- お役立ち記事
- How to comply with safety standards when procuring specific parts for the defense industry
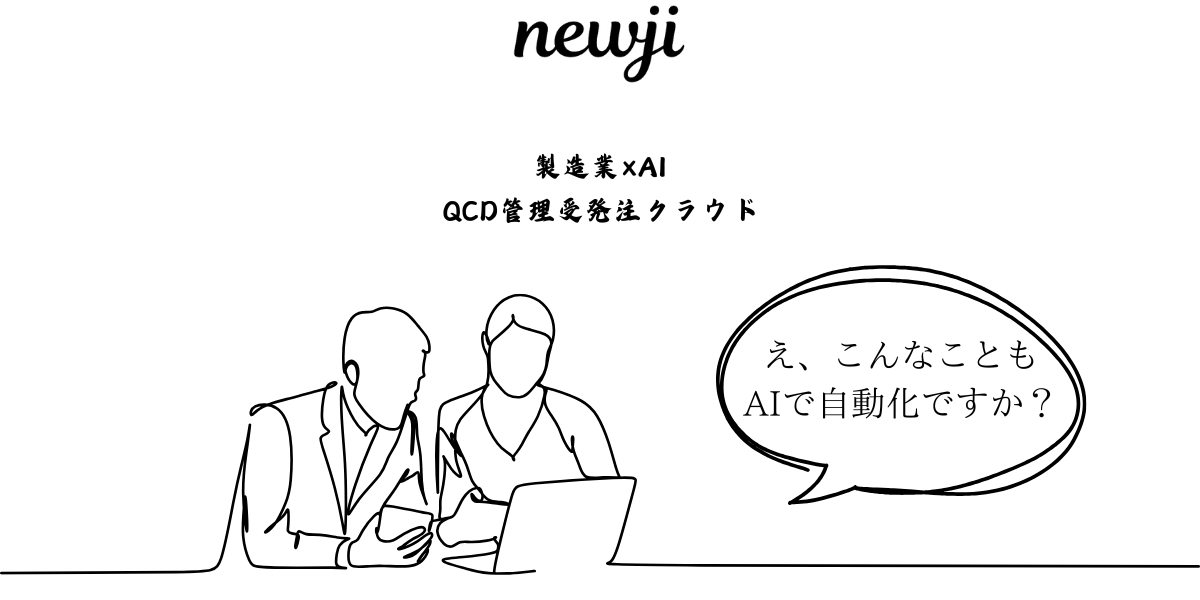
How to comply with safety standards when procuring specific parts for the defense industry
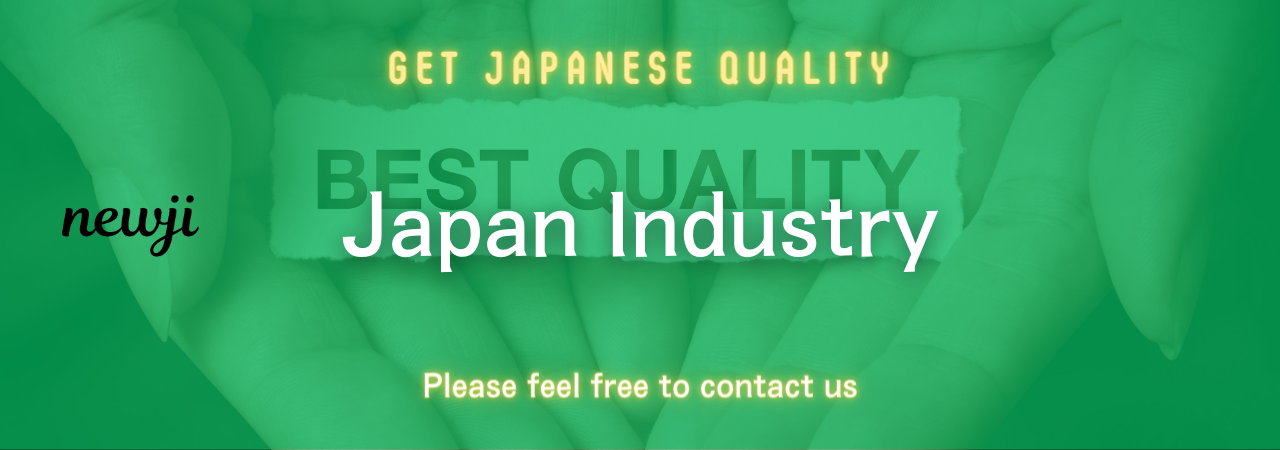
目次
Understanding Safety Standards in the Defense Industry
Procurement in the defense industry is a complex task that goes beyond mere purchasing.
There are stringent safety standards that must be adhered to, ensuring that all parts and components are reliable, safe, and effective for military applications.
Familiarizing yourself with these standards is crucial for maintaining compliance and ensuring the safety and security of defense operations.
Why Safety Standards Are Critical
Safety standards in the defense industry are essential for several reasons.
Firstly, they ensure the reliability and durability of parts under extreme conditions.
Military equipment often operates in harsh environments, where failure could lead to catastrophic consequences.
Therefore, each part must meet rigorous criteria to function correctly.
Safety standards also protect both military personnel and civilians.
Defective equipment can endanger lives, making it vital to maintain strict adherence to safety protocols.
Furthermore, compliance with safety standards helps prevent costly recalls and repairs, keeping projects within budget and on schedule.
Key Safety Standards in Defense Procurement
ISO Standards
The International Organization for Standardization (ISO) provides numerous standards that apply to defense procurement.
These standards cover various aspects, from quality management (ISO 9001) to environmental management systems (ISO 14001).
By complying with ISO standards, defense contractors ensure that their products meet global quality and safety benchmarks.
AS9100 Series
The AS9100 series is a widely recognized quality management standard specifically tailored for the aerospace and defense industries.
It incorporates ISO 9001 principles while adding additional regulations specific to aerospace and defense.
Adhering to AS9100 ensures that parts are manufactured consistently and reliably, reducing the risk of defects.
Military Standards (MIL-STD)
Military standards, known as MIL-STDs, are specifications set forth by the Department of Defense.
These standards define the processes and manufacturing practices needed to ensure products are suitable for military use.
MIL-STDs cover a wide range of requirements, including performance, testing, and evaluation, ensuring components can withstand military environments.
Steps to Ensure Compliance with Safety Standards
Conduct Thorough Research
Before procuring any specific parts, it’s paramount to conduct in-depth research into the applicable safety standards.
This includes reviewing the necessary ISO, AS9100, and MIL-STDs related to the parts you are acquiring.
Understanding these standards in detail will help identify the critical requirements for compliance.
Select Reputable Suppliers
Choosing the right supplier is an integral part of ensuring compliance.
Work with suppliers who have a proven track record in the defense industry and who are certified according to relevant standards.
Request documentation of their compliance and quality management systems to verify their credibility.
Implement Rigorous Testing and Inspection
Testing and inspection are crucial to validating that parts meet safety standards.
Establish a comprehensive testing protocol that includes stress testing, environmental simulation, and performance checks.
Partner with accredited laboratories to ensure that testing procedures meet industry requirements and produce reliable results.
Maintain Accurate Documentation
Documentation plays a critical role in demonstrating compliance with safety standards.
Keep thorough records of all procurement processes, testing results, and supplier certifications.
Accurate documentation not only proves compliance but also provides a reference for future audits or inspections.
Continuous Training and Education
Keeping up with the latest developments in safety standards is essential.
Regularly train procurement and quality assurance teams on new standards and industry best practices.
Continuous education ensures that your team is well-equipped to handle evolving safety requirements and maintain compliance.
Overcoming Challenges in Defense Procurement
Navigating Complex Regulations
The defense industry is bound by a complex web of regulations and standards.
Staying updated with the latest changes and understanding how they apply to your procurement processes can be challenging.
Developing a dedicated compliance team can help navigate these complexities and ensure that all parts meet the necessary requirements.
Managing Supply Chain Risks
Supply chain disruptions can impact the availability of compliant parts.
To mitigate these risks, build strong relationships with multiple suppliers and maintain a buffer stock of critical components.
This proactive approach ensures continuity in procurement, even in the face of unforeseen challenges.
Balancing Cost and Compliance
Balancing the need for compliance with budget constraints is a common challenge.
Investing in quality parts and reputable suppliers may initially seem costly but can prevent expensive issues in the long run.
Evaluate the total cost of ownership and prioritize compliance to achieve long-term savings and reliability.
Conclusion
Complying with safety standards in the defense industry is a necessity rather than an option.
By understanding key standards, selecting reputable suppliers, and implementing rigorous testing protocols, organizations can ensure their procured parts meet the required safety and quality benchmarks.
Overcoming procurement challenges through thorough research, effective risk management, and continuous training establishes a robust foundation for a safe and efficient defense supply chain.
Emphasizing compliance not only enhances the safety and reliability of military equipment but also fortifies the integrity and reputation of defense operations.
資料ダウンロード
QCD調達購買管理クラウド「newji」は、調達購買部門で必要なQCD管理全てを備えた、現場特化型兼クラウド型の今世紀最高の購買管理システムとなります。
ユーザー登録
調達購買業務の効率化だけでなく、システムを導入することで、コスト削減や製品・資材のステータス可視化のほか、属人化していた購買情報の共有化による内部不正防止や統制にも役立ちます。
NEWJI DX
製造業に特化したデジタルトランスフォーメーション(DX)の実現を目指す請負開発型のコンサルティングサービスです。AI、iPaaS、および先端の技術を駆使して、製造プロセスの効率化、業務効率化、チームワーク強化、コスト削減、品質向上を実現します。このサービスは、製造業の課題を深く理解し、それに対する最適なデジタルソリューションを提供することで、企業が持続的な成長とイノベーションを達成できるようサポートします。
オンライン講座
製造業、主に購買・調達部門にお勤めの方々に向けた情報を配信しております。
新任の方やベテランの方、管理職を対象とした幅広いコンテンツをご用意しております。
お問い合わせ
コストダウンが利益に直結する術だと理解していても、なかなか前に進めることができない状況。そんな時は、newjiのコストダウン自動化機能で大きく利益貢献しよう!
(Β版非公開)