- お役立ち記事
- How to create an optimal ordering plan using “lead time analysis” for purchasing department leaders
How to create an optimal ordering plan using “lead time analysis” for purchasing department leaders
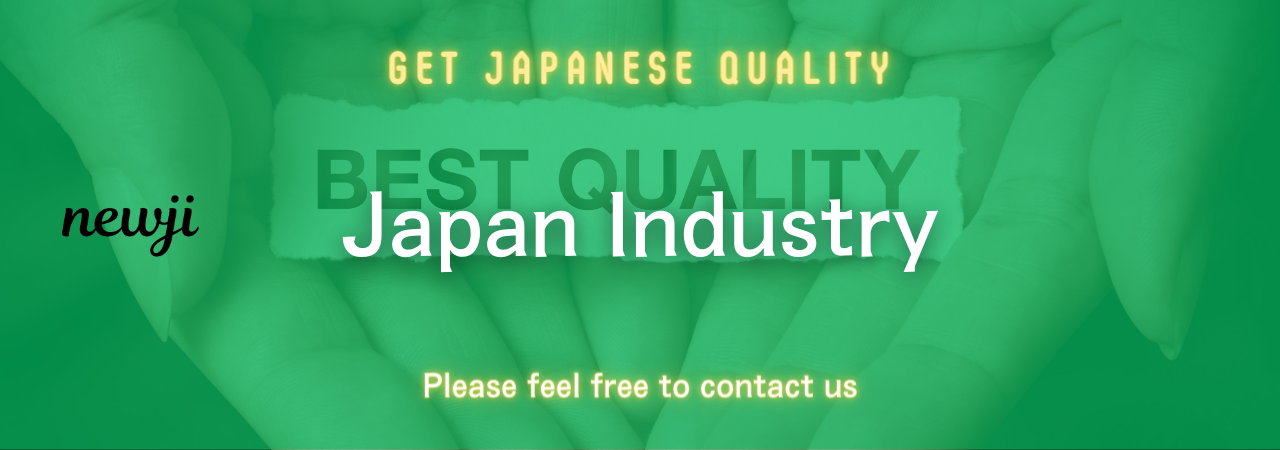
目次
Understanding Lead Time Analysis
Lead time analysis is a critical concept for purchasing department leaders who are tasked with ensuring that the right products are available when needed, without overstocking or understocking.
At its core, lead time refers to the time interval between the initiation of a purchasing order and the delivery of the product.
By understanding and analyzing lead times, purchasing departments can optimize their ordering plans, thereby improving efficiency and reducing costs.
It’s important to meticulously track and analyze the time it takes for suppliers to fulfill orders.
This includes the time taken for order processing, manufacturing, and shipping.
Investing in thorough lead time analysis helps in predicting future delays and adjusting orders accordingly.
Importance of Lead Time Analysis
Effective lead time analysis enables purchasing departments to maintain a perfect balance between supply and demand.
It plays a vital role in inventory management by avoiding excess inventory that can lead to wastage or shortages that can halt operations.
For purchasing managers, reduced lead times often lead to reduced holding costs, translating into significant financial savings.
When you optimize lead time, you also improve customer satisfaction by ensuring a steady supply of goods.
This is particularly important in industries where time-to-market is a major competitive advantage.
Steps to Conduct Lead Time Analysis
To perform lead time analysis effectively, purchasing leaders should follow a structured approach:
1. **Collect Data:** Gather historical data on order times, fulfillment times, and any delays encountered.
2. **Identify Variability:** Analyze the collected data to identify any patterns or inconsistencies in lead times.
3. **Evaluate Supplier Performance:** Assess the reliability and efficiency of your suppliers.
4. **Use Technology:** Employ analytical tools and software that can assist in real-time tracking and forecasting.
5. **Review Regularly:** Lead time analysis is not a one-off exercise and should be reviewed regularly to reflect any changes in supplier efficiency or process improvements.
Factors Affecting Lead Time
Several factors can affect the lead time in procurement processes, and it’s crucial to consider each to optimize ordering plans:
– **Supplier Capability:** The potential of a supplier to deliver goods on time without compromising quality is essential.
– **Manufacturing Processes:** Complex or outdated manufacturing processes might delay production, increasing lead time.
– **Transportation and Logistics:** Distance, transportation mode, and customs can greatly impact lead time.
– **Order Quantity:** Large order volumes often require more time to fulfill, while smaller orders might be processed faster.
– **Communication:** Delays in communication between buyers and suppliers can add to lead time.
Strategies to Reduce Lead Time
Reducing lead time can significantly enhance a purchasing department’s efficiency.
Here are some strategies to consider:
1. **Build Strong Supplier Relationships:** Establishing strong relationships ensures better collaboration and coordination with suppliers.
2. **Optimize Inventory Levels:** Use historical data to forecast demand accurately and maintain optimal inventory levels.
3. **Implement Technology Solutions:** Adopt solutions like ERP systems to streamline operations and improve transparency.
4. **Negotiate Better Terms:** Work with suppliers to negotiate better terms that include reduced lead times.
5. **Regular Supplier Evaluation:** Conduct regular performance evaluations to ensure suppliers meet expectations consistently.
Building an Optimal Ordering Plan
An optimal ordering plan involves strategic decision-making that aligns purchasing activities with business objectives.
Here are the key components:
– **Accurate Demand Forecasting:** Leverage analytical tools for precise demand predictions to avoid over or under stocking.
– **Effective Communication Channels:** Ensure seamless communication with suppliers and stakeholders to avoid misalignments.
– **Continuous Improvement:** Regularly review and refine purchasing processes for maximum efficiency and effectiveness.
– **Risk Management:** Prepare for unforeseen circumstances by developing a risk management plan which involves identifying potential risks in the supply chain and having contingencies in place.
– **Flexibility:** Maintain flexibility in ordering plans to quickly adapt to changes in demand or supply conditions.
The Role of Technology in Ordering Plans
Technology plays a pivotal role in enhancing order planning and execution.
Sophisticated software can analyze past and current data trends to predict future needs accurately.
Automation of mundane tasks such as reordering and inventory checks can free up valuable time for purchasing professionals.
Moreover, using centralized data management systems, all departments can access up-to-date information, facilitating coherent decision-making.
Challenges in Lead Time Analysis
While lead time analysis offers numerous benefits, it also presents certain challenges:
– **Data Accuracy:** Inaccurate or incomplete data can lead to incorrect analysis.
– **Supplier Inconsistencies:** Variations in supplier performance can complicate lead time predictions.
– **Market Volatility:** Sudden changes in market demand can render past lead time data less useful.
– **Technology Integration:** Implementation of new systems can be costly and time-consuming.
Overcoming these challenges requires a balanced approach that combines technology with human oversight and continuous improvement.
Conclusion
For purchasing department leaders, mastering lead time analysis and developing an optimal ordering plan are crucial to meeting business goals efficiently.
By understanding lead time factors, implementing strategic practices, and leveraging technology, purchasing managers can significantly enhance their operations.
A well-executed ordering plan not only reduces costs but also ensures that customer demands are met promptly, fostering a stronger competitive edge in the marketplace.
資料ダウンロード
QCD調達購買管理クラウド「newji」は、調達購買部門で必要なQCD管理全てを備えた、現場特化型兼クラウド型の今世紀最高の購買管理システムとなります。
ユーザー登録
調達購買業務の効率化だけでなく、システムを導入することで、コスト削減や製品・資材のステータス可視化のほか、属人化していた購買情報の共有化による内部不正防止や統制にも役立ちます。
NEWJI DX
製造業に特化したデジタルトランスフォーメーション(DX)の実現を目指す請負開発型のコンサルティングサービスです。AI、iPaaS、および先端の技術を駆使して、製造プロセスの効率化、業務効率化、チームワーク強化、コスト削減、品質向上を実現します。このサービスは、製造業の課題を深く理解し、それに対する最適なデジタルソリューションを提供することで、企業が持続的な成長とイノベーションを達成できるようサポートします。
オンライン講座
製造業、主に購買・調達部門にお勤めの方々に向けた情報を配信しております。
新任の方やベテランの方、管理職を対象とした幅広いコンテンツをご用意しております。
お問い合わせ
コストダウンが利益に直結する術だと理解していても、なかなか前に進めることができない状況。そんな時は、newjiのコストダウン自動化機能で大きく利益貢献しよう!
(Β版非公開)