- お役立ち記事
- How to Choose Measuring Equipment and Case Studies of Implementation
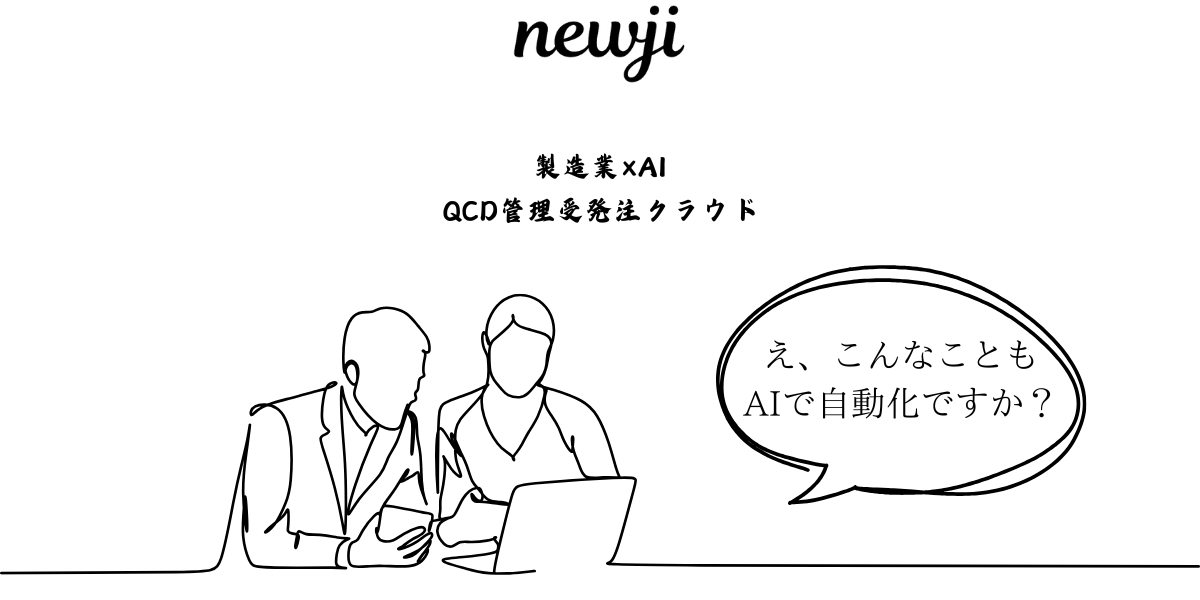
How to Choose Measuring Equipment and Case Studies of Implementation
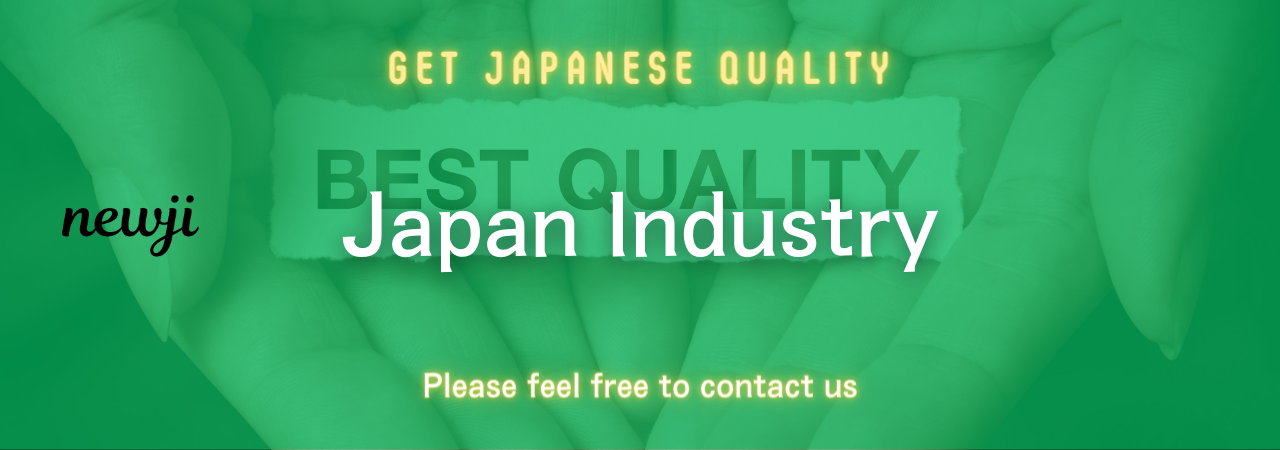
目次
Introduction
Choosing the right measuring equipment is crucial for ensuring accurate and efficient measurements in various applications.
Whether you are in manufacturing, research, or automotive industries, the correct tools can significantly impact your project’s success.
In this article, we will explore how to choose the right measuring equipment and share some case studies on their real-world implementations.
Understanding Your Requirements
Define the Purpose
First and foremost, determine the purpose of the measurement.
Are you looking to measure pressure, temperature, length, or something else?
Understanding what you need to measure helps narrow down the types of equipment suitable for the task.
Identify Measurement Range and Accuracy
It is essential to identify the range and accuracy you require.
For instance, if you need to measure small temperature variations, a highly accurate thermometer is necessary.
On the other hand, if you require large load measurements, you may need a different type of load cell.
Understand Environmental Conditions
Environmental conditions can significantly impact the performance of measuring equipment.
Consider factors such as humidity, temperature, and exposure to chemicals, as these can affect the equipment’s accuracy and lifespan.
Types of Measuring Equipment
Pressure Gauges
Pressure gauges are commonly used to measure the pressure of gases and liquids. There are various kinds, including mechanical, digital, and electrical pressure gauges.
Thermometers
Thermometers measure temperature and come in various forms, such as digital, infrared, and liquid-in-glass thermometers.
Calipers
Calipers are essential for measuring the distance between two opposite sides of an object. They are commonly used in manufacturing and mechanical engineering.
Load Cells
Load cells are transducers that convert a force into an electrical signal. They are widely used in weighing systems and industrial scales.
Factors to Consider When Choosing Measuring Equipment
Quality and Durability
Invest in high-quality, durable equipment, even if it means higher upfront costs.
Durable equipment typically provides more accurate and reliable measurements over time, reducing long-term costs.
Cost-Effectiveness
While it is essential to invest in quality, cost-effectiveness should also be considered.
Compare various brands and models within your budget to find the best fit that meets your needs without breaking the bank.
Ease of Use
Complex and hard-to-use equipment can lead to measurement errors and inefficiencies.
Choose tools that are user-friendly and come with proper instructions and support.
Compatibility
Ensure that the equipment is compatible with your existing systems or software.
Incompatibility can result in additional costs or even render the new equipment useless.
Case Studies: Real-World Implementations
Case Study 1: Digital Micrometers in Precision Engineering
A manufacturing firm specializing in precision engineering was facing challenges with their older measuring equipment.
They required high accuracy and repeatability to meet stringent quality standards.
The company decided to upgrade to digital micrometers.
These new devices offered improved accuracy and ease of use, resulting in fewer errors and higher productivity.
As a result, the firm saw a 20% increase in efficiency and a significant reduction in production costs.
Case Study 2: Wireless Temperature Sensors in Food Processing
A food processing plant had recurring issues with traditional thermometers.
The manual recording of temperatures was prone to errors and time-consuming.
By switching to wireless temperature sensors, the plant could automate the monitoring process.
These sensors provided real-time data to a centralized system, allowing for more effective quality control.
The plant experienced a 15% reduction in spoilage, improving overall profitability.
Case Study 3: Load Cells in Logistics
A logistics company was looking to improve its weight measurement processes for better inventory management.
Traditional scales were not providing the necessary accuracy for high-value items.
The company implemented load cells integrated with its inventory software.
This change allowed for more precise measurements and real-time inventory updates.
The logistics company reported a 25% increase in accuracy, leading to better resource allocation and customer satisfaction.
Case Study 4: Laser Distance Meters in Construction
A construction company handling large-scale projects needed a solution for quick and accurate distance measurements.
Traditional measuring tapes were not practical for the vast areas involved.
By adopting laser distance meters, the company could take measurements quickly and accurately.
The meters reduced the time and labor required for measurements by over 30%.
This improvement also enabled the project to stay on schedule and within budget.
Conclusion
Choosing the right measuring equipment is critical to the success of any project.
By understanding your specific requirements and considering factors such as quality, cost-effectiveness, ease of use, and compatibility, you can make informed decisions.
Real-world examples demonstrate that investing in the right equipment can lead to significant improvements in accuracy, efficiency, and overall productivity.
Whether you are in manufacturing, food processing, logistics, or construction, selecting the right tools can make all the difference. Make thoughtful choices and enjoy the benefits of precise and reliable measurements.
資料ダウンロード
QCD調達購買管理クラウド「newji」は、調達購買部門で必要なQCD管理全てを備えた、現場特化型兼クラウド型の今世紀最高の購買管理システムとなります。
ユーザー登録
調達購買業務の効率化だけでなく、システムを導入することで、コスト削減や製品・資材のステータス可視化のほか、属人化していた購買情報の共有化による内部不正防止や統制にも役立ちます。
NEWJI DX
製造業に特化したデジタルトランスフォーメーション(DX)の実現を目指す請負開発型のコンサルティングサービスです。AI、iPaaS、および先端の技術を駆使して、製造プロセスの効率化、業務効率化、チームワーク強化、コスト削減、品質向上を実現します。このサービスは、製造業の課題を深く理解し、それに対する最適なデジタルソリューションを提供することで、企業が持続的な成長とイノベーションを達成できるようサポートします。
オンライン講座
製造業、主に購買・調達部門にお勤めの方々に向けた情報を配信しております。
新任の方やベテランの方、管理職を対象とした幅広いコンテンツをご用意しております。
お問い合わせ
コストダウンが利益に直結する術だと理解していても、なかなか前に進めることができない状況。そんな時は、newjiのコストダウン自動化機能で大きく利益貢献しよう!
(Β版非公開)