- お役立ち記事
- How to achieve both cost reduction and quality improvement promoted by the purchasing department
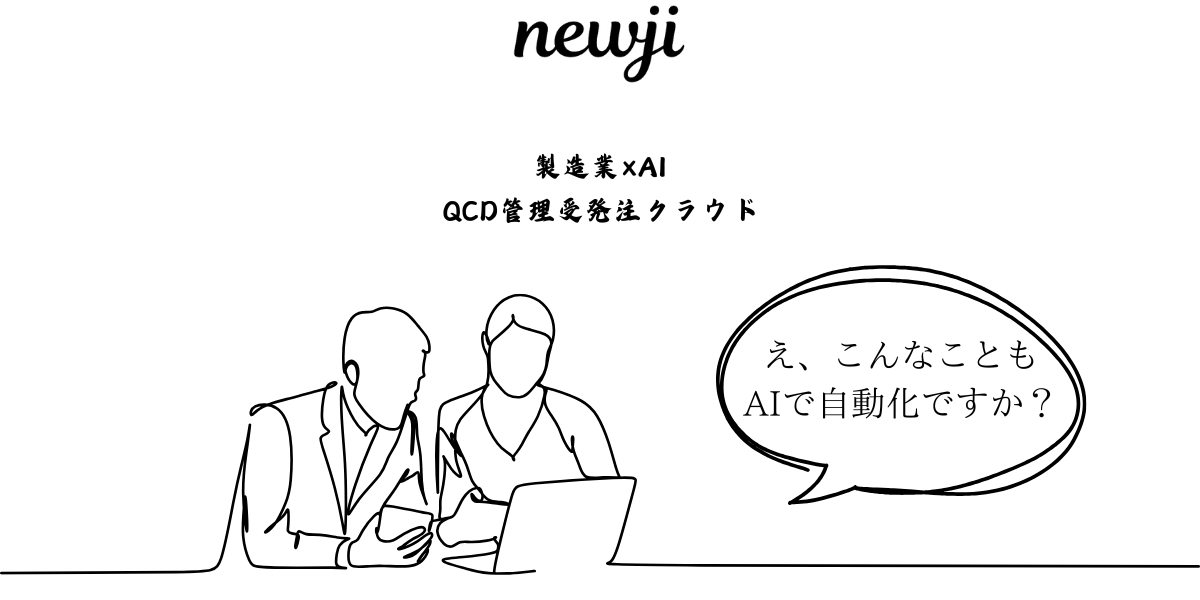
How to achieve both cost reduction and quality improvement promoted by the purchasing department
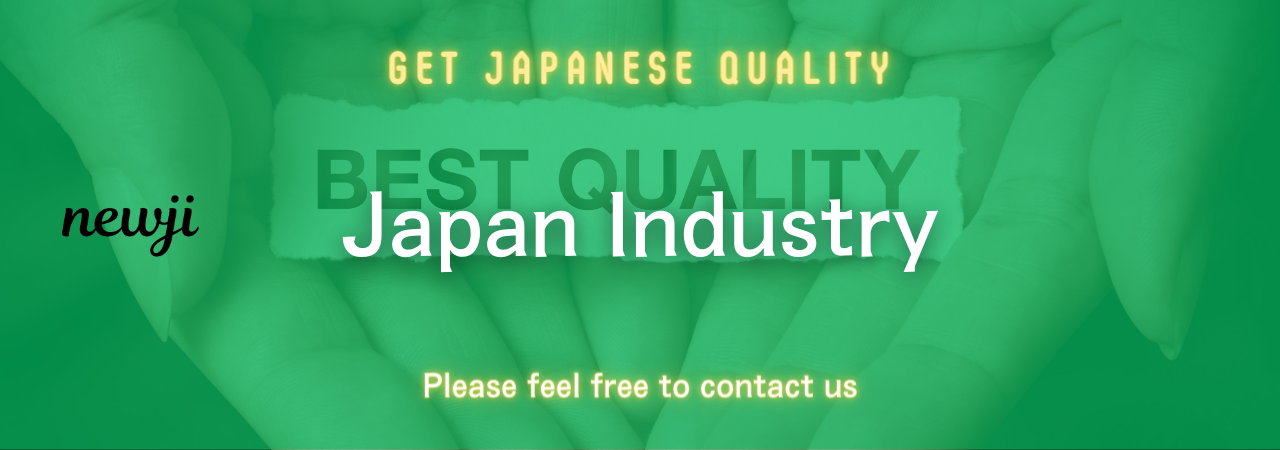
目次
Understanding the Balance Between Cost Reduction and Quality Improvement
The purchasing department plays a critical role in a company’s success by managing costs and ensuring quality.
It might seem challenging to maintain quality while reducing costs, but it’s entirely feasible with strategic planning and execution.
Achieving this balance is crucial for an organization to stay competitive and profitable.
In the modern business landscape, companies are under constant pressure to reduce costs without compromising quality.
This demand can be particularly weighty for those in the purchasing department.
Their influence extends across procurement, supplier management, and ensuring the acquisition of goods that meet required standards.
Let’s explore how this can be achieved practically and effectively.
Building Strong Supplier Relationships
One of the most effective ways to reduce costs while maintaining quality is by nurturing strong relationships with suppliers.
When a good rapport exists, there’s room for negotiation and collaboration, leading to better pricing and terms.
Suppliers who view your company as a partner rather than just a customer are more inclined to offer favorable deals and additional benefits, such as bulk discounts or extended payment terms.
Communicating openly about needs and expectations can also lead to suppliers prioritizing your orders, which enhances quality by reducing lead times and potential delays.
It’s crucial to perform regular evaluations of suppliers’ performance to ensure that quality standards are consistently met.
Implementing Strategic Sourcing
Strategic sourcing involves analyzing and optimizing the purchasing process to maximize efficiency and value.
It demands a comprehensive understanding of the market to identify where costs can be reduced without impacting quality.
For instance, a company might discover that switching to a different supplier or sourcing regionally can cut costs.
Strategic sourcing also involves supplier segmentation, allowing companies to classify vendors based on their importance and the nature of goods they provide.
This enables tailored sourcing strategies, ensuring that cost savings do not compromise essential quality specifications.
Utilizing Technology and Automation
Technology plays a pivotal role in helping purchasing departments achieve cost reduction and quality improvement.
Procurement software and automation tools streamline processes, reducing the time and labor associated with manual tasks and thus cutting costs.
Automation enhances accuracy and efficiency, decreasing the likelihood of errors that can lead to substandard quality or additional costs, like returns or rejections.
Additionally, technology can provide data analytics to uncover trends and insights, enabling more informed decision-making and better forecasting.
Focusing on Total Cost of Ownership
When trying to reduce costs, it’s tempting to focus on upfront costs alone.
However, a deeper investigation into the total cost of ownership (TCO) can result in more sustainable cost savings.
TCO encompasses all costs associated with the procurement of goods, including transportation, storage, handling, and disposal costs.
By evaluating TCO, purchasing managers can make more informed decisions about suppliers and materials, often finding cheaper alternatives that do not compromise on quality or increase long-term costs.
Companies should also evaluate whether higher-quality materials, which might be more expensive initially, could reduce costs over time through decreased waste, maintenance, or replacements.
Continuous Improvement through Lean Principles
Applying lean principles helps organizations focus on value through eliminating waste throughout their procurement processes.
Waste can take many forms, such as overproduction, waiting times, or excess inventory.
By identifying and eliminating these wasteful practices, companies can reduce costs significantly while enhancing quality.
A culture of continuous improvement allows for regular assessments of procurement practices and encourages innovation.
This, in turn, leads to heightened efficiency and effectiveness in achieving cost reduction and quality standards.
Training and Development of Staff
Well-trained purchasing staff are equipped to handle the complexities that come with balancing cost and quality.
Regular training sessions can keep the team updated on the latest trends, technologies, and strategies in procurement.
Knowledgeable staff can identify opportunities for better pricing and improved quality and are also more adept at negotiating with suppliers.
Investing in employee development fosters a proactive workplace culture where everyone contributes to continuous improvement efforts.
Collaborative Internal Communication
Achieving cost reduction and quality improvement is not solely the responsibility of the purchasing department.
It requires collaboration across multiple departments, such as production, quality control, finance, and more.
By maintaining open lines of communication, departments can work together to streamline processes.
This ensures all teams are aligned on goals and expectations, minimizing errors and improving quality.
Regular meetings and updates help keep everyone on the same page, while shared objectives contribute to a unified effort towards achieving the company’s aims.
Creating a Benchmark for Success
Setting benchmarks is pivotal to measuring success in cost reduction and quality improvement efforts.
Purchasing departments should maintain records and reports to track progress against these benchmarks.
Analyzing this data allows firms to understand what strategies work and which ones need adjustment or enhancement.
Over time, a company can establish best practices and models for others in the industry by frequently revising their practices and honestly evaluating outcomes.
In conclusion, while achieving both cost reduction and quality improvement is challenging, it is attainable with well-planned strategies.
A focus on strategic sourcing, technology, and collaborative efforts across departments lays the groundwork for success.
By concentrating on strong supplier relationships, total cost of ownership, and employee development, a company can navigate the complexities of procurement effectively.
資料ダウンロード
QCD調達購買管理クラウド「newji」は、調達購買部門で必要なQCD管理全てを備えた、現場特化型兼クラウド型の今世紀最高の購買管理システムとなります。
ユーザー登録
調達購買業務の効率化だけでなく、システムを導入することで、コスト削減や製品・資材のステータス可視化のほか、属人化していた購買情報の共有化による内部不正防止や統制にも役立ちます。
NEWJI DX
製造業に特化したデジタルトランスフォーメーション(DX)の実現を目指す請負開発型のコンサルティングサービスです。AI、iPaaS、および先端の技術を駆使して、製造プロセスの効率化、業務効率化、チームワーク強化、コスト削減、品質向上を実現します。このサービスは、製造業の課題を深く理解し、それに対する最適なデジタルソリューションを提供することで、企業が持続的な成長とイノベーションを達成できるようサポートします。
オンライン講座
製造業、主に購買・調達部門にお勤めの方々に向けた情報を配信しております。
新任の方やベテランの方、管理職を対象とした幅広いコンテンツをご用意しております。
お問い合わせ
コストダウンが利益に直結する術だと理解していても、なかなか前に進めることができない状況。そんな時は、newjiのコストダウン自動化機能で大きく利益貢献しよう!
(Β版非公開)