- お役立ち記事
- How “Stress Concentration” is Revolutionizing Japanese Manufacturing Techniques: Bridging Tradition with Innovation
月間76,176名の
製造業ご担当者様が閲覧しています*
*2025年3月31日現在のGoogle Analyticsのデータより
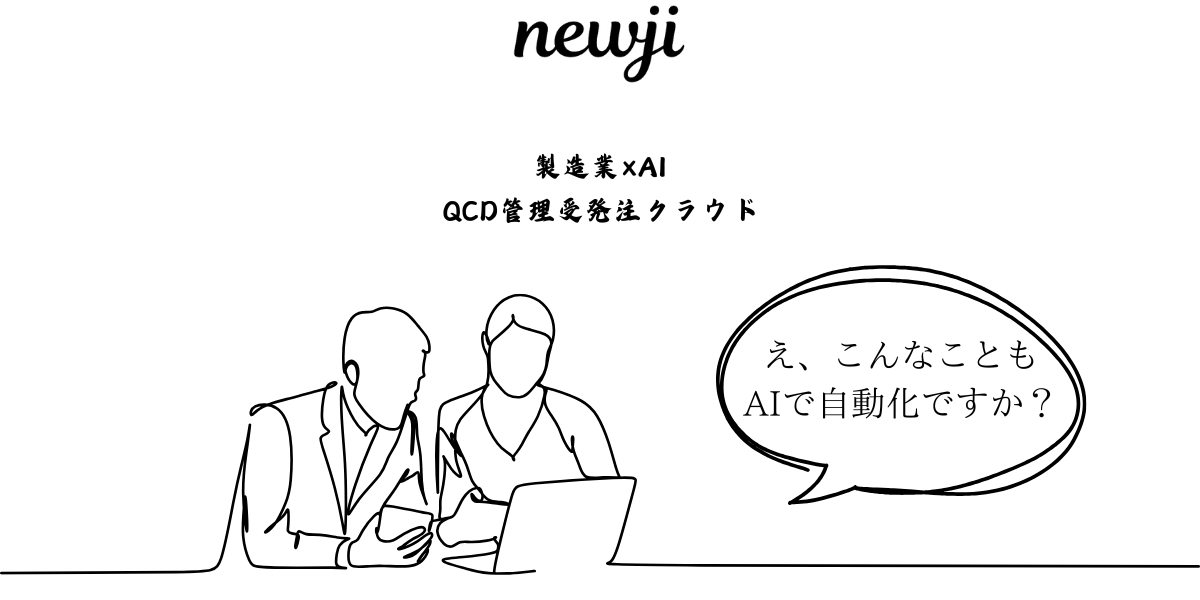
How “Stress Concentration” is Revolutionizing Japanese Manufacturing Techniques: Bridging Tradition with Innovation
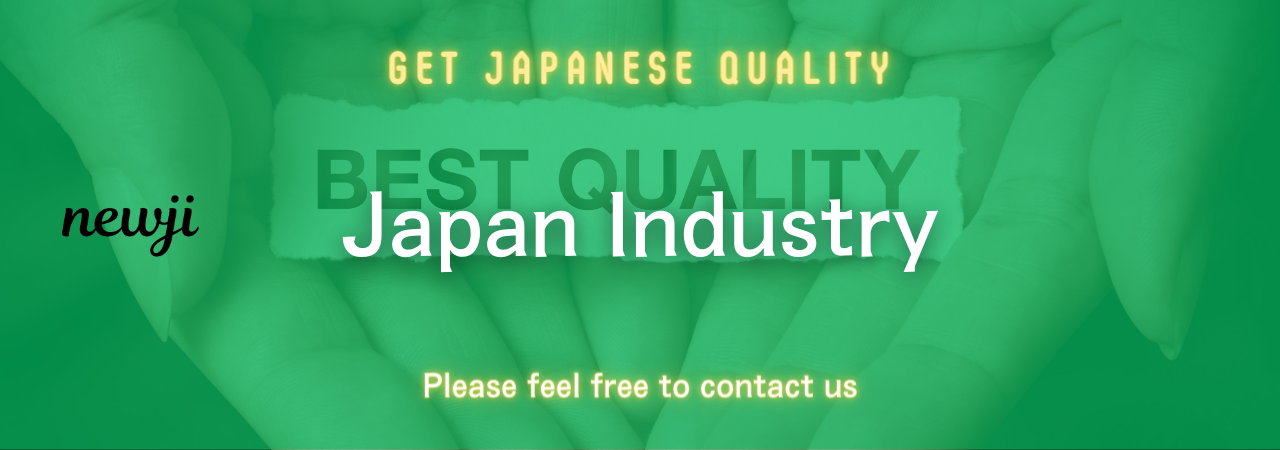
目次
Introduction to Stress Concentration in Japanese Manufacturing
Stress concentration has become a pivotal concept in modern Japanese manufacturing techniques.
This principle focuses on the distribution of stress within materials, ensuring durability and efficiency.
Japanese manufacturers have long been renowned for their precision and innovation.
Integrating stress concentration into manufacturing processes bridges traditional craftsmanship with cutting-edge technology.
This fusion enhances product quality and extends the lifespan of manufactured goods.
Understanding stress concentration is essential for companies aiming to collaborate with Japanese suppliers.
It offers insights into the meticulous nature of Japanese engineering and their commitment to excellence.
The Role of Stress Concentration in Manufacturing Processes
Stress concentration refers to areas within a material where stress is significantly higher than the surrounding regions.
These localized stresses can lead to material failure if not properly managed.
Japanese manufacturers utilize stress concentration principles to design products that withstand various forces and strains.
By anticipating stress points, they enhance the structural integrity of their products.
This proactive approach minimizes defects and reduces the likelihood of product recalls.
Incorporating stress concentration analysis into the manufacturing process allows for the creation of more resilient products.
It also contributes to the overall efficiency and reliability of manufacturing operations.
Bridging Tradition with Innovation
Japanese manufacturing is characterized by a harmonious blend of traditional techniques and modern innovations.
Stress concentration is a testament to this synergy, where ancient craftsmanship meets contemporary engineering.
Traditional methods emphasize meticulous attention to detail and quality.
When combined with innovative stress analysis tools, manufacturers achieve superior results.
This integration fosters continuous improvement and adaptability in manufacturing practices.
It also ensures that products meet the evolving demands of the global market.
By maintaining a balance between tradition and innovation, Japanese manufacturers stay ahead in a competitive industry.
Impact on Procurement and Purchasing
Incorporating stress concentration into manufacturing has significant implications for procurement and purchasing strategies.
Understanding the technical aspects of stress concentration aids in selecting the right materials and components.
Japanese suppliers often offer specialized products designed to optimize stress distribution.
Procurement teams must collaborate closely with suppliers to ensure that materials meet specific stress concentration requirements.
This collaboration enhances product quality and reduces the risk of material failure.
Moreover, knowledge of stress concentration helps in forecasting material needs and managing inventory effectively.
It also facilitates better cost management by minimizing waste and reducing the need for frequent replacements.
Advantages of Integrating Stress Concentration Techniques
Implementing stress concentration techniques offers numerous benefits to manufacturers and purchasing departments.
Enhanced Product Durability
Stress concentration analysis leads to the development of more durable products.
By identifying and mitigating potential stress points, manufacturers reduce the likelihood of product failure.
Cost Efficiency
Preventing material failure translates to cost savings by minimizing the need for repairs and replacements.
Efficient resource utilization ensures that materials are used optimally, reducing waste.
Competitive Advantage
Products designed with stress concentration in mind often outperform competitors in terms of reliability and longevity.
This can lead to increased market share and customer loyalty.
Improved Supplier Relationships
Collaborating on stress concentration techniques fosters stronger relationships with suppliers.
Shared knowledge and goals lead to more effective partnerships and better overall outcomes.
Disadvantages and Challenges
Despite its advantages, integrating stress concentration techniques presents certain challenges.
Increased Initial Costs
Implementing advanced stress analysis tools and training staff can lead to higher initial investments.
Complexity in Design
Designing products with stress concentration considerations adds complexity to the manufacturing process.
This requires specialized knowledge and expertise.
Supplier Dependence
Relying on suppliers for specialized materials and components may lead to dependency risks.
Ensuring consistent quality and reliability from suppliers becomes crucial.
Time-Consuming Processes
Stress concentration analysis can extend the product development timeline, potentially delaying time-to-market.
Supplier Negotiation Techniques
Effective negotiation with suppliers is essential for successful integration of stress concentration techniques.
Understanding Supplier Capabilities
Assess the technical expertise and resources of potential suppliers in stress concentration.
This ensures they can meet the specific requirements of your manufacturing processes.
Establishing Clear Communication
Clearly articulate your needs and expectations related to stress concentration.
Open communication fosters mutual understanding and collaboration.
Building Long-Term Relationships
Focus on building lasting partnerships rather than short-term gains.
Long-term relationships encourage suppliers to invest in meeting your stress concentration needs.
Leveraging Volume Discounts
Negotiate pricing based on volume commitments, which can lead to cost savings.
Flexible Terms
Seek flexible payment and delivery terms to accommodate the complexities of stress concentration processes.
Collaborative Problem-Solving
Work together with suppliers to address any challenges related to stress concentration, fostering a cooperative environment.
Market Conditions Influencing Stress Concentration Adoption
Various market conditions affect the adoption of stress concentration techniques in manufacturing.
Technological Advancements
Rapid advancements in technology provide new tools and methods for stress analysis, facilitating easier adoption.
Economic Climate
Economic stability influences investment in advanced manufacturing techniques.
During stable periods, companies are more likely to invest in improving their manufacturing processes.
Industry Standards
Evolving industry standards may mandate the use of specific stress concentration techniques for compliance.
Competitive Pressure
High competition drives manufacturers to adopt stress concentration techniques to differentiate their products.
Consumer Expectations
Increasing consumer demand for high-quality and durable products encourages the adoption of stress concentration practices.
Best Practices for Implementing Stress Concentration Techniques
Adopting stress concentration techniques requires strategic planning and execution.
Conduct Comprehensive Training
Ensure that your team is well-versed in stress concentration principles and their application in manufacturing.
Invest in Advanced Tools
Utilize state-of-the-art stress analysis software and equipment to enhance precision and efficiency.
Collaborate with Experts
Engage with industry experts and consultants to gain deeper insights into effective stress concentration methodologies.
Establish Robust Quality Control
Implement stringent quality control measures to monitor stress concentration factors throughout the manufacturing process.
Foster Continuous Improvement
Encourage a culture of continuous improvement to refine stress concentration techniques and adapt to new challenges.
Integrate with Supply Chain
Align stress concentration practices with your supply chain management to ensure seamless material flow and coordination with suppliers.
Monitor and Evaluate
Regularly assess the effectiveness of stress concentration techniques and make necessary adjustments based on performance data.
Case Studies: Success Stories in Japanese Manufacturing
Examining real-world applications of stress concentration techniques provides valuable insights into their effectiveness.
Automotive Industry
Japanese automotive manufacturers have incorporated stress concentration analysis to enhance vehicle safety and performance.
By identifying critical stress points in engine components, they have developed more reliable and efficient engines.
Electronics Sector
In the electronics industry, stress concentration techniques have led to the creation of more durable and compact devices.
This has resulted in products that can withstand higher operational stresses without compromising functionality.
Aerospace Field
Japanese aerospace companies utilize stress concentration principles to design lightweight yet robust aircraft components.
This not only improves fuel efficiency but also enhances the overall safety and longevity of the aircraft.
Future Trends in Stress Concentration and Japanese Manufacturing
The future of stress concentration in Japanese manufacturing is poised for significant advancements.
Integration with Artificial Intelligence
AI-driven stress analysis tools will enable more accurate and faster identification of stress points, enhancing manufacturing precision.
Sustainable Manufacturing Practices
Incorporating stress concentration with sustainable practices will lead to the development of eco-friendly and durable products.
Advanced Materials
The use of novel materials with superior stress distribution properties will further revolutionize manufacturing techniques.
Global Collaboration
Increased international collaboration will facilitate the exchange of knowledge and best practices related to stress concentration.
Automation and Robotics
Automation will streamline stress concentration analysis and implementation, increasing efficiency and reducing human error.
Conclusion
Stress concentration is revolutionizing Japanese manufacturing by seamlessly bridging traditional craftsmanship with modern innovation.
Its integration enhances product durability, efficiency, and quality, providing a competitive edge in the global market.
For procurement and purchasing professionals, understanding stress concentration is crucial in selecting the right suppliers and materials.
Despite certain challenges, the benefits of adopting stress concentration techniques make it a worthwhile investment.
By following best practices and fostering strong supplier relationships, manufacturers can effectively implement stress concentration strategies.
As the industry continues to evolve, stress concentration will remain a cornerstone of Japanese manufacturing excellence, driving future advancements and sustaining its reputation for high-quality products.
資料ダウンロード
QCD管理受発注クラウド「newji」は、受発注部門で必要なQCD管理全てを備えた、現場特化型兼クラウド型の今世紀最高の受発注管理システムとなります。
ユーザー登録
受発注業務の効率化だけでなく、システムを導入することで、コスト削減や製品・資材のステータス可視化のほか、属人化していた受発注情報の共有化による内部不正防止や統制にも役立ちます。
NEWJI DX
製造業に特化したデジタルトランスフォーメーション(DX)の実現を目指す請負開発型のコンサルティングサービスです。AI、iPaaS、および先端の技術を駆使して、製造プロセスの効率化、業務効率化、チームワーク強化、コスト削減、品質向上を実現します。このサービスは、製造業の課題を深く理解し、それに対する最適なデジタルソリューションを提供することで、企業が持続的な成長とイノベーションを達成できるようサポートします。
製造業ニュース解説
製造業、主に購買・調達部門にお勤めの方々に向けた情報を配信しております。
新任の方やベテランの方、管理職を対象とした幅広いコンテンツをご用意しております。
お問い合わせ
コストダウンが利益に直結する術だと理解していても、なかなか前に進めることができない状況。そんな時は、newjiのコストダウン自動化機能で大きく利益貢献しよう!
(β版非公開)