- お役立ち記事
- How safety management departments should implement HAZOP analysis to strengthen risk assessment
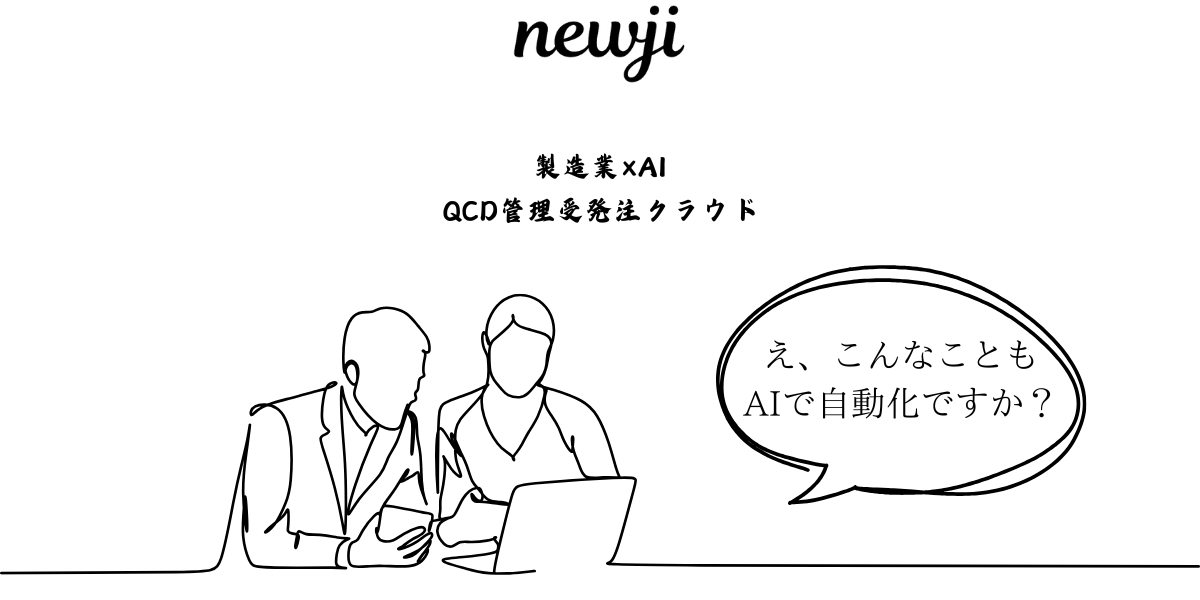
How safety management departments should implement HAZOP analysis to strengthen risk assessment
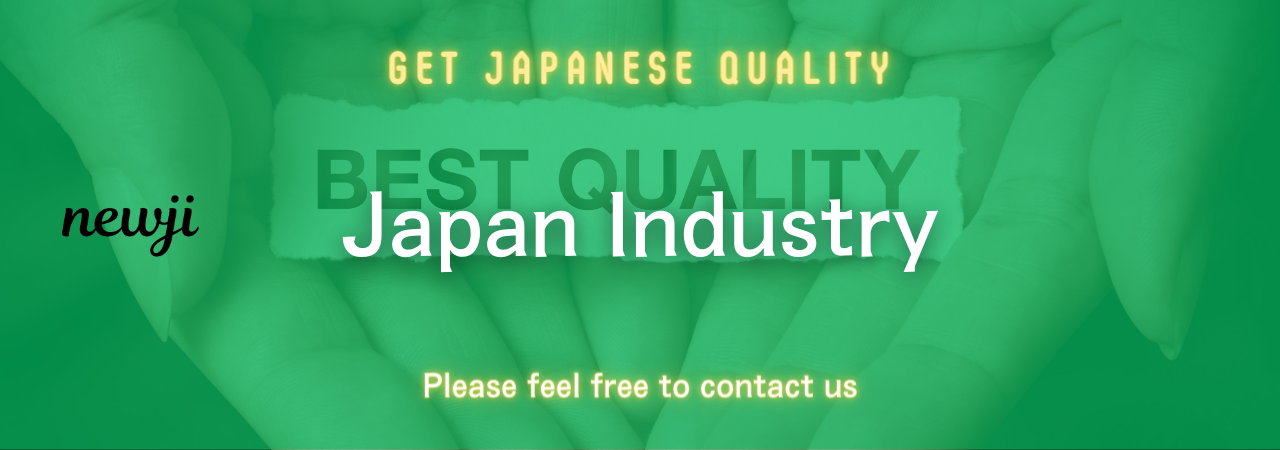
目次
Understanding HAZOP Analysis
Hazard and Operability Study, commonly known as HAZOP, is a structured and systematic technique used primarily for risk management in processes and systems.
It is widely employed in safety management departments to identify potential hazards and operational issues, making it an invaluable tool for improving workplace safety and efficiency.
The core objective of HAZOP is to review processes and operations to pinpoint potential deviations from the intended design and identify risks associated with those deviations.
This analysis helps in ensuring that all necessary safety measures are in place to mitigate any identified risks.
The Importance of a Thorough Risk Assessment
Performing a detailed risk assessment is crucial for any safety management department.
A risk assessment helps in evaluating the potential risks in a workplace, identifying which risks need attention, and implementing preventive measures to safeguard against accidents or operational failures.
The importance of such assessments cannot be overstated, as they form the backbone of a comprehensive safety management system.
Incorporating HAZOP into risk assessments provides a structured way to assess risks, ensuring that all potential hazards are systematically identified and evaluated.
This helps in creating a safer work environment by proactively addressing issues before they develop into actual problems.
Implementing HAZOP in Safety Management
Implementing HAZOP analysis involves several steps that are critical for a successful outcome.
Firstly, forming a competent and multidisciplinary team is essential.
The team should consist of experts with varied backgrounds who can bring a wide range of perspectives to the analysis.
Next, the scope of the HAZOP study needs to be clearly defined.
This includes setting boundaries for the assessment, determining the systems and processes to be analyzed, and establishing the objectives of the study.
A well-defined scope ensures that the analysis remains focused and thorough.
Once the groundwork is ready, the HAZOP team conducts a detailed review of each process or system under study.
The team uses guide words such as “more,” “less,” “no,” and “reverse” to explore all possible deviations from the design intent by posing questions that help identify potential hazards.
This systematic questioning is what makes HAZOP such a powerful tool.
Recording and Analyzing Results
As potential deviations and hazards are identified, they should be meticulously documented for further analysis.
The team assesses these findings to determine the likelihood of each hazard occurring and the potential consequences.
This step is crucial for evaluating the overall risk associated with each hazard.
After evaluating the risks, the team develops a set of recommendations or solutions to mitigate the identified risks.
These recommendations should focus on eliminating hazards, reducing the likelihood of occurrence, or minimizing the potential impact.
Implementing these measures proactively contributes to enhanced workplace safety.
Ensuring Effective Communication
Effective communication is key when it comes to implementing HAZOP analysis.
The findings and recommendations should be conveyed clearly and concisely to all stakeholders involved, from management to the teams responsible for executing the changes.
Proper communication ensures that everyone is aware of the potential risks, the reasons behind the recommended changes, and the necessary actions to implement those changes.
This collaborative approach helps in achieving buy-in from all levels of the organization, promoting a culture of safety and continuous improvement.
Continuous Monitoring and Reevaluation
The risk landscape is ever-evolving, and as such, the HAZOP process is not a one-time event.
Continuous monitoring of implemented safety measures is essential to ensure their effectiveness over time.
Regular reevaluation of risk assessments and HAZOP analysis should also be conducted to adapt to any changes in processes, technology, or the organizational structure.
Revisiting the analysis periodically allows safety management departments to stay proactive in their approach to risk management, reinforcing their commitment to maintaining a safe and efficient work environment.
Benefits of HAZOP Analysis in Risk Management
The benefits of integrating HAZOP analysis into risk management processes are manifold.
Firstly, it enhances the identification of potential hazards in a structured manner, reducing the likelihood of overlooked risks.
It also promotes interdisciplinary collaboration, leading to comprehensive insights and innovative solutions.
Furthermore, HAZOP analysis aids in improving operational efficiency.
By identifying and addressing potential disruptions and inefficiencies before they occur, organizations can prevent costly stoppages and maintain uninterrupted operations.
Lastly, a successful HAZOP implementation leads to a more robust safety culture within the organization.
When employees see their safety concerns being systematically addressed, it fosters trust and encourages active participation in safety initiatives.
Conclusion
HAZOP analysis is a critical tool for safety management departments aiming to strengthen their risk assessment processes.
By systematically identifying and addressing potential hazards, organizations can create a safer work environment and improve operational efficiency.
With a clearly defined scope, a capable team, and a commitment to continuous improvement, HAZOP can significantly enhance an organization’s safety management efforts.
Incorporating HAZOP into risk management not only helps in mitigating risks but also elevates the organization’s overall safety culture, ensuring long-term success and sustainability.
資料ダウンロード
QCD調達購買管理クラウド「newji」は、調達購買部門で必要なQCD管理全てを備えた、現場特化型兼クラウド型の今世紀最高の購買管理システムとなります。
ユーザー登録
調達購買業務の効率化だけでなく、システムを導入することで、コスト削減や製品・資材のステータス可視化のほか、属人化していた購買情報の共有化による内部不正防止や統制にも役立ちます。
NEWJI DX
製造業に特化したデジタルトランスフォーメーション(DX)の実現を目指す請負開発型のコンサルティングサービスです。AI、iPaaS、および先端の技術を駆使して、製造プロセスの効率化、業務効率化、チームワーク強化、コスト削減、品質向上を実現します。このサービスは、製造業の課題を深く理解し、それに対する最適なデジタルソリューションを提供することで、企業が持続的な成長とイノベーションを達成できるようサポートします。
オンライン講座
製造業、主に購買・調達部門にお勤めの方々に向けた情報を配信しております。
新任の方やベテランの方、管理職を対象とした幅広いコンテンツをご用意しております。
お問い合わせ
コストダウンが利益に直結する術だと理解していても、なかなか前に進めることができない状況。そんな時は、newjiのコストダウン自動化機能で大きく利益貢献しよう!
(Β版非公開)