- お役立ち記事
- How to adjust the production line due to supplier changes Why the purchasing department should cooperate with the production site
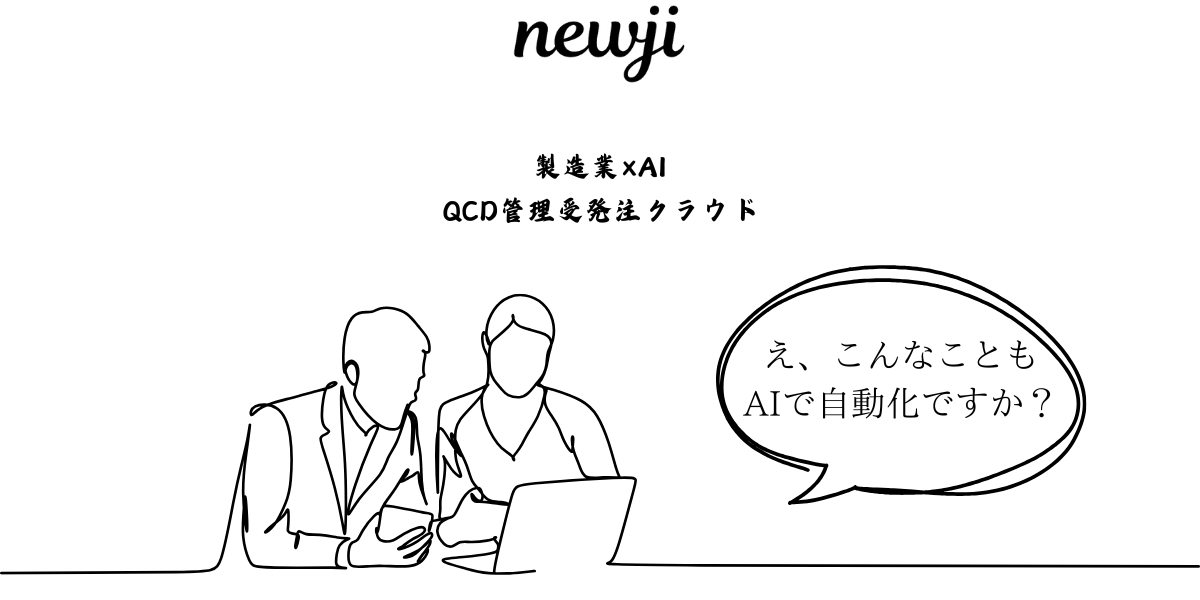
How to adjust the production line due to supplier changes Why the purchasing department should cooperate with the production site
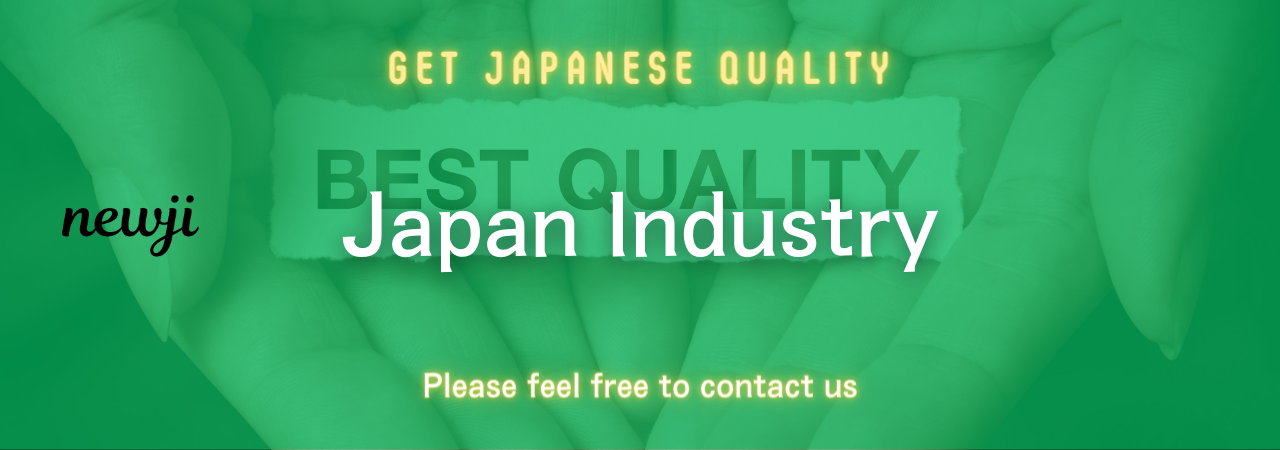
目次
Introduction
In the dynamic world of manufacturing, changes are inevitable.
One significant change that can disrupt operations is a shift in suppliers.
Such changes necessitate adjustments in the production line to ensure seamless operations and maintain product quality.
This process requires close cooperation between the purchasing department and the production site.
Understanding the reasons for and methods of adjusting the production line due to supplier changes can minimize disruptions and enhance efficiency.
Why Supplier Changes Occur
Changes in suppliers can result from various reasons.
These may include a search for cost efficiency, better quality materials, improved delivery times, or sustainability concerns.
Sometimes, a supplier may no longer be able to meet the company’s needs due to capacity issues or changes in their business direction.
Whatever the reason, the ability to adapt to these changes swiftly is crucial for maintaining smooth production operations.
The Importance of Collaboration
Effective cooperation between the purchasing department and the production site is vital when adjusting the production line.
Both departments have unique insights and expertise, making collaboration essential for successful transitions.
The purchasing department provides valuable information about new suppliers, such as raw material specifications and lead times.
Meanwhile, the production team understands the nuances of the manufacturing process and the impact of material changes on production lines.
Shared Objectives
Collaborating ensures that both departments are aligned with shared objectives.
The primary goal is to ensure that any supplier changes do not negatively impact production or product quality.
By working together, they can identify potential issues early and devise strategies to address them.
Assessing the Impact of Supplier Changes
Before making any adjustments, it’s crucial to assess how a supplier change will impact the production line.
This requires a detailed analysis of the differences between the current and new suppliers.
Factors such as material properties, availability, and consistency must be considered.
This assessment helps determine if modifications are needed in the production process.
Quality Control
One of the most critical areas to evaluate is quality control.
Different suppliers might have variations in how they produce materials, affecting the end product’s quality.
Regular testing and quality checks need to be implemented to ensure the new materials meet the required standards.
Production Timelines
Another key aspect is the impact on production timelines.
New suppliers may have different lead times or availability schedules.
Collaborating on schedule adjustments and managing inventory levels can help maintain continuous production flow.
Strategies for Adjusting the Production Line
Once the impact is assessed and understood, practical strategies can be employed to adjust the production line effectively.
Process Adjustments
Reviewing and potentially altering the existing production processes is crucial.
This may involve recalibrating equipment, updating standard operating procedures, or training staff on new techniques.
Conducting trial runs with the new materials can be beneficial to ensure compatibility and performance.
Inventory Management
Effective inventory management plays a critical role in easing the transition.
Having a buffer stock of old materials allows for a gradual shift to new materials without halting production.
This strategy also provides a safety net in case of unexpected delays from new suppliers.
Supplier Relationship Building
Establishing strong relationships with new suppliers can facilitate smoother adjustments.
Open communication and setting clear expectations regarding quality and delivery can prevent misunderstandings.
Collaborating closely with suppliers can also lead to improved outcomes and potential innovations in product development.
Conclusion
Adjusting the production line due to supplier changes is a complex but manageable process.
With thorough assessment, effective collaboration between the purchasing department and production site, and strategic adjustments, the transition can be smooth and beneficial.
The key is to remain proactive, communicate openly, and focus on shared objectives.
By prioritizing these elements, companies can enhance their adaptability and resilience in the ever-evolving manufacturing landscape.
資料ダウンロード
QCD調達購買管理クラウド「newji」は、調達購買部門で必要なQCD管理全てを備えた、現場特化型兼クラウド型の今世紀最高の購買管理システムとなります。
ユーザー登録
調達購買業務の効率化だけでなく、システムを導入することで、コスト削減や製品・資材のステータス可視化のほか、属人化していた購買情報の共有化による内部不正防止や統制にも役立ちます。
NEWJI DX
製造業に特化したデジタルトランスフォーメーション(DX)の実現を目指す請負開発型のコンサルティングサービスです。AI、iPaaS、および先端の技術を駆使して、製造プロセスの効率化、業務効率化、チームワーク強化、コスト削減、品質向上を実現します。このサービスは、製造業の課題を深く理解し、それに対する最適なデジタルソリューションを提供することで、企業が持続的な成長とイノベーションを達成できるようサポートします。
オンライン講座
製造業、主に購買・調達部門にお勤めの方々に向けた情報を配信しております。
新任の方やベテランの方、管理職を対象とした幅広いコンテンツをご用意しております。
お問い合わせ
コストダウンが利益に直結する術だと理解していても、なかなか前に進めることができない状況。そんな時は、newjiのコストダウン自動化機能で大きく利益貢献しよう!
(Β版非公開)