- お役立ち記事
- How purchasing departments can help improve supplier quality
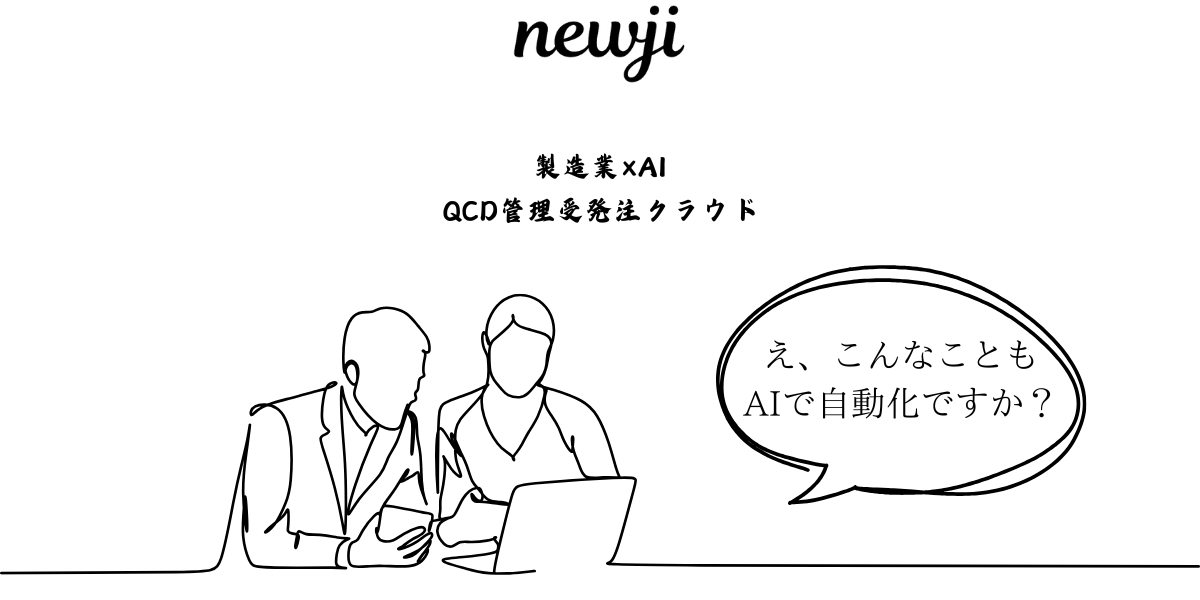
How purchasing departments can help improve supplier quality
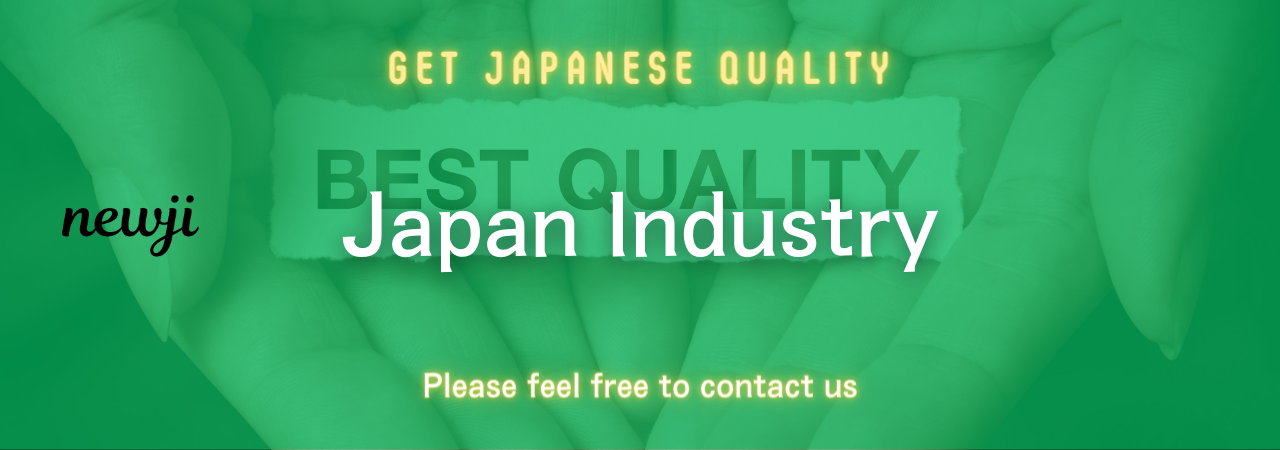
目次
Understanding the Role of Purchasing Departments
Purchasing departments play a crucial role in any organization.
They are responsible for acquiring goods and services needed for the company’s operations.
Beyond simply buying items, purchasing departments must ensure that these goods meet certain quality standards.
This responsibility doesn’t just impact their own department but has far-reaching effects on the overall success of the company.
Quality issues in the supply chain can lead to delayed production schedules, dissatisfied customers, and increased operational costs.
Thus, a proactive approach by purchasing teams can significantly improve supplier quality.
The Connection Between Supplier Quality and Business Success
Supplier quality directly affects a company’s product quality, reputation, and customer satisfaction.
When a supplier provides low-quality materials, it can lead to defects in the final product.
These defects can result in returns, repairs, or recalls, all of which harm a company’s reputation and bottom line.
On the other hand, working with suppliers who guarantee high-quality materials enhances product reliability and customer trust.
This positive image can lead to increased sales and a loyal customer base.
Therefore, purchasing departments must develop strategies to enhance supplier quality, which in turn drives business success.
Steps to Improve Supplier Quality
1. Establish Clear Quality Criteria
To improve supplier quality, purchasing departments need to establish clear, measurable quality criteria for suppliers.
This involves defining what constitutes good quality in context, considering industry standards and the company’s objectives.
Once these criteria are set, they should be communicated to all potential and existing suppliers.
Having clear expectations helps suppliers to understand what is required of them and strive to meet these standards.
2. Conduct Thorough Supplier Evaluations
Before engaging with a supplier, it is important to conduct a thorough evaluation.
This involves assessing their ability to meet your company’s quality requirements.
Evaluations should include reviewing the supplier’s past performance, capacity, technical capabilities, and financial stability.
Site visits can also provide insight into their operations and capabilities.
A rigorous evaluation process helps in selecting the right suppliers who can consistently provide high-quality materials.
3. Build Strong Supplier Relationships
Building strong, collaborative relationships with suppliers fosters a partnership mindset instead of a transactional one.
This can be achieved by communicating openly and regularly, understanding each other’s expectations, and addressing issues promptly.
Strong relationships encourage suppliers to be more committed to meeting quality standards and even suggest improvements.
Purchasing departments that focus on collaboration rather than just negotiation can achieve greater supplier quality improvements.
4. Implement Supplier Development Programs
Sometimes, suppliers may have the potential to provide high-quality products but lack certain resources or skills.
Implementing supplier development programs can help improve their capabilities.
These programs may include training sessions, technical assistance, or co-investing in new technologies or processes.
By investing in supplier development, purchasing departments can ensure that suppliers are well-equipped to meet quality standards consistently.
5. Monitor Supplier Performance Regularly
Once a contract is in place, it is crucial to continuously monitor supplier performance to ensure quality standards are being met.
Regular audits and performance reviews can identify areas needing improvement before they become significant issues.
Key performance indicators (KPIs) related to quality should be established and reviewed regularly.
Consistent monitoring and feedback can help maintain high supplier quality standards.
Leveraging Technology to Enhance Supplier Quality
Utilizing technology can greatly assist purchasing departments in tracking and improving supplier quality.
Software solutions that offer supplier management modules allow for efficient tracking of supplier performance data.
These tools can automate quality assessments and provide real-time analytics.
By leveraging technology, purchasing departments can decrease the likelihood of human error and make well-informed decisions quickly.
Embracing Predictive Analytics
Predictive analytics can be used to forecast potential supplier quality issues before they arise.
By analyzing historical data, companies can anticipate challenges and address them proactively.
This approach not only helps maintain supplier quality but also minimizes disruptions in production schedules.
The Role of Feedback in Quality Improvement
Providing suppliers with constructive feedback is essential in the quality improvement process.
Feedback should be specific, actionable, and focused on processes rather than people.
It is a good practice to recognize and reward suppliers who consistently meet or exceed quality expectations.
Positive reinforcement can motivate suppliers to maintain or even improve their quality standards.
Conclusion
The purchasing department’s role is not limited to just acquiring goods and services—it also encompasses ensuring the quality of those goods.
By implementing clear criteria, conducting rigorous evaluations, building strong relationships, and using technology strategically, purchasing departments can significantly improve supplier quality.
This not only enhances a company’s product offerings but also strengthens its market position, ultimately contributing to long-term business success.
資料ダウンロード
QCD調達購買管理クラウド「newji」は、調達購買部門で必要なQCD管理全てを備えた、現場特化型兼クラウド型の今世紀最高の購買管理システムとなります。
ユーザー登録
調達購買業務の効率化だけでなく、システムを導入することで、コスト削減や製品・資材のステータス可視化のほか、属人化していた購買情報の共有化による内部不正防止や統制にも役立ちます。
NEWJI DX
製造業に特化したデジタルトランスフォーメーション(DX)の実現を目指す請負開発型のコンサルティングサービスです。AI、iPaaS、および先端の技術を駆使して、製造プロセスの効率化、業務効率化、チームワーク強化、コスト削減、品質向上を実現します。このサービスは、製造業の課題を深く理解し、それに対する最適なデジタルソリューションを提供することで、企業が持続的な成長とイノベーションを達成できるようサポートします。
オンライン講座
製造業、主に購買・調達部門にお勤めの方々に向けた情報を配信しております。
新任の方やベテランの方、管理職を対象とした幅広いコンテンツをご用意しております。
お問い合わせ
コストダウンが利益に直結する術だと理解していても、なかなか前に進めることができない状況。そんな時は、newjiのコストダウン自動化機能で大きく利益貢献しよう!
(Β版非公開)