of mutual benefits and lead to more productive negotiations.
Understanding Market Conditions
Global Demand for Sustainable Products
There is a growing global demand for sustainable and environmentally-friendly products.
Companies that adopt low-VOC strategies are better positioned to meet this demand and can often charge a premium for their products.
Technological Advancements
Rapid technological advancements are making it easier and more cost-effective to reduce VOC emissions.
Staying abreast of these developments can help companies remain competitive.
Regulatory Trends
With increasingly stringent environmental regulations worldwide, companies that proactively reduce VOC emissions will find it easier to comply with future regulations, giving them a competitive advantage.
Best Practices
Regular Training and Education
Continuous training and education programs for employees on the importance of reducing VOC emissions and the correct usage of new technologies are vital.
Japanese companies often invest in regular training programs to ensure that all staff members are well-versed in best practices.
Continuous Improvement
Japanese manufacturing philosophies such as Kaizen (continuous improvement) encourage always striving for better and more efficient ways to reduce VOC emissions.
Regular reviews and audits help identify areas for improvement.
Collaborative Efforts
Collaborating with suppliers, customers, and even competitors can lead to shared solutions that benefit all parties.
Joint research and development projects can result in innovative low-VOC technologies and materials.
Conclusion
The fight against VOC emissions is crucial for the health of both people and the planet.
Japanese manufacturing companies have been leading the way through innovative technologies, stringent regulations, and best practices.
By adopting strategies such as material substitution, closed-loop systems, and advanced filtration, and by focusing on continuous improvement and collaboration, manufacturers can significantly reduce their VOC emissions.
While there are challenges associated with cost and technical adjustments, the long-term benefits of regulatory compliance, a healthier work environment, and a better standing in the market far outweigh these drawbacks.
As the global demand for sustainable products grows, companies that embrace these practices will be better prepared to thrive in an increasingly eco-conscious market.
In essence, the lessons from Japanese manufacturers are not just applicable domestically but offer valuable insights for companies worldwide.
By learning from their approach to combating VOC emissions, businesses can contribute to a more sustainable future while achieving operational excellence.
資料ダウンロード
QCD調達購買管理クラウド「newji」は、調達購買部門で必要なQCD管理全てを備えた、現場特化型兼クラウド型の今世紀最高の購買管理システムとなります。
ユーザー登録
調達購買業務の効率化だけでなく、システムを導入することで、コスト削減や製品・資材のステータス可視化のほか、属人化していた購買情報の共有化による内部不正防止や統制にも役立ちます。
NEWJI DX
製造業に特化したデジタルトランスフォーメーション(DX)の実現を目指す請負開発型のコンサルティングサービスです。AI、iPaaS、および先端の技術を駆使して、製造プロセスの効率化、業務効率化、チームワーク強化、コスト削減、品質向上を実現します。このサービスは、製造業の課題を深く理解し、それに対する最適なデジタルソリューションを提供することで、企業が持続的な成長とイノベーションを達成できるようサポートします。
オンライン講座
製造業、主に購買・調達部門にお勤めの方々に向けた情報を配信しております。
新任の方やベテランの方、管理職を対象とした幅広いコンテンツをご用意しております。
お問い合わせ
コストダウンが利益に直結する術だと理解していても、なかなか前に進めることができない状況。そんな時は、newjiのコストダウン自動化機能で大きく利益貢献しよう!
(Β版非公開)