- お役立ち記事
- How Purchasing Management Optimization Impacts the SME Supply Chain
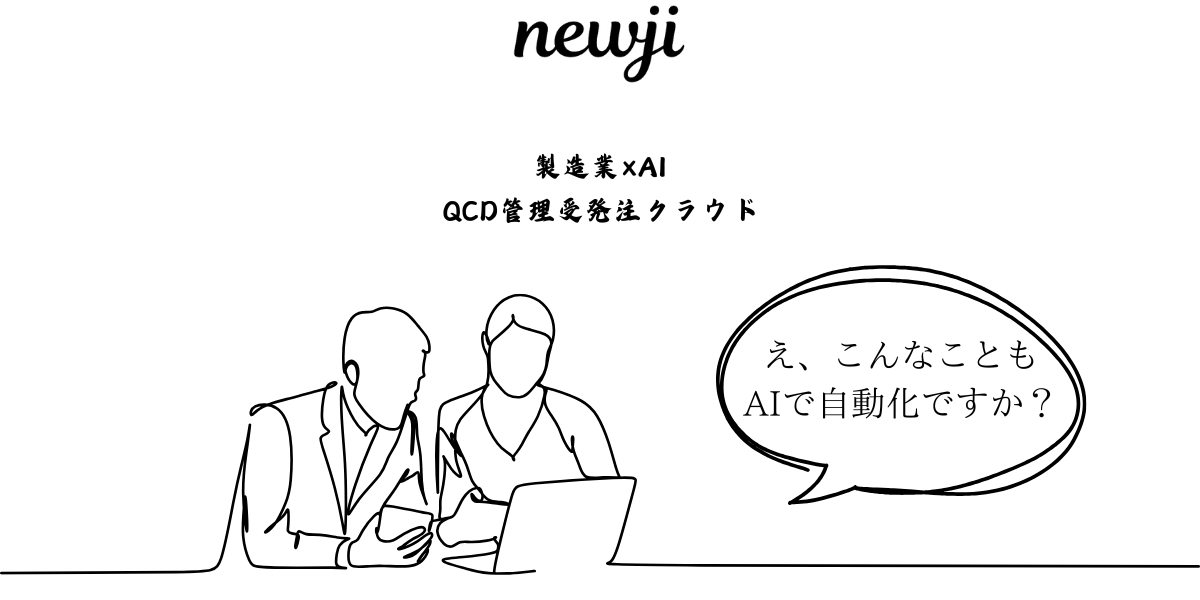
How Purchasing Management Optimization Impacts the SME Supply Chain
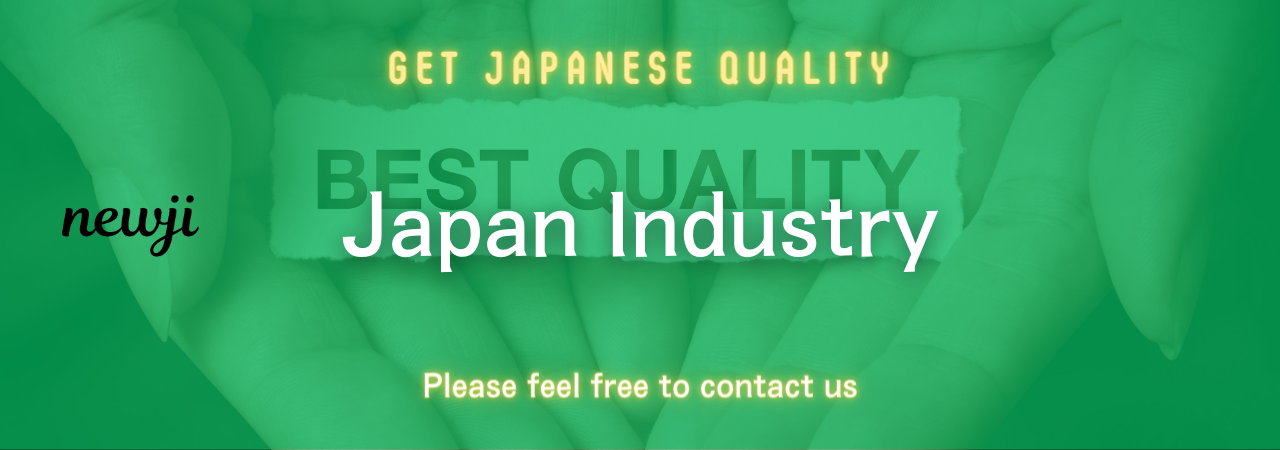
目次
Introduction to Purchasing Management Optimization
Purchasing management is an essential aspect of any business, particularly for small and medium-sized enterprises (SMEs).
Optimizing purchasing management can greatly impact the efficiency and effectiveness of the supply chain.
From reducing costs to ensuring the availability of products, optimizing purchasing is crucial.
What is Purchasing Management?
Purchasing management refers to the process of acquiring goods and services that a company needs to function.
This involves not just buying items but also negotiating with suppliers, managing contracts, and ensuring the timely delivery of goods and services.
For SMEs, managing these aspects efficiently can make a significant difference in profitability.
Why SMEs Need to Focus on Optimization
SMEs often operate with limited resources.
Therefore, every decision related to purchasing must be well-thought-out to avoid wastage and inefficiency.
Optimization helps in making these decisions more effective.
It leads to better cost control, improved supplier relationships, and supports business growth.
Cost Control
Cost control is one of the main reasons SMEs should focus on purchasing management optimization.
By negotiating better terms with suppliers and minimizing waste, businesses can save money.
Lower costs mean higher profit margins, which is crucial for sustaining business operations.
Improved Supplier Relationships
Another significant benefit is the improvement in supplier relationships.
Optimization involves better communication and contracts, which can lead to more reliable deliveries and potentially even more favorable terms.
Supporting Business Growth
When the purchasing process is optimized, other areas of the business can operate more smoothly.
This efficiency supports overall business growth, allowing SMEs to scale and compete more effectively in the market.
Steps to Optimize Purchasing Management
Analyze Current Processes
The first step in optimizing purchasing management is to analyze the current processes.
Understand where inefficiencies and bottlenecks are occurring.
This can involve reviewing purchase orders, delivery timelines, and supplier performance.
Leverage Technology
Technology can be a game-changer.
Various tools and software solutions can help streamline purchasing processes.
Automation of repetitive tasks, real-time inventory tracking, and advanced data analytics are just a few examples.
Negotiate with Suppliers
Effective negotiation can have a significant impact.
Businesses should build strong relationships with suppliers and negotiate terms that are favorable for both parties.
This can include better payment terms, discounts for bulk orders, or more flexible delivery schedules.
Implement a Vendor Management System
A vendor management system (VMS) can greatly assist in tracking supplier performance and managing contracts.
Such a system can send alerts when contracts are up for renewal or when a supplier’s performance drops below the required standard.
The Impact on Supply Chain Efficiency
Optimizing purchasing management directly impacts supply chain efficiency.
A well-optimized purchasing process ensures that the right products are available at the right time.
This minimizes delays and avoids situations where production may halt due to the unavailability of materials.
Reduction in Lead Times
Effective purchasing management helps in reducing lead times.
With better planning and supplier relationships, businesses can ensure quicker delivery of goods.
This leads to faster production cycles and quicker time-to-market for products.
Inventory Management
Proper purchasing optimization also streamlines inventory management.
By having a clear view of what is in stock and what needs to be ordered, businesses can avoid both overstocking and stockouts.
This balance is crucial for maintaining smooth operations and controlling costs.
Quality Control
Working closely with suppliers and having detailed contracts can also lead to improved quality control.
Quality products mean fewer returns and customer complaints, which can considerably enhance business reputation.
Common Challenges in Purchasing Management
Supplier Reliability
One of the challenges that SMEs face is ensuring supplier reliability.
It is essential to have backup plans and multiple suppliers to ensure that the business can continue to function smoothly.
Cost Fluctuations
Prices for raw materials and products can fluctuate.
Effective purchasing management requires staying updated with market trends and being ready to negotiate new terms as required.
Regulatory Compliance
Businesses must ensure that their purchasing practices comply with all relevant laws and regulations.
Failing to do so can result in legal troubles and fines.
Conclusion
Optimizing purchasing management is crucial for the success of SMEs.
It impacts all aspects of the supply chain, from cost control to inventory management and vendor relations.
By focusing on effective purchasing strategies, small and medium-sized businesses can enhance their efficiency, reduce costs, and support overall business growth.
Leveraging technology and improving supplier relationships are key steps in achieving optimization.
Despite the challenges, the benefits make the effort worthwhile, leading to a more resilient and competitive business.
資料ダウンロード
QCD調達購買管理クラウド「newji」は、調達購買部門で必要なQCD管理全てを備えた、現場特化型兼クラウド型の今世紀最高の購買管理システムとなります。
ユーザー登録
調達購買業務の効率化だけでなく、システムを導入することで、コスト削減や製品・資材のステータス可視化のほか、属人化していた購買情報の共有化による内部不正防止や統制にも役立ちます。
NEWJI DX
製造業に特化したデジタルトランスフォーメーション(DX)の実現を目指す請負開発型のコンサルティングサービスです。AI、iPaaS、および先端の技術を駆使して、製造プロセスの効率化、業務効率化、チームワーク強化、コスト削減、品質向上を実現します。このサービスは、製造業の課題を深く理解し、それに対する最適なデジタルソリューションを提供することで、企業が持続的な成長とイノベーションを達成できるようサポートします。
オンライン講座
製造業、主に購買・調達部門にお勤めの方々に向けた情報を配信しております。
新任の方やベテランの方、管理職を対象とした幅広いコンテンツをご用意しております。
お問い合わせ
コストダウンが利益に直結する術だと理解していても、なかなか前に進めることができない状況。そんな時は、newjiのコストダウン自動化機能で大きく利益貢献しよう!
(Β版非公開)