- お役立ち記事
- How to choose work efficiency tools for the manufacturing industry to improve productivity
月間76,176名の
製造業ご担当者様が閲覧しています*
*2025年3月31日現在のGoogle Analyticsのデータより
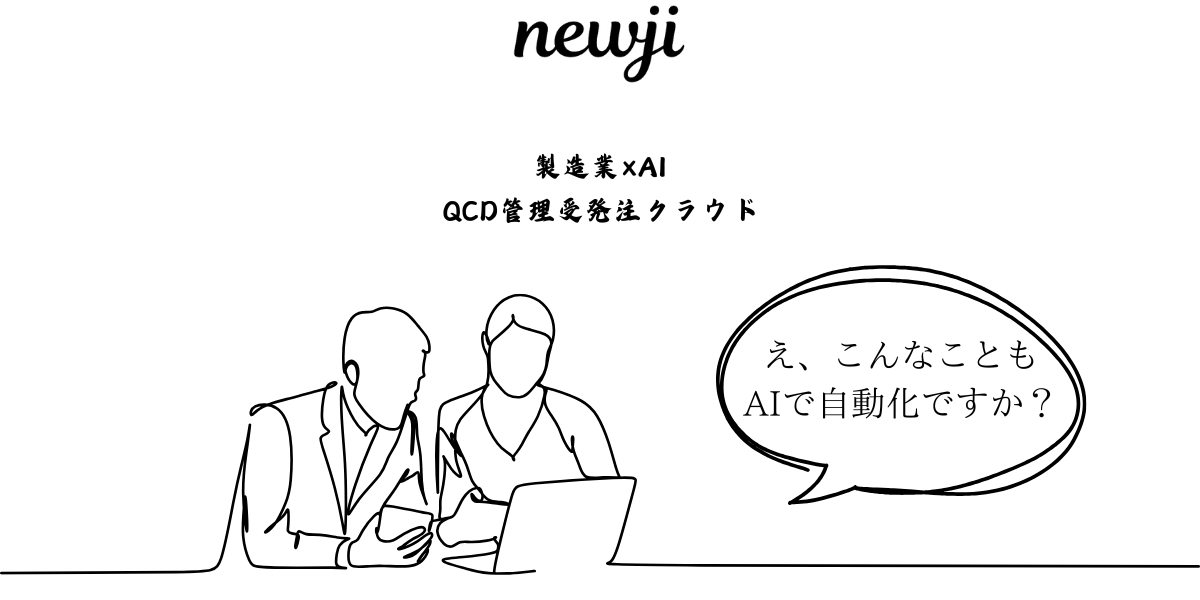
How to choose work efficiency tools for the manufacturing industry to improve productivity
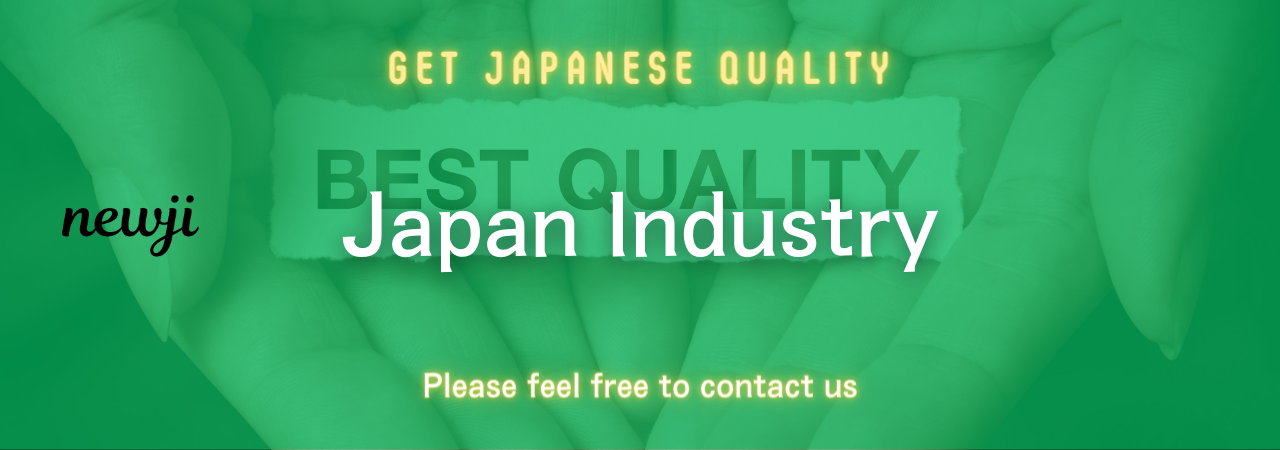
目次
Understanding Work Efficiency Tools in the Manufacturing Industry
In today’s fast-paced manufacturing industry, efficiency is key to staying competitive and ensuring high productivity levels.
To achieve this, businesses are increasingly turning to work efficiency tools that streamline operations and support workforce productivity.
However, selecting the right tools can be daunting, given the myriad of options available on the market.
In this guide, we’ll explore what to consider when choosing work efficiency tools tailored for the manufacturing industry.
Identify Your Manufacturing Needs
Before diving into the sea of available tools, it’s crucial to identify the specific needs of your manufacturing operations.
Begin by evaluating your current processes to determine where there might be bottlenecks or inefficiencies.
Consider factors like the complexity of tasks, the workflows involved, and any recurring challenges that hamper productivity.
By pinpointing these needs, you can target tools specifically designed to address those issues.
Consider the Size of Your Operation
The size of your manufacturing operation significantly influences the type of efficiency tools you need.
Small businesses might require solutions that are simpler and budget-friendly, while larger enterprises may benefit from more robust, scalable solutions.
Larger operations might also need more integration with existing systems to harmonize the workflow across departments.
Explore Different Types of Work Efficiency Tools
Once you’ve identified the needs of your manufacturing process, the next step is to explore the different types of tools available.
These tools generally fall into several categories, each serving a unique purpose in streamlining manufacturing operations.
Project Management Tools
Project management tools are vital for keeping track of manufacturing projects and ensuring tasks are completed on time.
These tools help manage schedules, allocate resources, and monitor progress.
Some popular project management tools include Trello, Asana, and Microsoft Project, which offer features like task assignments, timelines, and reporting.
Automation Software
Automation software is a game-changer for the manufacturing industry.
It helps automate repetitive tasks, reducing manual labor and minimizing errors.
Tools such as robotic process automation (RPA) can streamline production lines, while inventory management systems can automate stock control and order processing.
Enterprise Resource Planning (ERP) Systems
ERP systems are comprehensive solutions that integrate various business processes into a single platform.
These systems provide valuable insights into your manufacturing operations by consolidating data across departments.
Popular ERP systems like SAP, Oracle, and Microsoft Dynamics offer modules for financial management, production planning, and inventory control.
Communication and Collaboration Software
Effective communication is crucial in manufacturing, especially with teams operating in various locations or shifts.
Collaboration tools like Slack, Microsoft Teams, and Zoom facilitate real-time communication and support teamwork.
These tools enhance coordination and ensure that everyone stays informed about project updates and changes.
Assess the Features and Benefits
When evaluating work efficiency tools, it’s essential to look at the specific features each tool offers.
Consider how these features align with your manufacturing needs and whether they provide real benefits to your operations.
Scalability
Scalability is an important consideration, particularly for growing manufacturing businesses.
Choose tools that can grow with your operations, accommodating an increasing number of users, products, or production lines without sacrificing performance.
Ease of Use
The tools should be user-friendly and require minimal training for your staff.
An intuitive interface ensures that your team can quickly adapt and start using the tools effectively, reducing downtime and enhancing productivity.
Integration Capabilities
Manufacturing operations often require multiple tools to work in harmony.
Look for solutions that offer seamless integration with existing systems and software platforms used within your organization.
This interconnectedness can save time and minimize disruptions.
Data Security and Compliance
Data security is a top priority, especially when dealing with sensitive manufacturing data.
Ensure that the tools you choose comply with industry standards and regulations.
Check for features like data encryption, secure logins, and regular software updates to protect your information.
Evaluate Cost-Effectiveness
While considering work efficiency tools, cost is always a vital factor.
Analyze the costs involved in acquiring, implementing, and maintaining the tools.
Remember to balance the initial investment with the potential return on investment (ROI) gained through increased productivity and efficiency.
Subscription Models
Many tools offer subscription-based pricing models with flexible plans.
Determine whether a monthly or annual subscription best fits your budget and provides the necessary features.
Trial Periods and Demos
Take advantage of trial periods and demos to test the tools in a real-world setting.
This allows you to evaluate their functionality, ease of use, and impact on your manufacturing processes before committing to a purchase.
Implementation and Training
Once you’ve selected the ideal work efficiency tools, planning for implementation and training is the final crucial step.
Proper training ensures that your team fully understands how to leverage the tools to maximize productivity.
Create an Implementation Plan
Develop a detailed plan outlining how the tools will be integrated into your current processes.
Consider timelines, budgets, and resources needed for a smooth transition.
Invest in Training Programs
Provide comprehensive training programs for your staff to effectively use the new tools.
Training should cover all relevant features and best practices, ensuring that your team feels confident and empowered.
By following these guidelines, you’ll be well-equipped to choose the right work efficiency tools for your manufacturing operations, ultimately boosting productivity and maintaining a competitive edge in the industry.
資料ダウンロード
QCD管理受発注クラウド「newji」は、受発注部門で必要なQCD管理全てを備えた、現場特化型兼クラウド型の今世紀最高の受発注管理システムとなります。
ユーザー登録
受発注業務の効率化だけでなく、システムを導入することで、コスト削減や製品・資材のステータス可視化のほか、属人化していた受発注情報の共有化による内部不正防止や統制にも役立ちます。
NEWJI DX
製造業に特化したデジタルトランスフォーメーション(DX)の実現を目指す請負開発型のコンサルティングサービスです。AI、iPaaS、および先端の技術を駆使して、製造プロセスの効率化、業務効率化、チームワーク強化、コスト削減、品質向上を実現します。このサービスは、製造業の課題を深く理解し、それに対する最適なデジタルソリューションを提供することで、企業が持続的な成長とイノベーションを達成できるようサポートします。
製造業ニュース解説
製造業、主に購買・調達部門にお勤めの方々に向けた情報を配信しております。
新任の方やベテランの方、管理職を対象とした幅広いコンテンツをご用意しております。
お問い合わせ
コストダウンが利益に直結する術だと理解していても、なかなか前に進めることができない状況。そんな時は、newjiのコストダウン自動化機能で大きく利益貢献しよう!
(β版非公開)