- お役立ち記事
- How purchasing departments aim to improve on-time delivery rates in the manufacturing industry
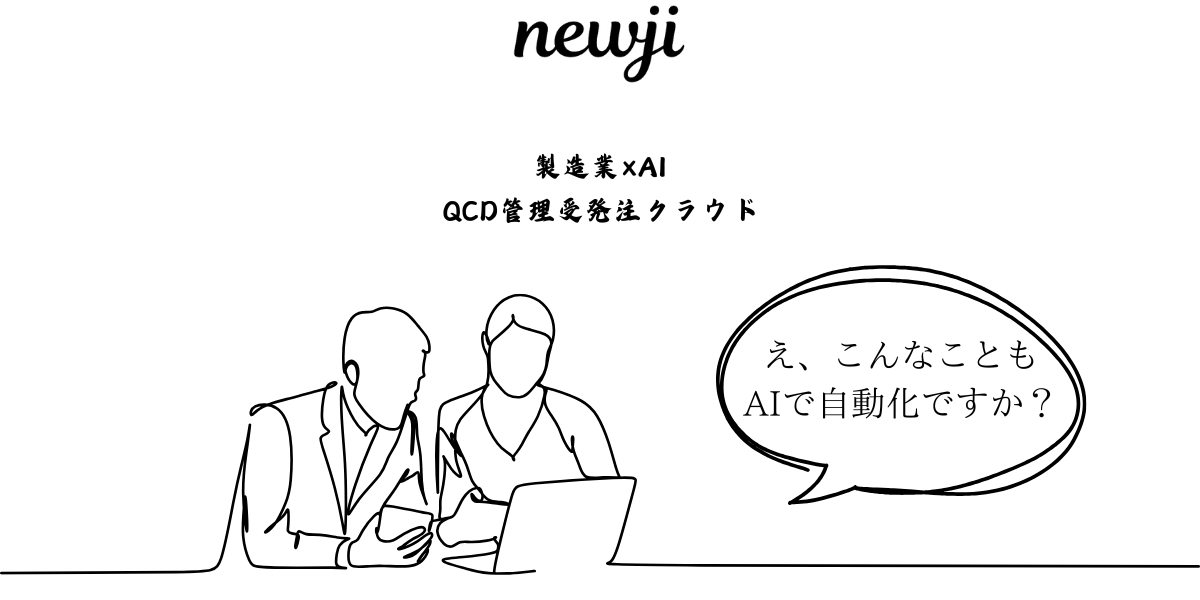
How purchasing departments aim to improve on-time delivery rates in the manufacturing industry
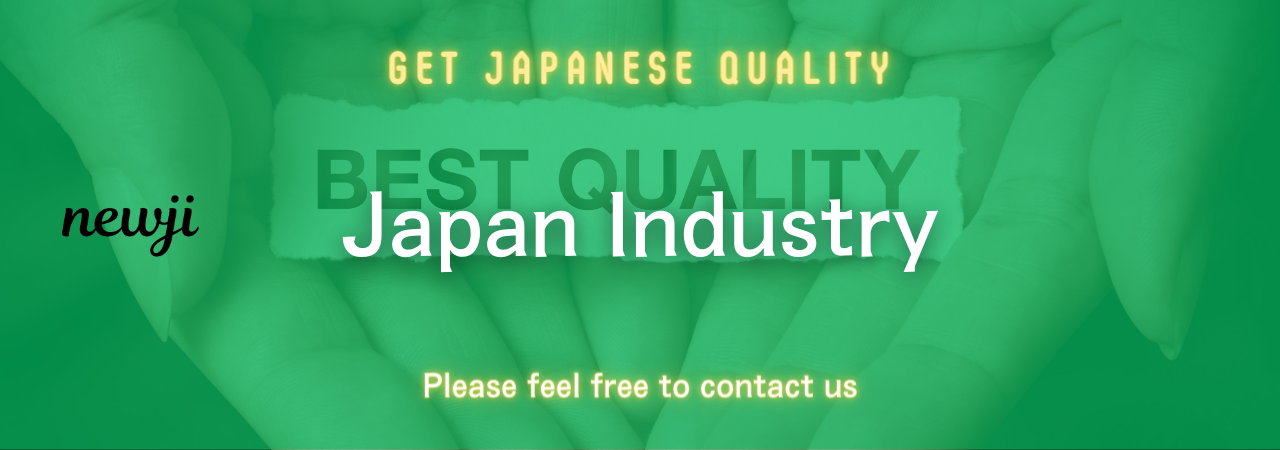
目次
Understanding On-Time Delivery in Manufacturing
On-time delivery is a critical aspect of the manufacturing industry, significantly impacting customer satisfaction and the overall efficiency of operations.
When products are delivered on schedule, it strengthens the relationship between manufacturers and their clients, fostering trust and reliability.
However, achieving high on-time delivery rates can be challenging due to various factors such as supply chain disruptions, production delays, and logistics issues.
In manufacturing, purchasing departments play a pivotal role in ensuring that on-time delivery rates are maintained or improved.
By collaborating closely with suppliers and maintaining effective internal processes, purchasing departments can contribute to a smoother workflow and timely delivery of products.
The Role of Purchasing Departments
Purchasing departments are responsible for acquiring the raw materials, components, and services necessary for production.
Their role is not just about negotiating prices, but also ensuring that materials are of high quality and delivered on time.
To improve on-time delivery rates, purchasing departments focus on several key areas:
Supplier Relationship Management
Building and maintaining strong relationships with suppliers is essential for purchasing departments.
Working closely with suppliers ensures that they understand the company’s needs and can deliver materials timely and reliably.
Frequent communication and collaboration can help identify potential issues before they affect delivery schedules.
By cultivating strong partnerships, purchasing departments can often negotiate better terms and more reliable delivery schedules.
Accurate Demand Forecasting
One of the challenges in maintaining on-time delivery is accurately forecasting demand.
Purchasing departments need to collaborate with other departments, such as sales and production, to gather data and predict future material needs.
Improved forecasting allows purchasing departments to order materials in appropriate quantities at the right times, reducing the risk of shortages or overstock situations.
Flexible and Diversified Supply Chains
A flexible supply chain is better equipped to handle unexpected disruptions.
Purchasing departments can work towards diversifying their supplier base to reduce the dependency on a single source.
This approach provides more options and reduces the risk of delays if one supplier faces issues.
It also allows for better negotiation power and cost management.
Improving Internal Processes
To achieve better on-time delivery rates, purchasing departments should also focus on optimizing internal processes.
Streamlining Procurement Procedures
Efficient procurement procedures reduce the lead time between ordering materials and receiving them.
Purchasing departments can leverage technology and automation to streamline their procurement processes.
Software solutions can automate purchase orders, track inventory levels in real-time, and provide valuable data insights to aid decision-making.
Collaborative Planning and Scheduling
Effective planning and scheduling are vital to coordinating the delivery of raw materials with production schedules.
Purchasing departments should work closely with production teams to ensure materials are available when needed without causing delays in manufacturing.
This collaboration can help alleviate bottlenecks and optimize resource utilization.
Performance Metrics and Continuous Improvement
Measuring performance using specific metrics is crucial for identifying areas of improvement.
Purchasing departments can track key performance indicators (KPIs) such as supplier lead times, procurement cycle time, and fulfillment rates.
Regularly reviewing these metrics allows departments to identify patterns or recurring issues and implement strategies for continuous improvement.
Leveraging Technology for On-Time Delivery
Technology plays a significant role in enhancing on-time delivery rates in manufacturing.
Advanced Analytics and Data Management
Advanced analytics tools can provide purchasing departments with insights into supplier performance, demand trends, and risk factors.
By analyzing data, departments can make informed decisions and predict potential disruptions that could threaten on-time delivery.
Supply Chain Management Software
Implementing supply chain management software can improve visibility and coordination across the entire supply chain.
These systems help integrate multiple processes, facilitating better communication among suppliers, purchasing departments, and production teams.
Real-time data from these systems can assist in making quick adjustments if there are changes in demand or supply conditions.
Automated Inventory Management
Automated inventory management systems help keep track of stock levels and automatically reorder materials when necessary.
This reduces the likelihood of stockouts and overstock situations, both of which can affect delivery schedules.
By ensuring that materials are available just in time, purchasing departments can better align supply with production demands.
Conclusion
Improving on-time delivery rates in the manufacturing industry is a complex challenge that requires purchasing departments to adopt a multi-faceted approach.
By focusing on building strong supplier relationships, optimizing internal processes, and leveraging technology, purchasing departments can contribute significantly to achieving high delivery performance.
Efficiency in procurement and a proactive stance towards potential issues empower these departments to ensure that manufacturers meet or exceed customer expectations.
As the industry evolves, continuing to adapt and improve strategies will be essential for sustaining and increasing on-time delivery rates.
資料ダウンロード
QCD調達購買管理クラウド「newji」は、調達購買部門で必要なQCD管理全てを備えた、現場特化型兼クラウド型の今世紀最高の購買管理システムとなります。
ユーザー登録
調達購買業務の効率化だけでなく、システムを導入することで、コスト削減や製品・資材のステータス可視化のほか、属人化していた購買情報の共有化による内部不正防止や統制にも役立ちます。
NEWJI DX
製造業に特化したデジタルトランスフォーメーション(DX)の実現を目指す請負開発型のコンサルティングサービスです。AI、iPaaS、および先端の技術を駆使して、製造プロセスの効率化、業務効率化、チームワーク強化、コスト削減、品質向上を実現します。このサービスは、製造業の課題を深く理解し、それに対する最適なデジタルソリューションを提供することで、企業が持続的な成長とイノベーションを達成できるようサポートします。
オンライン講座
製造業、主に購買・調達部門にお勤めの方々に向けた情報を配信しております。
新任の方やベテランの方、管理職を対象とした幅広いコンテンツをご用意しております。
お問い合わせ
コストダウンが利益に直結する術だと理解していても、なかなか前に進めることができない状況。そんな時は、newjiのコストダウン自動化機能で大きく利益貢献しよう!
(Β版非公開)