- お役立ち記事
- How QFD can help manufacturers reduce costs and improve quality
How QFD can help manufacturers reduce costs and improve quality
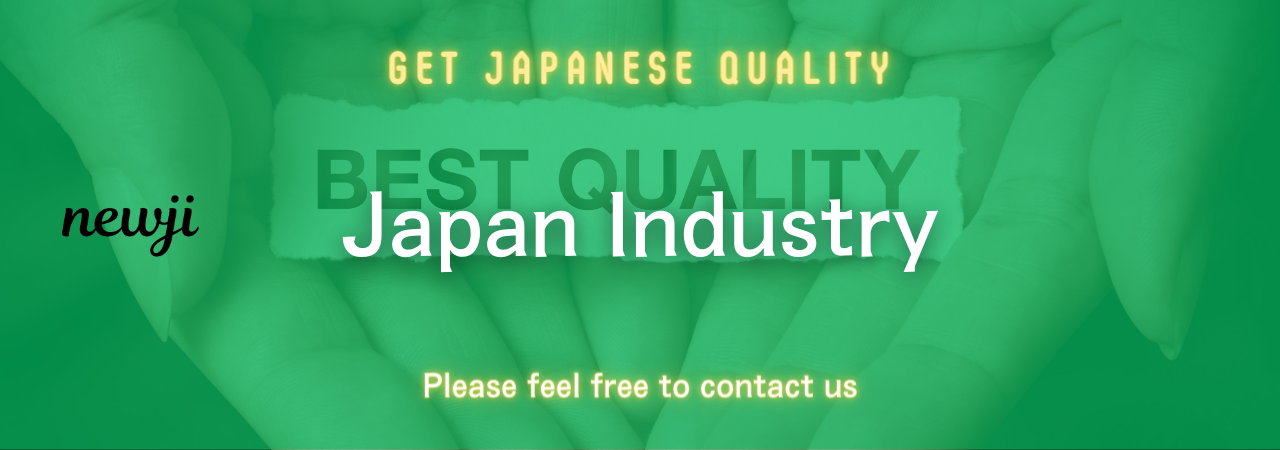
Quality Function Deployment (QFD) is a powerful tool that manufacturers can use to improve both their product quality and overall efficiency. By focusing on customer needs and systematically translating them into specific, actionable requirements, QFD helps companies make informed decisions that can significantly reduce costs and enhance the value delivered to customers. Let’s dive deeper into how QFD can achieve these goals and why it is a vital methodology for any manufacturer aiming for excellence.
目次
What is Quality Function Deployment?
QFD is a structured method that helps organizations translate customer requirements into technical specifications.
First developed in Japan in the 1960s, it has since become a global standard for quality assurance and product development.
The essence of QFD lies in its ability to capture customer needs (often referred to as the “voice of the customer”) and ensure they are addressed throughout the design and development process.
The Four Phases of QFD
The QFD process is typically divided into four phases:
1. Product Planning
This phase is all about understanding what the customers want.
Through surveys, interviews, and other forms of market research, companies gather detailed data on customer needs.
This information is then organized in a matrix often referred to as the “House of Quality,” which helps visualize the relationship between customer needs and product specifications.
2. Product Design
Once the customer requirements are clear, the next step is to translate these needs into specific product features.
This is where the engineering team comes in, working closely with the marketing team to ensure that every technical specification aligns with customer expectations.
3. Process Planning
With the product features defined, the focus shifts to how these features will be produced.
Process planning involves determining the best methods and materials for manufacturing, ensuring that the process is efficient and cost-effective.
4. Process Control
The final phase involves setting up quality control measures to ensure that the production process consistently meets the defined specifications.
This often includes developing standard operating procedures and conducting regular inspections and audits.
How QFD Reduces Costs
Implementing QFD can lead to significant cost savings for manufacturers. Here are some ways how:
Streamlined Processes
By clearly defining customer needs and aligning them with technical specifications early in the development process, companies can avoid costly revisions and rework.
This helps streamline the production process, making it more efficient and cost-effective.
Reduced Waste
QFD focuses on adding value by eliminating non-essential features and processes.
This reduces material waste and lowers production costs.
For instance, understanding that a customer prioritizes durability over aesthetic features can help a manufacturer focus resources on what truly matters.
Better Supplier Relationships
QFD often involves close collaboration with suppliers to ensure that their products meet the necessary quality standards.
This can lead to stronger supplier relationships and better pricing agreements, further reducing costs.
Improved Team Collaboration
QFD encourages cross-functional collaboration, bringing together teams from different departments such as marketing, engineering, and quality assurance.
This collaborative approach helps identify and solve potential issues early, reducing the likelihood of costly delays and errors.
How QFD Improves Quality
Quality improvement is at the heart of QFD. Here’s how it helps:
Customer-Centric Approach
By focusing on the voice of the customer, QFD ensures that the final product meets or exceeds customer expectations.
This customer-centric approach leads to higher quality products and greater customer satisfaction.
Rigorous Documentation
QFD involves detailed documentation at every stage of the development process.
This rigorous documentation helps maintain high standards of quality by ensuring that every team member understands their responsibilities and the specific requirements they need to meet.
Continuous Improvement
QFD is not a one-time activity but an ongoing process of continuous improvement.
By regularly revisiting and updating the QFD matrices, companies can adapt to changing customer needs and market conditions, ensuring their products remain of high quality.
Enhanced Problem-Solving
The systematic nature of QFD helps identify potential quality issues early in the development process.
This enables teams to address problems before they escalate, leading to higher quality outcomes and fewer defects.
Steps to Implement QFD in Your Organization
Implementing QFD requires careful planning and execution.
Here are some steps to get started:
Train Your Team
Before implementing QFD, it’s essential to train your team on the principles and practices of the methodology.
This ensures everyone understands their role and how QFD can benefit the organization.
Conduct Market Research
Gather detailed information on customer needs and preferences through surveys, interviews, and other forms of market research.
This data will form the foundation of your QFD process.
Develop the House of Quality
Create a House of Quality matrix to organize customer needs and translate them into specific product requirements.
This matrix will serve as a roadmap for your product development process.
Foster Cross-Functional Collaboration
Encourage collaboration between different departments, such as marketing, engineering, and quality assurance.
This cross-functional approach helps ensure that all aspects of the product development process are aligned with customer needs.
Implement and Monitor
Once you’ve developed your QFD plan, implement it and monitor its progress closely.
Regularly review and update your QFD matrices to ensure they remain relevant and effective.
QFD is a transformative tool that can help manufacturers reduce costs and improve quality by placing customer needs at the center of the product development process.
By streamlining processes, reducing waste, and fostering cross-functional collaboration, QFD enables companies to deliver high-quality products that meet or exceed customer expectations.
Implementing QFD requires careful planning and ongoing commitment, but the rewards in terms of cost savings, improved quality, and customer satisfaction are well worth the effort.
資料ダウンロード
QCD調達購買管理クラウド「newji」は、調達購買部門で必要なQCD管理全てを備えた、現場特化型兼クラウド型の今世紀最高の購買管理システムとなります。
ユーザー登録
調達購買業務の効率化だけでなく、システムを導入することで、コスト削減や製品・資材のステータス可視化のほか、属人化していた購買情報の共有化による内部不正防止や統制にも役立ちます。
NEWJI DX
製造業に特化したデジタルトランスフォーメーション(DX)の実現を目指す請負開発型のコンサルティングサービスです。AI、iPaaS、および先端の技術を駆使して、製造プロセスの効率化、業務効率化、チームワーク強化、コスト削減、品質向上を実現します。このサービスは、製造業の課題を深く理解し、それに対する最適なデジタルソリューションを提供することで、企業が持続的な成長とイノベーションを達成できるようサポートします。
オンライン講座
製造業、主に購買・調達部門にお勤めの方々に向けた情報を配信しております。
新任の方やベテランの方、管理職を対象とした幅広いコンテンツをご用意しております。
お問い合わせ
コストダウンが利益に直結する術だと理解していても、なかなか前に進めることができない状況。そんな時は、newjiのコストダウン自動化機能で大きく利益貢献しよう!
(Β版非公開)