- お役立ち記事
- How to create and utilize a quality function development concept diagram
月間76,176名の
製造業ご担当者様が閲覧しています*
*2025年3月31日現在のGoogle Analyticsのデータより
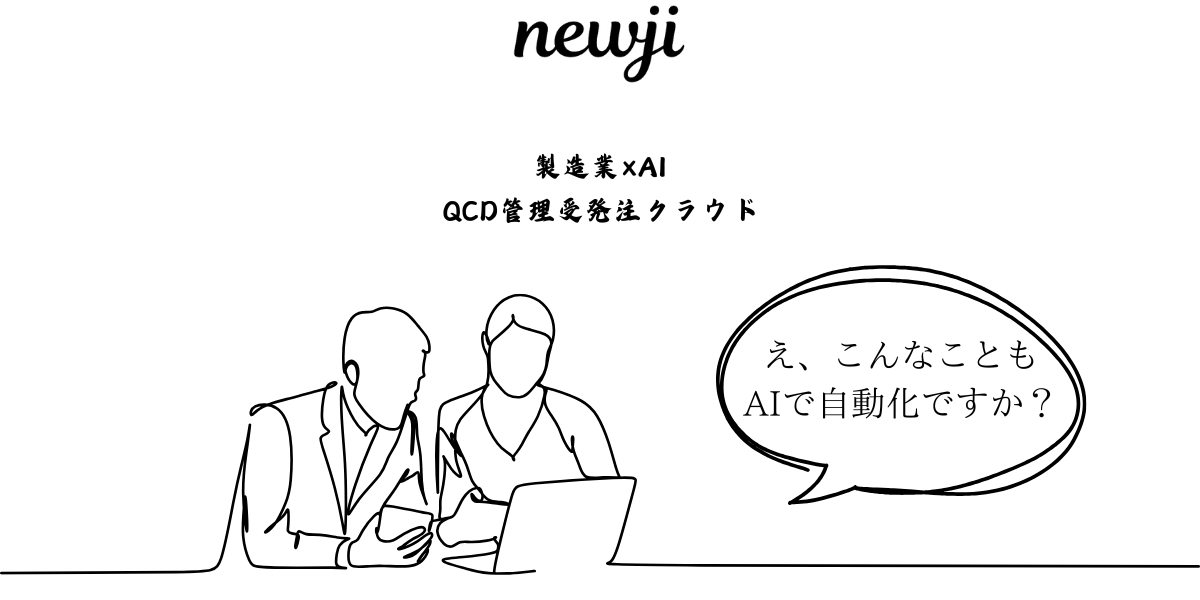
How to create and utilize a quality function development concept diagram
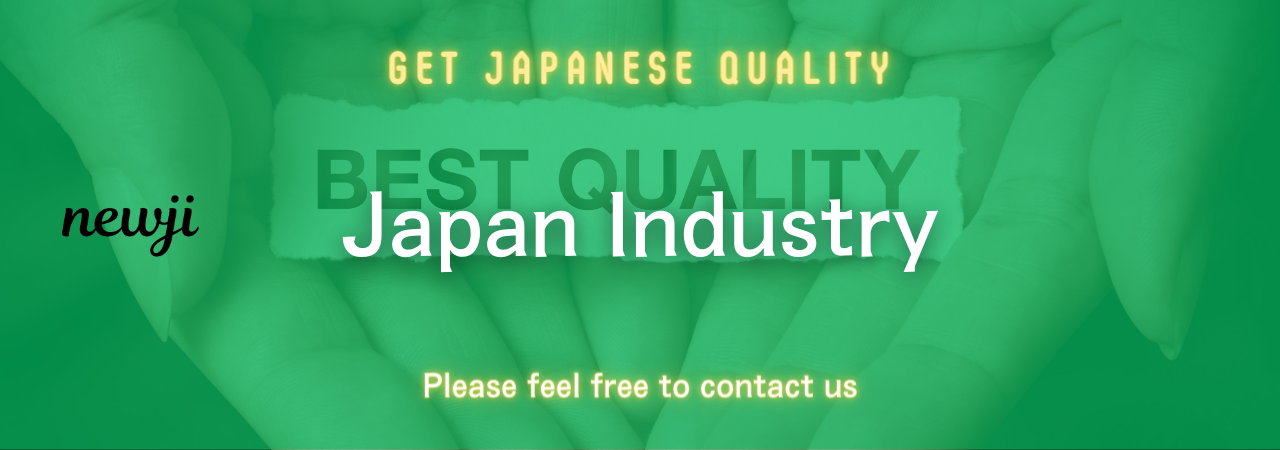
目次
Understanding Quality Function Development
Quality Function Development (QFD) is a structured method used to translate customer requirements into detailed product specifications.
It’s a critical component in product development, as it ensures that the voice of the customer is effectively heard and translated into designs and functionalities that meet or exceed their expectations.
A concept diagram plays a pivotal role in visualizing and organizing these requirements into actionable insights.
The Basics of Creating a QFD Concept Diagram
Creating a QFD concept diagram requires a structured approach.
The first step involves identifying and collecting customer needs, often referred to as the ‘Voice of the Customer’.
These needs are the foundation, serving as the primary inputs for the diagram.
Once customer needs are clearly defined, the next step is to prioritize them.
Not all customer needs hold equal weight, so it’s essential to rank them based on importance.
This prioritization helps in focusing on areas that will have the most significant impact on customer satisfaction.
Translating Needs Into Technical Requirements
After prioritizing customer needs, the QFD process shifts focus to translating these needs into technical requirements.
This step converts qualitative customer desires into quantitative technical specifications.
For instance, if a customer expresses a need for durability in a product, the technical requirement might be defined in terms of material strength or lifespan.
It is crucial to involve cross-functional teams during this phase.
Different departments such as engineering, marketing, and production can provide insights and develop a well-rounded set of technical specifications.
Developing the Relationship Matrix
A significant component of the QFD concept diagram is the relationship matrix.
This matrix is a grid that links customer needs to technical requirements.
Each intersection in the matrix is evaluated to determine the strength of the relationship between a customer need and a particular technical requirement.
The relationship matrix helps in identifying which technical requirements have the most substantial impact on meeting customer needs, allowing the development team to allocate resources efficiently.
Assessing Technical Competitive Benchmarks
An essential part of the QFD process involves benchmarking against competitors.
The concept diagram should incorporate a section that compares technical requirements against those of leading competitors.
This assessment not only highlights areas for improvement but also identifies opportunities for differentiation.
Technical benchmarks provide insights into industry standards and help ensure that the product meets or exceeds market expectations.
Evaluating the Final Design
Once all components of the QFD concept diagram are in place, the next step is to evaluate the final design.
This evaluation ensures that all customer needs are adequately addressed and translated into the product specifications.
The final design assessment often involves testing and simulations to verify that the product performs as intended under various conditions.
Utilizing the QFD Concept Diagram Effectively
Having created a comprehensive QFD concept diagram, the next step is to utilize it effectively throughout the product development process.
One of the key benefits of the QFD diagram is its ability to facilitate communication across different teams.
By providing a visual representation of the requirements and specifications, it ensures that everyone is on the same page.
Furthermore, the QFD diagram acts as a central reference point.
As changes occur in customer needs or technical requirements, the concept diagram can be updated, reflecting the latest information and ensuring that the product development stays aligned with customer expectations.
Continuous Improvement and Refinement
Utilizing a QFD concept diagram is not a one-time process.
It requires continuous improvement and refinement.
As customer needs evolve and new technologies emerge, the QFD diagram should be revisited and adjusted accordingly.
This continuous refinement ensures that the product remains competitive and relevant in a constantly changing market landscape.
The Benefits of a Well-Executed QFD Concept Diagram
A well-executed QFD concept diagram offers numerous benefits.
It improves product quality by aligning design processes with customer needs.
It also reduces time-to-market by streamlining the development process and minimizing unnecessary features or redesigns.
Moreover, it enhances team collaboration.
By providing a clear framework and reference for all parties involved, it fosters better communication and alignment.
Conclusion
Creating and utilizing a quality function development concept diagram is a vital part of modern product design.
By effectively translating customer needs into technical requirements, the QFD diagram not only improves product quality but also enhances customer satisfaction.
The key is to ensure continuous refinement and cross-functional collaboration throughout the development process.
In doing so, businesses can remain competitive and responsive to ever-changing customer expectations.
資料ダウンロード
QCD管理受発注クラウド「newji」は、受発注部門で必要なQCD管理全てを備えた、現場特化型兼クラウド型の今世紀最高の受発注管理システムとなります。
ユーザー登録
受発注業務の効率化だけでなく、システムを導入することで、コスト削減や製品・資材のステータス可視化のほか、属人化していた受発注情報の共有化による内部不正防止や統制にも役立ちます。
NEWJI DX
製造業に特化したデジタルトランスフォーメーション(DX)の実現を目指す請負開発型のコンサルティングサービスです。AI、iPaaS、および先端の技術を駆使して、製造プロセスの効率化、業務効率化、チームワーク強化、コスト削減、品質向上を実現します。このサービスは、製造業の課題を深く理解し、それに対する最適なデジタルソリューションを提供することで、企業が持続的な成長とイノベーションを達成できるようサポートします。
製造業ニュース解説
製造業、主に購買・調達部門にお勤めの方々に向けた情報を配信しております。
新任の方やベテランの方、管理職を対象とした幅広いコンテンツをご用意しております。
お問い合わせ
コストダウンが利益に直結する術だと理解していても、なかなか前に進めることができない状況。そんな時は、newjiのコストダウン自動化機能で大きく利益貢献しよう!
(β版非公開)