- お役立ち記事
- How to deal with global procurement risks faced by purchasing departments
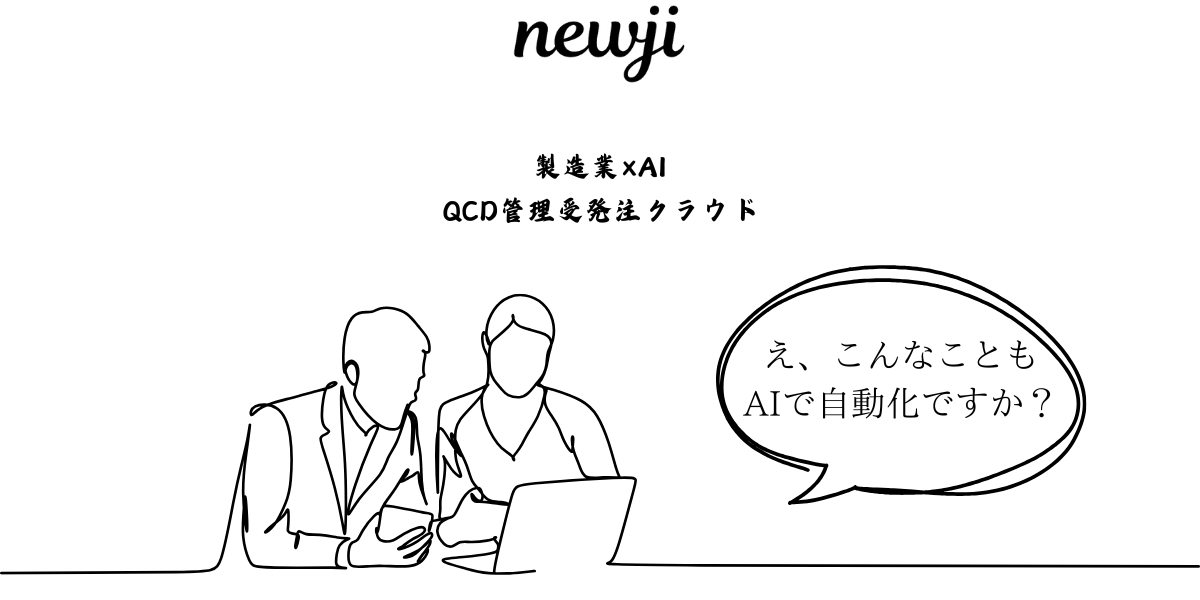
How to deal with global procurement risks faced by purchasing departments
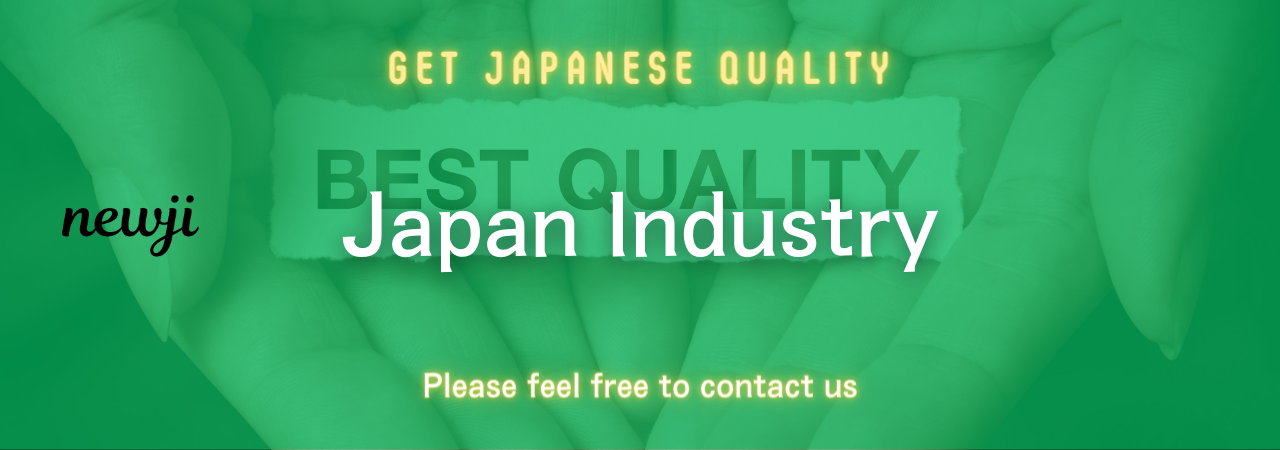
目次
Understanding Global Procurement Risks
In the interconnected world of business today, purchasing departments face a myriad of risks when engaging in global procurement.
These risks can stem from various sources, including geopolitical tensions, currency fluctuations, supplier reliability, and regulatory changes.
Understanding these risks is crucial to developing effective strategies to mitigate them.
Geopolitical Risks
Geopolitical risks can have significant impacts on global procurement.
Wars, trade disputes, and political instability can disrupt supply chains and lead to sudden changes in tariffs and trade regulations.
This can result in unexpected costs or supply shortages.
For purchasing departments, staying informed about geopolitical developments is essential.
One way to manage these risks is by diversifying the supplier base.
Relying on a single supplier or region can leave a company vulnerable to disruptions.
By developing relationships with multiple suppliers across different regions, purchasing departments can spread risk and increase resilience.
Currency Fluctuations
Currency fluctuations are another common risk in global procurement.
Exchange rate volatility can significantly alter the costs of goods, impacting the purchasing department’s budget and profitability.
While it is nearly impossible to predict currency movements accurately, there are strategies to mitigate these risks.
One approach is to implement hedging strategies.
Companies can use financial instruments, such as forward contracts or options, to lock in exchange rates for future transactions.
This can provide predictability and stabilize purchasing costs.
Supplier Reliability
Supplier reliability is a critical factor in global procurement.
Issues like late deliveries, poor quality products, or breaches of contract can lead to operational disruptions.
To address this, purchasing departments should conduct thorough due diligence when selecting suppliers.
Building strong relationships with key suppliers is essential.
Engaging with suppliers through regular communication and quality checks helps in maintaining high standards.
Implementing performance metrics and tracking supplier performance over time can also help identify weaknesses and areas for improvement.
Regulatory Changes
Regulatory changes can pose significant challenges in global procurement.
Different countries have varying standards and regulations which can impact compliance and legal obligations.
Ignoring these regulations can result in penalties or disrupted operations.
To manage this risk, purchasing departments should ensure they stay updated on regulatory changes in the countries where they operate.
Collaborating with legal teams and external consultants can help navigate complex regulatory landscapes.
Having contingency plans and flexible logistics options can ensure continued operations during sudden regulatory shifts.
Strategies to Mitigate Procurement Risks
By understanding global procurement risks, purchasing departments can devise strategies to mitigate or manage them effectively.
Risk Assessment and Monitoring
Regular risk assessments can help identify potential threats and vulnerabilities in the procurement process.
Monitoring these risks closely allows purchasing departments to respond proactively instead of reactively.
Developing a risk management framework tailored specifically to the organization’s needs is key.
This includes defining risk tolerance levels, identifying possible risk scenarios, and outlining a plan for addressing identified risks.
Technology and Data Analytics
Leveraging technology and data analytics can greatly enhance the ability of purchasing departments to manage risks effectively.
Data analytics can help identify trends and patterns that could signify potential risks, such as changes in supplier performance or market conditions.
Implementing procurement software can streamline operations and improve efficiency.
Automating certain processes, like contract management or order tracking, reduces human error and enhances transparency.
Building Strong Supplier Networks
Creating and maintaining strong relationships with suppliers is vital in managing procurement risks.
Supplier collaboration can lead to mutual benefits, such as improved quality, innovation, and reliability.
By engaging in open communication and establishing shared goals, both parties can work towards mitigating risks.
Strategic partnerships with key suppliers can also provide exclusive access to resources or products during times of scarcity.
Scenario Planning and Contingency Strategies
Scenario planning involves preparing for different potential risk scenarios and developing response strategies in advance.
This proactive approach allows purchasing departments to minimize disruptions when risks materialize.
Creating contingency plans such as alternative sourcing strategies or flexible logistics solutions ensures that operations can continue despite disruptions.
Having a clear crisis management plan in place enables quick and efficient responses to unforeseen events.
Conclusion
Dealing with global procurement risks requires a comprehensive understanding of potential threats and the implementation of effective strategies to mitigate them.
By being aware of geopolitical risks, currency fluctuations, supplier reliability, and regulatory changes, purchasing departments can develop robust plans for managing these challenges.
Using tools such as risk assessments, data analytics, and scenario planning alongside building strong supplier networks, purchasing departments can create resilient and agile procurement processes.
The ability to anticipate and adapt to changes in the global procurement landscape is essential for maintaining competitiveness and operational success.
資料ダウンロード
QCD調達購買管理クラウド「newji」は、調達購買部門で必要なQCD管理全てを備えた、現場特化型兼クラウド型の今世紀最高の購買管理システムとなります。
ユーザー登録
調達購買業務の効率化だけでなく、システムを導入することで、コスト削減や製品・資材のステータス可視化のほか、属人化していた購買情報の共有化による内部不正防止や統制にも役立ちます。
NEWJI DX
製造業に特化したデジタルトランスフォーメーション(DX)の実現を目指す請負開発型のコンサルティングサービスです。AI、iPaaS、および先端の技術を駆使して、製造プロセスの効率化、業務効率化、チームワーク強化、コスト削減、品質向上を実現します。このサービスは、製造業の課題を深く理解し、それに対する最適なデジタルソリューションを提供することで、企業が持続的な成長とイノベーションを達成できるようサポートします。
オンライン講座
製造業、主に購買・調達部門にお勤めの方々に向けた情報を配信しております。
新任の方やベテランの方、管理職を対象とした幅広いコンテンツをご用意しております。
お問い合わせ
コストダウンが利益に直結する術だと理解していても、なかなか前に進めることができない状況。そんな時は、newjiのコストダウン自動化機能で大きく利益貢献しよう!
(Β版非公開)