- お役立ち記事
- How to achieve both quality control and procurement efficiency in the purchasing department
How to achieve both quality control and procurement efficiency in the purchasing department
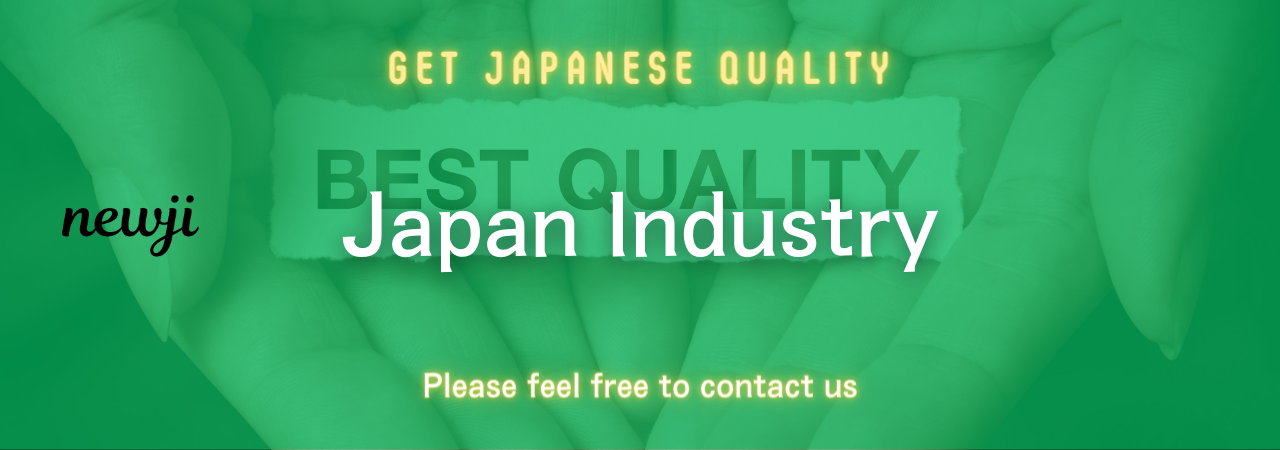
目次
Understanding the Importance of Quality Control and Procurement Efficiency
The purchasing department plays a crucial role in any organization by managing all aspects related to buying goods and services necessary for operations.
Achieving both quality control and procurement efficiency is vital because it ensures that the company can maintain its standards while also managing costs effectively.
Quality control in procurement involves ensuring that the products or services purchased meet the necessary standards and specifications.
This not only prevents defects and sub-par quality but also helps in maintaining the company’s reputation and customer satisfaction.
On the other hand, procurement efficiency focuses on streamlining the purchasing processes to save time and reduce costs, making sure that the organization operates smoothly and within budget.
Balancing these two aspects can be challenging but is essential for the long-term success of any business.
Steps to Improve Quality Control in Procurement
1. Set Clear Specifications
To begin with, it’s important to establish clear specifications for what you need to purchase.
This involves detailing the required quality, size, weight, design, and any other relevant features of the products or services you need.
Having precise specifications helps suppliers understand your expectations, reducing the chances of receiving substandard goods.
2. Supplier Assessment and Selection
Selecting the right suppliers is a critical step toward quality control.
Conduct thorough assessments of potential suppliers by evaluating their track records, certifications, and customer reviews.
Visiting their facilities, if possible, can also provide insights into their operations and quality assurance processes.
Choosing suppliers with strong quality control measures enhances the chances of receiving high-quality products.
3. Regular Audits and Inspections
Implementing a system for regular audits and inspections helps ensure that the suppliers maintain the quality standards over time.
Schedule regular visits to suppliers’ facilities and conduct random inspections on received goods.
This not only helps in identifying issues early but also keeps suppliers accountable for maintaining the desired quality.
4. Supplier Performance Monitoring
Continuously monitor the performance of your suppliers by keeping records of delivery times, quality of received goods, and responsiveness.
Use this data to evaluate whether suppliers are meeting your standards and expectations consistently.
Initiate corrective actions or reconsider your supplier options if you notice a persistent decline in quality.
Improving Procurement Efficiency
1. Automate Procurement Processes
Automating procurement processes can significantly improve efficiency by reducing manual tasks and minimizing the chances of human error.
Use procurement software to automate order processing, inventory management, and invoice processing.
This ensures faster transactions and provides better tracking of all procurement activities.
2. Centralize Procurement Functions
Centralizing procurement functions within your organization can lead to greater efficiency.
By consolidating purchasing efforts, you can leverage bulk purchasing power, negotiate better terms, and achieve economies of scale.
A centralized procurement team can also maintain a clearer overview of spending, helping in budget management.
3. Develop Strong Supplier Relationships
Build strong relationships with your suppliers to facilitate quicker negotiations and smoother transactions.
Good relationships with suppliers can lead to favorable terms, discounts, and prioritized service.
Regular communication and collaboration with your suppliers can further enhance procurement efficiency and quality management.
4. Implement Just-in-Time Purchasing
The Just-in-Time (JIT) purchasing strategy involves ordering goods only when they are needed for production or sales.
This minimizes excess inventory, reduces storage costs, and ensures that you have up-to-date products.
JIT requires precise demand forecasting but can enhance both efficiency and quality by reducing waste and obsolescence.
Balancing Quality Control and Procurement Efficiency
Finding the right balance between quality control and procurement efficiency requires strategic planning and continuous adaptation.
One way to achieve this is by developing a procurement strategy that aligns with your organization’s objectives.
Set priorities to focus on critical quality and efficiency goals, ensuring resources are allocated accordingly.
Regularly review and update the procurement process, incorporating feedback from internal stakeholders and suppliers.
Integrating technology is also key to balancing these aspects.
Use data analytics and reporting tools to gain insights into procurement operations, identify pain points, and make data-driven decisions.
Technology can help you streamline processes, track compliance, and maintain the standards necessary for quality control while boosting efficiency.
Training and development of the purchasing team play a crucial role in achieving this balance.
Equip your team with the skills needed to negotiate effectively, assess supplier capabilities, and utilize procurement software.
This fosters a culture of continuous improvement, where team members are encouraged to innovate and optimize purchasing activities.
Conclusion
Achieving both quality control and procurement efficiency in the purchasing department is essential for an organization’s success.
By implementing clear strategies for both improving quality and streamlining processes, businesses can not only cut costs and save time but also ensure they are delivering the best possible products and services to their customers.
Through supplier assessments, process automation, and strategic planning, you can create a seamless and effective procurement system that supports your organization’s goals.
Continuously monitoring and adapting these strategies will help maintain the crucial balance between maintaining high standards and achieving operational efficiencies.
資料ダウンロード
QCD調達購買管理クラウド「newji」は、調達購買部門で必要なQCD管理全てを備えた、現場特化型兼クラウド型の今世紀最高の購買管理システムとなります。
ユーザー登録
調達購買業務の効率化だけでなく、システムを導入することで、コスト削減や製品・資材のステータス可視化のほか、属人化していた購買情報の共有化による内部不正防止や統制にも役立ちます。
NEWJI DX
製造業に特化したデジタルトランスフォーメーション(DX)の実現を目指す請負開発型のコンサルティングサービスです。AI、iPaaS、および先端の技術を駆使して、製造プロセスの効率化、業務効率化、チームワーク強化、コスト削減、品質向上を実現します。このサービスは、製造業の課題を深く理解し、それに対する最適なデジタルソリューションを提供することで、企業が持続的な成長とイノベーションを達成できるようサポートします。
オンライン講座
製造業、主に購買・調達部門にお勤めの方々に向けた情報を配信しております。
新任の方やベテランの方、管理職を対象とした幅広いコンテンツをご用意しております。
お問い合わせ
コストダウンが利益に直結する術だと理解していても、なかなか前に進めることができない状況。そんな時は、newjiのコストダウン自動化機能で大きく利益貢献しよう!
(Β版非公開)