- お役立ち記事
- How to choose a project management tool to accelerate digitalization in manufacturing
月間77,185名の
製造業ご担当者様が閲覧しています*
*2025年2月28日現在のGoogle Analyticsのデータより
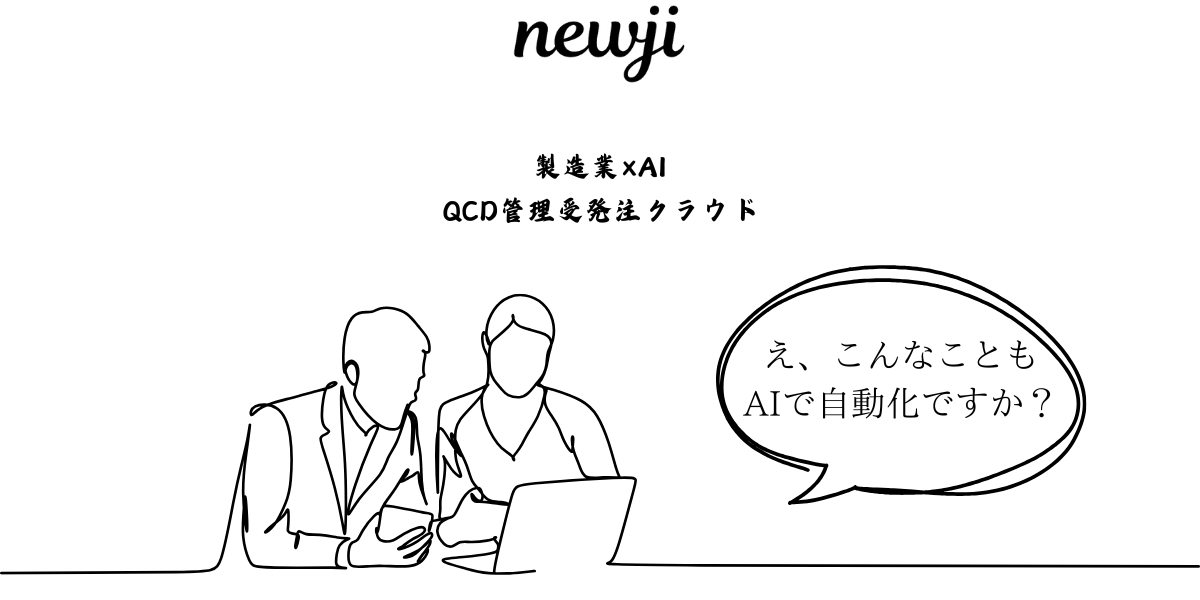
How to choose a project management tool to accelerate digitalization in manufacturing
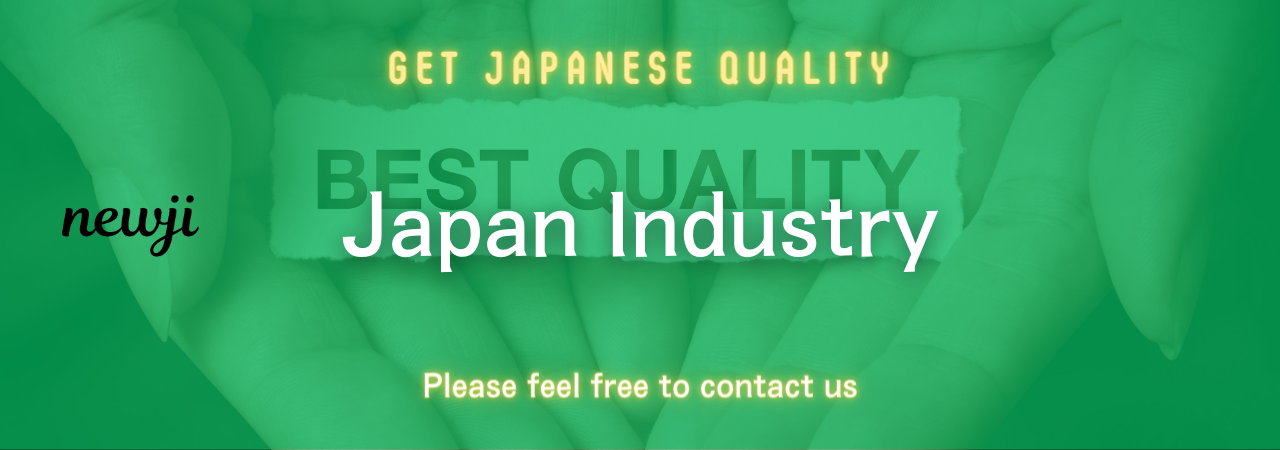
目次
Introduction to Project Management Tools
The manufacturing industry is undergoing a significant transformation with the advent of digitalization.
Key to this transformation is the effective management of projects, which involves planning, executing, and overseeing various tasks.
For a manufacturing company aiming to enhance its processes through digital means, selecting the right project management tool is crucial.
This tool will not only help in streamlining operations but also in bringing together all aspects of a project seamlessly.
Understanding Digitalization in Manufacturing
Digitalization in manufacturing involves the integration of digital technologies into every facet of the production process.
It aims to improve efficiency, quality, and flexibility in manufacturing operations.
Technologies such as the Internet of Things (IoT), artificial intelligence (AI), and big data analytics are revolutionizing the way products are designed, produced, and delivered.
To leverage these technologies, manufacturers need sophisticated tools that support project management and ensure that all departments are aligned and working towards common goals.
Importance of Project Management Tools
Project management tools are essential for coordinating tasks, timelines, and resources.
They allow team members to collaborate effectively, track progress, and make informed decisions based on real-time data.
In a digitalized manufacturing environment, these tools ensure that digital initiatives are implemented smoothly.
They facilitate communication across departments and help manage the complexities associated with digital transformation projects.
Key Features to Look for in a Project Management Tool
When selecting a project management tool for your manufacturing company, several features are vital:
1. Customization and Scalability
A tool should allow customization to fit the unique needs of your organization.
As your company grows and your processes evolve, the tool should gracefully scale with those changes.
2. Integration Capabilities
The ability to integrate smoothly with existing systems like ERP, CRM, and other manufacturing-specific software is crucial.
This integration ensures that information flows seamlessly across systems, providing a unified view of the project status.
3. Real-Time Analytics and Reporting
Having access to real-time data and analytics helps managers make quick, informed decisions.
The tool should provide comprehensive reporting features, allowing users to generate various reports with ease.
4. User-Friendly Interface
The easier a tool is to use, the faster team members will adopt it.
A user-friendly interface with intuitive navigation and clear instructions promotes efficient use and reduces the training time required.
5. Collaboration Tools
Modern project management tools should facilitate team communication and collaboration.
Features such as chat, file sharing, and task comments enhance teamwork, even if team members are scattered across different locations.
6. Security and Compliance
Considering the sensitivity of manufacturing data, the tool should have robust security measures.
It must comply with industry standards and regulations to protect proprietary and customer information.
Steps to Choose the Right Project Management Tool
1. Define Your Requirements
Start by identifying the specific needs and challenges your manufacturing business faces.
Consider what functions the project management tool must perform and what goals it should help achieve.
2. Research and Compare Tools
Look into various project management tools available in the market.
Compare their features, user reviews, customer support, and pricing models to narrow down your options.
3. Take Advantage of Free Trials
Most software providers offer free trials or demos.
Use this opportunity to test the tools, involving potential users to gather feedback on usability and features.
4. Evaluate Integration Ease
Ensure that the tool can be easily integrated with your current systems.
Check for available APIs and third-party compatibility to make integration straightforward.
5. Assess Long-Term Costs
Consider the total cost of ownership, including subscription fees, implementation, training, and possible upgrades.
Balance cost with the value the tool provides in achieving digitalization goals.
6. Get Feedback from Stakeholders
Involve key stakeholders in the decision-making process to ensure that the tool meets the needs of different departments.
Their input can highlight aspects you may have overlooked.
Conclusion
Choosing the right project management tool is a pivotal step in advancing your manufacturing firm’s digital transformation.
By focusing on features such as scalability, integration, and user-friendliness, you equip your team with the resources needed for success.
This decision not only supports efficient project execution but also enhances cross-functional collaboration, driving your organization toward its digitalization objectives.
Take the time to carefully evaluate options, involving stakeholders and leveraging resources wisely to ensure the choice aligns with your strategic vision.
資料ダウンロード
QCD管理受発注クラウド「newji」は、受発注部門で必要なQCD管理全てを備えた、現場特化型兼クラウド型の今世紀最高の受発注管理システムとなります。
ユーザー登録
受発注業務の効率化だけでなく、システムを導入することで、コスト削減や製品・資材のステータス可視化のほか、属人化していた受発注情報の共有化による内部不正防止や統制にも役立ちます。
NEWJI DX
製造業に特化したデジタルトランスフォーメーション(DX)の実現を目指す請負開発型のコンサルティングサービスです。AI、iPaaS、および先端の技術を駆使して、製造プロセスの効率化、業務効率化、チームワーク強化、コスト削減、品質向上を実現します。このサービスは、製造業の課題を深く理解し、それに対する最適なデジタルソリューションを提供することで、企業が持続的な成長とイノベーションを達成できるようサポートします。
製造業ニュース解説
製造業、主に購買・調達部門にお勤めの方々に向けた情報を配信しております。
新任の方やベテランの方、管理職を対象とした幅広いコンテンツをご用意しております。
お問い合わせ
コストダウンが利益に直結する術だと理解していても、なかなか前に進めることができない状況。そんな時は、newjiのコストダウン自動化機能で大きく利益貢献しよう!
(β版非公開)