- お役立ち記事
- How to collaborate with suppliers to achieve cost reduction and quality assurance at the same time
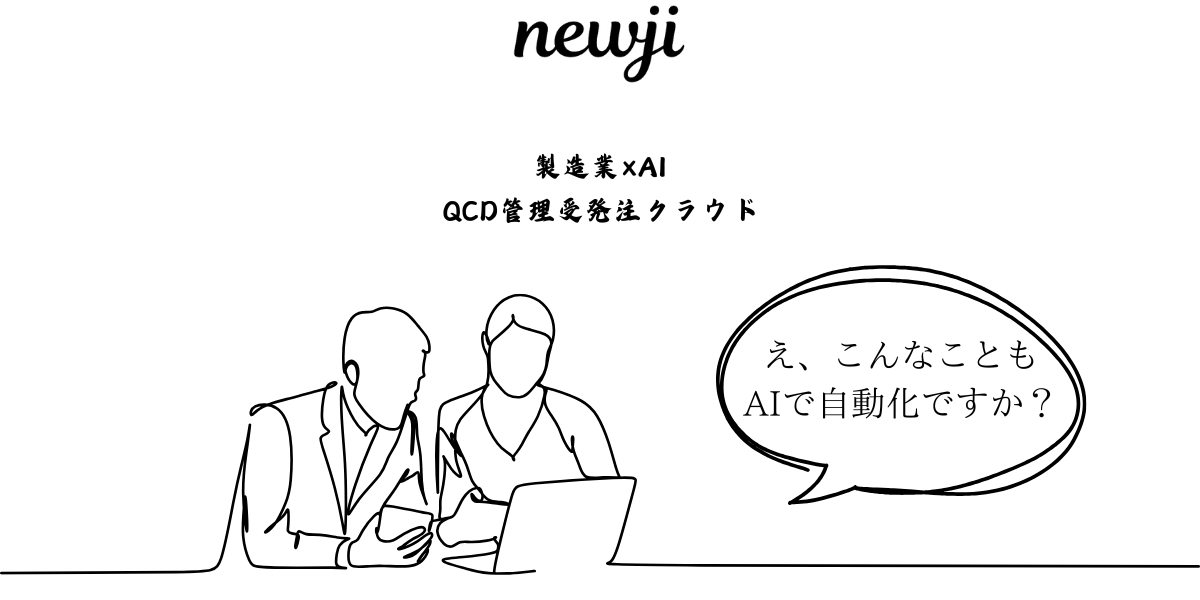
How to collaborate with suppliers to achieve cost reduction and quality assurance at the same time
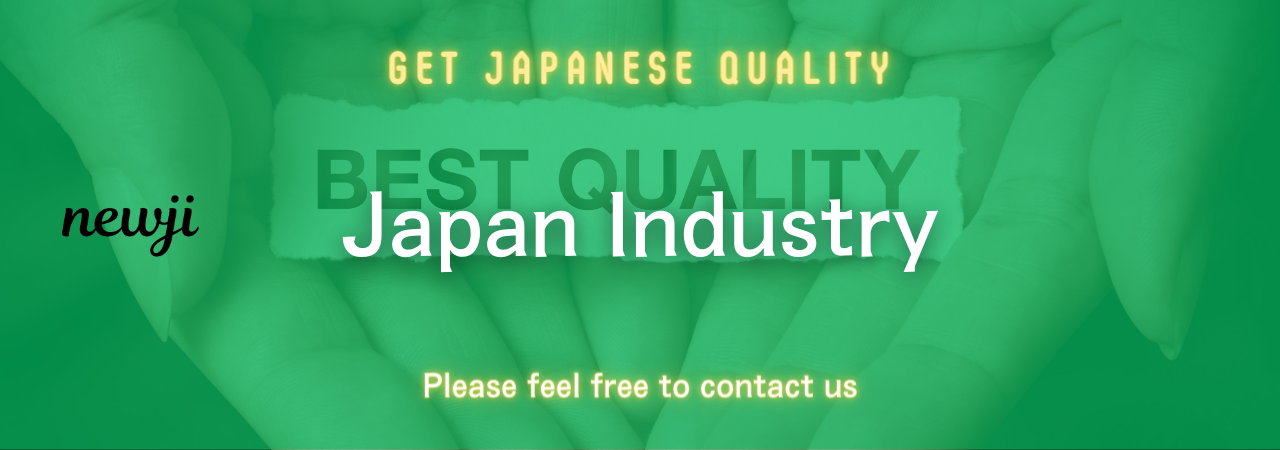
目次
Understanding Supplier Collaboration
Collaborating effectively with suppliers is a strategic move that can lead to both cost reduction and quality assurance.
This partnership goes beyond mere transactional interactions and involves engaging suppliers as integral parts of the supply chain.
The essence of effective collaboration lies in building a relationship hallmarked by trust, transparency, and shared goals.
Recognizing each other’s strengths and nurturing a mutual understanding lays the foundation for a successful partnership.
Establish Clear Communication Channels
Clear and consistent communication is vital for any collaboration to thrive.
Creating open lines where information flows seamlessly between your company and your suppliers can significantly enhance efficiency.
Regular meetings and updates help ensure that all stakeholders are aligned and working towards common objectives.
Utilizing technology, such as communication platforms and collaborative software, can facilitate smoother interactions and enable real-time information sharing.
Set Expectations and Goals
When collaborating with suppliers, it’s imperative to set clear expectations and define measurable goals at the outset.
These expectations should include quality standards, delivery timelines, and cost targets.
By establishing what success looks like for both parties, you can create accountability and maintain focus on the desired outcomes.
Regular evaluations against these benchmarks ensure that the collaboration remains on track.
Leverage Data and Insights
Data-driven decision-making is crucial in optimizing supplier collaborations.
By analyzing supply chain data, businesses can identify areas for improvement and anticipate potential issues.
Shared data analytics enable both parties to gain insights into production capabilities, inventory levels, and demand forecasts.
This information allows for proactive adjustments, which can lead to cost savings and improved quality control.
Implement Continuous Improvement Practices
Continuous improvement is a cornerstone of long-term collaboration success.
Encouraging a culture of learning and adaptation can drive innovation within the supply chain.
Through techniques such as regular audits and process evaluations, both businesses and suppliers can identify inefficiencies and work together to resolve them.
This approach not only enhances product quality but also uncovers opportunities for cost reductions.
Negotiate Collaborative Agreements
Traditional supplier agreements often focus solely on price points and delivery terms.
Collaborative agreements, however, consider broader aspects like quality agreements and long-term partnership benefits.
When negotiating, emphasize mutual advantages, such as volume discounts or joint investment in technology advancements.
Such agreements foster a shared commitment to achieving both quality and cost objectives.
Engage in Joint Problem Solving
Problems in the supply chain can sometimes be unavoidable; how they are addressed marks the difference.
Engaging in joint problem-solving with suppliers means tackling issues as a team, without the blame game.
This cooperative approach leverages both companies’ expertise to find effective solutions quickly.
It also strengthens the partnership by illustrating commitment to mutual support and improvement.
Invest in Supplier Development
An investment in a supplier’s capabilities can pay dividends in terms of improved product quality and reduced costs.
Supplier development initiatives, such as training programs or technology investments, can enhance efficiency and reliability.
By guiding suppliers in adopting industry best practices or new technological tools, you potentially boost their performance, benefiting your supply chain.
Monitor and Evaluate Supplier Performance
Regularly monitoring supplier performance is crucial to ensuring that the collaboration produces desired results.
Implement performance metrics to assess areas like defect rates, delivery punctuality, and cost variance.
Sharing this feedback with suppliers allows them to understand your priorities and identify areas for improvement.
Periodic performance reviews foster a culture of accountability and continuous enhancement.
Foster a Culture of Trust
The bedrock of effective supplier collaboration is trust, cultivated through shared success and transparent interactions.
Building trust involves consistent, fair dealings where both parties honor commitments and respect mutual benefits.
When suppliers trust that you value their contributions and interest genuinely in their success, they are more likely to invest in the partnership.
This trust leads to a smoother collaboration, paving the way for both cost savings and quality assurance.
Encourage Innovation and Flexibility
Encouraging innovation from suppliers can lead to cost savings and higher quality outputs.
Invite suppliers to bring forward new ideas or technological advancements that can benefit your operations.
Flexible collaborations allow for quick adaptations to market changes or unforeseen circumstances, preserving both quality and cost-effectiveness.
By fostering an environment where innovation is welcome, suppliers become proactive partners in enhancing product value.
In conclusion, a strategic and harmonious collaboration with suppliers can achieve both cost reduction and quality assurance concurrently.
By building a strong foundation based on communication, trust, and shared objectives, businesses can transform supplier relationships into robust partnerships that drive mutual success.
Always seek constant improvement and innovation in your supply chain to maintain a competitive edge in the industry.
資料ダウンロード
QCD調達購買管理クラウド「newji」は、調達購買部門で必要なQCD管理全てを備えた、現場特化型兼クラウド型の今世紀最高の購買管理システムとなります。
ユーザー登録
調達購買業務の効率化だけでなく、システムを導入することで、コスト削減や製品・資材のステータス可視化のほか、属人化していた購買情報の共有化による内部不正防止や統制にも役立ちます。
NEWJI DX
製造業に特化したデジタルトランスフォーメーション(DX)の実現を目指す請負開発型のコンサルティングサービスです。AI、iPaaS、および先端の技術を駆使して、製造プロセスの効率化、業務効率化、チームワーク強化、コスト削減、品質向上を実現します。このサービスは、製造業の課題を深く理解し、それに対する最適なデジタルソリューションを提供することで、企業が持続的な成長とイノベーションを達成できるようサポートします。
オンライン講座
製造業、主に購買・調達部門にお勤めの方々に向けた情報を配信しております。
新任の方やベテランの方、管理職を対象とした幅広いコンテンツをご用意しております。
お問い合わせ
コストダウンが利益に直結する術だと理解していても、なかなか前に進めることができない状況。そんな時は、newjiのコストダウン自動化機能で大きく利益貢献しよう!
(Β版非公開)