- お役立ち記事
- How to Achieve Cost Reduction and Efficiency by Shortening Molding Cycle Times
月間76,176名の
製造業ご担当者様が閲覧しています*
*2025年3月31日現在のGoogle Analyticsのデータより
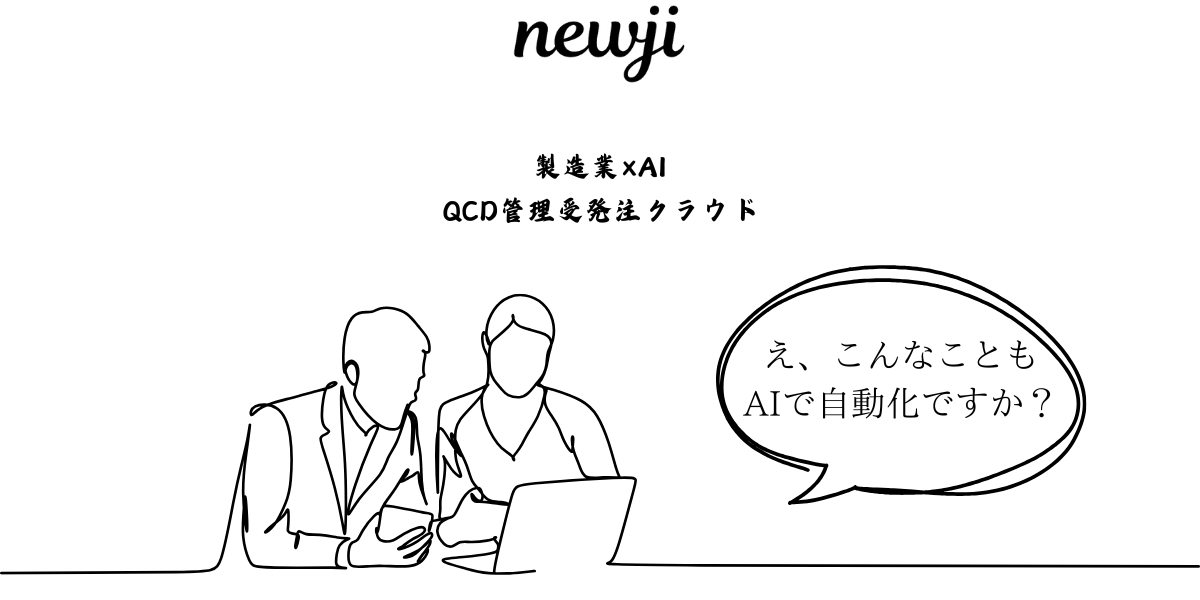
How to Achieve Cost Reduction and Efficiency by Shortening Molding Cycle Times
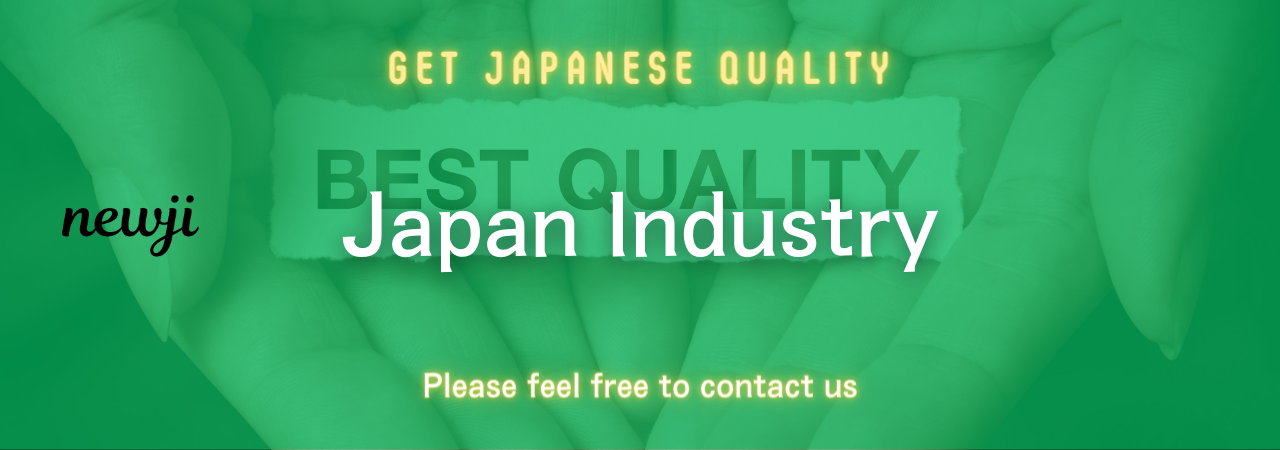
目次
Understanding Molding Cycle Times
The process of molding involves creating a specific shape from raw materials using molds.
This is essential in industries where precision and high volume are critical, such as in automotive, medical devices, and consumer goods.
Molding cycle time refers to the overall time taken to produce one cycle in the molding process, from mold closing to the ejection of the final product.
It’s an integral part of production as it directly affects the efficiency, costs, and productivity of the manufacturing process.
By focusing on reducing the molding cycle time, manufacturers can optimize production rates, lower energy consumption, and ultimately reduce operational costs.
Understanding the components of the cycle time and identifying areas of improvement can lead to significant cost savings and increased productivity.
Components of Molding Cycle Time
To shorten molding cycle times effectively, it is crucial to comprehend its various components, each contributing to the overall cycle time:
1. **Injection Time**: This is the period required to inject the material into the mold.
Factors influencing injection time include the viscosity of the material, injection speed, and pressure.
2. **Cooling Time**: Once the material is injected, it needs time to solidify and cool before the mold is opened.
Cooling time can be a significant portion of the cycle time, often taking up to 70% of it.
3. **Mold Clamping and Ejection Time**: This involves the time needed to open and close the mold and to eject the formed part.
Any inefficiency in this phase can elongate the cycle time unnecessarily.
4. **Handling Time**: It consists of any time lost between completing a cycle and starting the next one.
Streamlining this phase can significantly reduce cycle times overall.
Strategies for Reducing Molding Cycle Times
Here are key strategies to achieve cost reduction and efficiency by shortening molding cycle times:
1. Optimize Cooling Time
Cooling time is often one of the longest parts of the cycle, and thus optimizing it can lead to dramatic reductions in cycle time.
Consider these approaches:
– **Efficient Cooling Systems**: Implement advanced cooling technologies such as conformal cooling, which uses 3D-printed cooling channels that conform closely with the shape of the mold.
They offer consistent thermal regulation.
– **Material Selection**: Use materials with better thermal conductivity that cool faster, such as aluminum over steel, for molds.
– **Cycle Time Analysis**: Utilize software solutions that simulate the cooling phase to identify inefficiencies and optimize them before actual production.
2. Fast and Efficient Machine Clamping
Improving the speed and effectiveness of clamping and ejection procedures can significantly reduce cycle times:
– **Hydraulic Clamping Systems**: Use fast response hydraulic clamping systems that can reduce the time it takes to open and close the molds.
– **Ejection Enhancements**: Regularly maintain ejection systems to ensure they work smoothly and implement automatic ejection systems to quicken the process.
3. Streamlined Material Handling
The time taken to handle materials between cycles can often be reduced with streamlined processes:
– **Automation**: Implement robotic systems to handle parts between mold cycles, minimizing human intervention and potential delays.
– **Efficient Workflow Design**: Design smart workflows that minimize the distance and time it takes for raw materials and finished products to be transferred within the facility.
4. Optimize Material Selection and Preparation
Choosing the right material and preparing it effectively can also reduce cycle times:
– **Quality Materials**: Use high-quality materials that process more predictably and require less adjustment during the injection phase.
– **Pre-heating Materials**: For certain types of plastics, pre-heating can reduce viscosity and improve flow rates, leading to faster injection times.
Benefits of Shortening Molding Cycle Times
Shortening the molding cycle time brings several benefits that can transform manufacturing operations:
– **Cost Reduction**: Faster cycle times mean less energy is required per part, leading to decreased utility costs.
Additionally, more parts are produced in the same timeframe, lowering per-unit costs.
– **Increased Efficiency and Productivity**: More output in the same period boosts productivity without the need for additional resources, allowing companies to fulfill orders quickly.
– **Improved Product Quality**: Consistent cycle times and optimized processes can reduce defects, leading to higher quality products and less waste.
– **Competitive Advantage**: With reduced costs and improved delivery times, businesses can offer competitive pricing and better customer satisfaction.
In Conclusion
Shortening molding cycle times is a strategic move to enhance manufacturing efficiency and cost-effectiveness.
By focusing on areas such as cooling time, machine clamping, and material handling, improvements can be made that not only reduce cycle times but also improve overall production outcomes.
Implementing these strategies can lead to significant competitive advantages, offering companies the ability to produce high-quality products efficiently and economically.
資料ダウンロード
QCD管理受発注クラウド「newji」は、受発注部門で必要なQCD管理全てを備えた、現場特化型兼クラウド型の今世紀最高の受発注管理システムとなります。
ユーザー登録
受発注業務の効率化だけでなく、システムを導入することで、コスト削減や製品・資材のステータス可視化のほか、属人化していた受発注情報の共有化による内部不正防止や統制にも役立ちます。
NEWJI DX
製造業に特化したデジタルトランスフォーメーション(DX)の実現を目指す請負開発型のコンサルティングサービスです。AI、iPaaS、および先端の技術を駆使して、製造プロセスの効率化、業務効率化、チームワーク強化、コスト削減、品質向上を実現します。このサービスは、製造業の課題を深く理解し、それに対する最適なデジタルソリューションを提供することで、企業が持続的な成長とイノベーションを達成できるようサポートします。
製造業ニュース解説
製造業、主に購買・調達部門にお勤めの方々に向けた情報を配信しております。
新任の方やベテランの方、管理職を対象とした幅広いコンテンツをご用意しております。
お問い合わせ
コストダウンが利益に直結する術だと理解していても、なかなか前に進めることができない状況。そんな時は、newjiのコストダウン自動化機能で大きく利益貢献しよう!
(β版非公開)