- お役立ち記事
- How to approach environmentally friendly production in production line design
月間76,176名の
製造業ご担当者様が閲覧しています*
*2025年3月31日現在のGoogle Analyticsのデータより
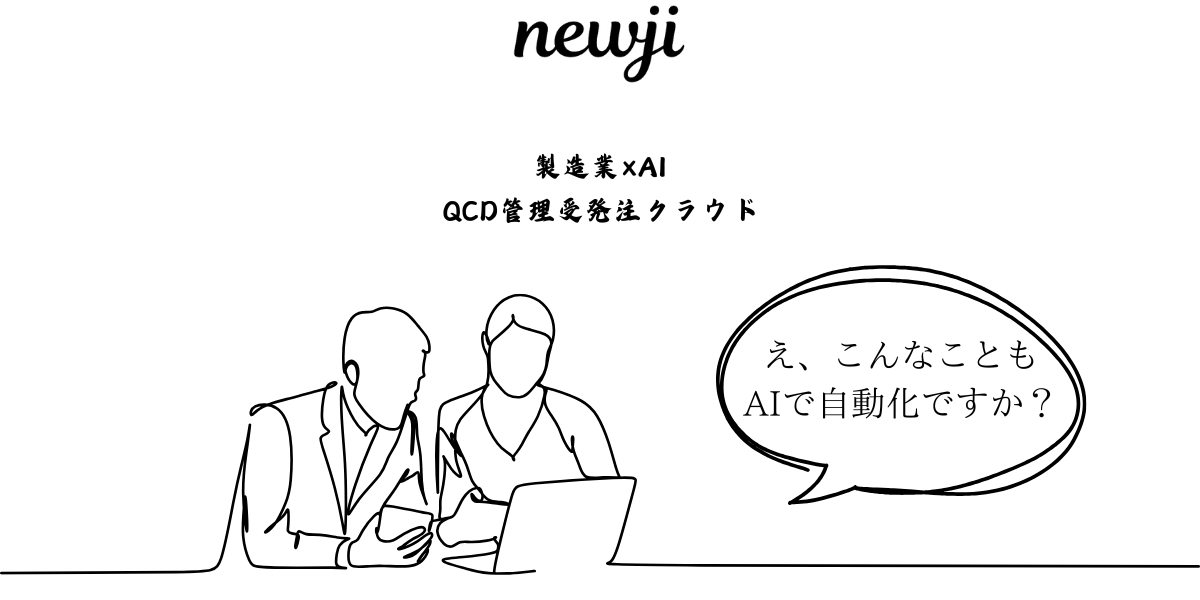
How to approach environmentally friendly production in production line design
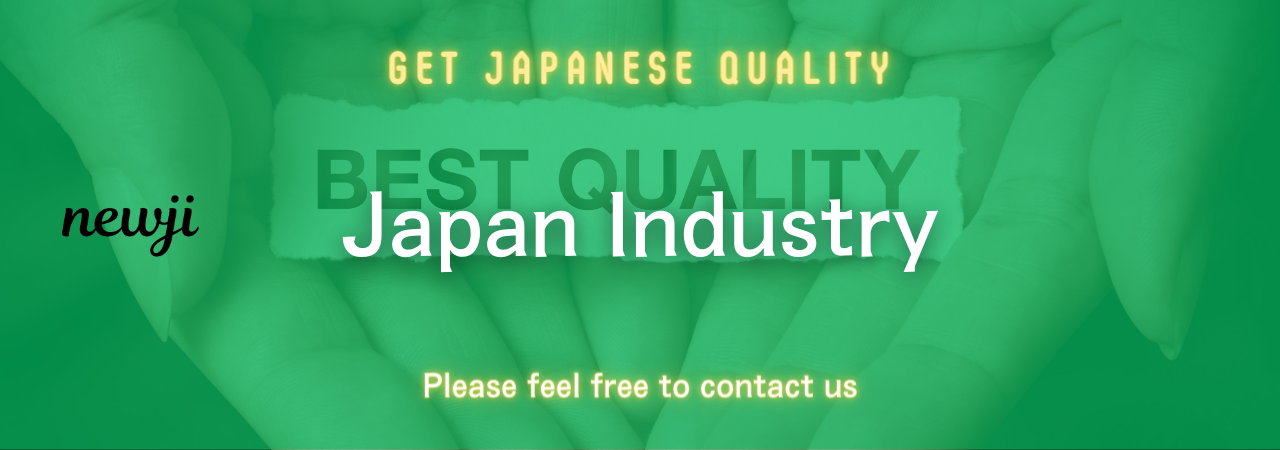
目次
Understanding Environmentally Friendly Production
When discussing production line design, it’s essential to incorporate environmentally friendly methods into the planning stages.
The focus on sustainability has never been more critical as industries strive to reduce their carbon footprint and minimize environmental impact.
But what does an environmentally friendly production line truly entail?
Environmentally friendly production involves the practice of designing manufacturing processes that reduce waste, conserve energy, and utilize eco-friendly materials.
It’s about creating a synergy between efficiency and sustainability.
By doing so, companies can not only contribute to environmental conservation but also enhance their brand image and potentially reduce costs over time.
Key Principles of Sustainable Production Line Design
To create a production line that aligns with sustainable practices, several core principles should be considered:
1. Reduce, Reuse, Recycle
The three R’s form the backbone of sustainable practices.
Reducing waste at every stage of the production line can be achieved through meticulous design and planning.
This includes minimizing excess materials and opting for durable packaging.
Reusing materials and components within the production cycle helps in conserving resources.
It’s worthwhile to explore ways to reuse byproducts of the manufacturing process in other areas.
Recycling should be implemented to ensure that materials aren’t wasted unnecessarily.
Setting up recycling stations and training staff on proper recycling methods can make a significant difference.
2. Energy Efficiency
Energy consumption is a critical factor in production line design.
Opting for energy-efficient machinery and equipment can substantially lower the environmental impact.
Incorporating energy-saving measures like automated power-down systems and energy-efficient lighting can also help.
Consider conducting regular energy audits to identify areas where improvements can be made.
This proactive approach ensures continuous enhancement in energy management.
3. Sustainable Materials
Choosing sustainable materials is a pivotal step toward green production.
This entails selecting materials that are biodegradable, renewable, or have a minimal environmental footprint.
When developing new products, prioritize those that can be produced using sustainable materials.
Partnership with suppliers who provide eco-friendly materials is also crucial.
Building a sustainable supply chain underpins the whole production process.
Incorporating Technology in Sustainable Production
1. Automation
Automation plays a crucial role in achieving environmentally friendly production.
Automated systems can optimize processes to enhance efficiency while minimizing waste.
Machines calibrated precisely reduce errors, thus conserving both materials and energy.
Additionally, automation can streamline processes and help manage waste more effectively, thus contributing to a decrease in emissions and other pollutants.
2. Monitoring Systems
Advanced monitoring systems are essential for tracking environmental metrics across the production line.
These systems can collect data on energy use, waste generation, and more.
By analyzing this data, adjustments can be made to improve sustainability.
Real-time feedback from monitoring systems allows for immediate corrective actions, optimizing environmental performance continually.
3. Digital Twins
Digital twin technology creates a virtual replica of the production line, allowing companies to simulate changes before implementing them physically.
This can help identify potential issues and test solutions without impacting the actual production process.
By using digital twins, companies can design more sustainable production lines and anticipate how changes will affect their environmental footprint.
Creating a Culture of Sustainability
For sustainability to thrive in production line design, it must be part of the company’s culture.
Employees at every level should be educated on the importance of sustainable practices and how they can contribute.
1. Training and Engagement
Providing training sessions and workshops on sustainability can foster an environment where employees feel empowered to contribute.
When employees understand the “why” behind certain practices, they’re more likely to comply and offer innovative solutions.
Engagement initiatives, such as green challenges or recognition programs, can motivate employees to champion sustainable practices.
2. Leadership Commitment
Leadership teams must be committed to driving sustainable changes.
Their commitment sets the overall tone and direction for the company.
By visibly supporting sustainable initiatives, leaders can encourage widespread adoption across the organization.
Benefits of Environmentally Friendly Production
Opting for environmentally friendly production isn’t just about compliance or brand image; it comes with tangible benefits:
1. Cost Savings
Although the initial transition might require an investment, sustainable practices often lead to cost savings.
Reducing energy usage and minimizing waste contribute directly to lowering operational expenses.
2. Enhanced Brand Image
Companies that adopt sustainable practices often enjoy an improved reputation.
Consumers increasingly favor brands that demonstrate a genuine commitment to environmental responsibility.
Hence, sustainability can be a significant differentiator in the marketplace.
3. Innovation and Growth
The move toward environmentally friendly production can spur innovation.
It can lead to the development of new, sustainable products and open up new markets.
Businesses at the forefront of sustainability often set industry standards and drive progress in their sectors.
In conclusion, integrating environmentally friendly practices into production line design requires planning and commitment but brings substantial long-term benefits.
Through embracing sustainability, companies not only safeguard the planet but enhance their operational efficiency and market position.
資料ダウンロード
QCD管理受発注クラウド「newji」は、受発注部門で必要なQCD管理全てを備えた、現場特化型兼クラウド型の今世紀最高の受発注管理システムとなります。
ユーザー登録
受発注業務の効率化だけでなく、システムを導入することで、コスト削減や製品・資材のステータス可視化のほか、属人化していた受発注情報の共有化による内部不正防止や統制にも役立ちます。
NEWJI DX
製造業に特化したデジタルトランスフォーメーション(DX)の実現を目指す請負開発型のコンサルティングサービスです。AI、iPaaS、および先端の技術を駆使して、製造プロセスの効率化、業務効率化、チームワーク強化、コスト削減、品質向上を実現します。このサービスは、製造業の課題を深く理解し、それに対する最適なデジタルソリューションを提供することで、企業が持続的な成長とイノベーションを達成できるようサポートします。
製造業ニュース解説
製造業、主に購買・調達部門にお勤めの方々に向けた情報を配信しております。
新任の方やベテランの方、管理職を対象とした幅広いコンテンツをご用意しております。
お問い合わせ
コストダウンが利益に直結する術だと理解していても、なかなか前に進めることができない状況。そんな時は、newjiのコストダウン自動化機能で大きく利益貢献しよう!
(β版非公開)