- お役立ち記事
- How SMEs Can Balance Quality and Cost in Precision Cutting
How SMEs Can Balance Quality and Cost in Precision Cutting
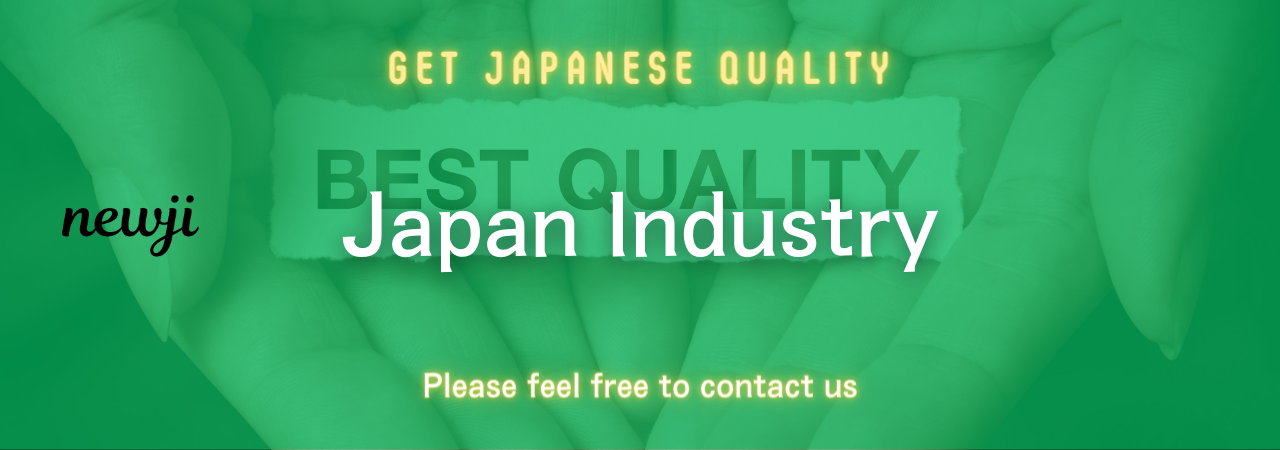
Running a small or medium-sized enterprise (SME) in the manufacturing sector isn’t a walk in the park, especially when it comes to precision cutting.
The dilemma often faced by SMEs is striking that fine balance between maintaining high-quality standards and managing costs.
Precision cutting is not just a technical process; it’s a delicate art that can have a significant impact on your product quality, customer satisfaction, and ultimately, your bottom line.
目次
Understanding Precision Cutting
Precision cutting refers to the process of cutting materials to exact specifications with minimal tolerances.
This is usually achieved through advanced machinery such as laser cutters, waterjet cutters, or CNC (Computer Numerical Control) machines.
These tools are designed to handle complex tasks with great accuracy, making them essential for industries where high precision is required, such as aerospace, medical devices, and electronics.
Why Precision Matters
When you’re working in industries that demand high-quality products, deviations from specifications can result in significant issues.
Poor cuts can lead to a cascade of problems, including:
– Reduced product performance
– Increased waste and cost
– Negative customer reviews
– Potential recalls and legal issues
Ensuring precision in cutting processes can mitigate these risks and foster trust with your clients.
Balancing Quality and Cost
Investing in precision cutting tools and processes can be expensive, which is why many SMEs struggle to find an appropriate balance between quality and cost.
However, it is possible to maintain high-quality standards without breaking the bank.
Invest in Reliable Equipment
One of the most significant investments you’ll make is in the machinery itself.
While it might be tempting to opt for cheaper equipment, low-quality machinery can result in poor cuts and lead to higher costs in the long run due to frequent breakdowns and maintenance needs.
Investing in reliable equipment from reputable manufacturers can offer:
– Longer lifespan
– Reduced downtime
– Consistent high-quality output
Always consider the total cost of ownership instead of just the upfront cost.
Regular Maintenance
Maintaining your cutting machinery is crucial for consistent quality and cost-efficiency.
Neglecting maintenance can lead to performance issues, costly repairs, and decreased lifespan of your equipment.
Some key maintenance practices include:
– Regularly cleaning the machine
– Checking for and replacing worn-out parts
– Lubricating moving parts as needed
– Running regular diagnostic checks
By adopting a proactive maintenance schedule, you can prevent unexpected breakdowns and maintain a consistent quality in your cutting processes.
Optimize Material Usage
Material cost is another significant factor that can affect your bottom line.
Optimal material usage can save you a substantial amount of money while ensuring quality.
Some strategies for optimizing material usage include:
– Nesting: Efficiently laying out the shapes to be cut on the material sheet to minimize waste
– Using leftover materials for smaller parts or prototypes
– Implementing precise tolerances to reduce material consumption
These practices not only reduce material waste but also demonstrate a commitment to sustainability, which can boost your company’s reputation.
Train Your Workforce
The skill level of your operators can significantly impact the quality and efficiency of precision cutting.
Invest in training programs that ensure your workforce is well-versed in operating cutting machinery, maintaining equipment, and understanding material properties.
Training can include:
– Hands-on experience with the equipment
– Understanding software for CNC machines
– Troubleshooting common issues
When your staff is skilled and knowledgeable, they can better utilize the machinery and produce high-quality parts.
Leveraging Technology
Advancements in technology offer various tools to help SMEs balance quality and cost in precision cutting.
Use CAD/CAM Software
Computer-Aided Design (CAD) and Computer-Aided Manufacturing (CAM) software are essential for precision cutting.
These tools allow you to design components with exact specifications and plan the cutting process efficiently.
Benefits of using CAD/CAM software include:
– Increased accuracy in designs
– Reduced setup time
– Improved material utilization
By leveraging these tools, you can reduce errors and ensure that the cutting process is as efficient as possible.
Adopt Automation
Automation can significantly improve both the quality and cost-efficiency of your precision cutting operations.
Automated systems can take over repetitive tasks, reduce human error, and increase the speed of production.
Implementing automation can offer:
– Consistent quality with minimal variations
– Lower labor costs
– Faster turnaround times
Though the initial investment in automation might be high, the long-term benefits make it a worthwhile consideration.
Outsourcing Options
For SMEs that find the upfront costs of machinery and training prohibitive, outsourcing precision cutting tasks to specialized firms can be an effective solution.
Benefits of Outsourcing
Outsourcing can provide several benefits, including:
– Access to high-end machinery without the capital expenditure
– Expertise from skilled operators
– Flexibility to scale production up or down based on demand
Outsourcing allows you to focus on your core competencies while still ensuring high-quality precision cutting.
Conclusion
Balancing quality and cost in precision cutting is not an insurmountable challenge.
By making strategic investments in high-quality equipment, maintaining your machinery, optimizing material usage, training your workforce, and leveraging advanced technologies, you can achieve the perfect equilibrium.
Whether you decide to manage everything in-house or opt for outsourcing, the key lies in a well-thought-out approach that considers all aspects of the production process.
By doing so, SMEs can maintain high standards of quality without incurring prohibitive costs, thereby achieving long-term success and customer satisfaction.
資料ダウンロード
QCD調達購買管理クラウド「newji」は、調達購買部門で必要なQCD管理全てを備えた、現場特化型兼クラウド型の今世紀最高の購買管理システムとなります。
ユーザー登録
調達購買業務の効率化だけでなく、システムを導入することで、コスト削減や製品・資材のステータス可視化のほか、属人化していた購買情報の共有化による内部不正防止や統制にも役立ちます。
NEWJI DX
製造業に特化したデジタルトランスフォーメーション(DX)の実現を目指す請負開発型のコンサルティングサービスです。AI、iPaaS、および先端の技術を駆使して、製造プロセスの効率化、業務効率化、チームワーク強化、コスト削減、品質向上を実現します。このサービスは、製造業の課題を深く理解し、それに対する最適なデジタルソリューションを提供することで、企業が持続的な成長とイノベーションを達成できるようサポートします。
オンライン講座
製造業、主に購買・調達部門にお勤めの方々に向けた情報を配信しております。
新任の方やベテランの方、管理職を対象とした幅広いコンテンツをご用意しております。
お問い合わせ
コストダウンが利益に直結する術だと理解していても、なかなか前に進めることができない状況。そんな時は、newjiのコストダウン自動化機能で大きく利益貢献しよう!
(Β版非公開)