- お役立ち記事
- How to Achieve Cost Reduction and Quality Improvement in Manufacturing Using QFD
月間76,176名の
製造業ご担当者様が閲覧しています*
*2025年3月31日現在のGoogle Analyticsのデータより
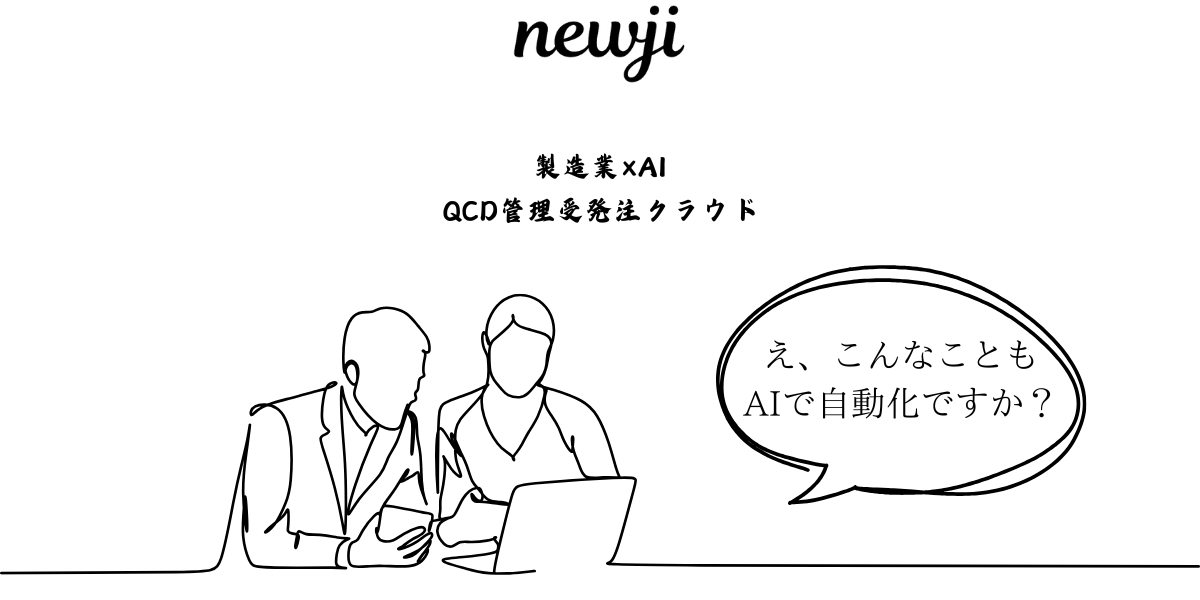
How to Achieve Cost Reduction and Quality Improvement in Manufacturing Using QFD
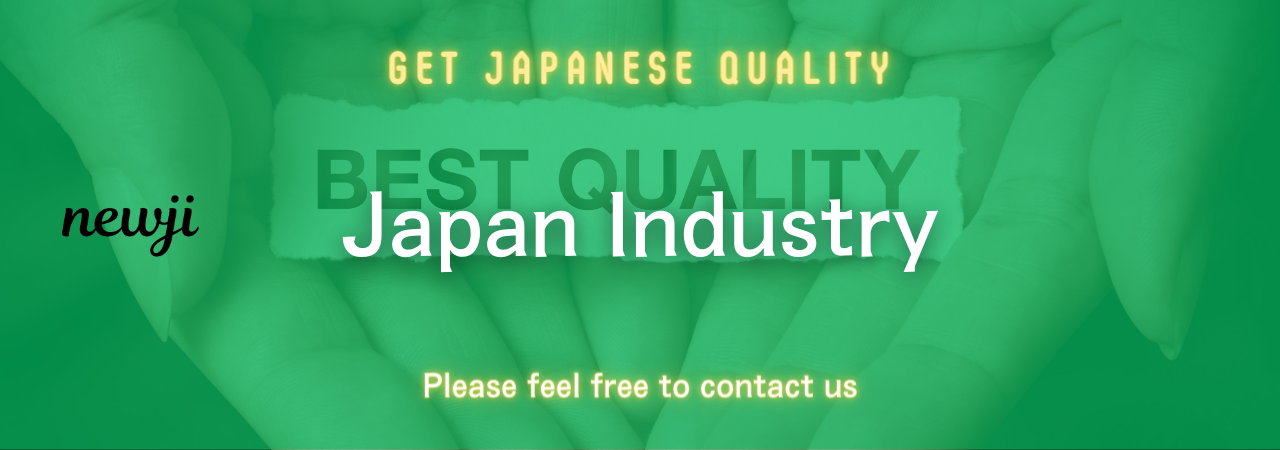
In today’s competitive market, manufacturers face immense pressure to produce high-quality products while keeping costs low.
One effective method for achieving both cost reduction and quality improvement is using Quality Function Deployment (QFD).
This methodology helps to transform customer requirements into detailed engineering specifications, ensuring that products meet or exceed customer expectations.
Let’s dive into how QFD can facilitate these objectives.
目次
Understanding Quality Function Deployment (QFD)
QFD is a systematic approach to product design and development that emphasizes understanding customer needs and translating them into specific technical requirements.
Originally developed in Japan in the late 1960s, QFD has become a global standard for ensuring product quality and customer satisfaction.
The method involves creating a series of matrices that link customer needs to engineering characteristics, production processes, and quality control measures.
The House of Quality
The House of Quality is the cornerstone of QFD.
It is the first matrix in the QFD process and serves as a visual map that helps teams understand the relationship between customer requirements and engineering design.
The matrix resembles a house, which is why it gets its name.
By filling out this “house,” teams can identify areas where improvements are needed and opportunities for cost reduction.
Steps to Implement QFD in Manufacturing
Identify Customer Needs
The first step in implementing QFD is to gather information about what customers want.
This can be done through market research, surveys, focus groups, or direct feedback.
The goal is to compile a comprehensive list of customer requirements, sometimes referred to as the “Voice of the Customer” (VOC).
Translate Customer Needs into Technical Requirements
Once customer needs are identified, the next step is to translate these needs into specific technical requirements.
This is where the House of Quality comes into play.
For example, if customers want a durable product, the technical requirement might be to use high-strength materials.
Prioritize Requirements
Not all customer requirements are equally important.
The next step is prioritizing these requirements based on factors like customer importance, competitive benchmarking, and feasibility.
This prioritization helps focus efforts on the most critical aspects, ensuring that resources are used effectively to meet the highest-priority needs.
Develop Solutions
After prioritizing requirements, the team can brainstorm and develop solutions to meet these needs.
This may involve selecting appropriate materials, designing specific features, or improving manufacturing processes.
At this stage, cross-functional teams, including design, engineering, and production, work together to create feasible solutions.
Validate and Test
Before full-scale production, it’s essential to validate and test the proposed solutions.
Prototypes and pilot runs can help identify potential issues and areas for further improvement.
These tests ensure that the final product meets the customer requirements and quality standards.
Benefits of Using QFD in Manufacturing
Enhanced Customer Satisfaction
By focusing on customer needs from the very beginning, QFD ensures that the final product aligns with customer expectations.
This leads to higher customer satisfaction and loyalty, which are crucial for long-term business success.
Cost Reduction
One of the primary goals of QFD is to identify and eliminate unnecessary costs.
By focusing on critical customer requirements, manufacturers can avoid over-engineering and reduce material and production costs.
Additionally, early identification of potential issues minimizes costly revisions and rework.
Improved Quality
QFD places a strong emphasis on quality by ensuring that customer requirements are met through rigorous planning and testing.
This systematic approach reduces the likelihood of defects and improves overall product quality.
As a result, manufacturers can achieve higher reliability and fewer returns or complaints.
Streamlined Communication
QFD fosters collaboration and communication among cross-functional teams.
By involving all relevant parties, from design to production, the process ensures that everyone is on the same page.
This alignment reduces misunderstandings and enhances overall efficiency.
Competitive Advantage
Manufacturers that employ QFD can differentiate themselves from competitors by consistently delivering high-quality products that meet customer needs.
This competitive advantage can lead to increased market share and profitability.
Challenges and Considerations
Complexity
Implementing QFD can be complex, especially for organizations that are new to the methodology.
It requires a deep understanding of customer needs and technical expertise to translate these needs into actionable requirements.
Time and Resources
The initial setup and implementation of QFD can be time-consuming and resource-intensive.
It involves extensive data collection, analysis, and collaboration, which may require additional investment and training.
Continuous Improvement
QFD is not a one-time exercise but a continuous process of improvement.
Manufacturers must regularly update and refine their QFD matrices to adapt to changing customer needs and market conditions.
Conclusion
Quality Function Deployment (QFD) offers a structured and effective approach for manufacturers aiming to achieve cost reduction and quality improvement.
By aligning product design and development with customer needs, QFD ensures that the final product meets or exceeds expectations.
While implementing QFD can be complex and resource-intensive, the benefits, including enhanced customer satisfaction, cost savings, improved quality, and a competitive advantage, far outweigh the challenges.
Manufacturers willing to invest in QFD will find themselves better positioned to succeed in an increasingly competitive marketplace.
資料ダウンロード
QCD管理受発注クラウド「newji」は、受発注部門で必要なQCD管理全てを備えた、現場特化型兼クラウド型の今世紀最高の受発注管理システムとなります。
ユーザー登録
受発注業務の効率化だけでなく、システムを導入することで、コスト削減や製品・資材のステータス可視化のほか、属人化していた受発注情報の共有化による内部不正防止や統制にも役立ちます。
NEWJI DX
製造業に特化したデジタルトランスフォーメーション(DX)の実現を目指す請負開発型のコンサルティングサービスです。AI、iPaaS、および先端の技術を駆使して、製造プロセスの効率化、業務効率化、チームワーク強化、コスト削減、品質向上を実現します。このサービスは、製造業の課題を深く理解し、それに対する最適なデジタルソリューションを提供することで、企業が持続的な成長とイノベーションを達成できるようサポートします。
製造業ニュース解説
製造業、主に購買・調達部門にお勤めの方々に向けた情報を配信しております。
新任の方やベテランの方、管理職を対象とした幅広いコンテンツをご用意しております。
お問い合わせ
コストダウンが利益に直結する術だと理解していても、なかなか前に進めることができない状況。そんな時は、newjiのコストダウン自動化機能で大きく利益貢献しよう!
(β版非公開)