- お役立ち記事
- How to choose a process analysis tool for the manufacturing industry to improve productivity
月間77,185名の
製造業ご担当者様が閲覧しています*
*2025年2月28日現在のGoogle Analyticsのデータより
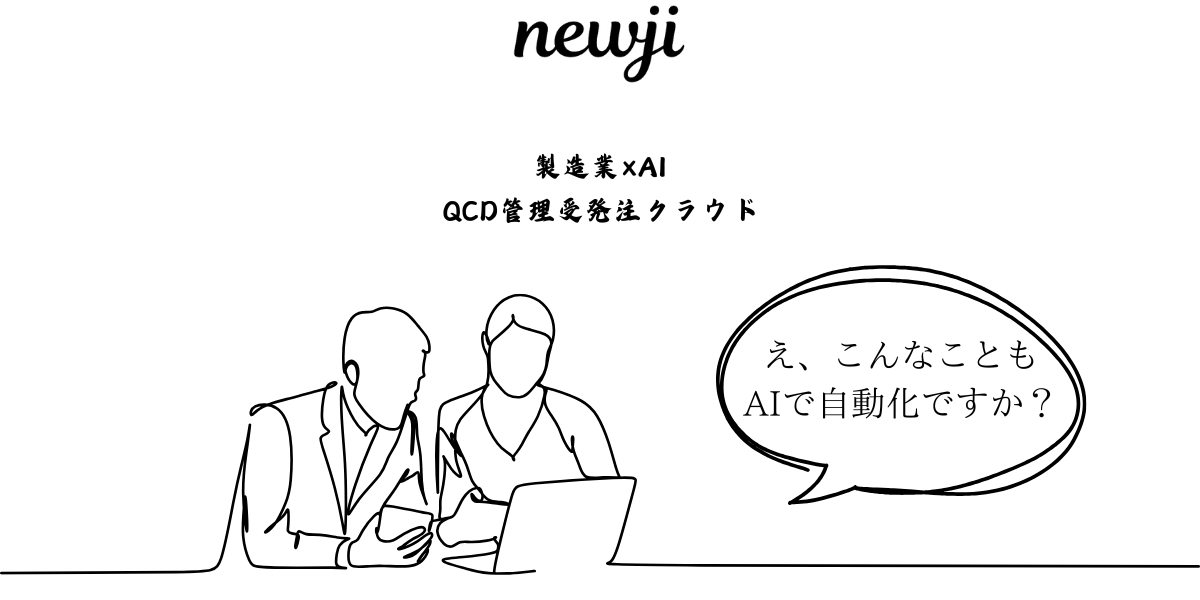
How to choose a process analysis tool for the manufacturing industry to improve productivity
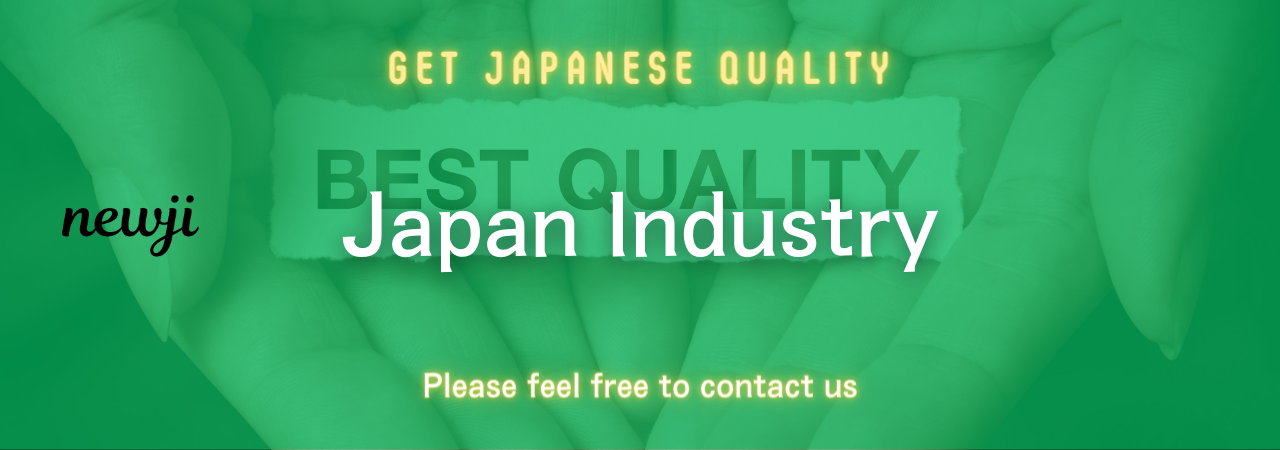
目次
Understanding Process Analysis Tools
The manufacturing industry is all about efficiency and productivity.
To stay competitive, it’s crucial to analyze existing processes and pinpoint areas for improvement.
That’s where process analysis tools come into play.
These tools help businesses understand and optimize their operations to enhance productivity and reduce waste.
Process analysis tools are designed to help you visualize, measure, and improve your manufacturing processes.
They allow you to identify bottlenecks, inefficiencies, and areas for cost reduction.
Choosing the right tool for your business is essential to boost productivity effectively.
Factors to Consider When Choosing a Process Analysis Tool
When selecting a process analysis tool, several factors must be considered.
By evaluating these aspects, you can ensure that the tool suits your manufacturing environment and addresses your specific needs.
1. User-Friendliness
One of the most important aspects is the tool’s user-friendliness.
A tool that is easy to navigate and understand will enable your team to use it efficiently.
Ideally, the tool should require minimal training and allow for intuitive usage.
A complicated tool can result in misinterpretations and wasted time.
2. Features and Functionality
Consider what specific features and functionalities are essential for your manufacturing processes.
Some tools offer a wide range of capabilities, such as data visualization, predictive analytics, or real-time monitoring.
Identify which features align with your organization’s goals and operational needs.
3. Integration Capabilities
A process analysis tool should easily integrate with your existing systems and machinery.
Compatibility with enterprise resource planning (ERP) systems, production management software, and other related technologies is crucial.
Integration ensures seamless data flow across systems, which enhances accuracy and efficiency.
4. Cost and Budget
Budget is always a critical consideration.
While the most expensive tool might offer extensive features, it may not be necessary for your operations.
Evaluate the cost against the expected return on investment.
It’s vital to balance functionality with affordability.
5. Scalability
As your business grows, so will your operational needs.
The tool you select should be scalable and adaptable to accommodate the changing demands of your manufacturing processes.
Scalability ensures the tool remains relevant and valuable over time.
6. Customer Support and Training
Reliable customer support and comprehensive training resources are essential.
These services can dramatically reduce downtime and troubleshoot any issues that may arise.
Evaluate the support structure offered by the vendor to ensure that assistance is readily available when needed.
Popular Process Analysis Tools for Manufacturing
Several process analysis tools are popular among manufacturing enterprises for their effectiveness and efficiency.
Here’s an overview of some widely-used tools:
1. Six Sigma Software
Six Sigma tools are geared towards improving process quality and reducing variation.
With techniques like DMAIC (Define, Measure, Analyze, Improve, Control) and DFSS (Design for Six Sigma), companies can achieve optimized processes.
Six Sigma software is particularly beneficial for those focused on quality control and process excellence.
2. Lean Manufacturing Software
Lean manufacturing tools prioritize waste elimination and enhancing process flow.
By focusing on value-added activities, lean software helps streamline processes.
This is ideal for businesses looking to eliminate unnecessary steps and improve production efficiency.
3. Value Stream Mapping (VSM) Software
Value Stream Mapping is a visualization tool that outlines the steps involved in manufacturing a product.
It helps identify inefficiencies and opportunities for improvement in the production flow.
VSM software is excellent for companies aiming to improve workflow and reduce lead times.
4. Overall Equipment Effectiveness (OEE) Tools
OEE tools measure the efficiency of manufacturing processes by evaluating availability, performance, and quality.
These metrics help identify areas for improvement and track the effectiveness of implemented changes.
OEE analysis is critical for maximizing production efficiency.
Steps for Implementing a Process Analysis Tool
Implementing a process analysis tool requires a strategic approach.
Here are the steps to ensure successful integration:
1. Define Objectives
Clearly outline the goals you wish to achieve with the tool.
Having well-defined objectives will guide the selection process and measure the tool’s effectiveness post-implementation.
2. Involve Key Stakeholders
Engage team members from different departments in the selection process.
Their input is valuable in identifying essential features and ensuring the tool meets cross-functional needs.
3. Test the Tool
Whenever possible, conduct a trial run or demo of the tool.
This will give you insights into its usability, compatibility, and overall value.
4. Train Your Team
Provide comprehensive training for your team on how to use the tool.
Proper training minimizes errors and ensures your team can leverage the tool to its fullest potential.
5. Monitor and Improve
Once implemented, continuously monitor the tool’s impact on your processes.
Gather feedback and make necessary adjustments to optimize its effectiveness over time.
Conclusion
Selecting the right process analysis tool for the manufacturing industry is crucial for improving productivity and competitiveness.
By considering factors such as user-friendliness, features, integration capabilities, and cost, you can choose a tool that aligns with your operational requirements.
Remember that successful implementation goes beyond choosing the right tool; it involves defining clear objectives, engaging stakeholders, and providing adequate training.
With the proper process analysis tool in place, manufacturers can streamline processes, reduce waste, and ultimately increase overall productivity.
資料ダウンロード
QCD管理受発注クラウド「newji」は、受発注部門で必要なQCD管理全てを備えた、現場特化型兼クラウド型の今世紀最高の受発注管理システムとなります。
ユーザー登録
受発注業務の効率化だけでなく、システムを導入することで、コスト削減や製品・資材のステータス可視化のほか、属人化していた受発注情報の共有化による内部不正防止や統制にも役立ちます。
NEWJI DX
製造業に特化したデジタルトランスフォーメーション(DX)の実現を目指す請負開発型のコンサルティングサービスです。AI、iPaaS、および先端の技術を駆使して、製造プロセスの効率化、業務効率化、チームワーク強化、コスト削減、品質向上を実現します。このサービスは、製造業の課題を深く理解し、それに対する最適なデジタルソリューションを提供することで、企業が持続的な成長とイノベーションを達成できるようサポートします。
製造業ニュース解説
製造業、主に購買・調達部門にお勤めの方々に向けた情報を配信しております。
新任の方やベテランの方、管理職を対象とした幅広いコンテンツをご用意しております。
お問い合わせ
コストダウンが利益に直結する術だと理解していても、なかなか前に進めることができない状況。そんな時は、newjiのコストダウン自動化機能で大きく利益貢献しよう!
(β版非公開)