- お役立ち記事
- How plastics are synthesized and how their molecular structure affects products
月間77,185名の
製造業ご担当者様が閲覧しています*
*2025年2月28日現在のGoogle Analyticsのデータより
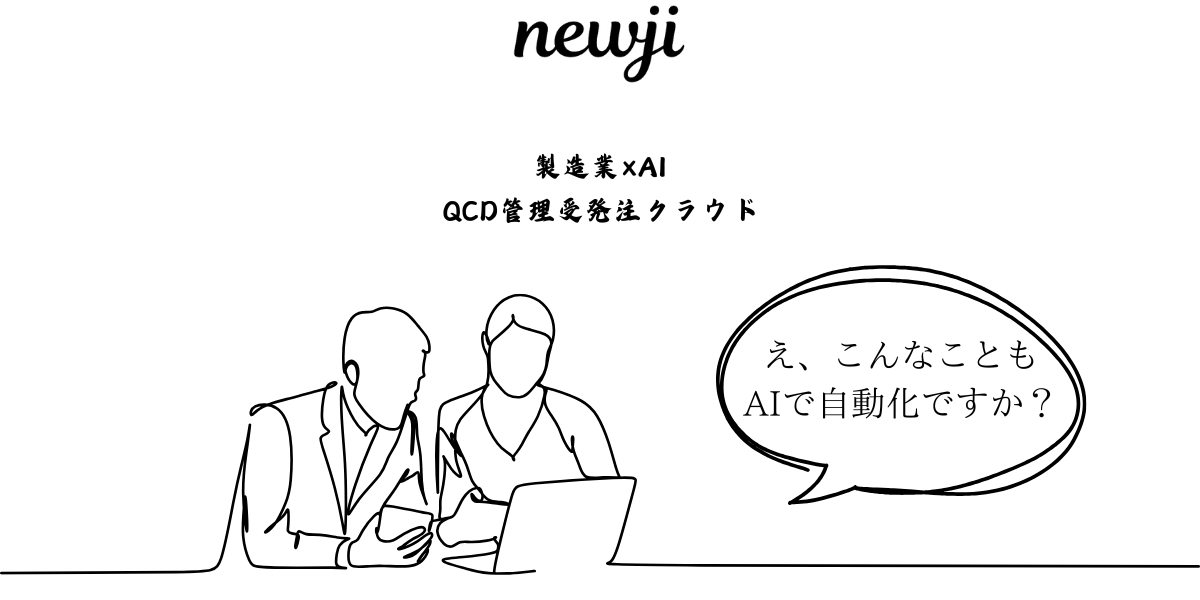
How plastics are synthesized and how their molecular structure affects products
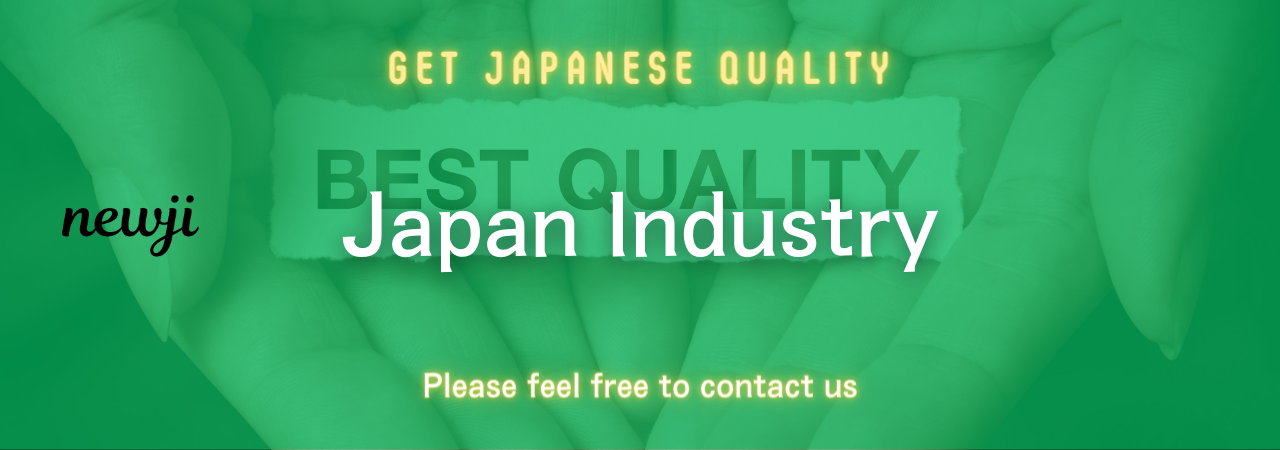
目次
Understanding Plastics: The Basics
Plastics have become a crucial part of modern life, featuring in everything from packaging to automotive parts.
At the core of their versatility and widespread use are their molecular structure and the process of synthesis which transforms raw materials into useful products.
Understanding how plastics are synthesized and how their molecular structure influences their characteristics can help us better appreciate their role in various industries.
The Synthesis of Plastics
Plastics are primarily synthesized through polymerization, a chemical reaction where small molecules known as monomers link together to form long chains called polymers.
These polymers are the building blocks of plastics, and their structure significantly influences the physical properties of the final product.
There are two main types of polymerization: addition polymerization and condensation polymerization.
In addition polymerization, monomers add to one another without the loss of any small molecules, creating a continuous polymer chain.
A common example of a plastic made via this method is polyethylene, widely used in packaging.
Condensation polymerization, on the other hand, involves the reaction of monomers with the elimination of small molecules such as water.
An example of this is nylon, used in textiles and engineering plastics.
Both processes allow for the tailoring of materials to have specific properties, which is critical in manufacturing products that meet precise performance criteria.
Raw Materials and Polymerization Catalysts
The synthesis of plastics begins with raw materials like crude oil, natural gas, or plant materials that are refined into monomers.
Once these monomers are obtained, they undergo polymerization.
The process often employs catalysts to speed up the generation of polymers without becoming chemically altered themselves.
Catalysts play a vital role in determining the efficiency and outcome of polymerization.
They can influence the molecular weight of the polymers, their distribution, and ultimately, the properties of the final plastic product.
For example, the presence of a Ziegler-Natta catalyst can create polymers with high tensile strength and elasticity, useful in making heavy-duty industrial products.
The Molecular Structure of Plastics
The molecular structure of plastics is crucial in defining their physical characteristics.
This structure refers to the arrangement of atoms and the degree of polymerization—how many monomers are in a single chain.
Linear, Branched, and Cross-Linked Polymers
Polymers can have several structural configurations: linear, branched, or cross-linked.
Linear polymers consist of long, repeating monomer units in a straight chain.
They tend to be more flexible and easier to process.
Polyethylene is a prime example, often used for its toughness and pliability.
Branched polymers possess side chains off the main chain, leading to different melting and flow properties.
A higher degree of branching can make a plastic less dense and increase its transparency, attributes desired in packaging materials like plastic wraps.
Cross-linked polymers have chains that are interconnected, resulting in a three-dimensional network.
This structure is responsible for the rigidity and resistance to melting of plastics like vulcanized rubber or certain epoxies, often used in tires and adhesives.
The Impact of Molecular Weight
The molecular weight of a polymer affects its strength, toughness, and durability.
A higher molecular weight usually results in stronger and more impact-resistant plastics.
For instance, high molecular weight polyethylene is used in products that require durability, such as bulletproof vests and strong chemical-resistant containers.
However, high molecular weight can also make a polymer more difficult to process and shape, requiring advanced techniques and tools to mold it effectively.
Balancing these properties is critical in manufacturing to ensure the plastic meets specific application requirements.
How Molecular Structure Affects Plastic Products
The unique arrangement of a polymer’s molecules directly impacts how the plastic performs in real-world applications.
From flexibility and resistance to heat and chemical exposure to clarity and color, every aspect is tied to the molecular structure of the plastic.
Thermoplastics vs. Thermosets
Plastics can broadly be categorized into two types based on their response to heat: thermoplastics and thermosets.
Thermoplastics, such as polycarbonate and acrylic, can be melted and reformed multiple times.
Their molecular structure features linear or slightly branched chains that allow them to be reshaped when heat is applied.
This property makes them ideal for recycling and repeated use.
Thermosets, like Bakelite or phenolic resins, undergo a curing process that forms permanent cross-links.
Once set, they cannot be remelted or reshaped without degrading the material.
Their durability and resistance to heat and chemicals make them suitable for electrical insulation and high-strength composites.
Conclusion: The Significance of Plastic Synthesis and Structure
The synthesis and molecular structure of plastics are fundamental in defining their characteristics and determining their suitability for different uses.
Understanding these aspects allows manufacturers to tailor plastics for specific applications, whether they need flexibility, strength, transparency, or resistance to extreme conditions.
As technology advances, the processes of plastic synthesis and manipulation of their molecular structures continue to evolve, opening new possibilities for more sustainable and efficient materials.
While the environmental impact of plastics remains a concern, ongoing research into biodegradable and recyclable plastics is striving to create solutions with less environmental footprint, ensuring that this versatile material can adapt to future needs.
資料ダウンロード
QCD管理受発注クラウド「newji」は、受発注部門で必要なQCD管理全てを備えた、現場特化型兼クラウド型の今世紀最高の受発注管理システムとなります。
ユーザー登録
受発注業務の効率化だけでなく、システムを導入することで、コスト削減や製品・資材のステータス可視化のほか、属人化していた受発注情報の共有化による内部不正防止や統制にも役立ちます。
NEWJI DX
製造業に特化したデジタルトランスフォーメーション(DX)の実現を目指す請負開発型のコンサルティングサービスです。AI、iPaaS、および先端の技術を駆使して、製造プロセスの効率化、業務効率化、チームワーク強化、コスト削減、品質向上を実現します。このサービスは、製造業の課題を深く理解し、それに対する最適なデジタルソリューションを提供することで、企業が持続的な成長とイノベーションを達成できるようサポートします。
製造業ニュース解説
製造業、主に購買・調達部門にお勤めの方々に向けた情報を配信しております。
新任の方やベテランの方、管理職を対象とした幅広いコンテンツをご用意しております。
お問い合わせ
コストダウンが利益に直結する術だと理解していても、なかなか前に進めることができない状況。そんな時は、newjiのコストダウン自動化機能で大きく利益貢献しよう!
(β版非公開)